Storage and handling fundamentals
Dan Holdmeyer, Contributing Editor | TLT Lubrication Fundamentals June 2022
Consider these best practices before building, redesigning or updating a storage area.
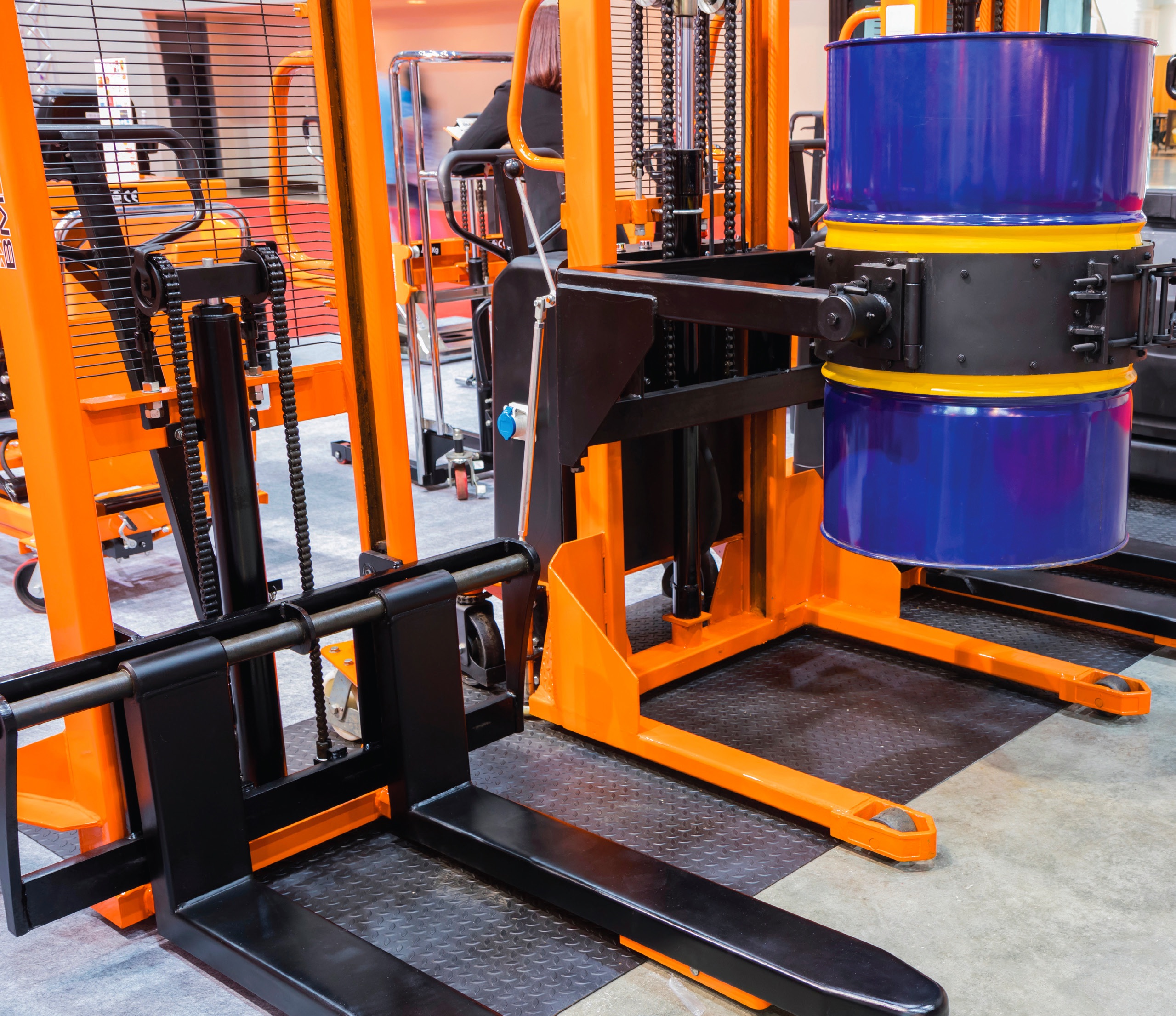
Many excellent articles have been written detailing best practices for storing and handling lubricants—mostly how to keep the lubricants clean and reduce cross contamination. I’d like to discuss some things to consider before building, redesigning or improving a storage facility.
