Gear oils and efficiency
Lynne Peskoe-Yang, Contributing Editor | TLT Gear Lubrication September 2020
What difference does gear lubrication make in the fuel-efficient drivetrain?
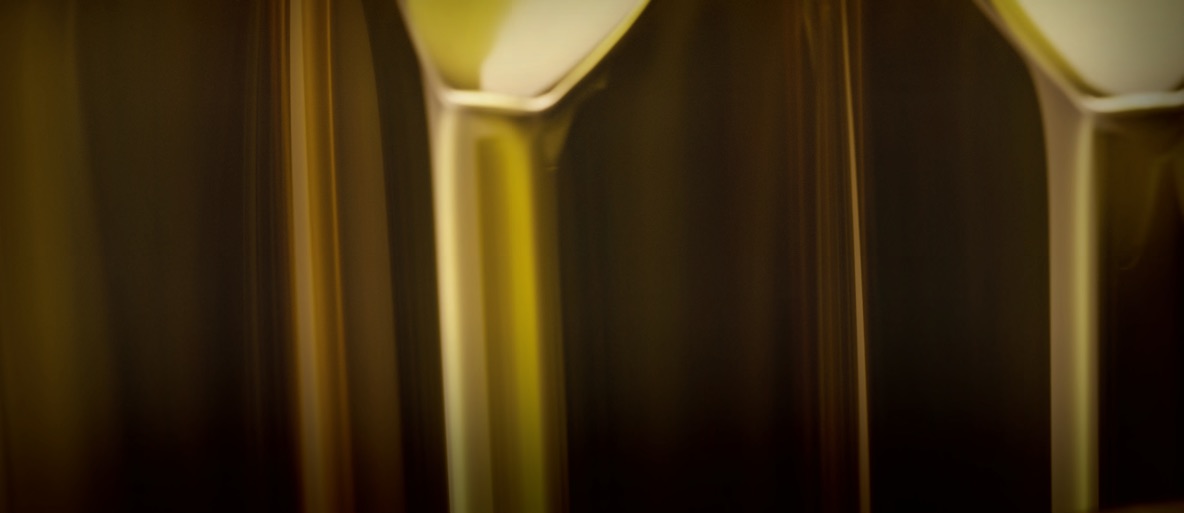
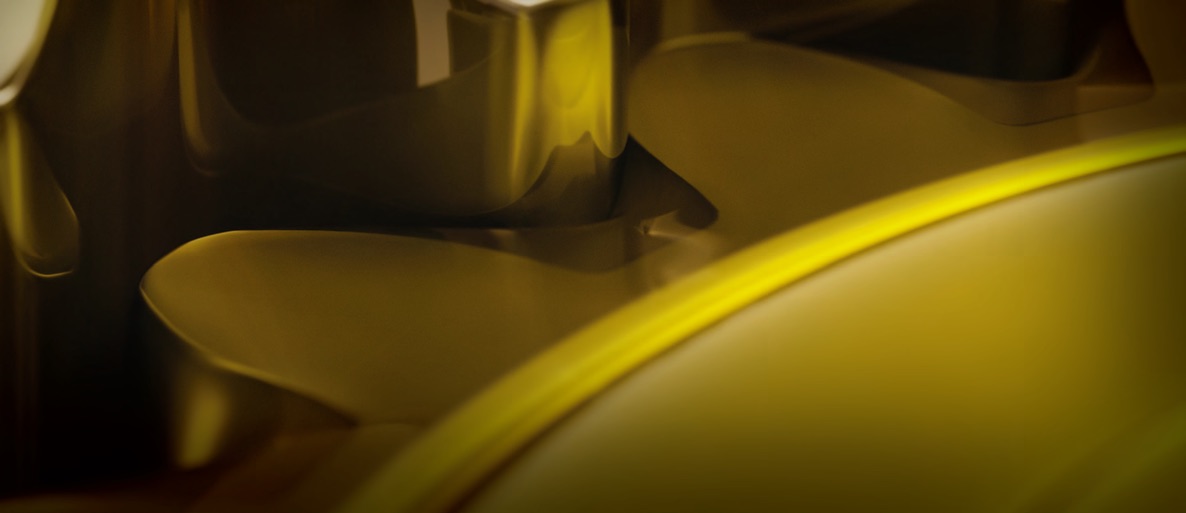
With international emissions and efficiency targets rapidly approaching, the pressure on automotive engineers has never been higher. The European Union’s (EU’s) 2021 target limits carbon dioxide emissions to 95 grams of CO
2 per kilometer for passenger vehicles, while the 2030 target aims to reduce the same measure by an additional 30%.
Tightening efficiency regulations can only energize the consumer market for hybrid and electric vehicles, and so far, the EU’s forecasts suggest this is indeed the case. But as Ishikazi and Nakano
1 report, “although the automobile market is shifting to electrification, in 2030, vehicles equipped with internal combustion engines will still account for approximately 90% of the annual sales volume of passenger vehicles.” In other words, combustion engines that do meet the new EU standards for efficiency will still be in high demand.
