The basics of lubricant water contamination
Dan Holdmeyer, Contributing Editor | TLT Lubrication Fundamentals January 2022
Steps taken after water contamination is identified depend on the type of product and its intended use.
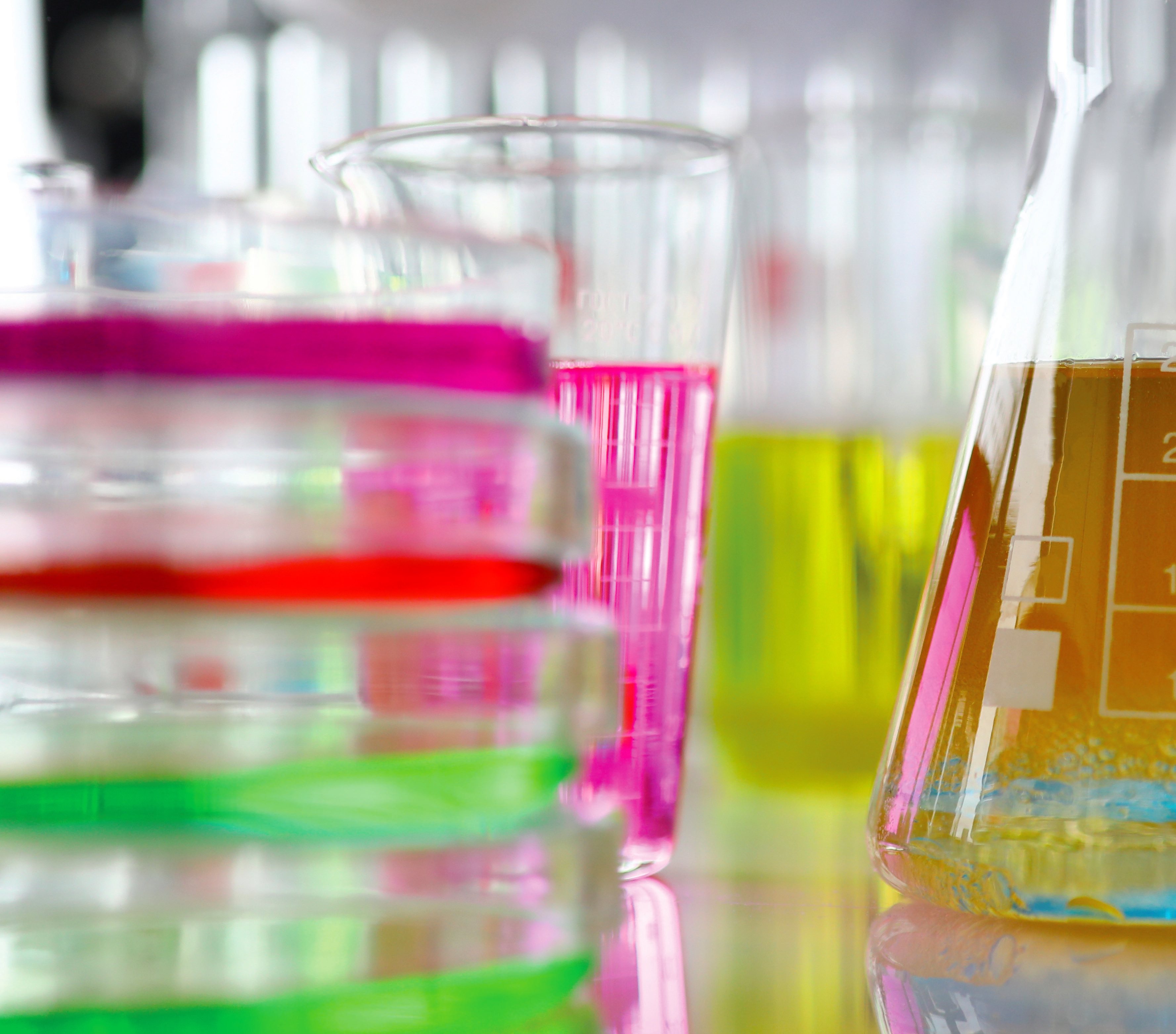
Water contamination in lubrication systems result in many issues with your equipment. It is a poor lubricant; it accelerates lubricant degradation and promotes rusting of ferrous parts. Water contamination in your oil compromises the lubricant’s protective film, thus allowing undue wear and resulting in shortened life expectancy. In certain operating conditions, the high pressures generated in the load zones of rolling element bearings can break the water molecules into its two atoms, hydrogen and oxygen. The hydrogen then can be absorbed onto the surface of bearing raceways, resulting in hydrogen embrittlement leading to premature bearing failure.
