Characterizing the velocimetry of viscosity modifier-containing lubricants in the elastohydrodynamic regime
Eliane Gendreau and Janet Wong | TLT Fellowship Research March 2022
Department of Mechanical Engineering Imperial College London, South Kensington Campus, London, SW7 2AZ, UK
Editor’s Note: This month TLT profiles the 2021 recipient of The Elmer E. Klaus Fellowship, Eliane Gendreau (Imperial College London). The Klaus Fellowship, along with The E. Richard Booser Scholarship, are awarded annually to graduate and undergraduate students, respectively, who have an interest in pursuing a career in tribology. As a requirement for receiving an STLE scholarship, students are given the opportunity to participate in a tribology research project and to submit a report summarizing their research. For more information on the Elmer E. Klaus Fellowship, visit www.stle.org.
Eliane Gendreau is a doctorate student at Imperial College London, Department of Mechanical Engineering, in the Tribology Group. Gendreau started her doctorate in 2018 under the supervision of Dr. Janet Wong. Her doctorate research focuses on the effect of polymer architecture on the performance of viscosity modifiers. Gendreau has developed a novel experimental platform allowing the in situ imaging of a ball-on-disc tribological contact. The project is funded by Shell University Technology Centre for Fuels and Lubricants. Gendreau can be reached at eliane.gendreau15@imperial.ac.uk.
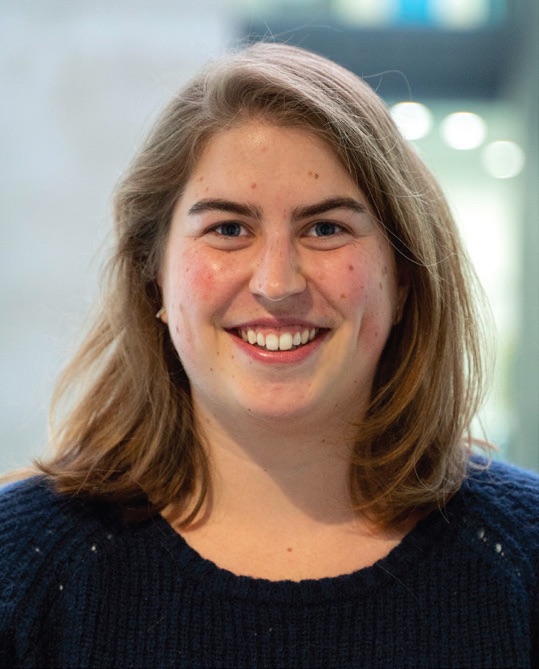
Eliane Gendreau
Introduction
Reducing friction in engineering components is at the heart of tribology at this time, for instance, to improve fuel economy in vehicles. Lubricants are a very effective tool to reduce friction, and their performance is enhanced using additives in their formulation, such as, to mention just a few, friction modifiers, antiwear additives, antioxidants and viscosity modifiers.
1
Viscosity modifiers are polymeric additives where the primary function is to increase the viscosity of lubricants. They improve the viscosity-temperature relationship while ensuring a good shear stability of the oil. They are widely used in engine lubricants, automatic transmission fluids, power steering fluids, industrial gear oils and aircraft piston engine oils.
1 For details on viscosity modifier additives functions, chemistries and mechanisms, the reader is referred to the review by Martini et al.
2
An interesting property of viscosity modifiers is that they can also play the role of friction modifiers.
3 Polymeric additives adsorbing on the contact surfaces form a boundary film that leads to a reduction in friction.
4 Recent studies in the boundary lubrication regime have proven that functionalized copolymers have the potential to be friction modifiers in addition to their use as viscosity modifiers.
4-6 In the elastohydrodynamic (EHD) regime, another mechanism leading to friction reduction observed with viscosity modifier-containing lubricants is shear-thinning.
7 Shear-thinning can be detrimental in some applications as it causes a lower film thickness and viscosity; however, a lower friction is favorable for fuel economy.
Another well-known way of reducing friction is through slip of the liquid at the contact surfaces. Choo et al.
8 developed a low load tribometer and concluded from experiments conducted using n-hexadecane and different contact surfaces that the lower friction results were most likely linked to slip. Fillot et al.
