Relating Macroscale Wear to Mechanical Properties of Transfer Films In UHMWPE-PEEK Tribological Composites
Brenden J. Miller and Harman S. Khare | TLT Scholarship Research April 2022
Department of Mechanical Engineering Gonzaga University, Spokane, Wash.
Editor’s Note: This month TLT profiles the 2021 recipient of The E. Richard Booser Scholarship Award, Brenden Miller (Gonzaga University). The Booser scholarship is awarded annually to undergraduate students who have an interest in pursuing a career in tribology. As a requirement for receiving an STLE scholarship, students are given the opportunity to participate in a tribology research project and to submit a report summarizing their research. For more information about the Booser scholarship, visit www.stle.org.
Miller graduates with an undergraduate degree in mechanical engineering in May 2022. He will be joining L3Harris Technologies Inc. in the Engineering Leadership Development Program –Mechanical. His research was conducted under the mentorship of STLE member Dr. Harman Khare. Miller’s interests and extracurricular activities include fly fishing, traveling and reading. You can reach him at bmiller13@zagmail.gonzaga.edu.
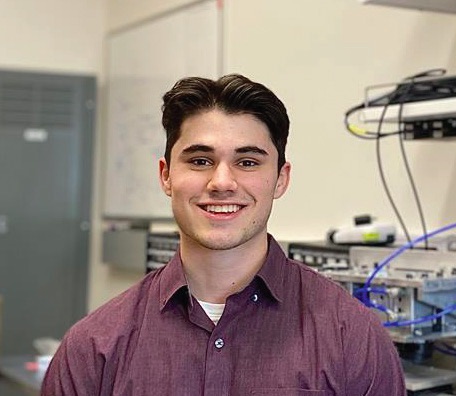
Brenden Miller
Abstract
Innovations in predictive design of materials are crucial for transforming reliability and performance of tribological systems. Material structure-property relationships are the cornerstone of predictive design, yet for many such systems, these remain poorly understood. Despite the development of advanced materials and recognition of the role interfacial films play in the wear of polymer composites, their nanomechanical properties remain poorly understood. This is in large part given the intrinsic challenges of accurately and quantitatively probing mechanical properties of sub-100 nm thin films. This research aims to bridge the gap between nanoscale structure and mechanical properties of polymeric interfaces to their macroscale wear, specifically in the design of tribological polymer composites. In this work, we present findings on both the macroscale, dry-sliding wear of a novel UHMWPE-PEEK composite as well as nanomechanical characterization of resulting interfacial transfer films using bimodal techniques in atomic force microscopy (AFM), capable of probing the local elastic and viscoelastic properties of thin films. These techniques will be used in combination with macroscale wear testing as a first step toward developing a framework for predicting and controlling macroscale wear of materials.
1. Introduction
Structure-property relationships are a cornerstone for the predictive design of tribological materials. Polymers and polymer composites are a ubiquitous class of materials that are often used for reducing friction and wear in applications that preclude use of conventional liquid lubricants. A host of polymeric materials have been shown to achieve dramatic reductions in interfacial wear through the addition of suitable quantities of fillers.
1,2 Wear reduction in polymer composites is often attributed to mechanical strengthening through increased load support at the filler-matrix interface or the arrestment of propagating of cracks.
3,4 Additionally, the ability of certain polymer composites to sustain low wear has been directly linked to the structural and chemical evolution of their sliding interfaces, in particular to the formation of robust interfacial films.
5-9 Formation of these films has in some instances been attributed to interfacial mechanochemistry, where shear stress-induced chain-scission creates reactive moieties with high affinity for metallic counter-surfaces or reactants in the surrounding environment.
10,11 The incidence, morphology, thickness and spatial coverage of interfacial films has been shown to generally correlate well with polymer wear rates.
8,12 However, little is known about the structure and mechanical properties of the interfacial films which allow them to provide a robust load-bearing interface. Given interfacial polymer films for ultra-low wear polymer composites range in thickness between 5-1,000 nm, an accurate measurement of mechanical properties is intrinsically challenging. As a result, most predictive models of polymer nanocomposite wear rely on bulk mechanical properties, which completely ignore the presence of surface-modified layers, resulting in large errors between predicted and measured tribological performance.
