The case of the failed bearing
Evan Zabawski | TLT From the Editor May 2020
Solving a murder using oil analysis.
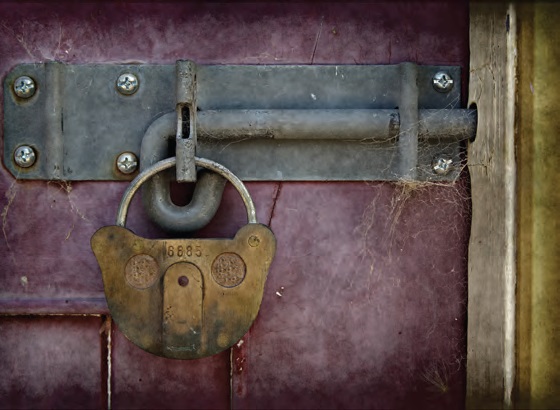
‘Understanding how to decipher causes from effects, while isolating critical information, is the key to solving it yourself.’
A locked-room mystery is an intriguing subgenre of crime or detective fiction wherein a crime, usually a murder, is committed where it appears impossible for the perpetrator to have committed the crime or evaded detection while entering or exiting the crime scene. This is a real, lubrication- related example.
The victim in our case is a failed pillow block bearing. It operates in a dry, dirty environment and its only recent maintenance was an oil change done nine months ago and regular quarterly greasing of its seals.
The overt evidence presented to us is via a post-failure oil sample, with the following abnormalities— very high wear metal concentration (predominantly tin, then iron, copper and lead), high particle count (maxed out the instrument) and analytical ferrography revealing high levels of rubbing wear (30-50 micron particles), sliding wear (>100 micron particles) and dust/dirt. The trend of the previous samples shows all these values increasing slowly over the last three years but jumping five-fold since the previous sample two months earlier.
The more subtle evidence arises from seeing that the stated oil is an R&O 68 whose baseline reveals no detectable calcium and a trace of phosphorus, but that the used oil sample has over 100 ppm calcium and over 200 ppm phosphorus, yet the viscosity is 67.9 cSt. The trend of the previous samples shows calcium and phosphorus increasing commensurately with wear metals, but that viscosity has remained unchanged.
Sifting through the evidence indicates that the elemental wear metals, rubbing wear particles and sliding wear particles are all just effects of the failure, not the cause. The calcium and phosphorus imply contamination or ingression from a different lubricant, yet the stable viscosity means either that the lubricant is of the same grade or that the contamination had no effect on the viscosity. To suggest the wrong type of lubricant caused the failure is questionable since a different additive chemistry, in the same grade of oil, would be unlikely to cause such an abrupt failure.
The particle count may be high, due to the wear metals, or it may be dust/dirt particles that caused the wear metals, or a little of both. The dust/dirt particles are the likely cause, but to suggest a dirty funnel or contaminated oil from a recent top-up introduced the dust/dirt could explain some of the particle count increase but does not explain the presence of calcium and phosphorus. What we must determine is how the dust/dirt, calcium and phosphorus are related to understand how the crime was committed.
To summarize: the victim is the bearing, the murder weapon is the dust/dirt, the high wear metal content is the proverbial blood on the floor and the bearing housing is the locked, or rather sealed, room. The pivotal pieces of information are the viscosity that did not change and the seemingly inexplicable appearance of calcium and phosphorus when it is not expected.
What single event would cause the calcium and phosphorus to appear in conjunction with a sharp increase in dust/dirt and particle count, to the point of a sudden, catastrophic failure? Solved it?
The solution is that the oil-lubricated bearing failed due to over-greasing. When the seals were last greased, some excess grease was forced into the oil (traces of a calcium-thickened, EP grease would explain the calcium and phosphorus without a viscosity change) but this also blew out the seals, allowing contamination from the dirty environment to enter in the form of dust/dirt and particle count. From there, the bearing abraded severely, shedding wear metals detected by elemental analysis and analytical ferrography, but also contributing to a further increase in particle count.
Like a good mystery story, all the clues were presented early on, but understanding how to decipher causes from effects, while isolating critical information, is the key to solving it yourself.
Evan Zabawski, CLS, is the senior technical advisor for TestOil in Calgary, Alberta, Canada. You can reach him at ezabawski@testoil.com.