KEY CONCEPTS
•
Commercial oil analysis laboratories play a key role in the oil condition monitoring industry, but sensor technology and electrification have the potential to disrupt the status quo.
•
Oil sensor technology is expanding, but high costs and low buy-in have prevented it from significantly displacing the role oil analysis laboratories play in the oil condition monitoring industry.
•
Electrification, especially in the trucking industry, has a high potential to disrupt the oil condition monitoring industry because many commercial oil analysis laboratories focus on diesel engine testing.
In the 1940s, the railroad industry in the U.S. began inspecting the oil that lubricated locomotive engines. The inspectors were looking for contaminants—metals that could cause wear and lead to catastrophic engine failure. Nearly 80 years later, the industries that rely on oil analysis have expanded beyond the railroad, and so have the kinds of tests that the oil condition monitoring industry has to offer.
The goal of oil condition monitoring (OCM) has always been to avoid machine failure. “The OCM strategy is to use predictive maintenance to understand when a machine is going to fail so that we can do what we need to do to avoid any downtime,” says STLE member Lisa Williams, training manager at Ametek Spectro Scientific. From power generation and trucking to pulp and paper, a plethora of industries rely on maintaining healthy oil to continue their operations.
The OCM, or oil analysis, industry is the key to helping other industries monitor and prevent wear and sustain healthy oil in their equipment. Commercial oil analysis laboratories play a big role in this sustainment by running tests on oil samples, interpreting the results and suggesting maintenance actions. But two new technologies have the potential to displace these laboratories’ lead role in the OCM industry: sensors and engine electrification.
How exactly and when these two technologies will impact OCM is still unknown, but they have the potential to drastically change how OCM companies do business—from pushing them to develop new technologies or testing new kinds of fluids, to catalyzing merges and rendering services obsolete. Matthew Spurlock, global technical manager at SGS, says, “I don’t think that there’s going to be a significant impact on the standard oil analysis industry as it sits today for at least 10 years, but we’re going to get to that inflection point, and then it’s going to happen very quickly.”
Today’s oil condition monitoring landscape
Today, there are approximately 200 oil analysis laboratories in North America. The global OCM market is a billion dollar industry and is expected to grow to $1.4 billion by 2026.
1
Some companies provide in-house oil analysis, but many operate as a third-party vendor, providing services to a range of operations. The list of industries that the OCM market serves is long, as is the machines they service
(see Table 1).
Table 1. List of oil condition monitoring industries
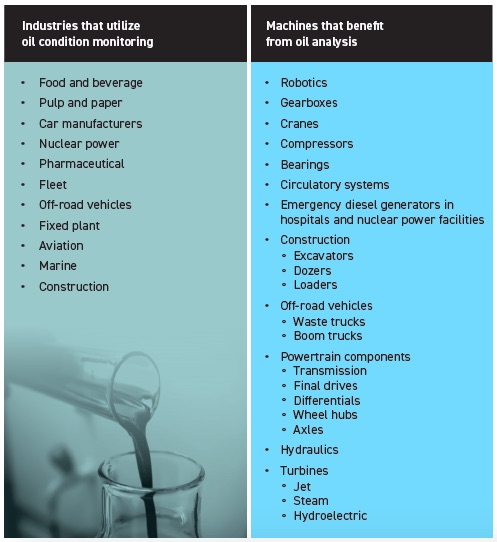
“OCM really starts with setting up a program within an organization,” says Williams. That organization could be a manufacturing facility or a truck depot. The oil analysis laboratory will work with its client to determine an oil sampling frequency of its equipment, which could range from a transmission or an engine on a vehicle to a steam turbine in a nuclear power plant. After determining the oil sampling frequency, a technician will start taking oil samples to gather data on the condition of that oil. Data collection can range from very minimal—for instance, testing the water concentration present in a steam turbine oil—to very complex, such as understanding the factors that are causing a particular wear pattern in an engine.