9 proposed an improved numerical model including nanoscale slip for the modeling of EHD lubrication, and obtained lower friction compared to the classical friction prediction that assumes no slip. Friction reduces when slip occurs as slipping surfaces cannot transfer as much momentum to the fluid as in the no-slip case; thus, the shear stress is lower.
10, 11
This work investigates the presence of slip for viscosity modifier-containing lubricants in a tribological contact in the elastohydrodynamic lubrication regime. Such polymer systems are good candidates in terms of slip as previous research showed that confined polymer solutions exhibit slip under certain conditions.
12-14 Many experimental techniques have been developed to observe slip, including particle image velocimetry,
15, 16 photobleached-fluorescence imaging velocimetry,
17 particle tracking velocimetry
18 and marker lines.
19 In this study, a phosphorescence imaging velocimetry technique was used. This
in situ and real-time technique allows access to the through-film velocity profiles of tribological contacts.
20 Interfacial slip is characterized by a discontinuity between the fluid velocity and the surface velocity at the surface; therefore this phenomenon can be detected in flow profiles.
17
Methodology
The tribological contact was a ball-on-flat contact under high-shear and high-pressure conditions. The flow profiles of polymer solutions were investigated for different concentrations and solvents. The main challenge for this experiment was the intensity of the dye phosphorescence. The film thickness for the polymer solutions was small, less than 300 nm, and as thinner films give lower phosphorescence intensity, the signal-to-noise ratio was low.
The experimental setup is shown in Figure 1. It consisted of a tribological ball-on disc contact with a microscope built on top of it. The experimental platform, an EHD1, was used to carry out the experiments in the elastohydrodynamic regime, where the two contact surfaces elastically deform and are fully separated by a thin film of lubricant. The ball was immersed in the lubricant and loaded against the disc. The entrainment speed and slide-to-roll ratio were controlled, as well as the temperature of the lubricant and the load. The lubricant was doped with dye molecules, and excited with a short pulse (<5 ns) from a 349 nm laser. A hall sensor on the disc was used to trigger the laser so that the laser pulse was always hitting the contact in the same position for each rotation of the disc. This created a spot where the intensity of the light emitted by the excited dye was then captured over time with a EMCCD camera. From these images, the phosphorescence response was known as a function of time and position. The first image was taken 2 μs after the laser pulse to make sure that only phosphorescence, and no fluorescence, was captured. The through-film velocity profiles were reconstructed from the intensity distributions over time.
20
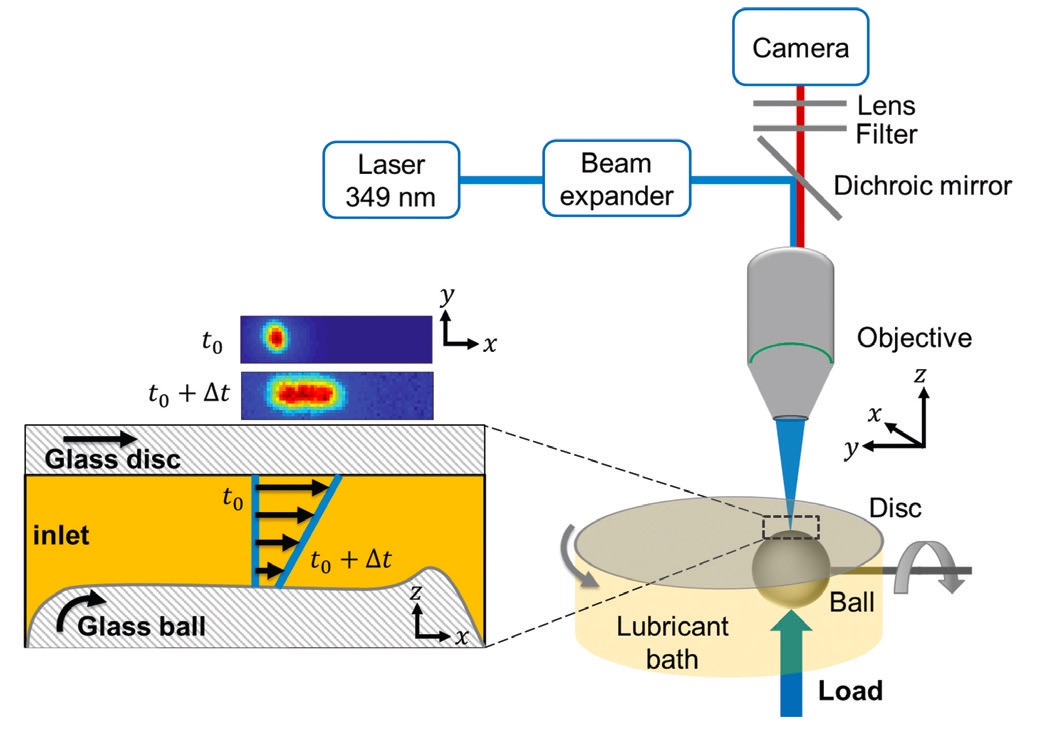
Figure 1. Schematic of the phosphorescence spectroscopy setup, with a zoomed-in representation of the ball-on-disc contact in the elastohydrodynamic regime on the left-hand side, in which the blue lines represent the initial column of excited dye molecules after the laser excitation at t0 and how they would spread after a short time Δt in the case of a Couette flow. An example of phosphorescence images is shown above the contact.
