TLT: What were your interests at the post-graduate and doctorate levels?
Mohan: I have always been interested in developing new materials as a passionate metallurgist. In my post-graduation, I started working on aluminum-silicon (Al-Si) alloys and found problems of failure starting at the tip of large primary silicon particles in hypereutectic side. I could change the nature of silicon particles by modification in the casting procedure, and the failure load could be increased. This work was published in Zeitschrift für Metallkunde (International Journal of Materials Research). It encouraged me to work on development/modification of materials with an application-oriented approach. Though, I joined industry for two years after my master’s degree but returned back to join research. I initiated my work on aluminum-lead (Al-Pb) composites to have a solid lubrication effect in tribological applications. The project was successful from a tribological aspect, and the work was published as research articles in Zeitschrift für Metallkunde, ASM International Proceedings, Wear, Materials Sci. & Eng., with citation of articles even in ASM Metals Handbook.
TLT: How long have you worked in a tribology-related field, and how did you decide to pursue research in this area?
Mohan: It is almost 34 years since I started in this field. As already mentioned, I had been passionate about new materials, but since my doctorate days, I focused basically in a tribological area. I have been working both on ferrous and nonferrous material from tribological aspects, but my focus has been on Al-based materials.
TLT: What has been your most rewarding accomplishment throughout your career in the tribology industry?
Mohan: Initially, I started working with solid lubricants, but later I switched over to tribology under dry conditions. As a metallurgical tribologist, it was important for me to explore how to minimize wear and friction or enhance friction by changing material composition, microstructure, distribution of second phase particles, particle size range from nano to micron, average size of particles, particle shape, etc. There are large numbers of factors which affect the properties of a final product. Alloys have a limitation of properties, whereas, in composites, the properties can be tailored as per need. With this idea, I started working on composites with different routes to achieve uniformity in distribution of particles. In 2012, we started work on
in situ composites using inorganic compounds in stoichiometric ratio. This work was on tribology of aluminum alloys dispersed with ZrB
2 or ZrB
2+Al
3Zr in different volume percents. Studies were conducted at ambient and high temperature. Interesting wear and friction results with volume percent of particles and size of particles increased the working range of applied loads and sliding velocities. However, at high temperatures, working temperature range is slightly squeezed. Results showed that this material could be a good alternative for clutch and brake applications. This work was published in ASME Journal of Tribology, Tribology International, etc.
TLT: What is the No. 1 piece of advice you would give to a person who might be interested in starting a career in the tribology industry?
Mohan: I recall an old quote of Rigney et al., 1984,
1 where he describes the situation of wear as a complex jigsaw puzzle in which pieces fit together here and there, but the overall pattern is far from clear. The situation has changed much in the last 35 years, but still lots of complexities are unanswered. We may consider a large number of variables affecting tribological phenomena, but from time to time, such situations arise that make us feel that we still know a little. There is lot of work to be done for the newcomers in this field. The scope is enormous.
TLT: Throughout the different segments within your career, which one has been the most interesting, challenging and/or rewarding?
Mohan: I remember the most interesting and challenging period was my doctoral research period. I hardly had any knowledge of tribology at that time, the field was totally new, and even minimal literature was available in my institution. It was not the period of the internet. So to have literature and basic knowledge of the subject, I had to move around. With the literature review, I decided to work on Al-Pb composites. It had a monotectic system, which means hardly any solubility of the constituent present at both the ends. Further, it also had a wide difference in density of constituent present and fabrication was almost impossible with conventional methods. Initially, heats were taken with a stirring apparatus, but the results were a complete failure as there was no mixing of lead in aluminum. It was important to study the mixing behavior, but due to experimental limitations, it was not possible to study the actual system. Hence, I decided to choose a system with a wide density gap. Finally, I modeled a system with a stirring arrangement to mix bromoform and mercury to understand its mixing behavior at ambient temperature. That made me understand that mixing of two species with large density difference was not possible just by stirring. This gave me an idea of using a baffled system for proper mixing, which helped in successful development of Al-Pb composites.
Sunil Mohan working on a multi-function tribometer (MFT).
TLT: Describe your contribution to the institute and your present area of interest toward sustainable tribology.
Mohan: In the last few years, I also have started working in erosion. One project has been completed on high-temperature solid particle erosion of type 446 stainless steel. In this study, erosion tests were conducted to evaluate the behavior of AISI 446 SS at a higher temperature. It addresses this aspect by using Response Surface Methodology (RSM). RSM is a multivariate technique based on the fit of a polynomial equation to statistical data, with an objective to simultaneously optimize the levels of these variables to attain the best system performance. To approximate a response function to experimental data, Central Composite Rotatable Design (CCRD) was used. Artificial neural networks (ANN) offers an alternative to the polynomial regression method as a modeling tool. Advances in computing power have enabled the application of ANN in providing nonlinear modeling for response surfaces and optimization. Studies were performed varying the temperature, impingement angle and velocity. This study deals with the synergistic effect of hot-corrosion enhancing the solid particle erosion behavior in heat exchangers.
