Clean lubricant program success
Jeanna Van Rensselar, Senior Feature Writer | TLT Lubrication Fundamentals May 2021
Particle count analysis, either in the lab or onsite, has the potential to catch issues early before they lead to equipment failure.
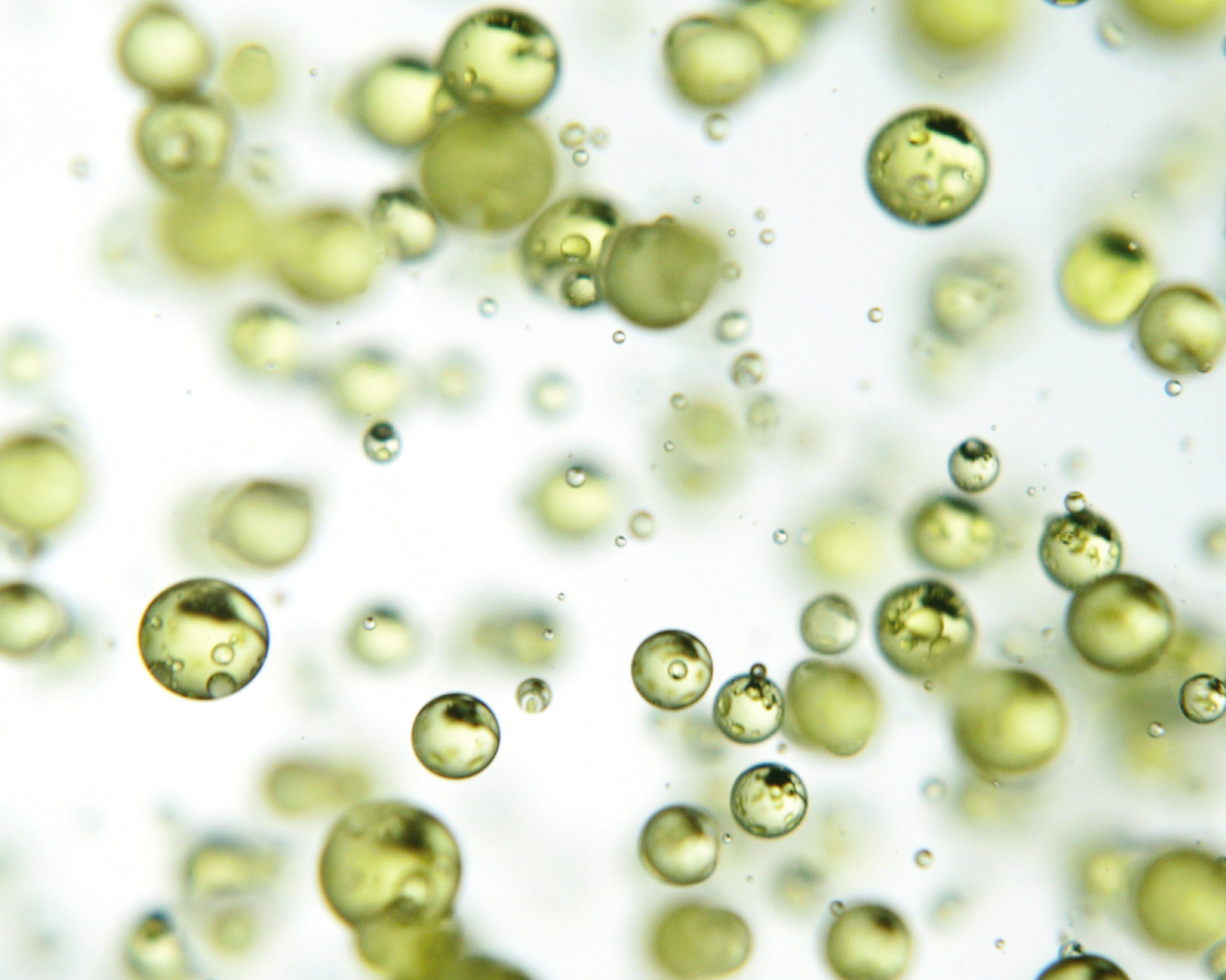
KEY CONCEPTS
• Particle count analysis detects the number and size of particles—but not the composition.
• Particle count analysis is an excellent part of a comprehensive oil analysis program.