To illustrate the flow of lubricants under no-slip boundary condition, Figure 2 shows two examples of through-thickness velocity profiles u(z), along with the phosphorescence images and corresponding normalized intensity distributions, obtained in pure rolling and pure sliding conditions, respectively, for a polymer solution and a polyphenyl ether, 5P4E. A fluid under pure rolling conditions that obeys the no-slip boundary condition does not experience any shearing.

Figure 2. Phosphorescence images, normalized intensities and velocity profiles. The first image is taken as the time reference. The dashed line in the velocity profile corresponds to a Couette flow. (a) DOP + 4.8 wt% PS (Mw=192k Da), pure rolling, Pmax=271 MPa, Ue=0.3 m/s, T=14 C. (b) 5P4E, pure sliding (ball faster), Pmax=188 MPa, Ue=0.072 m/s, T=25 C.
In Figure 2a, note that the shape of the excited spot does not change; all the molecules in the through-film column excited by the laser pulse travel at the same speed. The velocity of the fluid is the same as the velocity of the two contact surfaces (relative velocity of 1 throughout the thickness of the film), which means that the system is not experiencing interfacial slip.
When shearing 5P4E under pure sliding conditions
(see Figure 2b), the spot on the first phosphorescence image is circular, and then stretches as the fluid is sheared, as seen on the subsequent images. The intensity of the stretched spot is relatively uniform along the flow. This is characteristic of a Couette flow, i.e., a linear distribution of velocities between the two contact surfaces. This is consistent with the literature which showed that 5P4E has a near-Couette flow profile under these conditions.
20 Since there is no slip, the velocity of the liquid at the proximity of the walls is the same as the speed of the walls.
Results
This phosphorescence imaging velocimetry technique was used to investigate the behavior of polymer solutions. The polymer chosen was polystyrene (PS), of a molecular weight of 192k Da. PS has been extensively studied and is commercially available for a wide range of molecular weights. The solvents used were two phthalate esters, dibutyl phthalate (DBP) and dioctyl phthalate (DOP). These systems were chosen as phthalate esters are good solvents for polystyrene, and they are common systems found in the literature, their viscometry was studied21 as well as their behavior under shear. Kume et al.
22 showed that when a solution of a high-molecular weight PS in DOP is under shear, PS molecules align with the flow. Marx et al.
23 found that under severe shear conditions, PS molecules in phthalate esters undergo permanent shear thinning and degrade, leading to a drop of the solution viscosity. Previous works on phthalate esters and polystyrene suggest that these systems are good candidates to observe slip. Grzelka et al.
24 studied the slip behavior and interfacial friction of PS in diethyl phthalate (DEP). They sheared a drop of the polymer solution between two substrates and measured the slip length using a photobleaching technique. Note that the shear rate experienced by the fluid was relatively low, below 1 s
-1.
