Controlling particle contaminants
Jeanna Van Rensselar, Senior Feature Writer | TLT Best Practices November 2021
Best practices for avoiding lubricant contamination are established and simple to implement—the key to success is follow through.
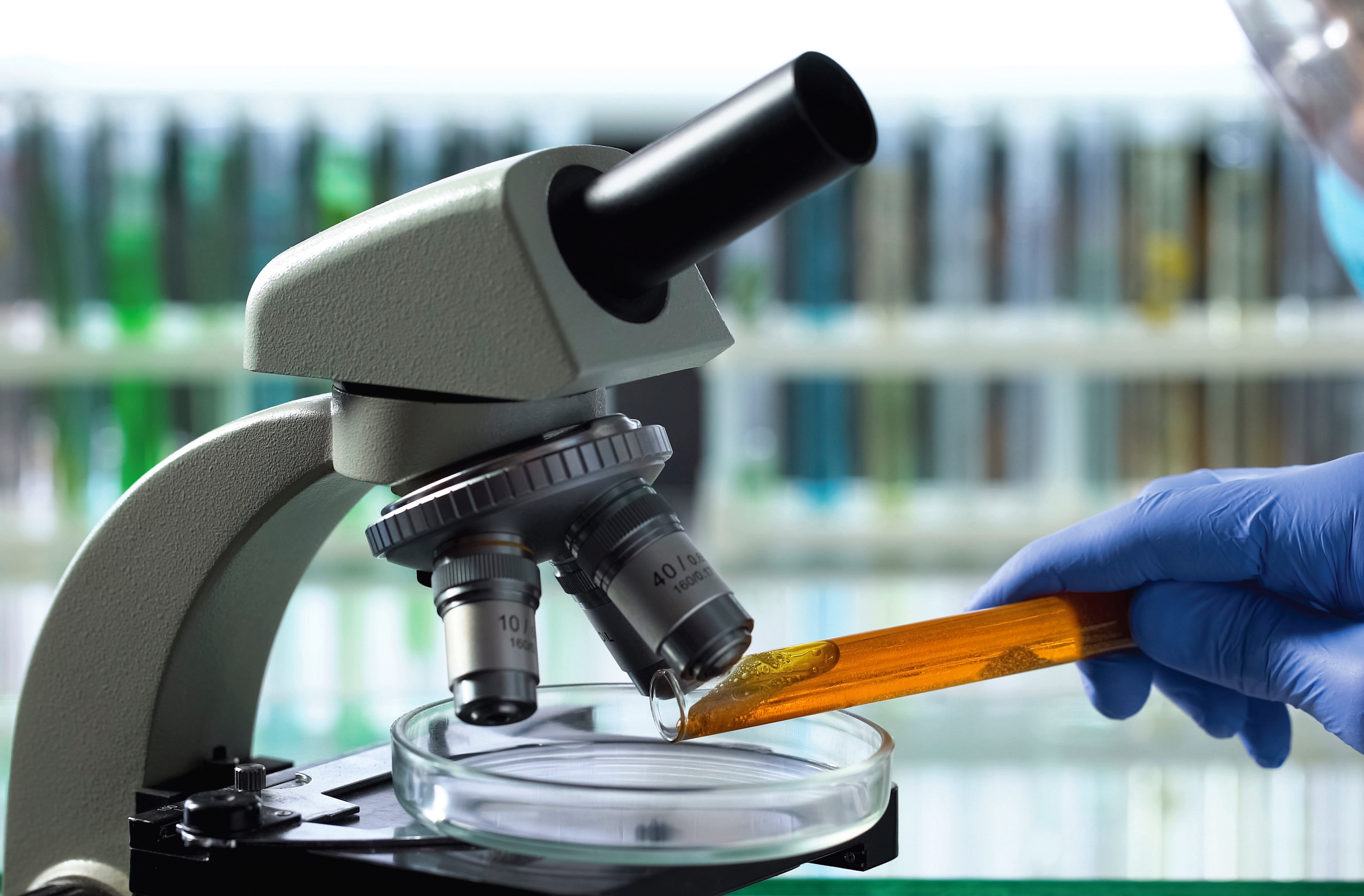
KEY CONCEPTS
•
Particles are the primary type of lubricant contamination.
•
Individual particle contaminants can’t be detected with the naked eye until they reach 40-50 microns—well above the threshold where they can cause damage.
•
There are a number of established best practices for avoiding particle contamination, including frequent testing even for new oil—which usually contains two to 20 times the amount of acceptable particulate.