Williams says the average cost of an oil sample for routine maintenance is between $30 and $45, which is relatively inexpensive considering the benefit of avoiding machine failure. She says perhaps 20% of routine samples need additional testing to further diagnose a problem or troubleshoot an existing issue.
Though the advent of sensor technology over the past 20-25 years has mimicked the types of tests oil analysis companies can run, the latter list is still longer, although sensor capabilities are growing. Some oil analysis companies have dedicated time and money to developing sensor technology, or at least considered it, but a decline in demand for lab-run oil analyses due to increased use of sensors has yet to take place. Still, Bill Quesnel, president at WearCheck Canada, says, “Sensors have the opportunity to make a radical shift in our industry.”
Perhaps the more pressing technology for OCM companies is the move toward electric motors, especially as a replacement for internal combustion engines in diesel trucks. Because the over-the-road truck industry makes up a large subset of the oil analysis customer base, and because electric motors require different lubrication strategies, OCM companies have to consider how the industry will shift when electrification occurs.
With both of these technologies on the horizon, Spurlock says now is the time for companies to consider how their business models may shift in the coming years.
Sensor technology
Oil sensors first came on the analysis scene around 20 years ago as a way to automatically collect operation data in machines running on used oil. They initially measured simple characteristics to detect wear, like ferrous density. But the capabilities of sensors continue to grow. On top of ferrous testing, sensors can now measure characteristics like oil base number, soot, changes in viscosity, additive depletion, particle count and relative humidity, which can be correlated to moisture content.
But lab testing capabilities still outnumber sensor capabilities. Williams says an oil analysis company could offer a client 20 or more tests, which could include in-depth microscope work and an elemental analysis, something sensors can’t fully provide yet. And labs can offer exception or add-on testing based on initial testing results, such as measuring oxidation, nitration and corrosion.
Oil condition monitoring sensor that uses the dielectric constant to determine oil condition. Photo courtesy of Bill Quesnel.
But sensors have other advantages. For example, sensors can be particularly helpful when they are installed in difficult to reach areas, such as in a gearbox in a wind turbine. “Sending somebody up-tower quarterly may not be a reality, but if we have sensor technology installed, we can get that data,” says Williams.
Sensors also are used in other capacities. “What you do see is a lot of sensors on inboard engines, but in terms of OCM, those sensors are usually just using algorithms to determine oil condition life. They’re not directly measuring properties of the oil,” says Quesnel.
Another advantage of sensors: they can serve as red flags. “The big bang around sensors is their early identification of root causes of failure. They’re very good at that,” says Spurlock. Early detection of wear generation is important, but ideally a sensor would detect factors that are capable of causing wear before the wear occurs. Spurlock says the two most common things that cause internal machine wear are particles—usually dirt and debris—and moisture contamination. “So if we can capture those two key root causes of failure by identifying their presence and then do something about it, that’s where the big wins come into play.” Oil health monitoring sensors also exist, but because the majority of the root causes of failure are due to these kinds of oil contaminants, Spurlock says sensors that measure particle and water contamination are the most useful for the end-user.
Still, oil sensor use isn’t widespread and hasn’t drastically disrupted the oil analysis industry. “The big problem is that the cost for these sensors is still prohibitive for the original equipment manufacturers (OEMs)—the people who make the engines,” says Quesnel. “We were told at one point when we were trying to commercialize our own sensor that it would have to be $10 or less to make it into widespread production in a diesel engine. Some sensors out there today that would be useful for diesel engines are on the order of $1,000 or several hundred dollars.”
The sensor industry has yet to produce a low-cost, high-production versatile monitor that can directly measure oil condition, which has prevented widespread sensor use. The situation is somewhat of a catch-22: To drive down sensor costs, their production needs to increase, but production won’t increase until demand does, which is currently stymied because of high costs. “The key roadblock in adoption is 100% on the price,” says Spurlock.