• The value of the program is contingent on the quality of the follow through.
Contamination is the leading cause of lubricant-related equipment failure. One way to head off damage is through particle count analysis, which is a measure of the amount and size of particles in fluids.
STLE member Rebecca Zwetzig, ISOCLEAN® certified lubricants program manager, Chevron Products Co., explains, “Lubricant cleanliness doesn’t always get the credit it deserves because it is an invisible problem. The particles that do the most damage are invisible to the human eye and can only be detected through particle count testing. Additionally, there is the misconception that lubricants work in a dirty environment so it’s OK if they are dirty.”
She adds that most organizations don’t take into account the real cost of contamination because they measure their operational budget in a different way than they do their capital expense budget—the cost of maintenance and the cost of repairing/replacing equipment isn’t correlated.“ When you look at its cost from a holistic level, the value is staggering,” she says.
There are many methods for detecting and measuring contamination—some of these methods are included in a basic oil analysis test panel. Particle count analysis, however, will take an oil analysis program to the next level (see Figure 1). This analysis can be contracted out, or it can be conducted in-house. In the latter case, there are several types of measurement devices on the market. The machinery, however, is only as effective as the in-house particle count program that supports it.
Setting up and maintaining a successful program is not that easy; it requires training on a number of fronts and follow through.
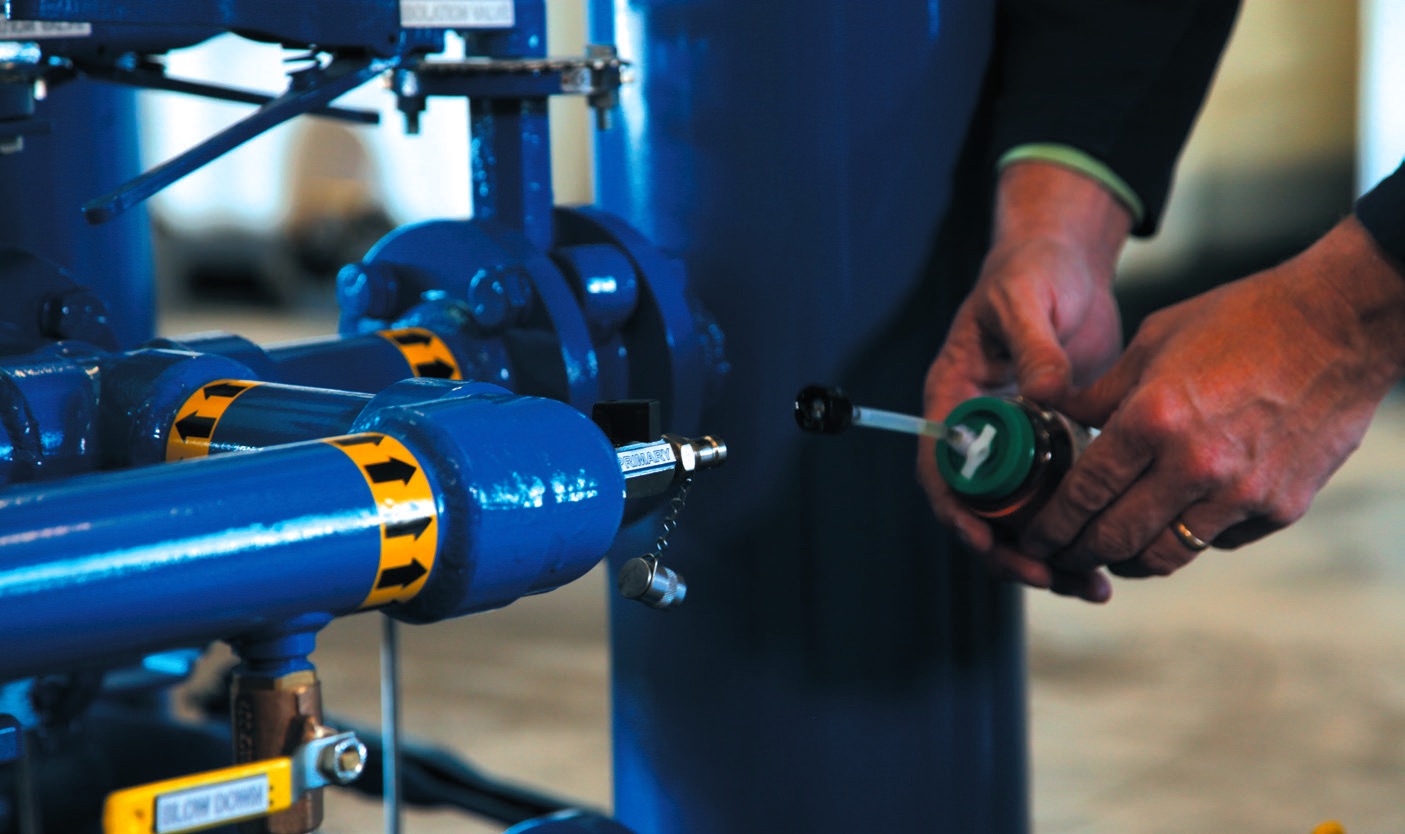
Figure 1. Oil sample collection in preparation for particle count. Figure courtesy of Chevron. © 2021 Chevron. All rights reserved.
