The art of manufacturing grease
Andrea A. Aikin, Contributing Editor | TLT Grease June 2020
Research is ongoing to develop improved products.
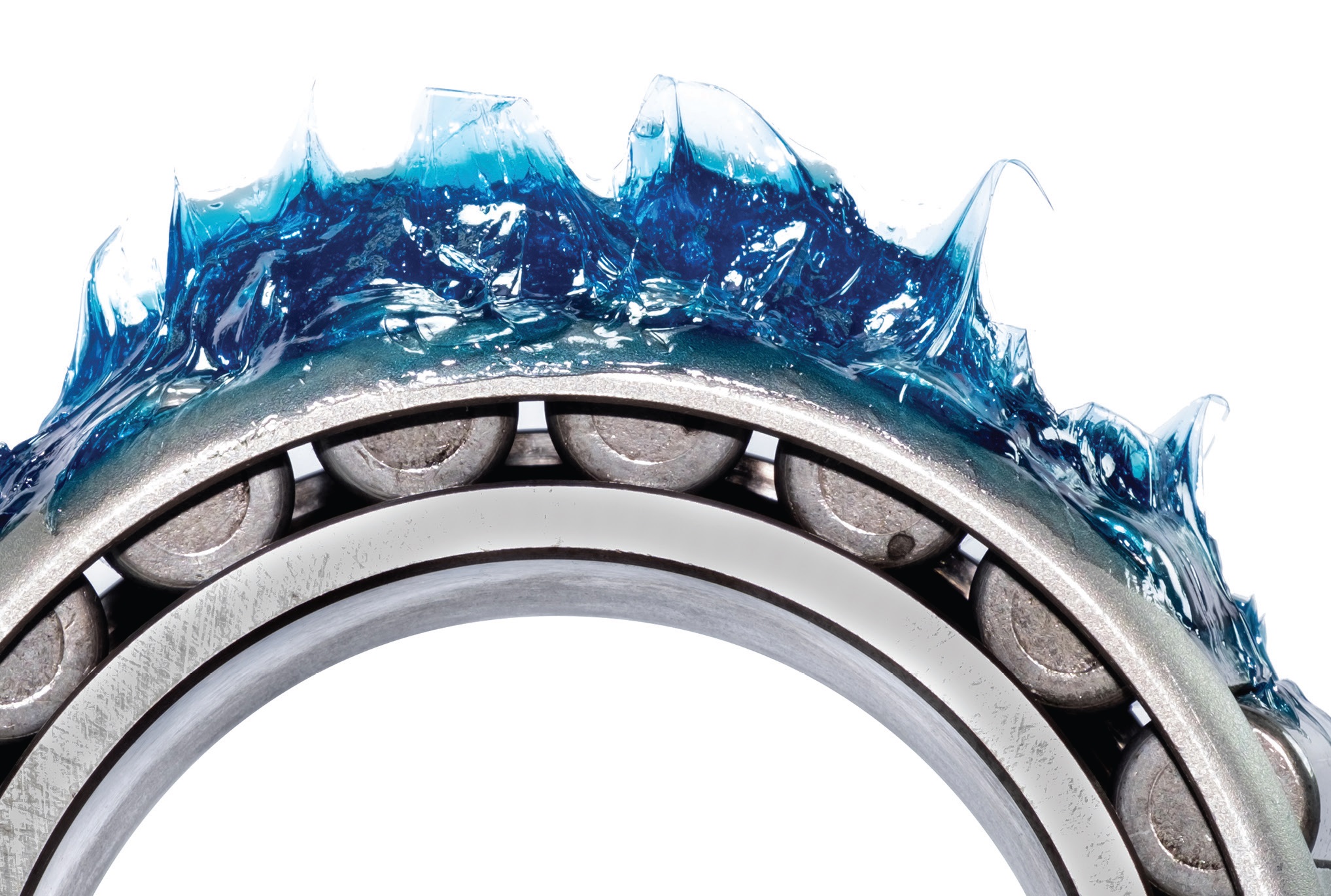
KEY CONCEPTS
•
Lubricating greases consist primarily of a base oil, thickener and performance additive.
•
Additives are the second most influential component of a grease.
•
Greases can be manufactured using different processes such as open kettle, closed kettle under pressure, autoclave/Stratco contractor process and continuous process.
Choosing a grease for a particular application requires understanding how the grease will hold up under operating conditions, which can include variable pressures and temperatures. Identifying the right grease can be challenging as the grease manufacturing process has dramatic impacts on the properties of the final product, and parts of the process require experience to fully control.
