Grease flow
Lynne Peskoe-Yang, Contributing Editor | TLT Grease December 2020
There are several factors influencing how grease performs at extreme temperatures.
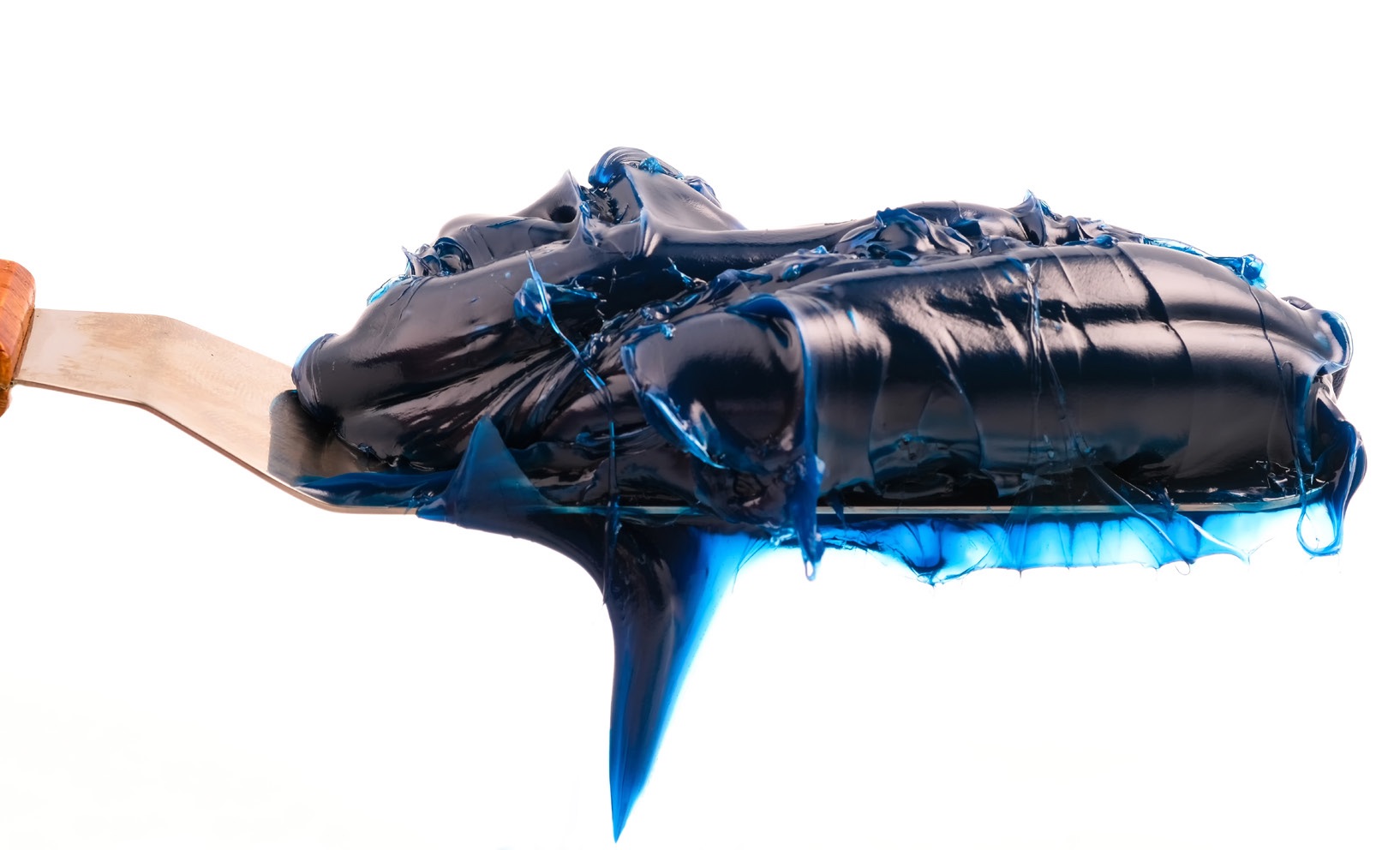
When temperatures drop, grease stiffens and soon fails to circulate throughout the system, leading to dangerously under-lubricated parts.
Rugged engineering is typically geared toward conditions like extreme heat, f lying debris or water exposure, but cold weather provides its own suite of design challenges. As temperatures drop, the same physical properties that make lubricants ideal for a particular application can become dangerous vulnerabilities in the system.
Lubricants at low temperatures
Exactly how the lubricant reacts to low temperatures depends on the formulation of the lubricant, but all lubricants change when they get cold enough. Lubricants flow more slowly at lower temperatures as the kinetic energy of their molecules is reduced. But few modern lubricant formulations can be described in terms of the behavior of one species of molecule. Not only does each ingredient in the formulation respond in a distinct way to changes in temperature, but the interaction between these molecules—the grease matrix that governs its overall physical behavior—plays a role in the final performance of grease in cold conditions.
