Fluid sampling
Dan Holdmeyer, Contributing Editor | TLT Lubrication Fundamentals March 2022
This can derail the best fluid analysis program.
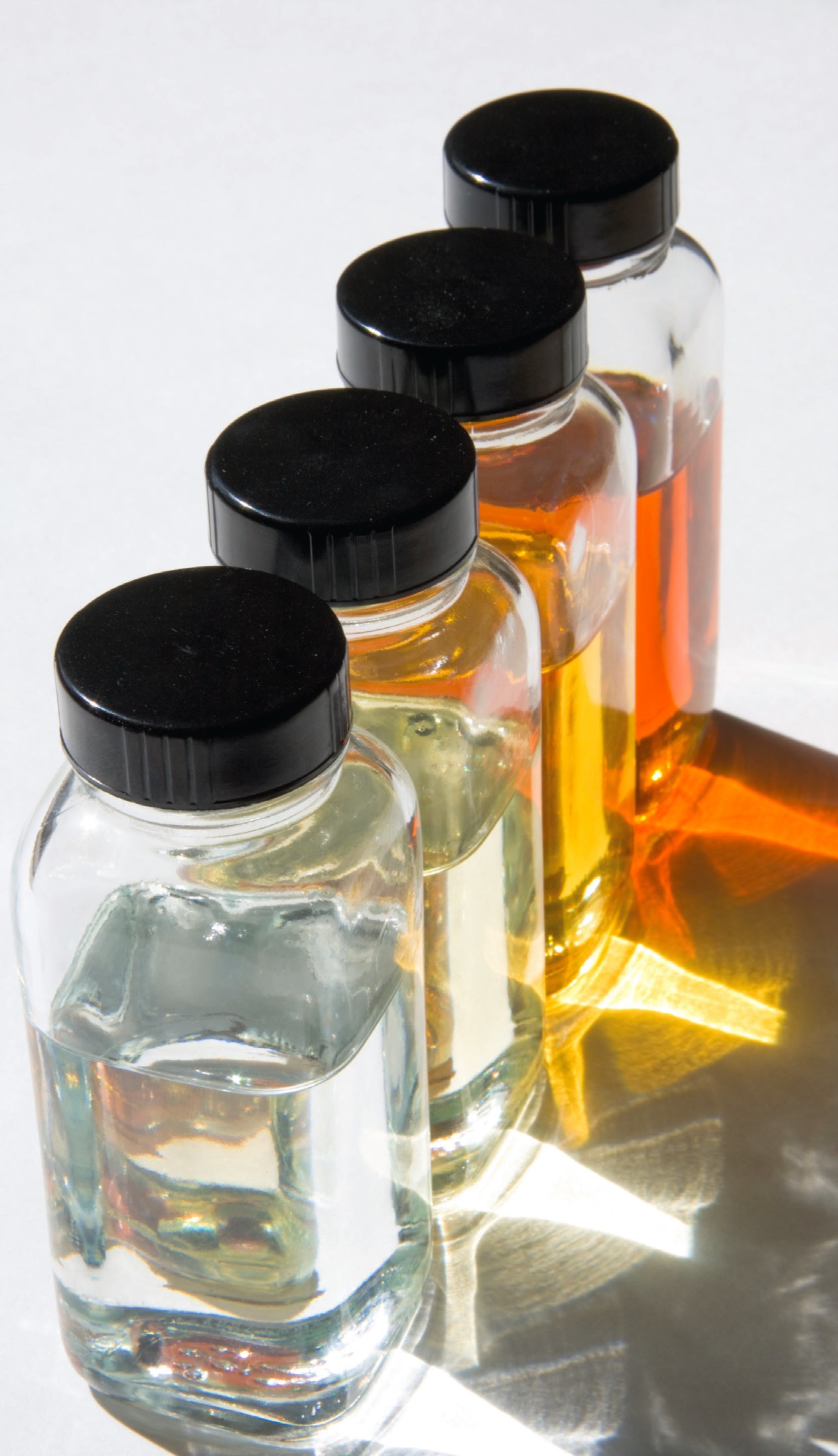
A well thought-out and planned fluid analysis program should be a key component of any successful preventive maintenance program. Planning and personnel training are critical to implementing a fluid analysis program, whether it is to extend oil drain intervals, maximize equipment life, reduce unscheduled downtime or any other maintenance or operational objective. Identifying the objective(s) will guide the decisions on what equipment to monitor and what test protocols are needed. Analysis interpretation education, along with management commitment to follow up and take corrective action, are ongoing challenges to most fluid analysis programs. Yet, with all this planning, commitment and interpretation, the analysis program may still fail with the first step of implementing it or taking the fluid sample.
A truly representative sample of the fluid in the lubrication system is needed to determine the condition of the fluid and the equipment. Realizing that typically a 3-4 ounce sample is taken from a system capacity of as little as a few to thousands of gallons emphasizes how critical it is to get a representative sample. Furthermore, the lab will use different portions of that sample for the various tests required in the protocol. Therefore, the sample should be drawn while the system is operational, or as soon as safely possible after shutdown, while all contamination and wear debris circulating in the system are still suspended in the oil and, thus, the sample.
In a circulating system, the sample should ideally be drawn while the system is in operation from a turbulent flow stream before it returns to the reservoir after lubricating critical components in the system, and not after the filter. A myriad of sample valves or ports are available on the market for use in tapping into low pressure, and even high pressure, turbulent flow streams. These are ideal for taking consistently representative samples but still require more than a “just grab a sample” technique. The sample port should be wiped clean before flushing out the sample port “standpipe,” or the “dead space” stagnate oil that has collected extra contamination and wear debris over time. This flushed sample should be discarded, and a fresh sample bottle should be used to collect a representative sample. Close the sample immediately after collecting the sample.