As stated in a 1952 article: “[A] major practical problem [for greases] is the provision of a structure that will stand up under shear and at all temperatures to which it may be subjected during use. At the same time, the grease must be able to flow into the bearing through grease guns and from spot to spot in the lubricated machine as needed and must not of itself add significantly to the power required to operate the machine, particularly at the start.”
1
These requirements have not changed with time and mean that every commercial grease must meet a number of requirements in order to perform successfully.
STLE-member Anoop Kumar, senior staff scientist with Chevron in Richmond, Calif., states that while advancements have occurred in how grease is made, “grease manufacturing is still considered an art because the properties of the final grease product hinge on so many factors, including the equipment used, the processing parameters, and the experience of the personnel involved in the manufacturing.”
In addition, STLE-member Evan Zabawski, senior technical advisor at TestOil, headquartered in Strongsville, Ohio, and TLT editor, notes that rheology is the science of deformation and flow of materials. Most solids are considered elastic (i.e., a material that when stressed will store deformation energy and recoil to its original shape), while most liquids are considered viscous (i.e., a material that when stressed does not store deformation energy and will start to flow). In other words, Zabawski says that “greases are viscoelastic materials, a little of both…greases are thick when at rest, and thinner under the application of shear, so they are described as shear thinning.”
Greases used for lubrication consist primarily of a base oil, thickener and performance additives.
Base oil
The base oil used in a grease influences high and low temperature properties, viscosity and thickening efficiencies. In relation to greases, Zabawski notes that “generally lower viscosity base oils are used for low-load/high-speed applications, and higher viscosity base oils are used for high- load/low-speed applications.” Greases have a high initial viscosity that drops with the application of shear to approximately the same viscosity as the base oil used in the grease.
Grease manufacturing is an art that continues to evolve as end-user needs develop and the market refines its requirements.
Kumar notes that “greases made with synthetic oil (e.g., polyalphaolefin) are expected to possess better high and low temperature characteristics compared to greases made with mineral oils.”
John S. Kay, vice president of engineering at STRATCO, Inc. and ECOPATH Holdings, LLC in Phoenix, Ariz., says that “naphthenic oils can result in lower thickener content that could improve pumpability in specific applications and improve other grease properties.” Certain synthetic oils also can offer special advantages under specific operating conditions, as well as offering material compatibility with seals.
Thickeners
The thickener is what sets a grease apart from a fluid lubricant. The thickener is a molecule, polymer or solid that is typically partially soluble in the lubricating fluid and imparts a semi-solid consistency to the grease. Soaps can be grease thickeners, while non-soap thickeners include polyurea, organophilic clays (e.g., bentonite) and other materials. Thickeners may be fibrous, spherical or platelets, and have an impact on the final grease properties. The following properties are impacted by the chosen thickener:
•
The
texture, which relates to the appearance and feel of a grease and affects its adhesiveness;
•
Dropping point, which is the temperature at which the grease releases a drop of oil under standard test conditions;
•
Shear or mechanical stability, which is the ability to resist permanent changes in consistency due to work;
•
Water resistance, which is the ability to withstand water without adverse effects on the grease’s structure;
•
Pumpability, which is the ability of a grease to flow under pressure through the grease dispensing system.
2
A simple or conventional grease is prepared by reacting a single organic acid with one or more inorganic bases, while a complex thickener is prepared from two or more organic acids (e.g., a primary soap [metallic stearate] and a complexing agent [metallic salt]).
3 The chosen agent modifies the grease characteristics and usually increases the dropping point, which is generally considered to be the temperature at which the thickener system fails, which helps to define the grease’s maximum service temperature.
Kumar says that thickeners are usually “prepared
in situ in a base oil involving a chemical reaction that can sometimes be highly sensitive to processing parameters like time, temperature, pressure/vacuum and agitation/mixing.”
Conventional lubricating greases are based on lithium, calcium, sodium, aluminum, barium or their complexes. According to a 2018 survey of worldwide grease production, 74.18%, by volume, contain lithium soap thickener.
4 The type of thickener influences grease properties such as temperature resistance, which relates to viscosity, and water washout, which is the ability of the grease to still perform and remain intact when submerged in water. Kumar notes that greases based on calcium, calcium sulfonate and aluminum complex thickeners are expected to possess better water resistance characteristics compared to sodium-based thickeners. Clay thickeners have no defined melting point, so they have been used in high temperature applications.