First, consider what lubricants to store. Past lubricant purchases are frequently used to develop the list of required lubricants to store; however, these are seldom accurate as to what is needed for the site. Over time, new lubricants are added as new machines introduced have OEM lists of recommended lubricants, which are purchased and used when the machine is installed. When relubrication and top up are required, these same lubricants are reordered regardless of if an equivalent lubricant is already in storage. Similarly, just because the lubricant is in storage doesn’t mean it is needed. Some lubricants may have been purchased for a specific machine that has either been idled or even removed from the site.
To determine what lubricants a site truly needs, a review of the lubricant requirements of all the equipment is a good place to start. Look for opportunities to consolidate lubricants, i.e., a lubricant may have a higher performance level than required in a specific application, but using it may eliminate a lubricant from inventory. This reduces chances of a misapplication by minimizing the number of lubricants on site, reduces inventory costs and helps keep fresh lubricants in inventory.
While looking at the lubricants used in various equipment, make sure that the right lubricant is being used. Many times, lubrication practices are verbally passed from one individual to another without documentation that results in misapplication that has been happening for years.
How much of each lubricant should be stored depends on the total reservoir capacity of all the machines that use each lubricant. Consider how often the oil is changed plus typical lubricant consumption in between oil changes. Only about a quarter of that volume should be stored so the inventory is turned approximately every three months. This also will keep the lubricants fresh, reduce potential contamination and minimize storage costs. However, if there is a critical machine that could shut down operations if it is out of service and it has a large lubricant reservoir, larger than the amount of that lubricant stored per the previous calculations, the amount of that lubricant in storage needs to be increased, or an arrangement with the lubricant supplier is needed to maintain a backup supply. Another consideration for adjusting how much lubricant to store is availability. If a lubricant is particularly rare and not even the lubricant supplier carries a ready supply, check on the lead time to acquire it, and adjust the inventory level to carry operations through the order lead time.
Although price discounts come with larger package sizes, the discount may be lost due to some inherent dangers in lubricant storage. The first danger is contamination. Contamination potential increases with prolonged storage. Consider, for example, how much more air breathing a drum will do with only a quarter of it filled with lubricant versus a full drum. The air moving in and out of the drum due to diurnal heating and cooling increases the chance of airborne dust contaminating the lubricant. This is where many of those storage and handling articles do an excellent job of discussing application of particulate and desiccant filters for drums, and storage tanks become very useful.
Shelf life is another danger in storing lubricants. Most lubricating oils have a shelf life of five years; however, many have a shorter shelf life due to potential additive drop out. Notably, metalworking fluids, two-stroke motor oils and biodegradable fluids are some of the fluid types that frequently have a shelf life of one to three years. Additionally, shelf life is dramatically reduced when lubricants are exposed to wide temperature swings. Freezing temperatures are particularly detrimental to shelf life. Since I haven’t stated it yet—lubricants should be stored inside, in a temperature-controlled environment, preferably in a dedicated room.
Greases are another lubricant type with limited shelf life, ranging from one to three years depending on the type of grease. Grease is made of three major components: oil, thickener and additives. The grease is designed to “bleed” a little oil with additive over time to provide lubrication to the bearing or application. Oil separation is not desired in storage though. To maximize storage life, keep the grease temperature above freezing and below 80 F (about 27 C), and store grease cartridges vertically to minimize oil separation.
Grease cartridges are a good example of when a smaller package size’s benefits outweigh the price discount of a larger package size. Carrying a couple of extra grease cartridges with a grease gun to meet regreasing needs on a site is more convenient than frequently returning to lubricant storage to refill the grease gun. Additionally, grease cleanliness is more easily maintained by changing out grease cartridges compared to refilling the grease gun. Refilling a grease gun via a pump from a pail, keg or drum is far cleaner than manually transferring the grease; however, when the pail, keg or drum is empty, extra care needs to be taken to keep the follower plate and pump clean when changing over to a new container. Additionally, there is always some grease clingage in the larger container that is wasted.
A similar concept should be considered for lubricating oils used in locations remote to the primary lubricant storage room. Air compressor rooms, or remote machinery, that require frequent minimal top up of a lubricant between oil changes, would benefit from a smaller lubricant storage cabinet nearby. The lubricant packages stored in this remote cabinet should be sized to accommodate typical lubricant consumption, between oil changes, by the remote equipment.
Access to lubricant storage should be limited. Lubrication specialists understand the importance of, and best practices of, maintaining lubricant integrity. Machine operators and other personnel may not have had training on lubrication best practices. Even well-intentioned help with lubricating equipment can lead to cross contamination and allow particulate and moisture contamination of quality lubricants that will lead to premature machine failure. For example, product funnels are to be avoided; if they are used, they need to be cleaned after each use and stored in a sealed bag.
