The Lubrizol Corp.
How Lubrizol Develops Industrial Lubricants in a Sustainable Way
By Derek Newbould and Shubhamita Basu, PhD | TLT CMF Plus November 2021
In a recent report
1, the United Nations defined sustainable development as “development that meets the needs of the present without compromising the ability of future generations to meet their own needs.” That’s why companies like Lubrizol that develop products consider sustainability to be essential. When they are developing lubricant technologies, whether for the automotive or industrial applications, sustainability remains a leading consideration for Lubrizol’s technology and product management teams.
Lubrizol’s formulators use life cycle assessment (LCA) to ensure products deliver the required performance by producing in a safe, efficient and responsible manner that minimizes the carbon footprint and preserves and protects natural resources. In this article, we want to take a closer look at the importance of using LCA, what Lubrizol’s technologies bring to the table and how these different technologies—products of low environmental impact and energy-efficient performance polymers—help improve the sustainability of industrial lubricants including hydraulic fluids, industrial gear oils (IGOs) and open gear lubricants (OGLs).
Why Now?
It has become increasingly clear that sustainability isn’t something one company or even one country can do alone. In fact, there is a growing consensus throughout the world that building a more inclusive future for the people and the planet is essential to its survival. Additionally, the COVID-19 pandemic has prompted companies to ask themselves how they can recover in a more environmentally sustainable way. Regulation around sustainability is increasing globally, as a result of heightened social awareness and pressure from constituents on their local politicians to enact laws and policies that drive more sustainable actions. Everywhere you look, sustainability is in motion.
Sustainability in the Lubricants Industry
Stakeholders across the lubricants industry know that sustainability is a vital driver to the long-term growth of their organizations and an opportunity to bring about long-term global change. That’s why, at Lubrizol, we don’t simply develop products in a vacuum. Instead, we use
life cycle assessment when developing new technology.
LCA is the factual analysis of a product’s entire life from a sustainability standpoint. With an LCA, the environmental effects of a product or service are evaluated from raw material extraction through disposal or recycling. This prevents burden-shifting between different phases of a product’s life cycle and measures other categories that factor into sustainability while minimizing opportunities to focus too closely on one factor over another. In other words, Lubrizol’s product development team has the tools and skills to develop products that are truly better for the environment. Using LCA helps the industry develop products and solutions that bring positive impacts to the environment and society that outweigh the footprint it takes to produce them. This allows companies to engage both suppliers and customers as we support each other in meeting our environmental goals. LCA helps bring sustainability to the forefront alongside product performance and cost.
In order to discuss sustainable lubricant development, it’s important to understand the terms used. Two terms regularly used when discussing sustainability are footprint and handprint.
Simply stated, environmental
footprint is the effect that a person, company, activity, etc., has on the environment; for example, the supply of natural resources that they use and any environmental impacts measured in carbon dioxide (CO
2) equivalents.
The positive impact of our products in use is referred to as our
handprint. Extending our reach and maximizing our handprint by providing products and solutions that meet and exceed our customers’ and consumers’ performance and sustainability goals are the focus of our product and technical teams.
Approaches to Developing Sustainable Industrial Lubricants
Development of sustainable industrial lubricants will have to be intentional. At Lubrizol, we use three broad approaches: designing products with low environmental impact, use of energy efficient performance polymers and development of additive packages to extend the drain interval. While we aim to improve our handprint through our products, we are committed to ensuring that our sustainable products meet or exceed industry and original equipment manufacturer (OEM) credentials and performance requirements.
Designing Products with Low Environmental Impact
The use of products with low environmental impact are on the rise with increased regulations and environmental awareness. While many different classes of products can be covered under this category, biolubricants are the most important product category. Biodegradable hydraulic fluids are the most popular sub-class of biolubricants commonly used in sensitive areas like forestry and waterways. Environmentally Acceptable Lubricants (EALs), the most coveted of all biodegradable hydraulic fluids, have demonstrated biodegradability, minimal aquatic toxicity and non-bioaccumulative potential and use biobased raw materials.