Oil cleanliness is the measure of particle contaminant in the oil. Particles sourced from the external environment include particles such as dirt that are prevalent throughout most operations. Internal sources of contamination include machinery wear in situations such as abrasion, erosion and fatigue that produce wear particles. Given this, the measure of cleanliness is the level of particulate contamination in the fluid.
While monitoring of new oil from the time it is formulated until the time it reaches its destination is critical, what will make the biggest difference in component service life is proactive management of contamination while the lubricant is in service. The stakes are high—about half of lost machine life is due to mechanical wear, and 82% of mechanical wear is due to contamination.
1
One of the biggest surprises to those new to machine maintenance is that most contamination particles are not visible to the naked eye. In fact, the average person wouldn’t be able to detect contaminants until they are 40-50 microns. The most common particle lab measurements are 4, 6 and 14 microns, and this is for a reason. It is at these levels that particles have the potential to start damaging the machinery. By the time contaminants are visible, they have far exceeded any kind of standards.
Scott Lee Hohnstein, president of Shoco Oil Inc. and founder of the Chevron ISOCLEAN Program, says, “Oil is the lifeblood for equipment and its components. Clean oil is a critical part of the reliability strategy of realizing the maximum life and value of equipment.”
Roy Aune, director of R&D for Liberty Oilfield Services, has deep roots in machinery maintenance. Growing up, his family had a farm equipment dealership that also sold bulk fuel and oil. “We knew the importance of regular oil changes, but I don’t think we understood that new oil could actually be dirty or the steps necessary to ensure the cleanliness of the oil throughout the lifecycle,” he explains.
Aune’s first job was managing a large fleet where he witnessed the impact of dirty oil, especially in hydraulic systems. “We adopted best practices for oil handling, hose making, etc., but the technology wasn’t there to filter the new oil to the necessary cleanliness levels without removing the additives,” he explains. “The reformulation of oils that could be dehydrated and filtered to the necessary specifications, along with the filtration equipment capable of consistently maintaining the specifications, drove the change.”
Chuck Irsik, division manager for Brannan Sand & Gravel Co., says that his view of the importance of oil cleanliness changed when he was introduced to certified clean oils by his supplier. “I saw the sampling results of this certified clean oil and realized the importance of removing contamination from my components in order to extend their life,” he says.
What these comments indicate is that not everyone immediately realizes the importance of contamination control, but once they do, they are sold.
Setting up a contamination control program involves three basic steps: setting targets, monitoring and mitigating. While setting up the program is not that difficult, the key to success is the aggressive implementation of the program.
How oil becomes contaminated
Although this list could be much longer, the following are some basic ways that oil becomes contaminated:
•
Storage containers are not properly sealed or lack proper storage conditions.
•
The devices used to check contamination are themselves contaminated.
•
Oil is dispensed from dirty containers.
•
Transfer devices, such as hoses and funnels, are contaminated.
•
Equipment is running without proper filtration and/or breathers.
•
The machine is generating wear debris while in use.
•
The oil arrives contaminated (assume that the oil will arrive contaminated).
“Oil can become contaminated from the manufacturer every time it is pumped into containers, whether that is a tank, railcar, tanker truck or any container all the way to the end-user,” Hohnstein says. “It also can be contaminated through air ingression in adverse environments. Contamination also can occur by allowing water or other contamination to enter the storage tanks throughout the chain of custody.”
Hohnstein adds that the following key practices are often overlooked.
•
Utilizing breathers to manage air ingression
•
Flushing equipment/system components when new or after any failure
•
Awareness of filters with a bypass
•
Understanding beta ratio and how it impacts filtration
•
Watching filter differential pressures
•
Monitoring the oil path through delivery, storage, dispensing reels, services trucks, etc. with tests that include Karl Fischer for water
•
Monitoring the oil analysis results and wear results on pre-cleanliness and post-cleanliness oil to determine the value of equipment life extension
•
Educating staff on the importance of oil cleanliness
•
Securing upper management support and change management throughout the entire organization in order to gain full buy in.
Cleanliness targets
When setting cleanliness targets, Hohnstein’s first recommendation is to utilize the OEM’s cleanliness specifications. “Always use the tightest ISO-cleanliness specification on the system, equipment and each component as your target,” he says.
Aune agrees, saying, “We largely rely on the OEMs to set the cleanliness specification. However, we understand the impact of reducing wear materials in the oil. So our desire is not only to meet specifications but to get the cleanest oil commercially available.”
“We determined cleanliness goals when we were upgrading our equipment and looking at extended warranties with the manufacturer’s service representative,” Irsik says. “We take into account the manufacturer’s oil specs and interval period and want to take full advantage of these warranties.”