Determine the optimum location of the lubricant storage room and any smaller storage cabinets to be convenient for lubricating the majority of the equipment on site, and yet convenient for lubricant delivery to the room. Plan a systematic manner within the storage room of storing types of lubricants (hydraulic oil, engine oil, grease, etc.) together. Include labeling of each area as such with the lubricants’ names under these labels. This will help prevent cross contamination and minimize misapplications.
Now that the specific lubricants, the package sizes and quantities needed are identified, remove and dispose of any lubricants currently in storage that are past their shelf life or are no longer needed on site. Also, dispose of any lubricants whose containers have not been kept closed to keep out contaminants. To help minimize disposal of containers of lubricants like this again, implement First In, First Out (FIFO) procedures to rotate inventory.
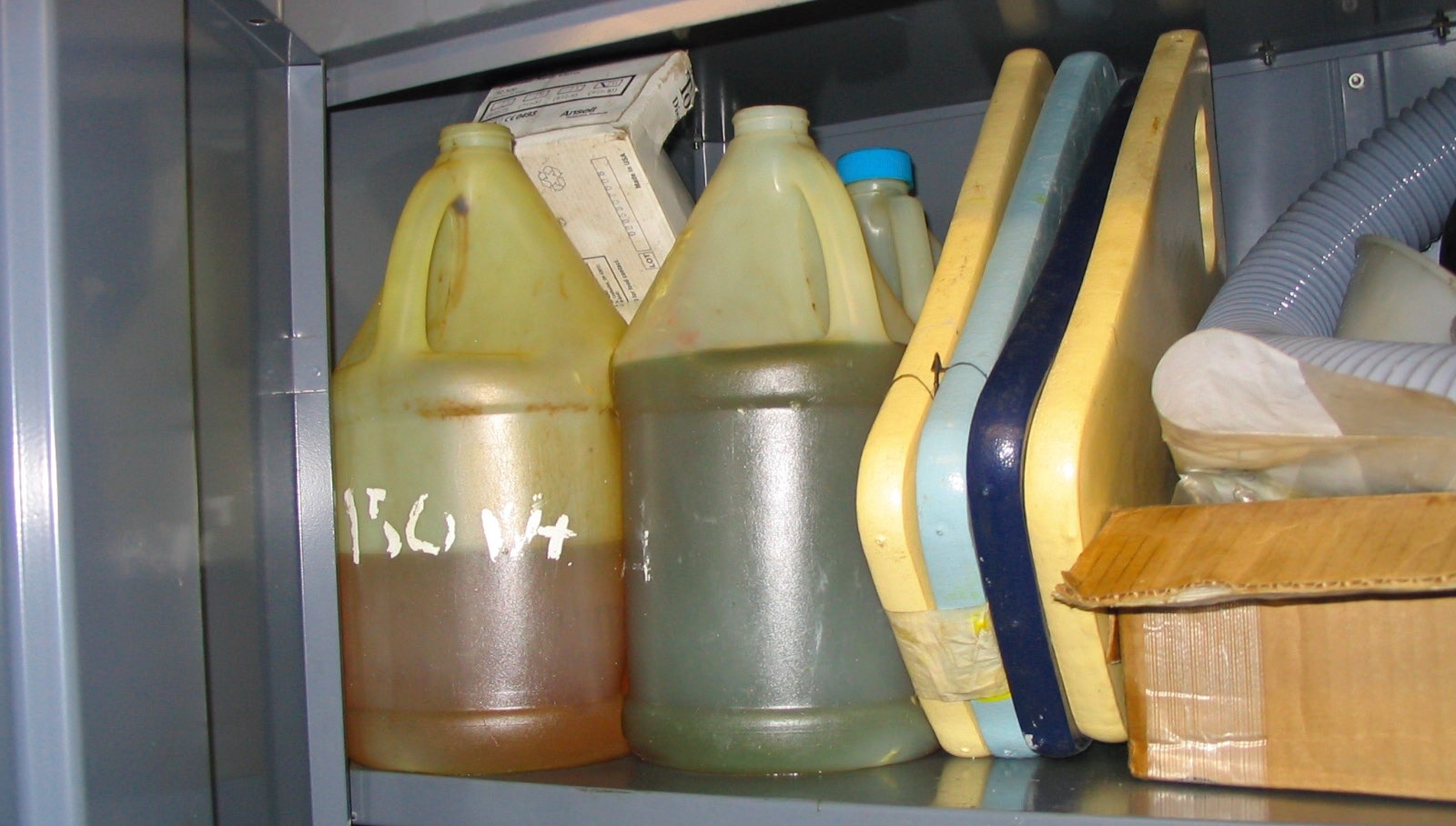
Small oil transfer containers poorly labeled and left open to collect airborne contaminants.
