Regrease properly
Dan Holdmeyer, Contributing Editor | TLT Lubrication Fundamentals April 2022
A simple equation and a checklist of important considerations can help to optimize the greasing of bearings.
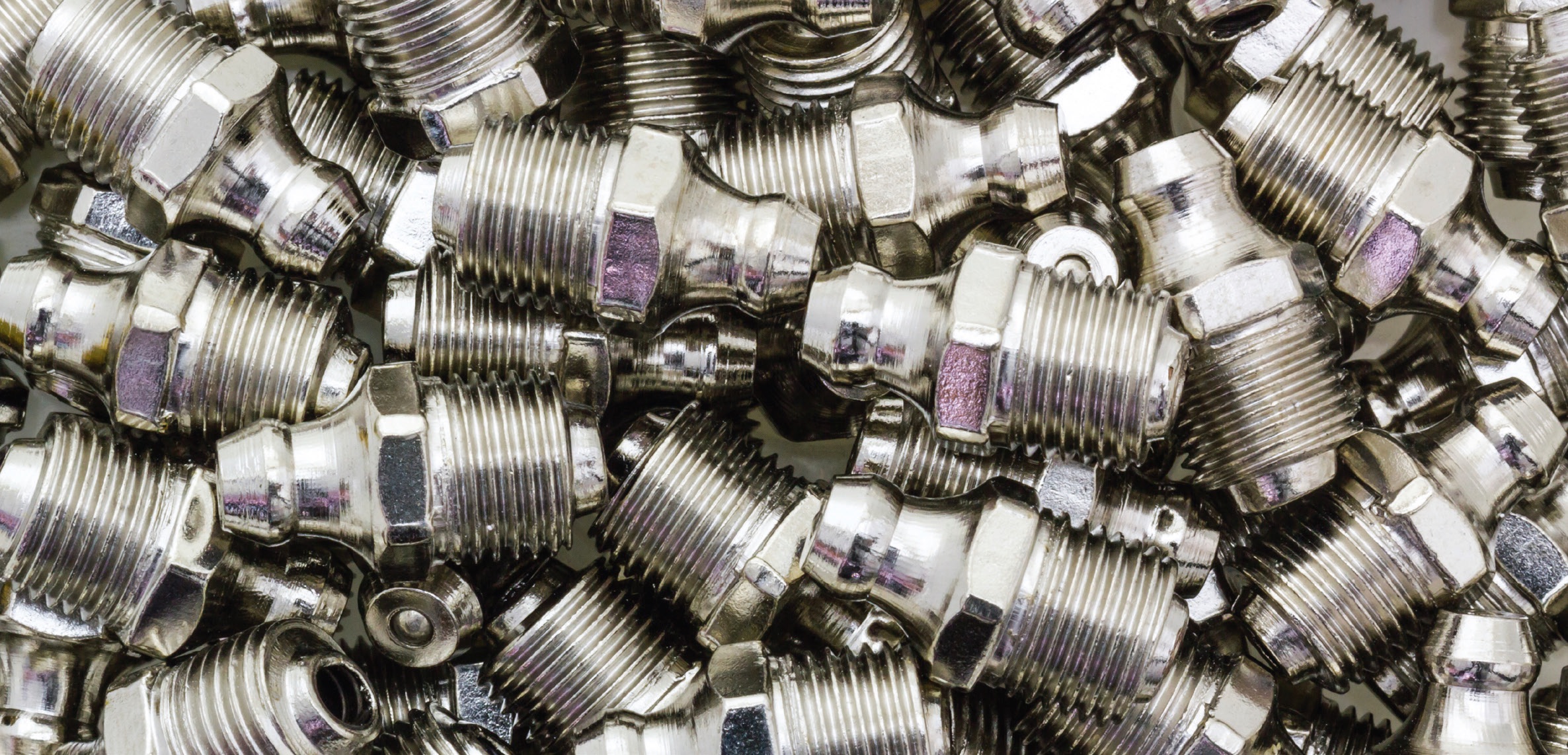
I realized a little grease is good, and there is such a thing as too much grease.
Several (more than 45) years ago, I would grease the farm implements by finding all the grease zerks, or grease fittings, on the machine and pump in grease until I saw fresh grease come out, somewhere. Fortunately, we only used one grease type on the farm, so grease compatibility wasn’t a concern there. However, I now realize my process still was flawed for several reasons.
Cleanliness
Although I knew to not put the grease gun tip in dirt and to keep dirt out of the grease inside the gun, I never thought about the grease zerk (see Figure 1). Of course, I would knock off clumps of dirt from the zerk, but I did not realize the ball valve in the zerk has a small groove around the exposed portion of the ball that collected dust and dirt. By not thoroughly cleaning the grease zerk before greasing, I was pushing the dirt into the bearing or journal, promoting excessive wear. In my defense, I did not see that dirt. The unaided eye can only see particles down to about 40 microns in size. I learned much later that it is the “invisible” particles, smaller than 40 microns, that get between the lubricated sliding and rolling surfaces and, thus, cause excess wear. Ideally, I would have left a little grease on the zerk after greasing to seal the zerk’s ball valve against dirt. Then, a quick wipe of the zerk would remove the small amount of grease, and dirt, off the zerk before greasing the next time. Today, grease zerk caps are available for keeping dust and dirt off the zerk between greasings, so long as they are not knocked off or lost.