Setting up a clean lubricant program
According to Zwetzig, the basic criteria an organization should have in place to ensure a successful cleanliness program that involves particle counting include:
• Education and training on the type of particle counter used and understanding the data reported
• Standard operating procedures that can be easily followed and are focused on consistency
• Establishing an ISO 4406 cleanliness level for new lubricants at delivery
• Using a consistent fluid analysis program to monitor lubricant health, including contamination from particles and/or moisture
• Understanding the filterability of lubricants to ensure no harm is done through the filtration process.
How particle count is measured
Particle counting used to be conducted using a microscope; today it is instrument driven and automated through the use of automated particle counters (APCs). APCs come in a variety of forms, including laboratory bench top units and inline units on equipment.
“These systems were derived to measure the size and distribution of contamination in the lubricant in use, since many of the particle contaminants are smaller than what can be detected by the human eye,” Zwetzig explains. “The lower limit of what a human eye can visibly detect is 40 microns, and a significant amount of wear occurs from particle contamination that is less than 15 microns.”
Richard Price, managing director, Filtertechnik Ltd., believes it’s important to remember that while the APC might be important for quality checks on new oil deliveries, determining the cleanliness of newly installed and flushed systems and day-to-day checks on operating systems, it is only one component of the overall condition monitoring program.
“With the right vision from management to achieve the goal of reliability and uptime, the instrument will become an essential part of the lubrication cleanliness program,” he says. “Basically, if the program is driven top-down with the right metrics and KPIs in place, then the instrument will prove its worth as part of the overall effort in achieving results.”
Price goes on to say that in some instances, Filtertechnik finds particle counters left over by contractors as part of the contractual obligations following installation of high-value assets such as turbines. “Whether that be offshore oil platforms or large power generation facilities, you would be surprised at the number of these units gathering dust,” he mentions. “Clearly, in writing the scope of the project, someone had the foresight to insist on cleanliness levels being met during the flushing process of the installation in line with the various ISO standards, yet this has not been continued into the operational phase.”
How particle count results are coded
The APCs that can discriminate the particle shape are laser light direct imaging PCs. Other types of APCs can factor in additive-induced particle counts (ghost particles). This can lead to false positives in reporting a higher particle count. Equipment using laser light/direct imaging technology is advantageous because it can help reduce the noise by using an algorithm to distinguish particles that are not contaminants at a certain micron level. This micron level might differ by manufacturer. Reported results from APCs yield a particle count number and size distribution, which are usually translated into a simplified or condensed reportable cleanliness standard or code. Advanced particle counters can give ISO counts as well as particle shape recognition, which can be helpful in root cause analysis.
ISO 4406:2021 is a standard method for coding the quantity of contaminant particles per milliliter of fluid at three sizes: 4 microns, 6 microns and 14 microns. Each number represents a contaminant level code for the correlating particle size. It is reported as XX/YY/ZZ where:
• XX = total number of particles ≥ 4 microns
• YY = total number of particles ≥ 6 microns
• ZZ = total number of particles ≥ 14 microns.
“The reported three-digit ISO code correlates to a table that specifies how many of that contaminate particle size are present per one milliliter of fluid,” Zwetzig explains. “For example, a code written as 20/17/13 would mean there are between 5,000 to 10,000 particles of size 4 microns and greater present, 650 to 1,300 particles of size 6 microns and greater and finally between 40 to 80 particles of size 14 microns and greater. Essentially, a laboratory counts the number of contaminant particles and evaluates the distribution classification that, in turn, provides the respective ISO 4406 classification code to indicate the level of lubricant cleanliness (see Table 1).”