In our study, we propose to investigate the behavior at much higher shear rates, in the range of 10
6-10
7 s
-1, which is commonly encountered by lubricants. Two solutions were prepared with a concentration of PS of 9.9 wt% in DBP and 4.8 wt% in DOP, to ensure a sufficient viscosity and film thickness in the tribological contact. Table 1 shows the characteristics of our test solutions. The low-shear dynamic viscosity was measured using a SVM 3000 Stabinger viscometer, and the film thickness was measured by optical interferometry using a EHD2 rig. It is noticed that while having a higher viscosity, the DBP+PS solution has a lower film thickness in the tribological contact at 0% SRR than the DOP+PS solution. The film thicknesses were also measured at other SRR, up to a SRR of 180%. At the entrainment speed of 0.3 m/s, no noticeable difference was found compared to the value measured in pure rolling.
Table 1. Polymer solutions characteristics
The velocimetry experiments were carried out at room temperature and under pure sliding conditions, where the disc is stationary and the ball rotates. Figure 3 shows the phosphorescence images and the reconstructed velocity profiles for pure DOP
(see Figure 3a) and for the two polymer solutions
(see Figures 3b and 3c).
No slip is observed for DOP
(see Figure 3a) and DOP+PS
(see Figure 3b). In both cases, the velocity of the fluid at the surfaces is the same as the velocity of the surfaces. On the other hand, the DBP+PS solution
(see Figure 3c) exhibits a clear slip at both contact surfaces. The velocity profile shows that at the proximity of the stationary disc surface (relative position is 0), the relative velocity of the fluid is not zero; at the ball surface (relative position is 1), the relative velocity of the fluid is less than 1, i.e., the fluid moves more slowly than the ball. It can be noted that the average velocity of the solution is higher than the relative entrainment speed which is 0.5, as slip occurs more at the slower surface (the disc). This supports the observations that the film thickness of DBP+PS is reduced.
25
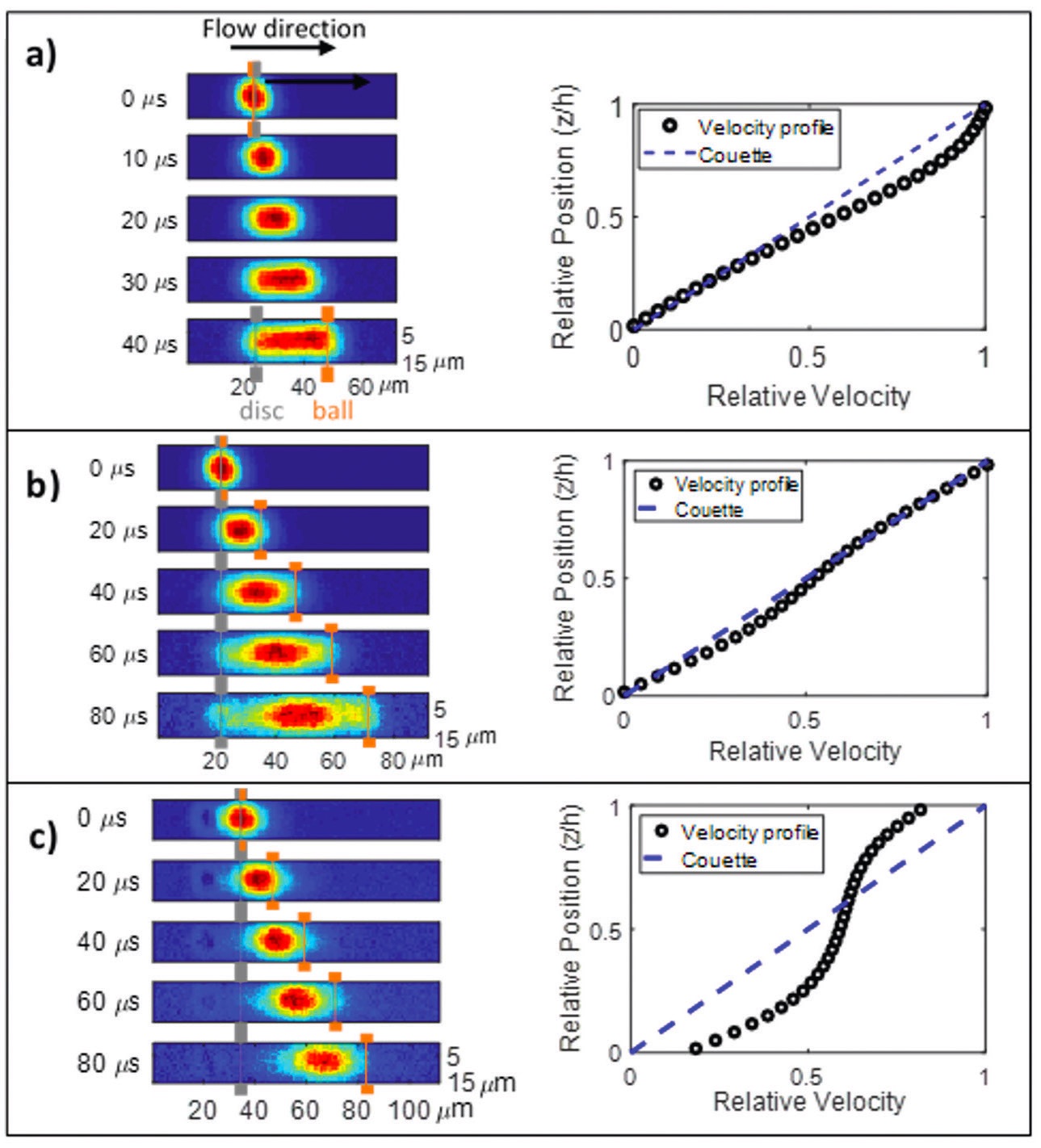
Figure 3. (a) DOP, (b) DOP + 4.8 wt% PS, (c) DBP + 9.9 wt% PS. Phosphorescence images and velocity profiles. The first image is taken as the time reference. Grey lines and orange lines represent the position of the disc and the ball, respectively. Dashed lines in velocity profiles correspond to a Couette flow. All three tests are done in pure sliding, with Pmax=188 MPa, Ue=0.3 m/s and T=25 C.