Interfacial films are essential to the development of low wear behavior and frictional properties of systems. Understanding how they develop and how their properties can be tailored holds promise for creating novel, ultra-low wear materials. This study aims to develop such a mechanistic framework for relating the nanomechanical properties of polymer composite transfer films to their macroscale friction and wear properties. Specifically, we present findings linking the macroscale wear behavior of novel ultra-high molecular weight polyethylene (UHMWPE) and polyether-ether-ketone (PEEK) composites to the nanoscale mechanical properties of their transfer films. UHMWPE-PEEK composites were chosen as a model polymer system—wear behavior of these composites have previously been characterized in the literature.
13 Amplitude modulation-frequency modulation (AM-FM) AFM will then be used to quantitatively probe the nanomechanical properties of resulting transfer films within highly localized regions.
2. Materials and methods
2.1 Sample preparation
Composite specimens for tribological testing were synthesized using a combination of powder metallurgy and compression molding, similar to methods reported elsewhere.
14 Powdered forms of UHMWPE (nominal particle size 150 μm, molecular weight 5,000 k g/mol from Goodfellow Corp., UK) and PEEK (Victrex 450PF with nominal size 80 μm from Goodfellow Corp., UK) were used in this study. Measured quantities of UHMWPE and PEEK were mixed in a glass beaker to obtain composite weight fractions of 0, 25, 50, 75 and 100 wt.% PEEK in UHMWPE. In order to adequately disperse the polymer blend, approximately 75 mL of ethanol was added to the glass beaker, followed by sonication at 400 W (Branson Sonifier 450) and 50% duty cycle for 10 minutes. Homogenized solutions were dried on a hot plate under ambient conditions for at least eight hours, until fully dry. Dried powders were compacted into a cylindrical preform and held at 390 MPa for 20 minutes in order to eliminate porosity. Compacted preforms were then wrapped in aluminum foil and placed in a PID-controlled furnace, where samples were free sintered in an ambient atmosphere. The sintering profile included a uniform temperature ramp at a nominal rate of 2° C/min to 180° C, a temperature soak at 180° C for an additional four hours, followed by a controlled ramp to ambient temperature at a nominal rate of 2° C/min. A similar sintering profile has been reported for UHMWPEPEEK composites elsewhere in the literature. 13 Cuboidal test specimens with nominal dimensions 6.35 mm x 6.35 mm x 12.5 mm were machined from the sintered cylindrical samples. Together with measured mass of this pin, bulk composite density was determined and compared to the theoretical (fully dense) density to estimate void fractions. All samples were determined to have densification of over 95%.
2.2 Wear testing
Macroscale wear testing was conducted on a custom-built reciprocating tribometer
(see Figure 1). The tribometer is equipped with two test stations, capable of conducting wear tests of two different test pins (against their respective countersurfaces) concurrently. Normal load is independently applied at each station through electropneumatically-actuated thrusters. Each polymer pin is affixed to a six-axis load cell (ATI Industrial Automation), capable of recording applied normal and frictional forces in real time. A contact load of 250 N was applied at the sliding interface, which resulted in a nominal contact stress of 6.2 MPa. The sliding countersurface comprised of a lapped AISI 304 stainless steel substrate, which was mechanically polished to a nominal average surface roughness (Ra) of 170±30 nm. Polymer pins were run-in against a 240 grit sandpaper prior to testing against the steel countersurface to ensure conformal contact between the pin and the reciprocating table. Polymer wear was quantified through interrupted mass measurements on a precision analytical balance (Mettler Toledo AT261), with a 10 μg readability. Each polymer pin was run for a total distance of 11.48 km. All experiments were conducted in triplicate (with freshly prepared pin and substrate) to quantify reproducibility.
Figure 1. A custom-built linear reciprocating tribometer was used to perform all wear testing. The tribometer allows for two independent composite pins to be tested simultaneously, which recording real time values of interfacial forces. All experiments were conducted under ambient environment and temperature.