Lubricating grease, for example, consists of base oil with thickener and generally other performance additives. “Base oil greatly influences the flow properties of a grease,” explains STLE member Dr. Anoop Kumar, senior staff scientist at Chevron. All else being equal, for example, “synthetic oil-based grease is expected to flow better than a grease formulated with mineral base oil,” Kumar explains. “Base oil viscosity and polymer present in the grease also might influence the flow characteristics of a grease at low temperatures.”
“As a rule of thumb, the performance of the base fluid at low temperatures might give a good indication of the low-temperature properties of the final grease formulation, yet it is not the only parameter in the equation,” says Dr. George S. Dodos, chemical engineer at Eldon’s S.A., Greece. Choosing the right base oil helps, but there are several other factors influencing how grease performs at extreme temperatures. “The use of lower viscosity base oils enhances the cold-flow pumpability (of the grease). On the other hand, the type and amount of thickener plays a role in terms of the cohesion of the formed network,” explains Dodos. These microscopic chemical structures within the lubricant determine its macroscale response to the loss of kinetic energy that constitutes a temperature drop.
The use of lower viscosity base oils enhances the cold-flow pumpability. Alternatively, the type and the amount of thickener plays a role in terms of the level of rigidness/cohesion of the formed network and how it is affected as the temperature falls, as well as in terms of parameters such as the tendency to absorb water.
Effects of low-temperature grease flow
When temperatures drop, grease stiffens and soon fails to circulate throughout the system, leading to dangerously under-lubricated parts. “If grease is already applied to the bearing, the torque required to start the equipment might be quite high, and in extreme conditions there could be equipment failure,” warns Kumar.
“An excessive increase in consistency and stiffening means that the grease is more resistant to flow,” due to the cold, says Dodos. Unfortunately, the cold-induced stiffening is worst wherever the lubrication is needed most. For example, in the case of a ball bearing, “the grease might retard the rotational ability and increase the torque, leading to overheating, loss of efficiency and failure,” explains Dodos. “Compromised pumpability, due to grease hardening, could cause premature failures in centralized lubrication systems and could potentially starve the application of lubricant.”
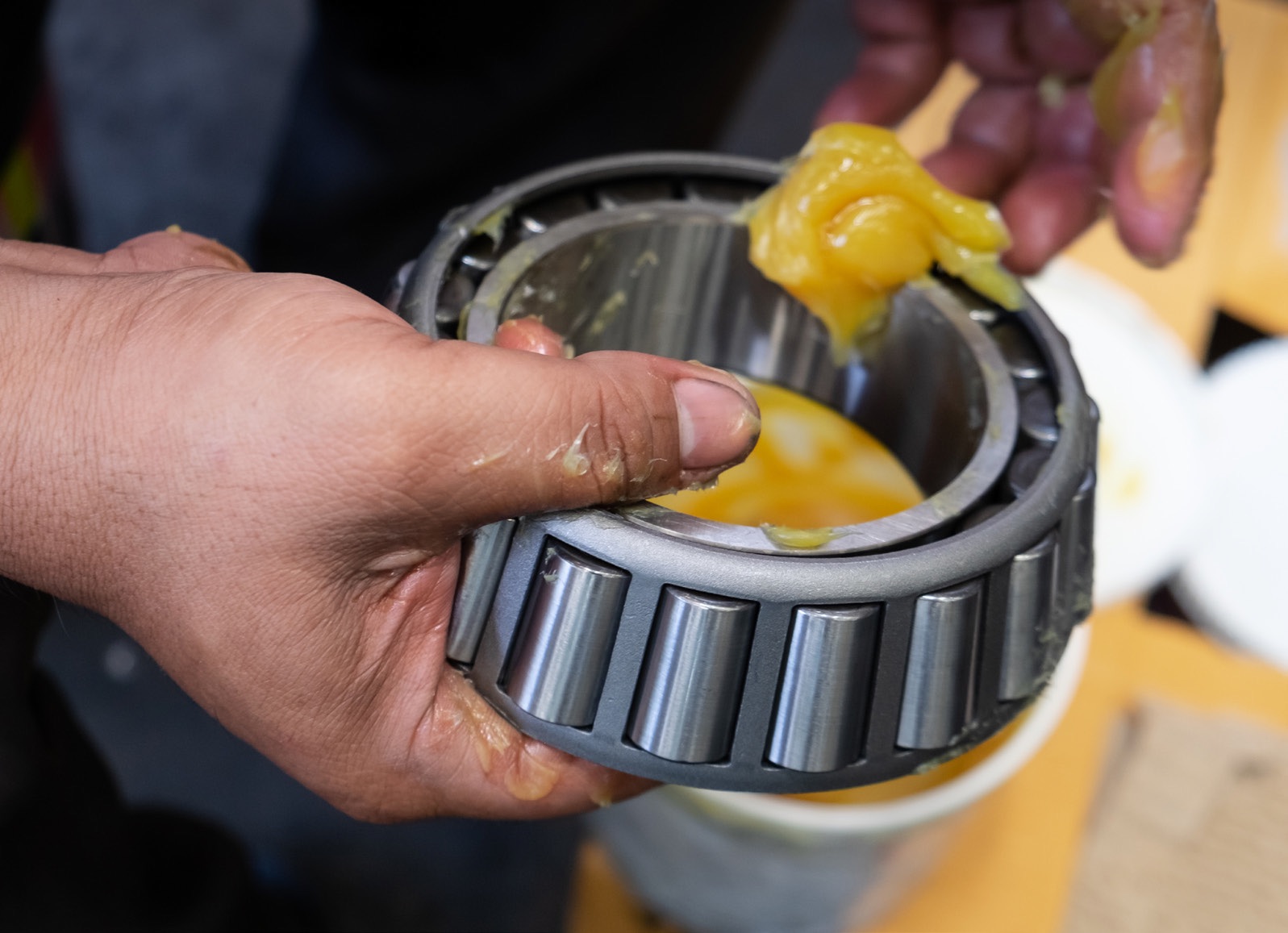
Lubricating grease consists of base oil with thickener and generally other performance additives.