The question arises as to why one system, DBP+PS, gives slip, whereas the other two solutions, DOP and DOP+PS, do not. One possible slip mechanism is depletion, in which the solute goes away from the wall, creating a gradient in the polymer concentration and, thus, in the viscosity through the thickness of the film.
12 However, this mechanism is very unlikely to be at play here, as Grzelka et al.
24 have showed that for their DEP+PS system, the friction coefficient at the wall strongly depends on the polymer volume fraction, ruling out the possibility of a depletion layer at the wall.
Knowing this, coupled with the fact that the DBP+PS solution has a higher viscosity, it can be inferred that this solution slips at the wall because it experiences a higher shear stress, leading to more slip than for the solution DOP+PS. Another possible reason is that DBP+PS might have more mobility at the surface, as the molecules of DBP are smaller than the molecules of DOP. A higher mobility at the surface promotes slip.
26
Note that DOP and DBP may interact with the surface (as suggested by their no-slip flow profiles), even though they may have different adsorption strength. Since the molecule of DBP is smaller than DOP, PS may displace adsorbed DBP more readily than adsorbed DOP. This implies that the solid-liquid interface may be different in the two cases. A higher concentration of polymer
24 and a higher polymer surface coverage
27 might facilitate slip.
Conclusions
Interfacial slip of polymer solutions in the elastohydrodynamic regime was investigated by a phosphorescence imaging velocimetry technique which allowed
in situ observations of flow behaviors at the microscopic scale. Velocity profiles of DBP+PS and DOP+PS were successfully reconstructed from phosphorescence images of the tribological contact. Both DBP and DOP obey the no slip boundary condition and give Couette flow profiles, while slip is only observed with DBP+PS. Possible explanations for the difference of behaviors between the two polymer solutions were proposed, though more work is needed to discriminate the effect of the solvent and the effect of the polymer concentration. Future work will include the exploration of other possible reasons for the low film thickness, as well as the study of the impact of pressure and film thickness as they play a role in slip
9 and flow profiles.
28
Acknowledgements
The authors would like to thank STLE for the generous support provided by the Elmer E. Klaus Fellowship. Eliane Gendreau is funded by the Shell University Technology Centre for Fuels and Lubricants at Imperial College London. The authors would like to acknowledge Dr. S. Jeffreys for the training and support on the experimental setup.