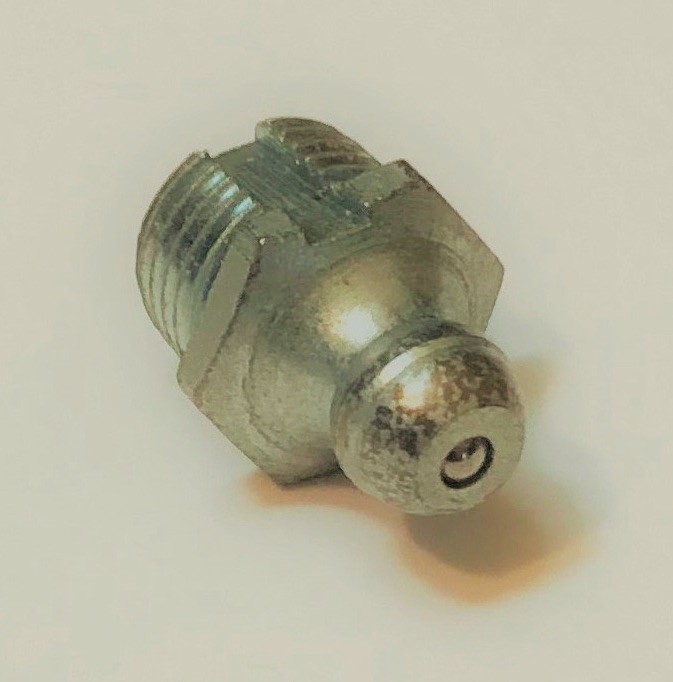
Figure 1. Slotted grease zerk.
Amount of grease
Pumping grease until fresh grease appeared worked well for slow speed journal bearings and bushings. This practice purged the journal of old grease and of any dirt that may have collected at the edge of the bearing. The bead of grease around the journal along the bearing also served as a barrier to dirt and contaminants from entering the bearing. Although sometimes the purged grease would collect in a hidden cavity and ultimately made a huge mess that I eventually had to clean. The lesson learned from that extra work was to estimate how much grease might be needed to purge the bearing, and if the bearing is taking more than that, to look at other places for the purging grease.
Journal bearings consist of a shaft, which rotates within a conforming metal sleeve or bearing (the journal being the portion of the shaft encased in the bearing). Bushings are a form of journal bearing, except the shaft does not make a full rotation. Because the shaft is not fully rotating, a full fluid film is not developed and, thus, bushings operate in the boundary lubrication regime. Grease helps support the load in this regime.
Higher speed journal bearings are typically oil lubricated, operating in a full fluid or hydrodynamic lubrication regime. Although simple in concept, lubrication of high-speed journal bearings can be complex and is beyond the scope of this article.
Bearing type
Rolling element bearings are more sensitive than journal bearings to the amount of grease pumped into them.
I was used to packing automotive wheel bearings full before placing them back on the spindle (see Figure 2). This was a proven successful procedure as the bearing housing around the spindle had a cavity for the grease to go just out of the rolling elements’ path. The rolling elements still contacted the grease just enough to wick out enough oil to lubricate the bearing but not enough to cause churn and resistance.
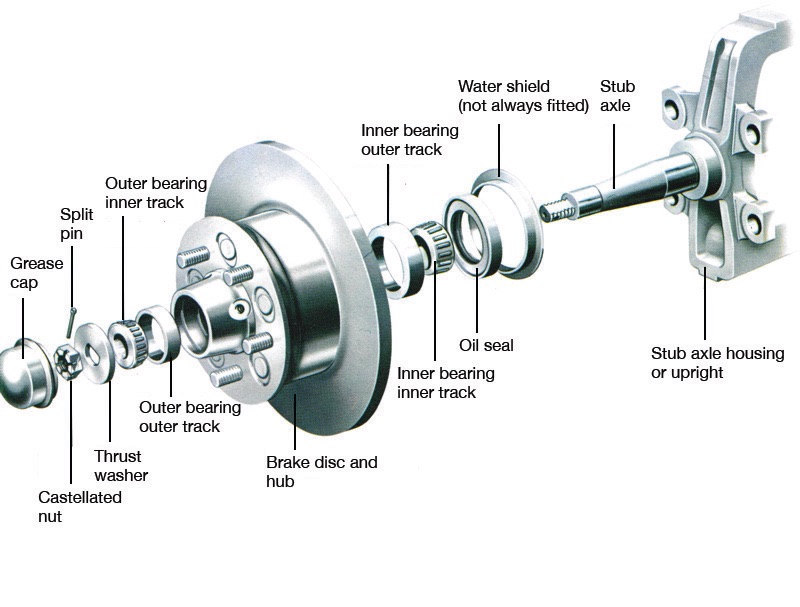
Figure 2. Automotive style spindle bearings. Figure courtesy of Hannan Ahmed, CC BY-SA 4.0, via Wikimedia Commons.