2.3 Atomic force microscopy
Nanoscale topography and nanomechanical characterization of polymer transfer films was conducted on an Oxford Instruments MFP-3D Origin+ AFM. Specifically, measurements were conducted using amplitude modulation-frequency modulation (AM-FM) AFM on representative regions measuring 50 μm x 50 μm. Each raster scan resulted in measurement of surface topography, and maps of elastic modulus, dissipation and stiffness. All measurements were conducted using a diamond-like carbon coated silicon probe (BudgetSensors Tap300DLC), with a nominal fundamental frequency of 300 kHz. Initial AM-FM AFM measurements were conducted on a substrate comprising a blend of polystyrene and polyolefin elastomer spincast onto a silicon substrate (PS-LDPE-12M, Bruker Nano). PS and LDPE domains on this substrate have well-characterized values of elastic modulus and dissipation and were therefore used to optimize scan and probe parameters.
15 The PS-LDPE substrate was further scanned both before and after measurements on UHMWPE-PEEK transfer films to rule out measurement artifacts attributable to tip history.
3. Results and discussion
Figure 2 shows measured values of steady state wear rate for tests pins with various weight fractions of PEEK in UHMWPE. Wear rate for unfilled UHMWPE (“0 wt.% PEEK”) was measured to be 5.5 x 10
-8 mm
3/Nm. Wear rate with the addition of 25 wt.% PEEK was seen to increase to 1.7 x 10
-7 mm
3/Nm, and negligibly when PEEK concentration was increased to 50 wt.% and 75 wt.% (2.2 x 10
-7 mm
3/Nm and 1.9 x 10
-7 mm
3/Nm, respectively). A significant increase in wear rate (1.2 x 10
-5 mm
3/Nm) was observed for pure PEEK. Values of wear rate for both unfilled UHMWPE and pure PEEK are comparable to values reported elsewhere in the literature.
13,16 Error bars represent standard deviation across replicates. These results indicate that UHMWPE and PEEK do not necessarily have beneficial synergies for reducing wear; however, the UHWMPE matrix appears to dominate wear characteristics for PEEK loadings as high as 75 wt.%. Conversely, the addition of 25 wt.% UHWMPE to a PEEK matrix is sufficient to decrease wear rate of unfilled PEEK by nearly two orders of magnitude.
Figure 2. Steady state wear rates of tested composites show that the addition of PEEK to a UHMWPE matrix increases wear by less than an order of magnitude. Steady state wear rate of unfilled PEEK is significantly higher. Error bars indicate standard deviation of data from independent replicates.
Representative optical micrographs of resulting transfer films are shown in Figure 3. Transfer film development was observed for all polymer composites that were tested in this study. Test pins with 0, 25, 50 and 75 wt.% PEEK showed the development of a transfer film which provided nearly complete coverage on the steel substrate, appearing to anchor to surface scratches in several locations. Transfer films for these compositions also exhibited occasional bands along the sliding direction of thicker film (visible as blue and brown colors on the optical images). In contrast, transfer films for pure PEEK pins were seen to be patchier, with incomplete coverage on the steel substrate.
Figure 3. Optical micrographs of transfer films on steel countersurfaces at the end of testing. All tested compositions exhibit development of transfer films; however, morphology of unfilled PEEK transfer films is distinctly different from any UHMWPE-containing transfer film. Scale bar in each image corresponds to 100 μm.
In order to quantify variations in transfer film morphology, selected transfer film regions were imaged using an amplitude modulation (“tapping mode”) AFM; corresponding topographical images are shown in Figure 4. The direction of macroscale sliding during wear testing for each image is vertical (top to bottom). In general, variations in local morphology and thickness of transfer film were observed for each of the five transfer films as a function of spatial location within the macroscale wear track, with certain local regions appearing thicker than others. AM-AFM measurements were therefore collected at both thinner and thicker regions of transfer film; only a subset of these images is shown in Figure 4. Transfer films with pure PEEK pins show a strong morphological correlation with sliding direction, consistent with optical micrographs, with highly oriented bands of transfer film along the direction of macroscale sliding. Measured average surface roughness for all transfer films was less than 100 nm, therefore resulting in a smoothening of the bare steel substrate. No evidence of a correlation between filler content and transfer film roughness could be deduced from measured data.