Many criteria need to be met in order to create an EAL and the best-in-class EALs balance performance credentials along with environmental requirements. Lubrizol has been working in this field and has developed Lubrizol® 5686EL, an ashless hydraulic additive package for synthetic esters specially developed to meet stringent environmental requirements of EU Ecolabel. Lubrizol 5686EL is listed on the LuSC
2 list and can be treated at 1.25 wt% to offer exceptional performance credentials. The finished fluids, Lubrizol® 5687, 5685 and 5689, cover three key viscosity grades—ISO 32, 46 and 68, respectively—and offer an easy way to enter the biodegradable hydraulic fluid market. These finished fluids meet the specifications or have been approved by leading pump OEMs, environmental agencies, and industry bodies
(Table 1). In fact, Lubrizol is among the few companies with commercial fluids approved by the USDA BioPreferred for 10 years.
Using Energy Efficient Performance Polymers
The use of energy efficient performance polymers in hydraulic fluids, IGOs and OGLs can help us create sustainable solutions across the gamut of industrial products. Formulations with these polymers can increase productivity, reduce energy consumption and decrease CO
2 emissions.
Unlike automotive applications, there is neither a CAFE standard for energy efficient hydraulic fluids nor testing protocols to define energy efficiency. In the absence of a standard testing protocol, Lubrizol has developed a 4-step strategy to create an energy efficient hydraulic fluid including bench tests, rig tests, controlled field evaluation and proof of performance in real-world field tests. Through these series of evaluations, an energy efficient hydraulic fluid formula was developed that showed consistent efficiency gains without impacting reliable performance and the results were scientifically proven and statistically validated.
The hydraulic fluid formulation to increase efficiency without compromising durability uses Lubrizol® 5703 as the performance additive package and LUCANT™ as the energy efficient performance polymer. This LUCANT based energy efficient hydraulic fluid showed diesel fuel savings of up to 2.7% when tested in a field trial using heavy-duty mobile equipment. In addition, when tested in a plastic injection molding machine this formula allowed for an 8.5% reduction in electricity usage. Such reduction in electricity or fuel usage can be translated into a significant reduction in CO
2 emissions and a tangible sustainable solution.
LUCANT is a unique class of engineered performance polymers with superior thickening efficiency and exceptional shear stability. Because of its unique architecture, it can reduce traction coefficient and increase energy efficiency while reducing secondary flow losses. Furthermore, LUCANT shows improved thermal and oxidative stability and is NSF H1 approved.
LUCANT can also be used in formulating both IGOs and OGLs. Synthetic IGOs formulated typically with polyalphaolefin (PAO)—base oil and thickeners—are used in applications where higher performance is essential; however, such synthetic IGOs can often be expensive. LUCANT can be used in combination with PAO base oil to formulate synthetic IGO. Because of its superior thickening efficiency, LUCANT based IGO offers a cost-effective formulating approach with improved temperature reduction properties. Compared to a conventional IGO in mineral oil, such LUCANT based synthetic IGO can run 17 °C cooler with 16% reduction in electricity consumption when tested in the FZG rig,
Fig 1.
Fig 1: LUCANT based synthetic IGO runs 17 °C cooler compared to mineral oil based IGO as tested in a proprietary FZG test
Additionally, LUCANT based OGLs run 21 °C cooler compared to mineral oil based OGL in the same test described above along with 20% energy savings. In a field trial conducted in a sugar mill, the LUCANT based OGL ran 10 °F cooler than the incumbent OGL which ran hotter even with water cooling and led to severe wear damage,
Fig. 2. Another plus point of LUCANT based OGL was its clear appearance which helped expedite the cleaning process which wasn’t the case for the incumbent OGL.