Further, another project is on tribology of polymer matrix composites using hemp fiber. My future plan is to develop sustainable and environment friendly material for tribological applications. In this direction, I have already contributed an article to an Elsevier publication.
Sunil Mohan analyzing the data from an MFT.
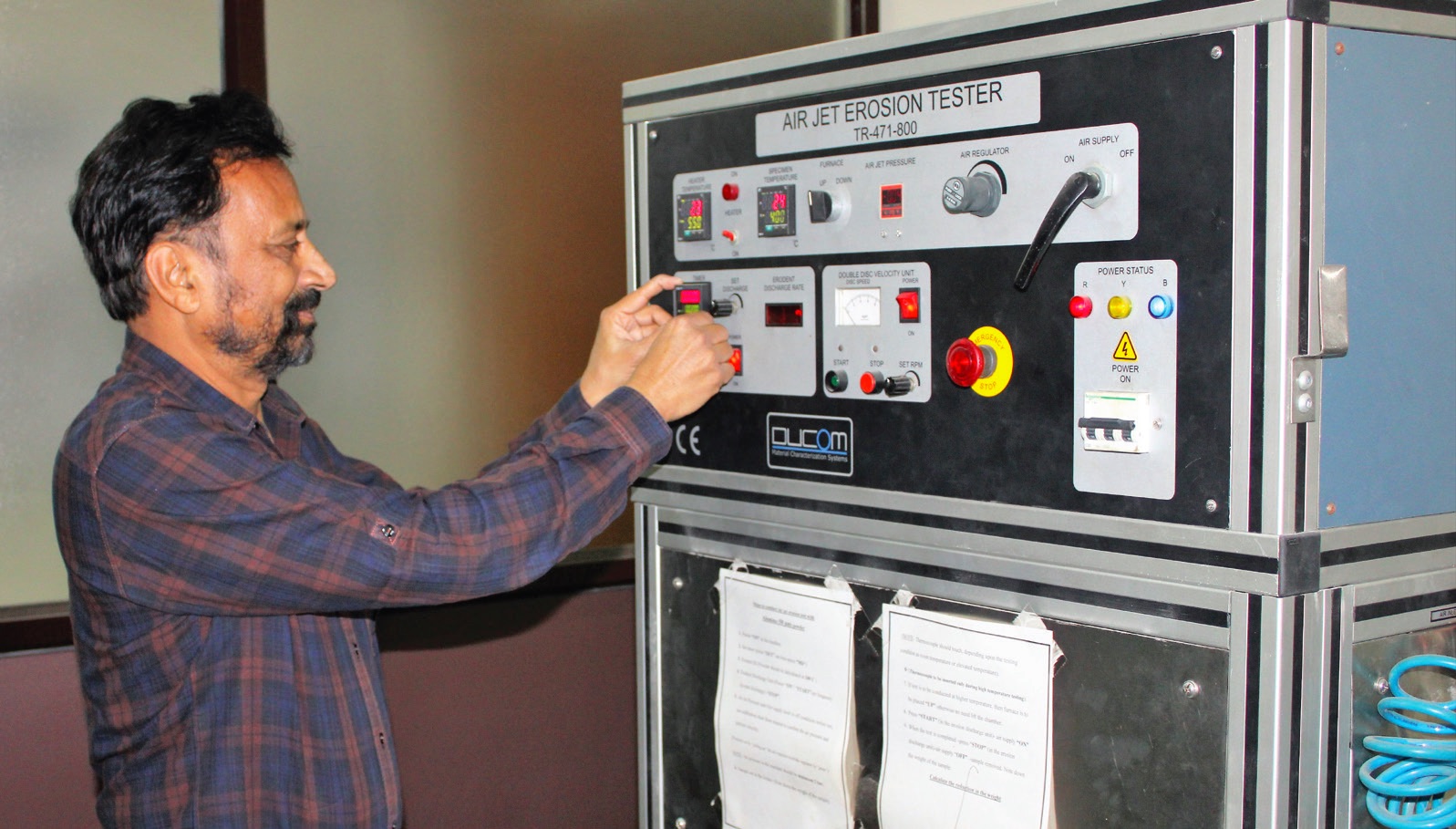
Sunil Mohan working on an air jet erosion tester.
TLT: What is the one thing you wish you would have learned earlier in your career?
Mohan: The designing aspect is definitely the one. With a change of material, especially when we wish to minimize fuel consumption, the weight reduction is a must. Once we replace materials like steels/cast iron with lighter ones, many times the design alterations also are important—for example, if vehicles have packaging limitations that do not allow increased driveshaft diameter. This is important in trucks and large passenger vehicles, where a two-piece driveshaft is sometimes used because of length restrictions. In such situations discontinuously reinforced aluminum (DRA) offers a solution. A two-piece steel driveshaft can be replaced by single-piece DRA driveshaft, which has reduced weight and also saves supporting weights, and it also is cost effective.
You can reach Sunil Mohan at smohan.met@iitbhu.ac.in.
REFERENCE
1.
Rigney, D. A., Chen, L. H. and Naylor, M. G. S. (1984), “Wear processes in sliding systems,”
Wear, 100, pp. 195-219.