TLT: Tell us about your work.
Wiley: Well, QualiChem has business in both the metalworking industry and the water treatment industry. I serve primarily as the head of marketing for the metalworking division. The owners and upper management at QualiChem were very strategic in their growth plans for the metalworking business, dating back to 2004. They focused on addressing market needs across the U.S., Canada and Mexico, when possible, selling through a network of distributors. After several years of fast-paced growth domestically, QualiChem was ready to start exporting their success outside of North America. I was initially brought on board to help develop Asia and Europe.
Seven years of navigating regulations, building brand awareness, finding distributors, localizing products and processes and supporting end-users has led to operations in China and Germany and customers all over both Asia and Europe. Our focus is quality and technology, and this often leaves us as one of the higher priced options in most markets, so it’s extra important that we understand the customers’ unique needs and/or wants. No matter where in the world an industrial plant may be, the machines, materials, tooling, the fixturing, etc., are largely all the same. Differentiation comes from people, culture, language and the nuances in communicating that these elements bring. Understanding this, and applying it, is what I do from a macro perspective.
TLT: What machining processes are giving manufacturers the biggest gains in productivity?
Wiley: Interesting question. From my perspective, as a metalworking fluids supplier serving a broad range of industry segments, I would suggest that there are two manufacturer types who each realize gains differently. Production facilities: high volume, limited product variation; and contract facilities: small volumes, wider product variation.
In the production facilities, we are seeing customers gain the most when they are stabilizing processes at a high level of productivity. What leads to the productivity gains here? In these facilities, we are often asked to help deliver a solution for the expanded use of high-pressure systems for coolant and cutting oil. Today, 1,000 psi is common, with more shops moving into pressures exceeding 2,000 psi. Higher pressures allow for more effective chip formation, removal of chips from the cutting zone and better delivery of the coolant or cutting oil into the work zone.
The need for high pressures comes, in part, from new drill technologies paired with very capable and programmable high-pressure pumps. The medical industry, for example, has made tremendous productivity gains from the combination of advanced machines, drills, pumps and cutting oils, on materials like titanium, cobalt chrome and 17-4 PH stainless. Ultimately this is all about shortening cycle times and eliminating secondary operations.
Another big boost in productivity has come from more companies selecting the right machines for the parts that need to be produced. This helps preserve the shop’s floor space but also helps eliminate steps and secondary operations in the process and lots of associated handling. Why produce on two dozen Swiss-style screw machines what you can produce on three multi-spindles? Why do on two machines what can be done on one mill-turn?
It’s important for us as a fluid supplier to remain engaged with the companies that are producing tomorrow’s machines, tooling and accessories. When possible, we look for opportunities to codevelop solutions, but, at the very least, we try to remain informed about advancements that can impact metalworking fluid selection, application, life span, compatibility with workpiece and machine components and maintenance.
From a developmental perspective, the productivity gains that the medical, aerospace and electronics industries seek present a great opportunity to implement new metalworking fluid technologies. Fluids that are cleaner running and lower consumption have extended useful service life, all while delivering a targeted set of characteristics for a production environment. An innovative supply chain working closely with formulators can keep fluids an integral component in high production machining, grinding and forming applications.
The productivity gains that the medical, aerospace and electronics industries seek present a great opportunity to implement new metalworking fluid technologies.
For contract facilities or job shops (as many are called), productivity gains are important, too, just as they are for production shops. While these shops have access to the same machines, tooling and accessories, their metalworking fluid priorities may not always be centered on reducing cycle times and extending tool life. Having coolants and cutting oils that are easy to use without a dedicated maintenance department, safe to use on a variety of metals and plastics and in a variety of machines and application types without bothering the operators or health, safety and environmental (HSE) managers—these are their metalworking fluid priorities.
TLT: What areas of metalworking do you see growing the fastest and the slowest?
Wiley: These are interesting times for a question such as this. There’s been so much dramatic change in the past 24 months affecting short- and long-term growth and trends. There have been so many industries impacted by the pandemic and global economic lockdowns.
The fastest trends in metalworking technology are automation and other technologies that remove or limit the need for human intervention in any process—using robots to feed machines with raw materials and tooling, using computers to pre-mix and maintain metalworking fluid systems and using optics for 100% quality inspection. The adoption of robotics has become affordable enough that it’s no longer limited to production lines.
I first started seeing robots in small-to-medium sized shops in the Netherlands back in 2012, because it was then already quite expensive to employ a person to do repetitive tasks in and around a machine tool. Considering the impact that labor shortages continue to have, I suspect that robotic-assisted manufacturing will continue to be a growth area for metalworking.
Additive manufacturing is another area of rapid growth. I think by a more traditional or purist definition, metalworking probably doesn’t include 3D printing and other additive manufacturing techniques. Or maybe this is just my personal feeling about a technology that comes with significant implications for producers of metalworking fluids. Will additive manufacturing replace cutting, grinding, forming and rolling? No, not entirely, not in my lifetime, not in my opinion.