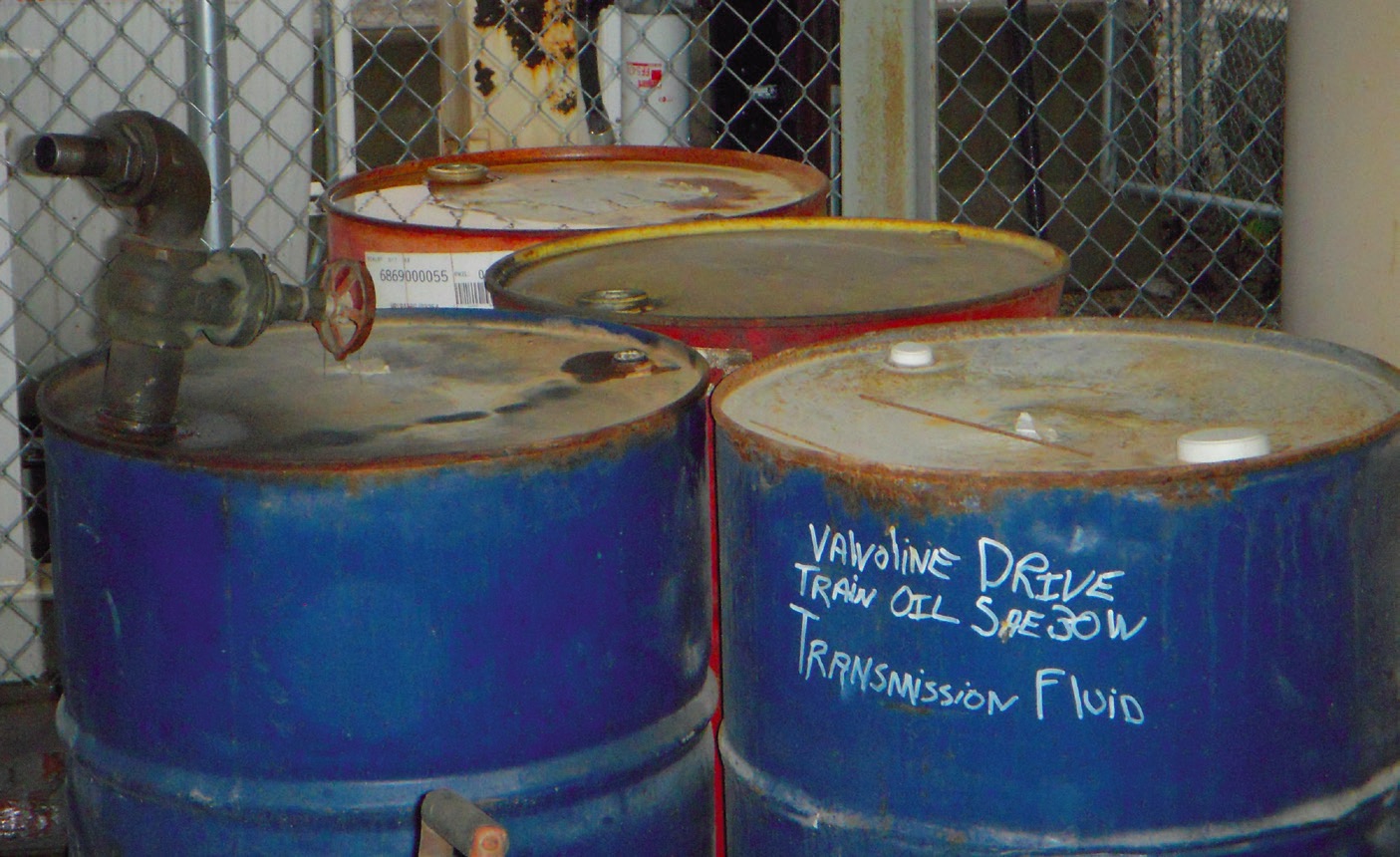
Poorly maintained lubricant storage with lubricants that should be disposed of.