Figure 4. Topographic AFM images at representative regions on transfer films from the five tested compositions. Scale bars correspond to 10 μm.
Local nanomechanical properties of transfer films were quantified using AM-FM AFM. With each composition, several replicates were collected at various locations on the transfer film to capture spatial variability. The latter also helps mitigate artifacts in measured properties due to local film thickness, in particular, due to substrate effects. Figure 5 shows representative histograms of transfer film elastic modulus, measured across transfer films for the five tested compositions. The pure UHMWPE transfer film was observed to have a significantly lower elastic modulus than pure PEEK transfer film, as expected. Trends in elastic modulus with increasing concentration were surprisingly non-monotonic. Although transfer films from 25 wt.% and 75 wt.% PEEK pins had elastic moduli comparable to unfilled UHMWPE, the transfer film from 50 wt.% PEEK exhibited a distinctly higher elastic modulus, although a value still lower than pure PEEK. Although it remains unclear why measured modulus for 50 wt.% is higher, it is plausible that this might be due to a combination of spatial heterogeneity and substrate effects. AMFM AFM measurements were conducted on the PS-LDPE “standard” substrate both prior and subsequent to measurements on UHMWPE-PEEK transfer films to rule out tip history effects, including wear. Measured elastic moduli for this substrate, shown in Figure 5, inset, are identical to values obtained with a new probe prior to scanning with composite transfer films, and are consistent with values reported elsewhere,
15 thus ruling out effects of tip wear. Additional measurements, particularly in regions of varying transfer film thickness, are therefore required to better understand the origin of observed trends in nanomechanical properties, in particular, for more systematically deconvoluting the effects of composition and film thickness.
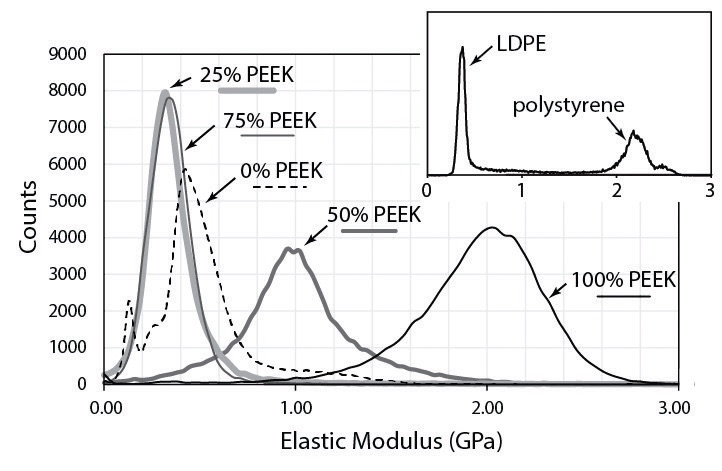
Figure 5. Histograms of transfer film elastic moduli corresponding to varying pin composition, measured over a 50 μm x 50 μm area using AM-FM AFM. Inset: A histogram of elastic modulus measured over a standard PS-LDPE spin-coated substrate, using the same probe as the one used for UHMWPE-PEEK measurements confirms the accuracy of measured values of elastic modulus.
4. Conclusions
This work presents findings on the wear behavior of UHMWPE-PEEK composites and an investigation of the links between transfer film nanomechanical properties and macroscale wear. Based on these preliminary results, we find that:
1.
Wear rate of UHMWPE composites is sensitive to PEEK weight fractions; however, differences in wear rate are small except in the case of unfilled PEEK. Values of unfilled UHMWPE and PEEK are consistent with values reported in the literature.
2.
In general, all UHMWPE-PEEK composites result in the formation of transfer films that provide adequate coverage on the steel substrate. Unfilled PEEK results in the formation of patchy transfer films.
3.