Shielded bearings, on the other hand, are designed to keep grease in the bearing and dirt out of the bearing. If too much grease is pumped into these bearings, the grease has no place to go, so the rolling elements must plow through the grease inside the bearing as it rotates. This churning tends to heat up and create pressure in the bearing. The heat changes the bearing fit and leads to premature wear and failure. Additionally, pressure can easily overcome the shield structure, resulting in the grease leaking out and dirt entering the bearing. The bearing now needs to be relubricated more frequently to keep in lubricant protecting the rolling elements and to purge out any contamination that is now able to enter the bearing.
So, if too much grease is introduced to a shielded or sealed bearing, the grease has no easy path to alleviate the pressure, and the bearing will fail prematurely.
Electric motors are particularly susceptible to overgreasing of their bearings beyond the potential for bearing failures. Excessive grease from electric motor bearings can find its way into the motor windings causing overheating and electrical shorts within the motor.
Grease gun calibration
Having burnt out an electric motor or two on the farm, I realized a little grease is good, and there is such a thing as too much grease, but I didn’t know how to determine, nor deliver, the right amount of grease for specific rolling element bearings.
A general rule of thumb is to pump grease equal to about 1/3 to 1/2 the volume of space between the inside and outside races of the bearing. (Now, does that mean minus the volume of the rolling elements?) Higher rpm bearings would get grease amounting closer to 1/3 the volume, whereas slower bearings would get closer to 1/2 the volume. That’s helpful, but I was still needing more definitive guidance.
Many years ago (but less than 40) I learned from an STLE education course a simple equation for regreasing bearings. The equation is as follows, where OD is the bearing outside diameter and W is the bearing width, both in inches, to determine the number of ounces of grease to relubricate a rolling element bearing.
0.114 x OD (in) x W (in) = Grease (oz)
None of the grease guns I’ve used had a meter on it measuring pumped grease. So, to determine how many pumps on my grease gun equaled an ounce of grease, I used a postal scale. I pumped grease from my grease gun until I had one ounce piled on the scale. My gun took 18 pumps per ounce of grease. Other grease gun outputs may be as high as one ounce per 10 pumps or as low as one ounce per 28 pumps, as examples. Be sure to calibrate your grease gun.
As an example, I would only use three pumps to regrease my electric motor because the bearings outside diameter measured two inches and the width was 3/4 inches. Or,
0.114 x 2 OD x 3/4 W = 0.171 ounces of grease
0.171 ounces x 18 pumps/ounce = 3.078 pumps
That is considerably less than the dozen or so grease pumps I would put into those electric motors.
The same calculations apply to other shielded and sealed rolling element bearings not in electric motors.
Frequency
It was our standard practice to grease the farm equipment before heading out to the fields each time. It was, and still is, a good practice for the unsealed journal bearings and bushings.
Enclosed rolling element bearings, e.g., pillow block, shielded or sealed bearings, require less frequent relubrication. Electric motor bearings generally don’t require lubrication but once a year or every six months, when not operated in a harsh environment. Factors contributing to a harsh environment are higher levels of dust or dirt, water contamination, excessive vibration or temperatures above approximately 150 F. Harsh environments require an increase in relubrication frequency.
The infrequent electric motor use on our family farm required even less frequent relubrication than once per year. In fact, many smaller electric motors today have sealed for life bearings and require no relubrication. Check with your electric motor supplier to determine if the bearings are sealed or what relubrication frequency is required. Do not assume that because the motor has a grease zerk it requires relubrication. Grease zerks may be installed on all motors to simplify procedures, reduce mistakes and lower costs during production.
Bearing relief
Another method of determining the right amount and frequency of regreasing rolling element bearings is to lubricate the bearing while it is spinning and then allow it to relieve itself of excess grease. Some bearings are designed with relief ports or plugs opposite of the grease zerk. Be sure the relief port is open and free of debris to allow the bearing to purge any excess grease. Some grease zerks have built-in relief ports. Purging of bearings without relief ports can be accomplished by removing the grease zerk for about five to 10 minutes after relubrication to allow the bearing to purge itself of any excess grease while it is still spinning. Be sure to replace the grease zerk after purging. Make note of how much grease was applied to help determine the optimum regrease frequency and quantity.
Lubrication starvation
If you can safely measure the bearing temperature while it is in operation before regreasing, compare that temperature to the operating bearing temperature five to 10 minutes after regreasing. If the bearing has a noticeable drop in temperature, the bearing was likely starving for lubrication, and the regrease interval should be shortened.
In summary, when greasing, think about using the same or comparable and compatible grease, keeping dirt out of the grease and bearing, what type of bearing you are greasing, how much grease is needed, when the last time the bearing was greased and whether the bearing is running hot.
Dan Holdmeyer is retired from Chevron Lubricants and is based in Washington, Mo. You can reach him at dan.holdmeyer@gmail.com.