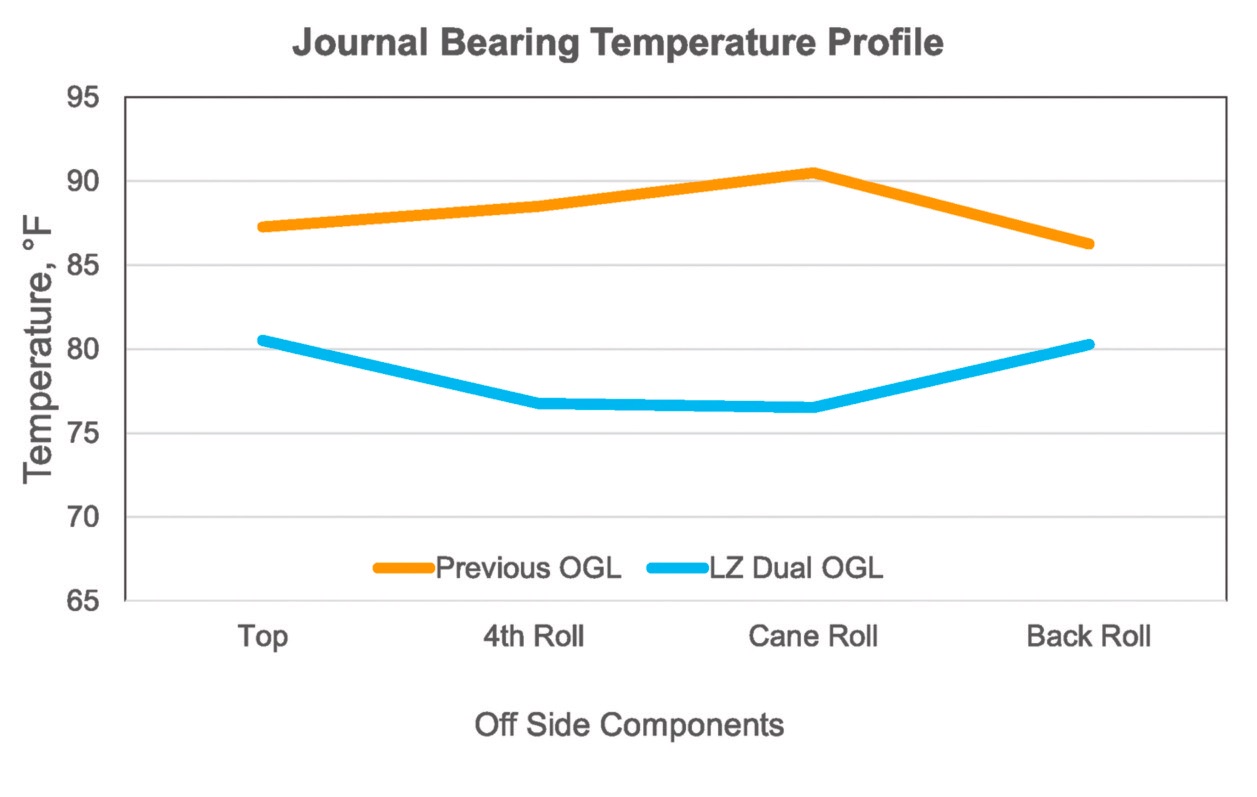
Fig 2: LUCANT based OGL ran cooler without the need for water cooling
In short, IGOs and OGLs with LUCANT ran cooler and offer extended gearbox durability, which means longer time between replacement of oil and equipment. With less waste, operations become more sustainable over the long haul.
What the Development of LUCANT Means to You
As lubricant manufacturers move forward designing products, it is important that they make sure they take the entire life cycle into account. Companies that focus on both footprint and handprint when designing sustainable products will have a clear advantage over others that focus on only one aspect of sustainability. Increased use of performance polymers like LUCANT in product development can help them create sustainable industrial products with relative ease.
There are three different LUCANT grades possible: HC-600, HC-1100 and HC-2000. These polymers are globally available and can be used in applications like hydraulics, IGOs and OGLs, and the performances are scientifically-proven and statistically-validated.
At Lubrizol, formulators use sustainability as the central design parameter and are dedicated in developing sustainable solutions beyond those described here. Through its technology initiatives, Lubrizol is committed to grow its positive impact in the society. For more information about the importance of incorporating sustainability in the development of industrial lubricants and how Lubrizol is rising to meet these challenges, contact your Lubrizol representative today.
References
1: “Our Common Future: Report of the World Commission on Environment and Development”. UN Documents. n.d. Web. click
here.
2: LuSC List: Lubricant Substance Classification List