Table 1. ISO 4406 cleanliness.
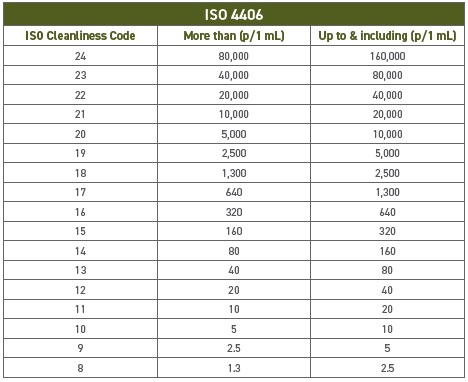
She adds that a key element of success is designating a Lubrication Excellence Champion that is familiar with lubricants, their application and the importance of machinery reliability. She also recommends someone with credible lubrication certifications such as:
• STLE’s OMA I (Oil Monitoring Analyst™)
• STLE’s CLS (Certified Lubrication Specialist™)
• CRL (Certified Reliability Leader®)
• MLT I, II or III (Machinery Lubrication Technician).
Price recommends setting targets as a starting point, then achieving the targets and verifying their achievement for management. “Setting the targets is the easy part,” he says. “There are numerous tools that can assist with establishing the life extension on oils and assets resulting from tightened targets on cleanliness. In fact, this is a key part of establishing the return on investment because it will help justify to management the financial value of the project rather than trying to convince management simply through the technical benefits.”
He advises that achieving the desired targets will highlight a host of areas to be considered—from supply, storage, handling and transfer through to the asset itself.
Price observes that companies who have achieved world-class particle analysis programs have:
• Audited their lubricant and machine suppliers
• Clearly defined their storage, handling and transfer processes to minimize the risk of self contamination
• Upgraded not just the filters on the equipment but also the seals, breathers and gaskets
• Revisited their maintenance procedures to minimize contaminant ingression.
“Above all, they have put training at the heart of the program,” he says. “Whether it is raising awareness with operators or educating maintenance and engineering personnel, knowledge is a key part of the success.”
The particle counts in an asset can change with factors such as operational load and temperature—highlighting the importance of taking particle counts under the same conditions each time in order to understand long-term trends. Price says that having APCs onsite will facilitate frequent sampling, and embedded sensors will deliver real-time monitoring.
Ensuring success
STLE member Rodney Sims, president of Innovative Lube Technologies, LLC, explains that the main issues preventing companies from having successful cleanliness programs that involve particle counting include lack of time, lack of training and lack of standard operating procedures.
“Consistency is key to a successful program; this can be accomplished with standard operating procedures, superior monitoring equipment and educated/trained personnel,” he concludes. “Using the wrong products and/or procedures will generally shorten the life expectancy of the piece of equipment. Monitoring, interpreting the information correctly and responding in a more timely way will extend the life of your equipment. These are key elements to a best-in-class oil analysis program. Being proactive is a must for having a complete reliability program.”
He also advises that measurement without follow through won’t work—likening it to measuring one’s body mass. “The results will only reflect the actual practices, and if one’s diet and exercise regime do not change, then there will be no change in the results. To bring about improvements, one must bring about change in one’s habits. With cleanliness programs, the measurements simply reflect the practices onsite, usually poor practices. Therefore, the issues must be addressed to see improvements that will meet the goals being set.”
The aspects that can go wrong with a particle count program are the same as those that can go wrong with almost any type of oil analysis program, i.e., incorrectly located and inadequate sampling fittings, the lack of sampling fittings, poor training that leads to a faulty sampling process, etc.
“Ultimately, monitoring the results and dealing with the bad actors sooner rather than later is critical to success,” Price summarizes. “The longer the machine is left running at higher levels of contamination, the higher the wear rate and the shorter the service life. The benefit of a cleanliness program that includes particle count is to reduce wear rates to improve reliability and extend the service life.”
Jeanna Van Rensselar heads her own communication/public relations firm, Smart PR Communications, in Naperville, Ill. You can reach her at jeanna@smartprcommunications.com.