Until that roadblock is surpassed, either from government subsidies, increased consumer demand or a commitment to large-scale production in order to decrease cost, sensors won’t likely make a significant impact on the OCM market. Even if costs do come down, Williams doesn’t think sensors will make the industry obsolete. “We’re still going to need people with expertise so that [end-users] know what to do with sensor technology,” she says. For example, she says a sensor may report that additive levels are low without diagnosing why or suggesting follow-up actions. Deciding whether to change the oil versus filtering it requires some understanding of what the data means and “that doesn’t come with sensor technology,” says Williams.
Automated data interpretation software does have the potential to replace oil analysis technicians. “But the reality is that a software becoming widespread that can analyze complex data without an expert is a ways off, and what is currently available is expensive,” says Williams. If or when software use becomes widespread, the industry may see a large shift in the kinds of jobs available—from oil technician to software developer. But the expertise of understanding complex changes in oil will still be required in some capacity. “The type of job in the industry has the potential to shift, but with cost being a big barrier, I don’t see it happening anytime soon,” says Williams. She thinks the industry would take a hybrid approach, coupling the technology with lab work.
When and if sensor technology causes a shift in the OCM market is a large unknown. When sensors were first developed two decades ago, there was a lot of interest and a global market for the technology, especially in the diesel engine industry. “The problem is, 20 years later, no manufacturer has decided they’re going to make a million sensors to get the cost down, and no company has decided they want to buy a million in order for somebody to make a million, to get the cost down. So it is a catch-22,” says Quesnel.
Electrification
Another factor that has the potential to disrupt the OCM market is engine electrification, particularly in large commercial trucks that travel long distances. Companies that monitor diesel engine oil comprise the bulk activity in the OCM market in North America. A switch to electric in over-the-road fleets would significantly impact large sections of the oil analysis industry. But it’s not there yet.
In contrast, passenger vehicle electrification is well underway. Last year, Boston Consulting Group estimated that sales of electrified cars will surpass 50% of the market by 2026,
2 replacing internal combustion engines. Although electrification of heavy trucks is still in its infancy, it has started to occur. OEMs have produced commercial electric semi-trucks and are currently testing their capabilities.
A factor that has the potential to disrupt the OCM market is engine electrification, particularly in large commercial trucks that travel long distances.
“What’s driving electrification of vehicles, especially in the commercial space for fleet trucking, is reduced cost of ownership. It’s number one,” says Quesnel. That cost of ownership depends on the market’s ability to overcome certain hurdles. Producing an efficient electric motor for a large truck traveling long distances has different obstacles than producing an electric motor for a passenger vehicle or a mid-size commercial truck. The former requires more power, which necessitates larger, heavier batteries. Even if the cost of the actual motors comes down, other factors will affect total cost, such as the efficiency of the charging stations and the infrastructure to support charging across long distances.
But many experts agree electrification is not a question of if but when. “The replacement of the internal combustion engine globally is certainly well on its way. Over-the-road trucks now have electric motors. Vehicles now have electric motors. Everything else that runs on an internal combustion engine is eventually going to be transitioned over to an electric motor. When that’s going to happen, I don’t know, but it will happen,” says Spurlock.
Some passenger car OEMs have already committed to phasing out internal combustion engines in their vehicles as early as mid-decade, says Quesnel. “Passenger cars are going to be the first wave, but electrification of large trucks is going to come soon after. I would say by 2040, we may see a rapid reduction in the amount of internal combustion engines on the roads in North America. It’s going to happen faster in Europe.”
But how much will engine electrification impact OCM companies? “That’s the million dollar question. Is there going to be a need for OCM? That’s the one on everybody’s mind,” says Quesnel. That’s because electric motors don’t require oil. They do need grease and fluid for cooling. And an electric vehicle will still require a transmission, although it’s lubrication may change as well. Williams says it’s these components that oil analysis companies will need to focus on in order to adapt, and Spurlock agrees that monitoring grease is just as important in preventing failure as monitoring oil.
But whether companies will want or need to monitor non-oil components is unknown. “There’s no market for it yet,” says Quesnel. “If these electric vehicles are extremely reliable and have low failure rates, or if the failures are not lubricant related, there will be no market.” He says OCM companies will need to figure out how the motors will fail and if those failures are lubricant related.
