Minimum quantity lubrication machining
Don Smolenski, Contributing Editor | TLT Machinery June 2020
This emerging technology offers potential cost savings and environmental benefits on the shop floor.
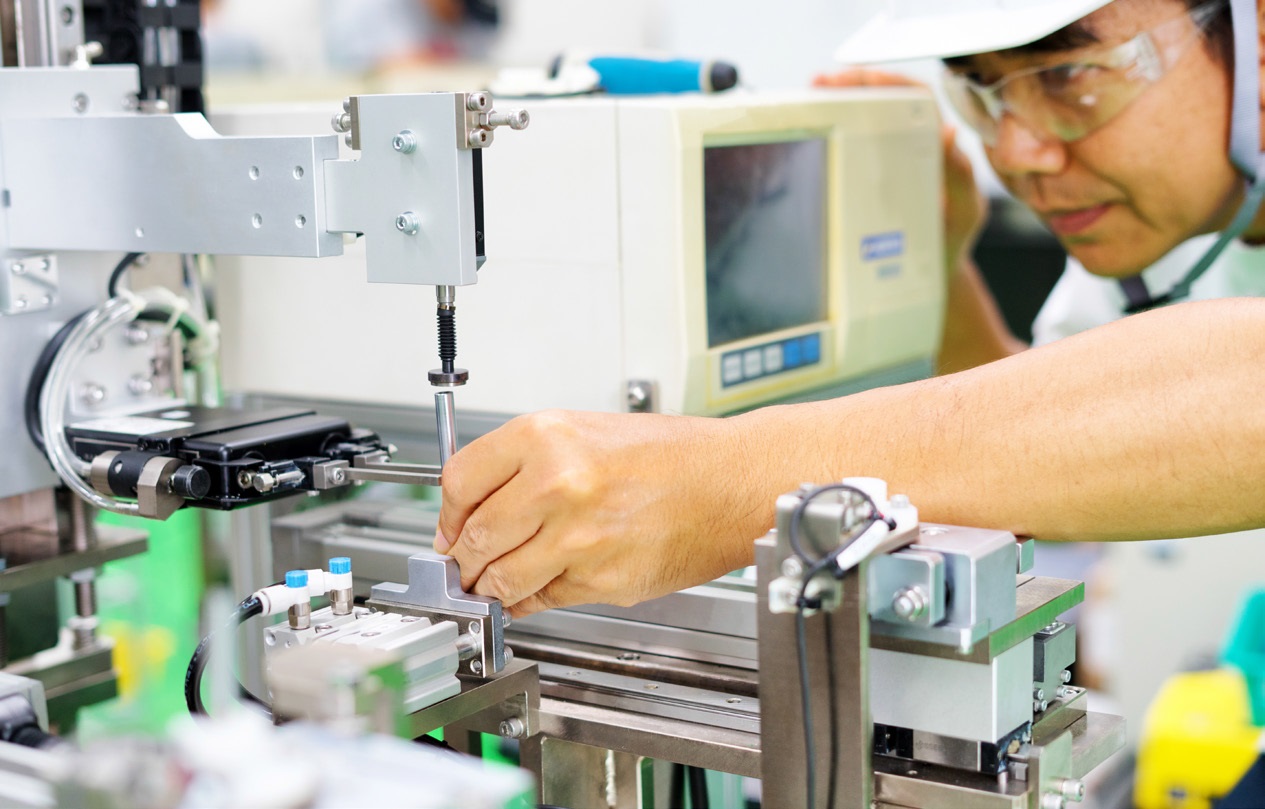
Machinists can overcome the challenges of using minimum quantity lubrication (MQL) with education and training.
Minimum Quantity Lubrication (MQL) is a process that uses small amounts of a specially formulated lubricant applied directly to the tool-workpiece interface. This replaces the traditional flood coolant (metal-removal fluid). There are several potential benefits of MQL in addition to significantly reduced metal-removal fluid usage. With MQL, the fluid is “once through” usage as opposed to a recirculating sump. This eliminates the need for constantly adjusting fluid concentration. Tramp oil and microbial contamination are eliminated, which eliminates the need for the use of biocides. Fluid disposal costs also are eliminated. The coolant is specifically formulated and applied for each individual operation and will be inherently cleaner since it is not recirculated. Ostensibly this results in improved tool life and part surface finish. Potential cost savings and significant environmental benefits are possible.
There are certainly challenges, however. The fluid concentration must be precisely controlled, and special cutting tools may be required. Heat removal from the tool and workplace is absolutely critical and must be meticulously ensured. Each machining process will have specific requirements. For instance, milling is less rigorous than gear hobbing—the latter requiring higher lubricity. An MQL mixing system must deliver a precise amount of aerosol (fluid droplets of appropriate size) for optimum wetting and lubrication using a metering valve to form this desired aerosol mixture. This is fed to the tool-workpiece interface. The aerosol is switched off as the spindle travels from one machined area to another, further reducing fluid usage.
Many MQL processes require a through-tool lubrication path, which allows the aerosol lubricant to reach the tool-workpiece interface more effectively. Any partial plugging of the passageways will inhibit this ability, and the lubricity will be lost. If lubricity is not carefully maintained, overheating and poor parts quality will result. Aerosolizing the fluid also must be proven to not result in significant mist exposure to the workers.
Initial worker acceptance of MQL may be a challenge but can be overcome by proper education and training. Finally, chip handling must be addressed. One of the major functions of flood coolant is to carry off the chips. There are a variety of techniques for effectively removing chips without the use of coolant such as a vacuum system, chip conveyors, etc., but a retrofit of an existing machining line could be significantly costly.
The well-established use of flood coolants for metal removal has likely inhibited the implementation of MQL. In an industry where production efficiency is crucial and downtime is very expensive, the unknowns of such a new technology pose the potential threat of complications. It also is a threat to traditional coolant manufacturers. For these and other reasons, MQL is likely to be more successful in new machining lines rather than in retrofitting existing applications.
Ford Motor Co. has successfully used MQL machining in a Detroit-area manufacturing plant for many years. Ford now uses MQL in at least six plants globally, and this will increase in the next few years.
REFERENCES
1. Click
here .
2. Modern Machine Shop. Available
here.
3. Click
here.
4. Click
here.
Don Smolenski is president of his own consultancy, Strategic Management of Oil, LLC, in St. Clair Shores, Mich. You can reach him at donald.smolenski@gmail.com.