Non-circulating systems create more of a challenge in getting a representative sample. A popular method used for these systems is a vacuum pump where a tube is inserted into the system via a fill or dip stick port. This method involves system intrusion, which may introduce contamination from opening the system to insert the tube or from the tube scooping up some contamination from the ports while being “snaked” into the system. Additionally, if the tube reaches all the way to the sediment at the bottom of the system, erroneously high levels of contamination and wear particles will be reported in the analysis results. A common mistaken practice with this vacuum pump technique is to reuse the tube for several sample draws. To avoid cross contamination of samples, a new tube should be used for each sample drawn. If those pitfalls are avoided, the next challenge is to consistently pull a sample mid-oil level, which is most representative of the system oil.
It is very critical to consistently pull samples from the same point in the system. A good fluid analysis program monitors trends in the analysis to determine proper corrective action. However, if several samples are taken mid-oil level on one side of the sump and then the next sample is taken from another side that is less turbulent that naturally allows wear debris to drop out of suspension, the analysis results will indicate a normal condition while there may have been an increase in wear. This would be analogous to even though your thermostat keeps your house at the same relative temperature, you get widely varied temperature readings in the basement compared to the sunroom.
The drain-plug sampling procedure is used primarily in mobile fleet operations. Sample ports are generally used when samples are taken from the engine without draining, particularly when sampling to extend oil drain intervals. If drain-plug sample ports are used, the tube should extend to the mid-oil level from the drain-plug valve. For the most representative sample, wipe clean the drain-plug valve exterior and flush out the sample port “standpipe” or tube before collecting the representative oil sample with a new, clean sample bottle. The sample can be drawn with the engine running or immediately after engine shutdown.
A less than ideal sampling method is to wipe the drain plug exterior clean, remove the drain plug and “catch” a sample with a new, clean sample bottle from the oil drain stream after 1/3 to 1/2 of the sump is drained. This is a last resort but may be required if a sample port isn’t available. This sampling method is taken immediately after engine shut down to get the most representative sample.
In all these sampling methods, never take a sample from the bottom of the sump, the filter nor the filter housing. If the sample collection is missed during draining, do not dip a sample from the waste oil collection. Not only is that a waste of the oil analysis cost but can even be more expensive if corrective action steps are taken due to abnormal test results. Yes, it has been done. Fortunately, it is rare that corrective action is taken based on a single result as action plans are developed from trends in the analysis results. If, however, the “dip” sample analysis results are abnormal enough, and depending on the system, the unit may need to remain idled until a second sample is drawn and analyzed.
For good trend analysis, consistently sampling from the same location is important, and sampling at a consistent interval also is advantageous. Wear debris levels will vary greatly when sampled at a 100-hour service life interval versus a 500-hour interval. Iron wear metal levels that are normal at 500 hours of service are alarmingly high for 100 hours of service and are worthy of investigation. Imagine if your house thermostat is set up in the sunroom; the furnace or air conditioner will keep the rest of the house exceptionally cold during the day and excessively warm at night. Timing of sampling is critical to analysis of the results. Contamination levels also will vary if samples are taken before or after a filter change.
Counterintuitively, the sample bottle should not be filled to the top. Ideally the bottle should be filled somewhere between 2/3 full to about the “shoulder” (just below the neck) of the bottle. The laboratory needs to agitate the sample to assure the entire sample is again representative of the system fluid before drawing portions of it for the various tests, and this cannot be done if the sample bottle is filled to the very top.
Sampling supplies (bottles, tubing, valves, clean rags, etc.) should be kept in an enclosed storage area or somewhere away from dirt and dust. Sample bottle caps should remain on the bottle until the sample is ready for collecting to minimize airborne contamination and be immediately replaced after the sample is collected. Do not put the cap in your pocket while drawing the sample, as this will contaminate the sample.
We are not done yet! It is amazing to me to see some of the sample bottle labels that arrive in the lab without sufficient data. We’ve talked about the importance of how many hours of service is on the oil. It also is important to identify hours on the system, if the filter was changed recently and how much make-up oil has been added. This information helps interpret the results and determine if any corrective action is required. Even worse are samples that arrive without identifying the oil in the sample; sometimes the viscosity grade, or SAE, is not identified! Without this information, the analyst cannot say if the viscosity is off-spec, or if, for example, the oil should be an engine oil when the additives look like a gear oil. The make and model of the equipment along with the component sampled dictate wear metal alarm limits so the laboratory can flag abnormal levels for analysis and corrective action.
The equipment identification also is critical for developing trends in a system. A sample mislabeled “Compressor #1” will start a different sample analysis trend from the “#1 Compressor” data. Fortunately, most laboratories offer digitalized labeling processes, which includes bar coded or QR coded labels to help keep unit identification consistent. Then, just the supporting information like the hours or miles on the oil and unit, oil name, filter change and make-up oil need to be added to the label.
So, the sample site is wiped clean, a representative sample is drawn from the system while operating—from the same previous sample location, at the relatively same interval—the cap is tight on the bottle and the label is completed accurately with supporting data. Now is the time to send the sample to the laboratory. Do not delay. A lot of time and effort is invested in establishing an effective fluid analysis program, including painstakingly obtaining a representative and properly labeled sample, but timely corrective action may be catastrophically delayed if the sample is not shipped immediately.
Dan Holdmeyer is retired from Chevron Lubricants and is based in Washington, Mo. You can reach him at dan.holdmeyer@gmail.com.