Additive technology has developed quickly in the past decade, but cost, cycle times and material density and strength will all need to improve before additive manufacturing displaces traditional metalworking. With so many potential benefits, such as part designs not possible from other methods of manufacturing, eliminating the waste associated with traditional manufacturing and producing parts that require less or no cleaning after manufacturing, additive manufacturing will continue a fast-paced growth.
Switching from technology to a more macro look at industries, the fastest growing will be segments that are participating in the transition to electrification. Cars, trucks and heavy industries will all eventually be run on batteries, or it would seem that’s where we are headed. Fossil fuel-powered engines and the corresponding drivetrains and components, the production of which represents a large portion of the metalworking fluids consumed globally, will be replaced by electric motors. The entire automotive industry is, of course, significantly impacted by the current supply chain disruptions, availability of steel and aluminum, computer chips and other inputs.
Aerospace development in printed engine blades, lighter composite materials and more fuel-efficient designs will always be moving forward, even when the airline industry has been struggling with ups and downs in demand. From a metalworking fluids perspective, the aerospace industry represents an important growth opportunity. The increased use of nickel alloys, titanium alloys and advanced aluminum alloys means more manufacturers who need metalworking fluids that can provide the necessary multi-metal protection and demanding range of performance requirements.
Going tangent from the original question, aerospace as an industry, primarily commercial, also represents one of the metalworking fluid industry’s greatest competitive, regulatory and compliance challenges for the future. Standards for material compatibility varies from one aerospace company to the next. With some manufacturers, there are no compatibility requirements; with others, they can be numerous. Add to that the list of global chemical registries, REACH and other assorted regulations, and the list of fluids suited to a global aerospace supply chain will be very small with little room for differentiation.
TLT: Looking down the road, what are any other trends that you see in metalworking?