Kay notes that “the thickener would certainly be considered by many to have the most influence since this component is key to establishing the grease’s basic capabilities and determining its application.” The thickener type determines the type of application where the grease can be used (e.g., high temperature, excessive water or moisture exposure, electrical device suitability, food-grade). For example, lithium cannot be used in a food-grade grease, but aluminum can be. Kay says that “some thickeners actually have inherent property advantages that avoid the need for specialty additives.”
Additives
Kay notes that additives are the second most influential component of a grease, as additives supplement desired properties not provided by the thickener and base oil. A goal of additives is improving grease performance in stressful operating conditions. Zabawski says that “a common additive is a viscosity modifier that modifies the base fluid’s properties to enhance performance in highly variable temperature additives.”
Grease additives can also be solid materials, like graphite, to provide protection under heavy loads.
Kay says that additives “are specifically developed to improve finished grease properties in order to make them even more suitable for special applications.” Additives can enhance a number of different properties, including load bearing capacities, water resistance, oxidation stability, mechanical stability, lubricity and oil separation.
A wide range of materials can act as grease additives, depending on the final properties sought for the grease. Additives also can be solid materials, like graphite, to provide protection under heavy loads, or ceramic powder to protect in static high-pressure applications.
Manufacturing
Greases can be manufactured using different processes like open kettle, closed kettle under pressure, autoclave/Stratco contractor process and continuous process. Kumar notes that “processing makes a considerable difference” in the end product’s properties and performance. For example, lithium greases made through the Stratco contractor process are popular and an industry standard, while open kettle lithium greases, made through continuous process units, are still efficient for producing large volumes.
Kay says that manufacturing methods affect the properties of the finished grease, including oil separation, thermal properties, dropping point and even the reaction efficiency of the thickener components.
Richard L. Burkhalter, president of Covenant Engineering Services, LLC in Branson, Mo., notes that “most grease manufacturers utilize the open kettle process for making lubricating grease.” Some manufacturers use pressure reactors to create the thickener base, and then finish the grease product in open kettles. Burkhalter says that as lubricating greases are “a non-Newtonian, pseudo-plastic fluid,” the design of a grease manufacturing process contains many nuances. Some of these nuances have been well documented, but many others require experience to adequately address and control.
Zabawski says that after greases leave the reaction vessel, they typically go through a homogenizer or mill to break down the fibrous structure of the thickener—or to improve the dispersion of the base oil in the thickener. The amount of oil and the milling time needed depend on the consistency required of the final grease product.
Changes going forward
Both Kay and Kumar note that the increasing demand for lithium for lithium batteries in electronics and electric vehicles has led to pressure on lithium prices and its potential availability for use in greases.
5 Kay reports that the cost of lithium in India recently rose six-fold in a short timeframe. This may lead to pressure on manufacturers either to make these greases more efficiently or to develop alternatives to lithium if costs continue to rise.
Kay considers the most dynamic component going forward to be the additives, as each specialty additive manufacturer seeks to improve their product lines.
Burkhalter notes that the grease manufacturing process hasn’t changed much in the past 50 years, but recently work has been done to develop the use of Micro Wave (MW) for heating the processing reactor. This MW process is close to commercialization for the industry, in general, as it has the benefit of speeding up the manufacturing process and reducing energy costs, while also reducing required man hours. Burkhalter says process control is the area where major improvements are currently happening.
Conclusion
All of this information indicates that manufacturing of grease is an art that continues to evolve as end-user needs develop and the market refines its requirements.
REFERENCES
1.
Vold, M.J., and Vold, R.D. (1952), “Lubrication and Lubricants,”
J. Inst. Petroleum Technology, 38, pp. 155-163.
2.
Phillips 66 Company, (2012), “Premium Greases Guide: A Versatile Lineup of High-Quality Greases for all Major Industry Segments,” Available
here.
3.
Moon, M., Turner, D., and Tusznski, B., “Lubrication Fundamentals: NLGI Grease Glossary Definitions of Terms Relating to the Lubricating Grease Industry,” Available
here.
4.
Shah, R. and Braff, S. (Nov./Dec. 2018), “Lithium Ion Battery Demands and a Discussion of Lithium Supply Crisis: How Worried Should We Be?”
NLGI Spokesman, 82, (5), pp. 26-35.
5.
McGuire, N. (2020), “Lithium’s Changing Landscape: Marketers of Lithium Grease Thickeners Can Expect a Little Turbulence in the 2020s,” TLT,
76 (2), pp. 32-39.
Andrea R. Aikin is a freelance science writer and editor based in the Denver area. You can contact her at andrea.r.aikin@gmail.com.