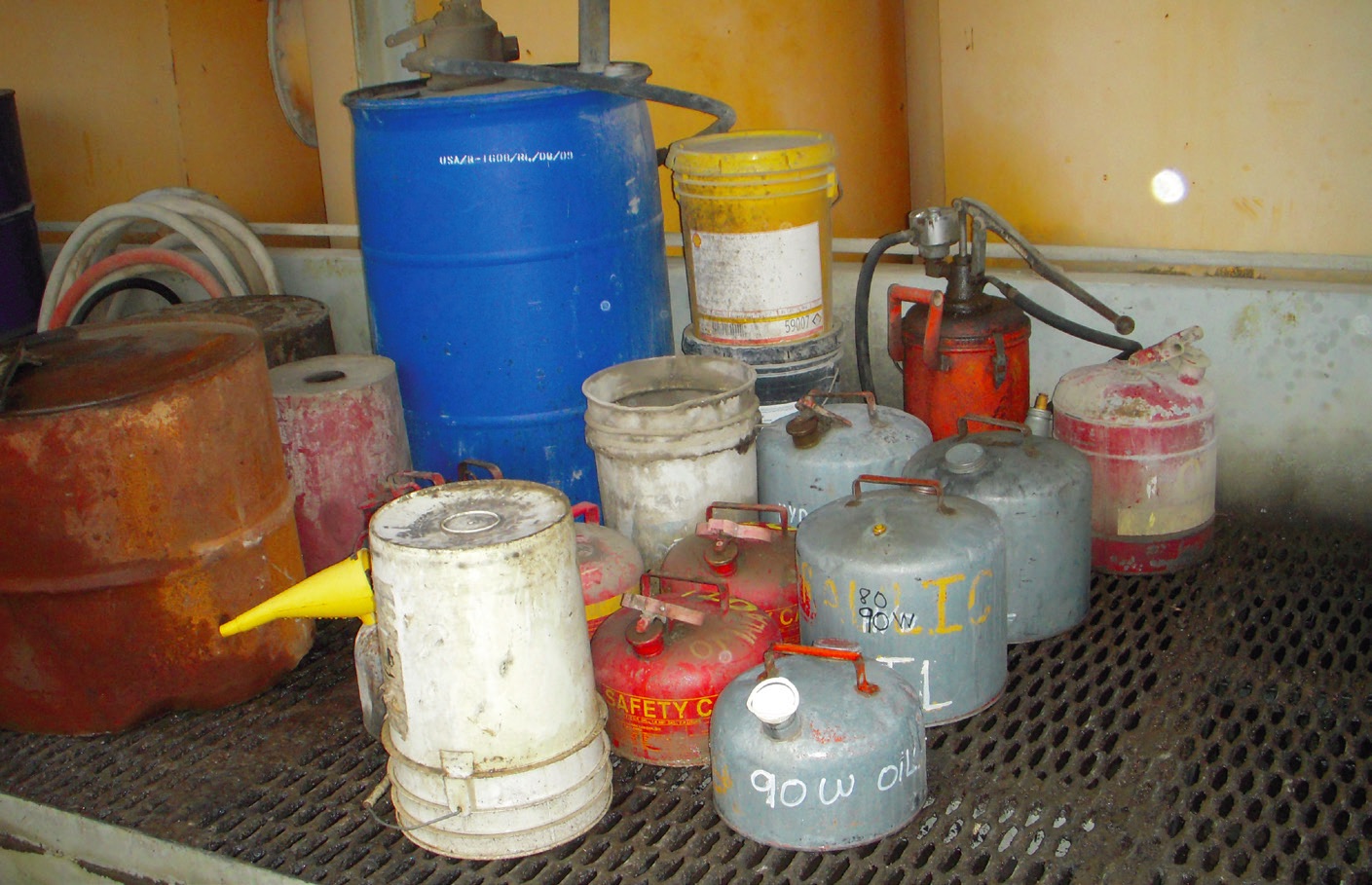
Poor lubricant storage.
The next step toward best-in-class storage and handling is to work with lubricant dispensing equipment suppliers to safely maintain your lubricant investment integrity. Some of the components to consider are fire suppression, oil disposal system, desiccant and particulate filters on oil storage containers, labels on storage containers and dedicated smaller transfer containers.
Dan Holdmeyer is retired from Chevron Lubricants and is based in Washington, Mo. You can reach him at dan.holdmeyer@gmail.com.