Targets are usually based on equipment type, vulnerability to failure caused by contamination, the criticality of the equipment and the potential for external contamination ingression from the operating environment (
see How Contamination Causes Failure). A simple way to set those targets is by using the ISO code.
How contamination causes failure
There are three primary ways that contamination leads to machine damage and failure:
•
Abrasion results from particles that are lodged between two sliding surfaces. These particles gouge and score material from the surface of the machine.
•
Erosion is a particular issue for systems that involve fluids that flow forcefully. When contaminated, lubricant in high-speed, tight-clearance conditions damages all of the surfaces it contacts. The compounding factor is the velocity of the flowing lubricant and the contaminants’ higher density relative to the oil.
•
Fatigue is a particular issue for situations that involve rolling contact—most commonly between rolling element bearings and their races but also at the pitch line of gears and in cam/tappet interfaces. The contaminants in these situations lead to denting and fatigue stress, which, in turn, lead to spalling and ultimately fatigue failure.
ISO standard 4406:2017 addresses particle count and measures the number of particles greater than 4, 6 and 14 microns per milliliter. Those measurements are then converted to the ISO code (also called the range code).
Most labs report particulate contamination in a three number ISO code format such as 20/15/11; 20 is the range of particles bigger than 4 microns, 15 is the range bigger than 6 microns, and 11 is the range of particles bigger than 14 microns. It’s important to note that for each range code unit increase, the number of particles in the range doubles on average.
Best practices for achieving targets
To keep the oil clean in the maintenance facilities, at certain companies, maintenance staff installs desiccant breathers on all the storage tanks. As oil is pumped out, only dry filtered air enters the tank. Tanks are filled via flat face hydraulic fittings to eliminate any possibility of contaminants coming in through a fill port. In addition to their standard oil testing program, they added testing at various points in the delivery chain to make sure there is no contaminant ingress.
“On our mobile equipment, transmissions and gearboxes have desiccant breathers,” Aune says. Color-coded flat face fill and drain couplings can be installed on equipment. These fittings will only couple with a corresponding coupling half of the same color, eliminating the opportunity to accidentally put the wrong fluid in a tank. They also eliminate the need to open a fill port to pour in fluids, a definite source of contamination.”
Challenges in achieving targets
One of the TestOil’s lubrication field engineers, Dwon Ruffin, CLS, sometimes sees trouble spots when he is on site. “Common sources of contamination that often are overlooked are steam and the shop fans that cool the area,” he says. “These things move particulate throughout the room. Just taking a look at the back of a fan might produce some evidence.”
Aune says the issues lie with both personnel and equipment. “The first challenge was to convince stakeholders in our organization that this investment in cleaner oil will pay for itself by significantly reducing maintenance costs,” he says. “After the institutional challenges were met, we had to make significant changes to our facilities to ensure the clean oil is kept clean. Modifying tanks, replacing product lines and adding new fill lines while continuing to service fleets daily was a challenge for sure.”
Irsik agrees that buy in can be an issue. “Some of the challenges in trying to achieve cleanliness goals were breaking old habits of transferring the clean oil from the dispenser or tank to the component and getting all of our technicians and crew members to see the benefits of this new process of transferring fluids,” he says.
Monitoring new oil
As pointed out earlier, it comes as a shock to many people that new oil almost never arrives clean. In fact, it is safe to assume that it doesn’t.
Hohnstein recommends that end-users incorporate the following processes into their maintenance practices to ensure they are receiving clean oil and to keep it clean throughout the oil path. “The first step is to request a certificate of cleanliness to verify the oil meets the end-user’s desired cleanliness target at the time of delivery,” he says. “In addition, they should obtain a sample of the oil at the time of delivery, submit the sample for cleanliness testing and compare the results with the target code. Finally, they should ensure that the lubricant distributor is utilizing proper distribution practices when dispensing oil into the end-user’s storage tanks.”
Irsik advises equipment operators to trust but verify that the product is the cleanest available.
“We committed to a ‘start clean, stay clean’ program,” Aune adds. “Step one was to buy the cleanest oil commercially available. The biggest impact on meeting our cleanliness targets was absolutely the ability to source oil with the cleanliness levels we see today—it simply wasn’t possible before.”
A good contamination-avoidance program relies on the expertise of maintenance personnel.
Best practices for managing contamination
Lubricant is vulnerable to contamination from the moment it is formulated to when it is flushed out of the system. Lubricant contamination needs to be managed at several key points.
1.