REFERENCES
1.
Mortier, R. M., Fox, M. F. and Orszulik, S. T. (2010),
Chemistry and technology of lubricants, Springer.
2.
Martini, A., Ramasamy, U. S. and Len, M. (2018), “Review of Viscosity Modifier Lubricant Additives,”
Tribol. Lett., 66 (2), pp. 1-14, doi: 10.1007/s11249-018-1007-0.
3.
Spikes, H. (Oct. 2015),“Friction Modifier Additives,”
Tribol. Lett., 60 (1), p. 5, doi: 10.1007/s11249-015-0589-z.
4.
Guangteng, G., Smeeth, M., Cann, P. M.and Spikes, H. A. (Mar. 1996), “Measurement and Modelling of Boundary Film Properties of Polymeric Lubricant Additives,”
Proc. Inst. Mech. Eng. Part J J. Eng. Tribol., 210 (1), pp. 1-15, doi: 10.1243/PIME_PROC_1996_210_473_02.
5.
Fan, J., Müller, M., Stöhr, T. and Spikes, H. A. (Dec. 2007), “Reduction of friction by functionalised viscosity index improvers,”
Tribol. Lett., 28 (3), pp. 287-298, doi: 10.1007/s11249-007-9272-3.
6.
Gmür, T. A., Mandal, J., Cayer-Barrioz, J. and Spencer, N. D. (Dec. 2021), “Towards a Polymer-Brush-Based Friction Modifier for Oil,”
Tribol. Lett., 69 (4), p. 124, doi: 10.1007/s11249-021-01496-w.
7.
Marx, N., Fern ndez, L., Barcel , F. and Spikes, H. (2018), “Shear Thinning and Hydrodynamic Friction of Viscosity Modifier-Containing Oils. Part II: Impact of Shear Thinning on Journal Bearing Friction,”
Tribol. Lett., 66 (3), pp. 1-11, doi: 10.1007/s11249-018-1040-z.
8.
Choo, J. H., Glovnea, R. P., Forrest, A. K. and Spikes, H. A. (Jul. 2007), “A low friction bearing based on liquid slip at the wall,”
J. Tribol., 129 (3), pp. 611-620, doi: 10.1115/1.2736704.
9.
Fillot, N., Berro, H. and Vergne, P. (Sep. 2011), “From continuous to molecular scale in modelling elastohydrodynamic lubrication: Nanoscale surface slip effects on film thickness and friction,”
Tribol. Lett., 43 (3), pp. 257-266, doi: 10.1007/s11249-011-9804-8.
10.
Savio, D., Fillot, N., Vergne P. and Zaccheddu, M. (Apr. 2012), “A model for wall slip prediction of confined n-alkanes: Effect of wall-fluid interaction versus fluid resistance,”
Tribol. Lett., 46 (1), pp. 11-22, doi: 10.1007/s11249-011-9911-6.
11.
Savio, D., Fillot, N., Vergne P., Hetzler, H., Seemann, W. and Morales Espejel, G. E. (Jul. 2015), “A multiscale study on the wall slip effect in a ceramic-steel contact with nanometer-thick lubricant film by a nano-to-elastohydrodynamic lubrication approach,”
J. Tribol., 137 (3), doi: 10.1115/1.4029937.
12.
Barnes, H. A. (Mar. 01, 1995), “A review of the slip (wall depletion) of polymer solutions, emulsions and particle suspensions in viscometers: its cause, character, and cure,”
Journal of Non-Newtonian Fluid Mechanics, 56 (3). Elsevier, pp. 221-251, doi: 10.1016/0377-0257(94)01282-M.
13.
Cuenca, A. and Bodiguel, H. (Mar. 2013), “Submicron flow of polymer solutions: Slippage reduction due to confinement,”
Phys. Rev. Lett., 110 (10), p. 108304, doi: 10.1103/PhysRevLett.110.108304.
14.
Guyard, G., Vilquin, A., Sanson, N., Jouenne, S., Restagno, F. and McGraw, J. D. (Apr. 2021), “Near-surface rheology and hydrodynamic boundary condition of semi-dilute polymer solutions,”
Soft Matter, 17 (14), pp. 3765-3774, doi: 10.1039/d0sm02116d.
