Wind turbines: Promise and problems
Don Smolenski, Contributing Editor | TLT Machinery August 2020
Tribology assists with the operation and maintenance.
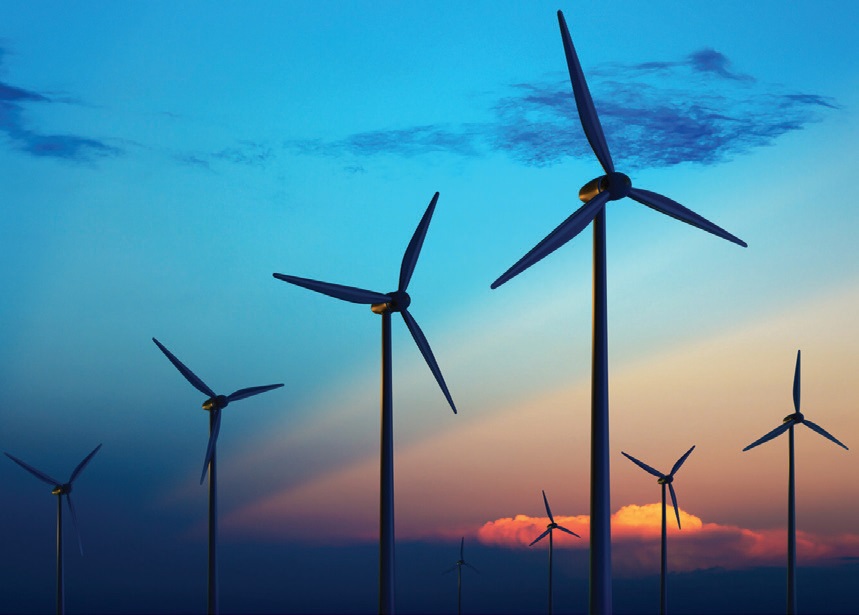
Many turbines have failed from bearing surface fatigue, which produces debris that further leads to abrasion of other components.
Several years ago, while driving at night along the west shore of Lake St. Clair in Michigan, I noticed a significant number of red blinking lights on the east (Canadian) shoreline. Turns out they were wind turbines just onshore a short way off the lake. I wasn’t all that familiar with them, but I do know a wind turbine is a high-tech version of the old wooden windmills in Holland, Mich. Basically, it converts kinetic energy from the wind into electrical energy. The wind spins the turbine blades causing a shaft to turn, which might then employ a gearbox to convert to high-speed rotation and ultimately power a generator. The turbine components are usually located 200 feet or more above the ground (or water). Since early installations, wind turbines have undergone significant and nearly continuous improvements, typically employing better materials, improved designs, greater rotor diameter and height, etc.
There also has been considerable focus on reducing wind power costs, especially operating and maintenance costs, which can amount to two-thirds or more of the investment cost over the lifespan of the turbine. One of the lowest-priced energy sources available today is land-based, utility-scale wind, at about $0.02-$0.06 per kilowatt hour. Unexpected maintenance/failures, however, increase the costs and reduce the amount of energy produced. The often-remote location (e.g., offshore) and the height make maintenance a challenge. An analysis of almost 3,000 onshore wind turbines predicted they will generate electricity effectively for only 12-15 years—not the expected 20-25 years.
Many turbines have failed from bearing surface fatigue, which produces debris that further leads to abrasion of other components of the gearbox. This is where tribology comes in. In addition to hardware and design improvements, lubricant formulators can help by optimizing a combination of several key parameters: wear, scuffing and micropitting resistance (to help prevent premature failure), seal compatibility (to minimize lubricant leakage), aging and oxidation resistance (to extend lubricant life) and so on. Of course, lubricants must perform acceptably over a wide range of ambient temperatures.
Another way that tribology assists with reducing failures is condition monitoring. With most wind turbines in remote locations and difficult access, condition monitoring becomes more important. When the first large wind turbines were installed, oil samples were often only taken every six months or so. Trend analysis for important oil quality parameters was less than optimal. Now oil analysis and condition monitoring for both onshore and offshore wind turbines is more frequently being done using online sensors for monitoring oil level and condition, as well as hardware condition, similar to those used in some automotive engines. Micro-acoustic, dielectric, FTIR and other types of sensors are used to track viscosity, acid number, water content, oxidation, wear metals, conductivity and oil additive elements. Sampling and transmission of data is pretty much continuous. This enables more precise trending of important oil and machine condition, which, in turn, improves reliability and ultimately cost competitiveness.
Now when I see the blinking red lights across the lake, I know that tribology had a hand in the successful operation of those wind turbines.
FOR FURTHER READING
1.
Walford, C. (2006), “Wind Turbine Reliability: Understanding and Minimizing Wind Turbine Operation and Maintenance Costs,” Sandia 2006-110. Available
here.
2.
Mendick, R. (December 2012), “Wind farm turbines wear sooner than expected, says study,” The Telegraph. Available
here.
3.
McGuire, N. (2019), “Lubrication challenges in the wind turbine industry,” TLT,
75 (9),
pp. 34-43. Available
here.
4.
R. David Whitby, R. D. (2017), “Monitoring wind turbine oils,” TLT,
73 (9), p. 88. Available
here.
Don Smolenski is president of his own consultancy, Strategic Management of Oil, LLC, in St. Clair Shores, Mich. You can reach him at donald.smolenski@gmail.com.