Measured elastic modulus of transfer films shows a dependence on filler concentration; however, modulus trends non-monotonically with filler concentration. Future work will more systematically explore the origins of this observed behavior.
5. Acknowledgement
Brenden J. Miller gratefully acknowledges STLE for honoring him with the E. Richard Booser Scholarship. Authors acknowledge the National Science Foundation’s Major Research Instrumentation Program (Award #1919528) for supporting acquisition of instrumentation used in this research.
REFERENCES
1.
Friedrich, K. (2018), “Polymer composites for tribological applications,”
Advanced Industrial and Engineering Polymer Research, 1, pp. 3-39.
2.
Friedrich, K., Lu, Z. and Hager, A. M. (1995), “Recent advances in polymer composites’ tribology,”
Wear, 190, pp. 139-144.
3.
Lancaster, J. K. (1972), “Polymer-based bearing materials: The role of fillers and fibre reinforcement,”
Tribology, 5, pp. 249-255.
4.
Lancaster, J. K. (1972), “Polymer-based bearing materials: The role of fillers and fibre reinforcement in wear,”
Wear, 22, pp. 412-413.
5.
Bahadur, S. (2000), “The development of transfer layers and their role in polymer tribology,”
Wear, 245, pp. 92-99.
6.
Fusaro, R. L. (1990), “Self-lubricating polymer composites and polymer transfer film lubrication for space applications,”
Tribol. Int., 23, pp. 105-122.
7.
Jain, V. K. and Bahadur, S. (1978), “Material transfer in polymer-polymer sliding,”
Wear, 46, pp. 177-188.
8.
Haidar, D. R., Ye, J., Moore, A. C. and Burris, D. L. (2017), “Assessing quantitative metrics of transfer film quality as indicators of polymer wear performance,”
Wear, 380-381, pp. 78-85.
9.
Ye, J., Khare, H. S. and Burris, D. L. (2013), “Transfer film evolution and its role in promoting ultra-low wear of a PTFE nanocomposite,”
Wear, 297, pp. 1095-1102.
10.
Harris, K. L., Pitenis, A. A., Sawyer, W. G., Krick, B. A., Blackman, G. S., Kasprzak, D. J. and Junk, C. P. (2015), “PTFE tribology and the role of mechanochemistry in the development of protective surface films,”
Macromolecules, 48, pp. 3739-3745.
11.
Harris, K. L., Pitenis, A. A., Sawyer, W. G., Krick, B. A., Blackman, G. S., Kasprzak, D. J. and Junk, C. P. (2015), “PTFE tribology and the role of mechanochemistry in the development of protective surface films,”
Macromolecules, 48, pp. 3739-3745.
12.
Burris, D. L. and Sawyer, W. G. (2005), “Tribological sensitivity of PTFE/alumina nanocomposites to a range of traditional surface finishes,”
Tribol. Trans., 48, pp. 147-153.
13.
Liu, Y. and Sinha, S. K. (2013), “Mechanical and tribological properties of PEEK particle-filled UHMWPE composites: The role of counterface morphology change in dry sliding wear,”
J Reinf Plast Compos, 32, pp. 1614-1623.
14.
Khare, H. S., Moore, A. C., Haidar, D. R., Gong, L., Ye, J., Rabolt, J. F. and Burris, D. L. (2015), “Interrelated effects of temperature and environment on wear and tribochemistry of an ultralow wear PTFE composite,”
Journal of Physical Chemistry C, 119, pp. 16518-16527.
15.
Lamour, G., Yip, C. K., Li, H. and Gsponer, J. (2014), “High intrinsic mechanical flexibility of mouse prion nanofibrils revealed by measurements of axial and radial Young’s moduli,”
ACS Nano, 8, pp. 3851-3861.
16.
Haidar, D. R., Alam, K. I. and Burris, D. L. (2018), “Tribological insensitivity of an ultralow-wear poly(etheretherketone)–polytetrafluoroethylene polymer blend to changes in environmental moisture,”
The Journal of Physical Chemistry C, 122, pp. 5518-5524.