15.
Tretheway, D. C. and Meinhart, C. D. (Mar. 2002), “Apparent fluid slip at hydrophobic microchannel walls,”
Phys. Fluids, 14 (3), pp. L9-L12, doi: 10.1063/1.1432696.
16.
Joseph, P. and Tabeling, P. (Mar. 2005), “Direct measurement of the apparent slip length,”
Phys. Rev. E - Stat. Nonlinear, Soft Matter Phys., 71 (3), p. 035303, doi: 10.1103/PhysRevE.71.035303.
17.
Ponjavic, A. and Wong, J. S. S. (May 2014), “The effect of boundary slip on elastohydrodynamic lubrication,”
RSC Adv., 4 (40), pp. 20821-20829, doi: 10.1039/c4ra01714e.
18.
Boukany, P. E. and Wang, S. Q. (Feb. 2009), “Exploring the transition from wall slip to bulk shearing banding in well-entangled DNA solutions,”
Soft Matter, 5 (4), pp. 780-789, doi: 10.1039/b804791j.
19.
Plucinski, J. Gupta, R. K. and Chakrabarti, S. (Jun. 1998), “Wall slip of mayonnaises in viscometers,”
Rheol. Acta, 37 (3), pp. 256-269, doi: 10.1007/s003970050113.
20.
Galmiche, B. Ponjavic, A. and Wong, J. S. S. (2016), “Flow measurements of a polyphenyl ether oil in an elastohydrodynamic contact,”
J. Phys. Condens. Matter, 28 (13), doi: 10.1088/0953-8984/28/13/134005.
21.
Hua, C. C. and Wu, M. S. (Mar. 2006), “Viscometric properties of dilute polystyrene/dioctyl phthalate solutions,”
J. Polym. Sci. Part B Polym. Phys., 44 (5), pp. 787-794, doi: 10.1002/polb.20739.
22.
Kume, T., Hashimoto, T., Takahashi, T. and Fuller, G. G. (Nov. 1997), “Rheo-optical studies of shear-induced structures in semidilute polystyrene solutions,”
Macromolecules, 30 (23), pp. 7232-7236, doi: 10.1021/ma9705984.
23.
Marx, N. Ponjavic, A. Taylor, R. I.and Spikes, H. A. (Sep. 2017), “Study of Permanent Shear Thinning of VM Polymer Solutions,”
Tribol. Lett., 65 (3), pp. 1-15, doi: 10.1007/s11249-017-0888-7.
24.
Grzelka, M., Antoniuk, I., Drockenmuller, É., Chenneviére, A., Léger, L. and Restagno, F. (May 2021), “Slip and Friction Mechanisms at Polymer Semi-Dilute Solutions/Solid Interfaces,”
Macromolecules, 54 (10), pp. 4910-4917, doi: 10.1021/acs.macromol.0c02804.
25.
Wang, P. and Reddyhoff, T. (2017), “Wall slip in an EHL contact lubricated with 1-dodecanol,”
Tribol. Int., 113, pp. 197-205, doi: 10.1016/j.triboint.2016.10.034.
26.
Blake, T. D. (Jan. 1990), “Slip between a liquid and a solid: D.M. Tolstoi’s (1952) theory reconsidered,”
Colloids and Surfaces, 47 (C), pp. 135-145, doi: 10.1016/0166-6622(90)80068-F.
27.
Ewen, J. P., Kannam, S. K., Todd, B. D. and Dini, D. (Apr. 2018), “Slip of Alkanes Confined between Surfactant Monolayers Adsorbed on Solid Surfaces,”
Langmuir, 34 (13), pp. 3864-3873, doi: 10.1021/acs.langmuir.8b00189.
28.
Ewen, J. P., Gattinoni, C., Zhang, J., Heyes, D. M., Spikes, H. A.and Dini, D. (Jul. 2017), “On the effect of confined fluid molecular structure on nonequilibrium phase behaviour and friction,”
Phys. Chem. Chem. Phys., 19 (27), pp. 17883-17894, doi: 10.1039/c7cp01895a.