Besides these effects on machine components, water contamination also affects oil degradation. Many of the metals in the machinery the lubricant is protecting, such as copper and iron, act as catalysts in oxidizing the lubricant, reducing the life of the lubricant in your system. Additionally, certain additives such as antiwear, extreme pressure and phenolic antioxidants additives are readily hydrolyzed by water, compromising additive effectiveness and the creation of acidic byproducts. These acidic byproducts raise the acid level in the oil and can cause corrosive wear. Other additives, such as detergents, dispersants and rust inhibitors, can be quickly consumed with water in the lubricating oil.
Water contamination will present itself in your lubricant in three phases. One phase, dissolved water, is not visible. Dissolved water in a lubricating oil is typically brought in by moist air being absorbed into oil. Depending on the oil, the temperature and the atmospheric pressure, oil may contain 6%-12% air, and depending on the air’s humidity, varying amounts of dissolved water is in your oil. Many industrial lubricant applications, such as hydraulics, turbines, gears, etc., allow 100-600 ppm of water (0.01%-0.06%) so long as the water remains in the dissolved state, or below the oil’s saturation point for its temperature and the system pressure. Saturation point goes up with increased oil temperature.
Additional water, beyond the saturation point percentage, added to agitated or circulated oil will create an emulsion of microscopic water droplets in the oil, and the oil will appear cloudy or hazy. Emulsified water is much more detrimental to a lubrication system than dissolved water, and, thus, the water content should be kept below the saturation point for the oil type and temperature, typically 100-300 ppm or less.
If given enough time to rest unagitated, most industrial oils in an emulsified phase will “drop out” the water. Typically, layers of free water, free oil and preferably no layer of emulsified oil and water, or least a minimal emulsion layer, form. The free water will be on the bottom and the oil at the top.
In many cases, emulsified water contamination is relatively easy to detect by haze or suspended water. Where doubt exists, a simple “crackle” test, in which a small amount of the oil is placed in a shallow dish and heated to the boiling point of water on a hot plate, provides a positive identification of water. The crackle test (no ASTM number) is a quick and practical field test for qualifying gross water contamination of greater than 500 ppm and typically will not detect dissolved water.
The primary laboratory test used to quantify parts per million of water contamination is the Karl Fischer test (ASTM D1744). The test can indicate water content from 50 to 1,000 ppm.
The amount of free water is easily estimated by observing the height of the free water layer versus the free oil layer. Don’t waste time and money sending an oil sample with free oil at the bottom to the laboratory for analysis. Drain the free water from your system.
When water contamination has been identified, the steps that can be taken depend on the type of product and its intended use. Most industrial oils are designed to demulsify water so the free water can be drained from the system. This is most effective after an overnight, or over-the-weekend, machine idle time, draining the water before starting up the system again. If the machine is in continuous service, the oil charge can be removed and placed in a gravity separation system that allows the oil to cool, lowering the saturation point, and allows the free water to drop out of solution so the oil charge can then be recycled versus disposed. Large lubrication system reservoirs, like those of steam turbines, are designed large enough to give time in the reservoir for the oil to cool and drop out the free water. The reservoirs utilize baffles inside to prevent the oil from flowing straight from the oil return line to the circulation pump inlet line.
If the water contamination continues to overwhelm the gravity separation method in place, other methods of water removal may be required. Removal via centrifuge, or absorption removal by specifically designed filter media, speeds up the water removal process but only takes out emulsified and free water. Centrifuge and absorption removal processes have limited capacity and are generally used in an offline circuit, often referred to as a kidney loop.
Vacuum dehydration, or dehydration by air stripping, removes emulsified water, free water and dissolved water plus other low-boiling liquid impurities such as fuels and solvents. The removal of dissolved water is quite often necessary where large charges of oil are exposed to water due to the process or system—for example, lubrication systems in hydro-electric plants, paper mills and steam turbines. Air stripping or vacuum dehydration can remove water to less than 100 ppm water contamination. These have limited capacity also.
Unlike most industrial oils, engine oilsdo not have demulsifying additives. Detergent and dispersant additives are critical engine oil additives that hold water contamination in emulsion. Fortunately, engines run hot enough to evaporate any water contamination. However, you still need to know if you have water contamination, particularly water contamination from the cooling system. Hence, to detect an engine coolant leak, the oil analysis lab looks for unique coolant additives versus water in the oil sample because the water will likely be evaporated.
Whenever water contamination in a lubricant system is discovered, the source of the contamination needs to be identified and eliminated. Some common sources of contamination are system washdowns with high pressure water, open reservoir fill points, cooler leaks, other leaky seals and even improper handling.
Dan Holdmeyer is retired from Chevron Lubricants and is based in Washington, Mo. You can reach him at dan.holdmeyer@gmail.com.