Currently, there’s no standardization in the OCM market for electrified trucks. Before that can happen, a list of questions will need answering. Will vehicles be outfitted with reduction gearbox differentials or single or multi-speed transmissions? Will electric motors be wet or dry? “We still don’t know what the look of the standard electric truck is going to be,” says Quesnel, and that will affect both the lubricants that will be required and how often they need to be tested. “The question is, are fleet owners going to view lubricant testing of an electric powertrain as important as lubricant testing of an internal combustion engine powertrain? That’s what remains to be seen.”
Quesnel says the oil analysis industry will need to wait and see what fluids and lubricants OEMs decide to use for their electrified vehicles and then design tests to detect and prevent failure. “I think we’re still sitting on the sidelines [knowing] electrification is going to happen. Now we’re going to wait to see how dependable electric vehicles are.” Quesnel says the industry can guess where areas of interest might lie. For example, transmission fluid, which currently comprises a small fraction of the OCM industry, could take on a larger share of oil analyses. For that to occur, “There has to be a shift from the consumer deciding that sampling transmission fluid is important. The only reason that will start to happen is if they experience costly failures,” says Quesnel.
Even if oil analysis labs shift to monitoring the types of fluids present in electric vehicles, other industries may be better poised to step into the role. For example, “Labs that specialize in insulating fluid condition monitoring are more akin to the fluid an electric motor will need,” says Quesnel. “I really don’t see that there is going to be a lot of OCM occurring for electric vehicles because I think they are going to have much higher reliability.”
Spurlock thinks electrification of the trucking industry will push many oil analysis companies to other markets that aren’t as immediately affected by the change, like the turbine, marine, aviation and fixed plant markets, which will increase competition in those industries. “I also think we’re going to see more merging of oil analysis companies,” says Spurlock. “I’ve said for a long time that any laboratory that is only focused on running oil samples in their lab and nothing else, their time is limited. They’ll be closing their doors I suspect within 10-15 years.”
One consequence of engine electrification in the OCM industry may be that electric motors can be fitted with more sensors because the kinds of sensors that electric vehicles may need, such as conductivity and heat sensors, already exist. But Quesnel says because existing OCM sensors are very specialized, they are unlikely to translate to electric vehicles, and the ones that electric vehicles will need are already available and cheap. “Onboard sensors tend to be very specific,” says Quesnel. “An onboard sensor on an engine will measure things like rapid viscosity drop, fuel elution, increased soot load or ingression by water and coolant. But with an electric motor and a transmission, the concern will be copper corrosion or excessive heat. They are worried about viscosity, but not as much. They are worried about low conductivity, high resistivity—things that current OCM sensors aren’t designed for.” But because low-cost sensors with these properties already exist, “This could herald a dominance of sensors in the OCM industry for electrified vehicles,” says Quesnel.
Sensors for grease may be an even more difficult sell. “It’s easy to put an oil sensor in the flow of oil because the oil is moving. Grease isn’t moving through a system the way oil is,” says Spurlock.
Still, Williams thinks that a move to sensor technology and electrification will require a skilled workforce. “We have to know how to manage those components. We have to know how to interpret our sensor data. And we have to know when to take action. If we don’t have those things, these more expensive technologies are going to be ineffective,” she says.
Where to go from here
So, what should oil analysis companies be doing today? “Some planning is good. It’s a matter of keeping an eye on the industry,” says Quesnel. “But until there’s some significant penetration in the market, [we won’t know] how our customers are going to react or what their requirements are going to be.” He says he’s seen companies make drastic changes to their operations to adapt to small industry changes. “But now we’re talking about a radical change in the industry.”
Spurlock agrees that a change is inevitable. “Many labs that aren’t forward thinking will continue doing business as usual, but if they don’t change what their approach is and what they’re willing to do after 10 years, it’s going to be too late.”
REFERENCES
1.
Available
here.
2.
Available
here.
Berly McCoy is a freelance science writer and producer based in Northwest Montana. You can reach her at kimberly.mccoy@westernalum.org.