Wiley: There will always be the trends that include new tooling materials, new tooling designs, new fixturing concepts, new lubricants, more capable machines and new variants of all the other inputs into the metalworking process. But I would like to mention two exciting trends I see that lay outside the product and processes of metalworking.
First, over the past four or five years, there has been an explosion of garage-based, micro-manufacturers. Entrepreneurs with ideas, who have taken their savings, invested in a starter level computer numerical control (CNC), learned how to program and started making parts. They make custom putters, flashlights, knives, firearm accessories, personal grooming products, pencils, pens, replacement handles for manual windows, sprockets for mountain bikes and all sorts of other widgets.
Some of these shops have grown from one machine in a rented storage unit to companies with over 100 machines. And you can watch all of this happen on social media. Instagram is filled with these manufacturing entrepreneurs proudly displaying their craftmanship. Aluminum parts with a highly reflective surface finish win you big internet points.
Second, and I think more importantly, is the increase in the call for driving your people toward a career in manufacturing, a career that does not necessarily require a college degree in engineering, chemistry or metallurgy. I’m talking about the more traditional trade school programs but with a curriculum for machinists.
I recently had the chance to visit Danville Community College’s Precision Machining Laboratory, located in Danville, Va. Danville’s facilities are amazing. They have a five-semester program starting students with the fundamentals of manual machining and concluding with programming CNC mills and lathes
(see photos).
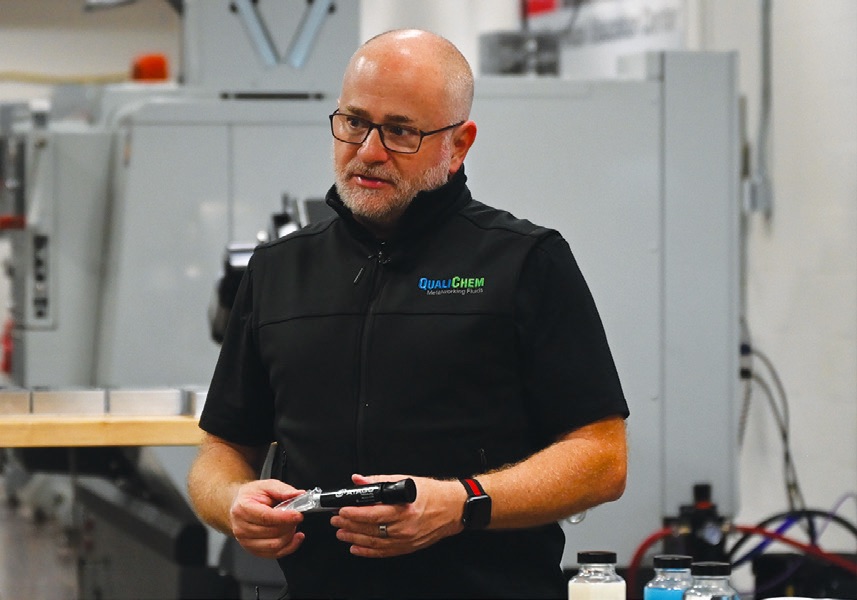
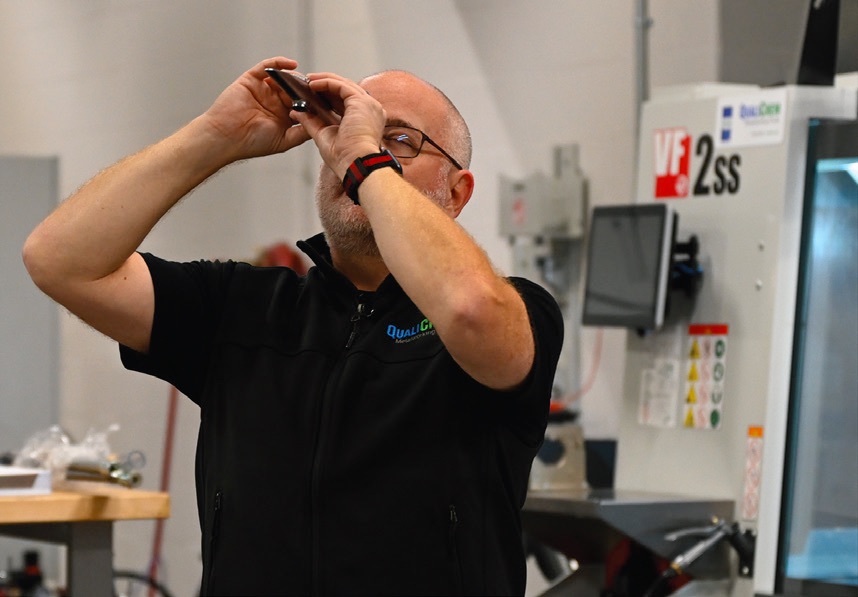
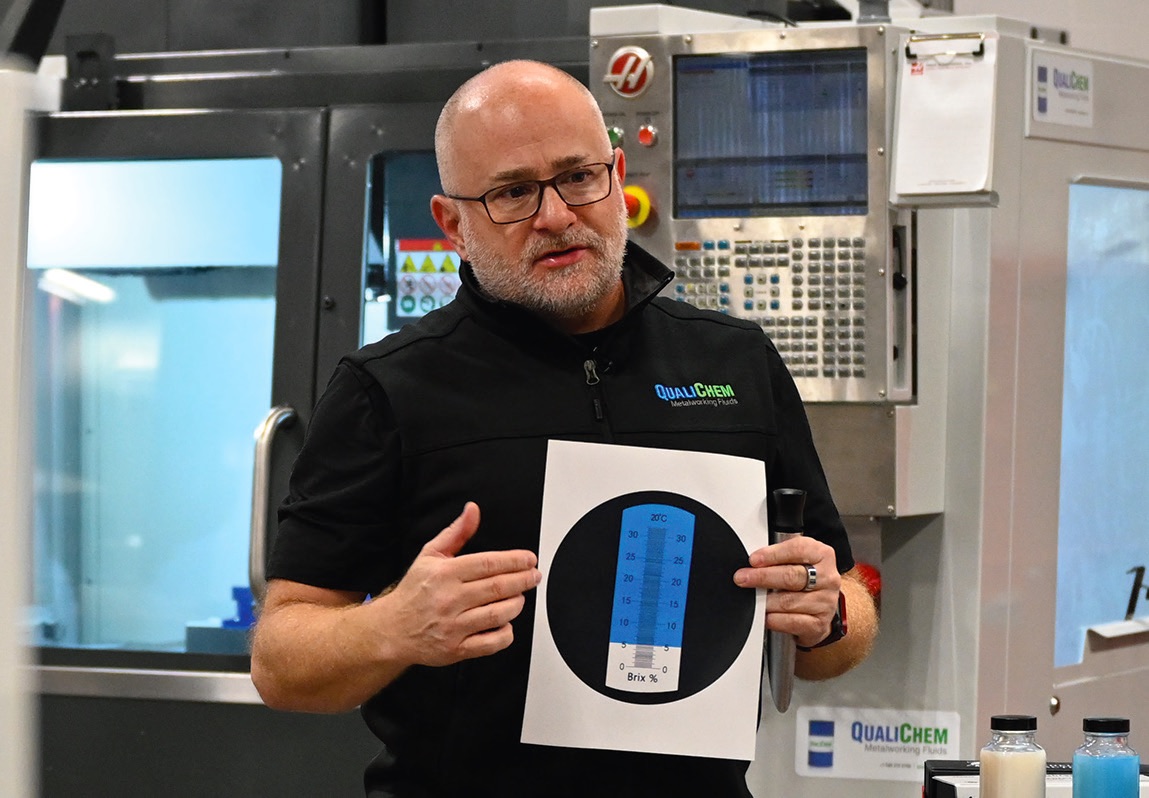
John Wiley teaching about the use of a refractometer at Danville Community College in Danville, Va. (a) Wiley with a refractometer in hand, (b) using the refractometer and (c) holding up an example of the Brix scale they will see when looking into a refractometer.
Everywhere I travel, companies are looking for good, qualified CNC programmers and operators, or people who can make parts from a print. These are good paying jobs and highly transferable skills. It was nice being able to talk with some of the students and learn about their motivations for enrolling in the program. Whether you want to be your own boss making widgets in your garage or working for a larger company making widgets, the trends in metalworking careers seem bright.
You can reach John Wiley at jwiley@qualichem.com.