Receiving new oil. Achieving targets starts with new oil. New oil from drums or bulk deliveries usually contains anywhere from two to 20 times the amount of acceptable particles for most lubricated equipment. This is primarily due to the number of times it is transferred between storage devices before it is delivered. Ideally all new oil should be tested before it is put in service. A good practice is to introduce new oil that is at least two ISO codes cleaner than the in-service targets.
2.
Storage and conditioning. Assuming the new oil has been tested on arrival and any issues have been mitigated, the oil should be kept clean and dry until it is ready for use. If it is stored for a long time, or there is any question about the cleanliness of storage containers, it may need to be retested before use.
3.
Introducing the lubricant into the equipment. There are two factors involved: ensuring that the lubricant entering the machine is clean and also that the correct lubricant is being used in the first place. During the fill process, operators should always use clean pumps, carts and hoses to dispense the fluid, and the pump or cart should have the recommended filter. After the oil has been dispensed, the filling cap should be clean before it is replaced, and the equipment should be checked for leaks. To ensure that the correct lubricant is introduced, there should be a failsafe system such as color coding.
4.
Keeping the oil clean while in use. The best way to ensure clean operating oil is to employ air breathers in the reservoirs that prevent contaminants such as dirt and water from entering the system.
5.
Filtering the oil while in use. The correct filter—the one recommended or approved by the OEM—should be used. Note that smaller pore size isn’t necessarily better. While the breather is designed to address external contamination, the filter’s job is to remove internally generated contaminants.
6.
Lab testing. This ensures that oil changes are based on condition, not calendar time or operating hours. Any oil change has the potential to expose the oil to contaminants. Lab testing will prevent unnecessary changes and, at the same time, will pinpoint unusually high contamination that warrants a timely oil change. Regular oil analysis also will identify trends in particulate size and type that may require immediate action before the equipment fails or needs to be removed from service.
Irsik says that the practice that made the biggest difference in their ability to meet cleanliness targets was removing transfer cans, buckets or containers from the shop and adding additional oil transfer reels, hoses and dispensers throughout all of the maintenance areas and making them accessible to crew members. “We also provided replacement/top-off oils in smaller containers and switched from cumbersome five-gallon pails to more manageable one-gallon containers. Once the seal is broken on a container, we will replace it with a new one and will not reuse the container,” he says.
Best practices training
A good contamination-avoidance program relies on the expertise of maintenance personnel. There are a number of excellent sources of maintenance training—most of which can lead to STLE certifications. This training and the resulting certifications are a smart investment in the future of any contamination control program. During training, employees will learn the effect and consequences of contamination and also the benefits of contamination control.
Return on investment
A well-structured contamination control program will require some investment, but compared to the cost of downtime and permanent equipment failure, it is slight. Costs associated with a contamination control best practices program may include:
•
Lubrication management software—depending on the oil analysis lab, this may not be necessary
•
Upgrades to the lube storage area
•
Upgrades to oil dispensing system
•
New and/or better air breathers
•
New filtering units or upgrades to existing ones
•
Labeling discipline
•
More frequent oil analysis by an outside lab
•
Lubrication training for maintenance staff.
The relatively minor investment that this requires will pay dividends in the form of improved equipment reliability, reduction in the cost of typically effected parts such as bearings and significantly longer life for hydraulic systems and pumps.
“Lubrication engineers have known for some time that excess water in oil causes additional wear,” Aune says. “They also have shown that a higher concentration of wear materials in lubricating oil leads to a corresponding reduction in equipment life. Additionally, the size of the particles that are most responsible for the wear generally are too small to be filtered out by onboard filtration systems. For many fleets, I believe the additional investment in cleanliness best practices will be paid back many times over by the reduction in maintenance costs.”
Conclusions
There are many OEMs, formulators, distributors and oil analysis labs that offer help in setting up a best practices contamination control program. “These best practices have led to cleaner oil sample results, which have led to extending change intervals, and, in some instances, not changing the fluid until the oil sample indicates change is needed,” Irsik says.
“This is all in an effort to lower cost and extend the useful life of a component,” Aune concludes. “Oil testing from the engines, transmissions and gearboxes on our equipment has shown an average 45% reduction in wear materials since we implemented the program. There is empirical evidence that this reduction should drive a meaningful reduction in maintenance costs.”
REFERENCE
1.
Cracking the ISO code to Lubricant Cleanliness, Des-Case. Available
here. Information is based on a research study by STLE and the National Research Council of Canada (NRCC).
Jeanna Van Rensselar heads her own communication/public relations firm, Smart PR Communications, in Naperville, Ill. You can reach her at jeanna@smartprcommunications.com.