Whether the power source is an internal combustion engine or an electric motor, the overall efficiency, in terms of emissions, must improve to meet these new standards. For this purpose, formulators are increasingly turning to ultra-low viscosity oil, which improves fuel economy, though not without a host of knock-on effects throughout the drivetrain.
These new ultra-low viscosity oils will have to protect the components of the fuel-efficient drivetrain without affecting its fuel economy. “Energy efficiency is rapidly changing lubricant formulations. The lubricant is being asked to do a lot more with less,” says STLE-member Donna Mosher, technical support manager for transportation lubricants at BASF. “New gear-train designs are using less oil, operating at higher loads and hotter temperatures, and oil drain intervals’ demands are extending. The oil formulation is changing to address these new designs.”
Viscosity and the Stribeck curve
The Stribeck curve, which estimates the friction coefficient of a given system as a function of lubrication viscosity, suggests the general rule that lower viscosity in a gear lubricant contributes to higher efficiency, but knowing this rule is insufficient. Driving cycles, vehicle condition and control systems can all trigger changes in temperature, shear and pressure on the lubricant that fall outside expectations predicted by the curve. “Simply changing the viscosity of the lubricant to gain efficiency can rapidly result in early failures,” warns Mosher. Intimate knowledge of the application and oil formulation also are essential, as “viscosity is just one parameter that is used for efficiency,” says Mosher.
Among other factors, Mosher recommends considering the downstream impacts of lowering a lubricant’s viscosity on the oil drain interval (ODI). “If the oil viscosity is too low and the efficiency decreases due to more asperity contacts, the wear will increase,” as will the lubricant’s temperature, potentially compromising both component life and the overall ODI.
The operational needs of the application also must be taken into account, as some systems are prone to respond differently to certain oil types over time, says STLE Vice President Dr. Ken Hope, global PAO technical service manager at Chevron Phillips Chemical. “For instance, does the base oil have a tendency to absorb or shed water? Would the viscosity properties be subject to change given shear, absorption of moisture or process components? Looking at the lubricant as a system of component parts and the interplay of those parts within the intended application is key to designing the most efficient lubricant.”
Formulating efficiency
Regardless of the formulator’s personal or institutional commitment to fuel economy, a lubricant can only stretch as far as the laws of tribology permit. Ishikazi and Nakano recommend that designers consider the full life cycle impact of their oils and additives, as the emissions released during production can vary widely depending on the oil type and manufacturing plan.
Switching oil types without assessing the possible downstream effects on all components risks trading small inefficiencies for much larger ones, given the limited role of gear lubrication in emissions levels. A historical review by STLE-member Mark T. Devlin in 2018
2 found that vehicle energy loss due to friction in the engines, axles and transmission accounts for only 5%-15% of fuel combustion energy, while the rest is unaffected by gear lubricant formulation, though future advancements within the drivetrain might increase this limited impact.
Over the past five years, says Mosher, new drivetrain configurations have poured into the market, all featuring widely varying approaches to the structural challenge of fuel-efficient design. But focusing the fuel economy conversation on the drivetrain alone sidelines an opportunity to incorporate best practices in lubricant formulation. “These new drivetrain configurations tend to focus on the gearbox design, with lubricant sometimes being an afterthought,” says Mosher. “By bringing the lubricant formulation into the gearbox design early in the design process, collaboration results in gearbox design selection, [leading to] improved efficiencies.”
Chemistries of the future
Formulators have no choice but to adapt to necessary regulations, but R&D investment will likely expand to meet this need. The rapid shift to electrification in vehicles will encourage “diversified investment in a number of technologies, including vehicle electrification, autonomous driving and artificial intelligence,” predicts Ishikazi and Nakano.
Despite the complexity of the Stribeck curve, Ishikazi and Nakano forecast that, on the whole, “the viscosity of mineral engine oil is expected to continually decrease in the future,” as the consumer market increases pressure to invest in electric motors and their lubricants.
“The popularization of synthetic engine oil as we move toward 2030 will require the consideration of both the reduction in viscosity and the extension of the oil drain interval,” write Ishikazi and Nakano. As manufacturers scramble to keep up with regulations and consumer demand, “the largest challenge I see is the speed of change,” says Mosher.
REFERENCES
1. Ishikazi, K. and Nakano, M. (2018), “Reduction of CO
2 Emissions and Cost Analysis of Ultra-Low Viscosity Engine Oil,
Lubricants, 6 (4), 102, Doi:10.3390/lubricants6040102.
2. Devlin, M. T. (2018), “Common Properties of Lubricants that Affect Vehicle Fuel Efficiency: A North American Historical Perspective,”
Lubricants, 6 (3), 68, Doi:10.3390/lubricants6030068.