Grease flow testing methods
The multitude of variables affecting the behavior of grease at low temperatures makes it virtually impossible to predict the success of any particular formulation in this setting. To assess the impact of changes to the formula, a number of standardized test methods are available
to grease technicians, each designed to investigate a specific aspect of the surprisingly complex response of lubricants to cold.
One of the most widely utilized cold-flow tests, the Kesternich method (DIN 51805), was originally developed to test the cold resistance of vulcanized rubber. The apparatus measures how much a bit of material, like rubber, can bend without breaking at low temperatures. The device slowly cools the specimen while adding pressure, measuring how the material responds to each decrease in temperature while under stress. For fluids like grease, it measures the flow pressure of a sample at several cold-temperature intervals until the grease hardens completely.
The Kesternich method “has been proved to provide results with good precision,” says Dodos, and requires a smaller sample of grease than most other cold-flow measurement techniques. Other methods for predicting the pumpability of greases at low temperatures, like the U.S. Steel Grease Mobility Method or the Lincoln Ventmeter Test, “have proved their value in developing grease for low-temperature applications, yet the lack of standardization is a limiting factor,” in their applicability, notes Dodos.
The existing specification for NLGI GC-LB grease, ASTM D4950, only offers a low temperature torque limit, while the new High-Performance Multiuse (HPM) grease specification adds low-temperature flow limits using both the U.S. Steel Grease Mobility Method and the Kesternich Method.
Effects of time
Extreme temperatures are limited in their effect on machinery by another important metric: time. The longer a grease is subjected to low temperatures, the more pronounced the effects of the cold might be.
To diagnose low-temperature grease lubrication issues, Dodos first looks for common symptoms like restricted motion on specific components, difficulty in getting lubricants to spread throughout the desired range and freeze-up. Exposure time adds another variable to the calculation of cold-flow grease behavior. “Because of the different behavior of biologically-based oils compared to conventional ones, the low-temperature properties of the corresponding greases could be affected by the exposure time,” including any time spent in storage onsite, says Dodos.
Cold-flow principles in action
The typical response to concerns about low-temperature pumpability and flow is to recommend a grease formulation with a lower NLGI number. Special additives, like cold-f low improvers, can mitigate cold-flow issues to a certain extent, says Dodos. “With regards to the base fluid, mineral oils with low paraffinic content (i.e., napthenics), as well as synthetic oils with improved cold-flow properties, would fit the purpose,” adds Dodos.
More helpful, however, is considering the full range of data available about a complete formulation before selecting it. To prepare for extreme weather, says Kumar, “the very first thing a technician should do is select a grease that has better flow properties at low temperatures, either by checking with the supplier or by reviewing the product data sheet for low-temperature claims.” Technicians working with cold-temperature applications “should select a grease that can pump easily at the lowest possible temperature,” advises Kumar.
Cold-temperature grease technicians have to be experts in the needs of their equipment at all prescribed operating conditions. For cold-temperature applications, Dodos recommends that operators collaborate closely with lubricant suppliers to ensure optimal performance. Above all, he says, extreme temperatures should be taken seriously, whether hot or cold. “The operating limit of the lubricant should not be marginal to the application temperature,” Dodos says.
FOR FURTHER READING
1. Aengeneyndt, J. and Kesternich, W. (1945), “A New Method for Determining the Resistance of Soft-Rubber Products to Low Temperatures,” Rubber Chemistry and Technology, 18 (2), pp. 401-404. DOI: 10.5254/1.3546738.
2. Cheng, D. C.-H. (1981), “Viscosity (Part 1),” Measurement and Control, 14 (3), pp. 73-78. DOI: 10.1177/002029408101400301.
3. See NLGI grease specifications here.
Lynne Peskoe-Yang is a freelance writer based in Tarrytown, N.Y. You can contact her at lynnepeskoeyang@gmail.com.