20 Minutes With Amir Kadiric
Rachel Fowler, Managing Editor | TLT 20 Minutes May 2020
Imperial College academic collaborates with industry to address the latest challenges in reliability and efficiency of tribological systems.
Amir Kadiric - The Quick File:
Dr. Amir Kadiric is a Reader in Mechanical Engineering and a member of the Tribology Group at Imperial College London. He obtained his M.Eng. degree in mechanical engineering and a doctorate in tribology from Imperial College in 2005. He subsequently took a post at SKF’s Engineering and Research Centre in the Netherlands where he worked on research in rolling bearings. He returned to Imperial in 2007 to take up an academic position.
At Imperial, Kadiric is involved in a wide range of research and teaching activities. He teaches the undergraduate and master’s level Mechanical Transmissions Technology and Tribology courses in the department of mechanical engineering. The majority of his time is spent on research projects and supervision of postgraduate students and postdoctoral staff. His research is broadly concerned with tribology of machine elements, with a particular focus on failure mechanisms of pitting, micropitting and scuffing. In recent years, he has developed substantial
activities in the reliability and efficiency of electric vehicle transmissions.
A feature of Kadiric’s research is his close collaboration with industry, which helps to ensure that the fundamental research conducted in his labs at Imperial has a real-world impact. He currently works with several companies in the automotive, aerospace, energy and manufacturing sectors across Europe, U.S. and Japan. Together with STLE Fellow Hugh Spikes, Kadiric also leads the SKF University Technology Centre for Tribology at Imperial. Away from his day-to-day activities, Kadiric is a member of several technical committees and journal editorial boards in the field of tribology.
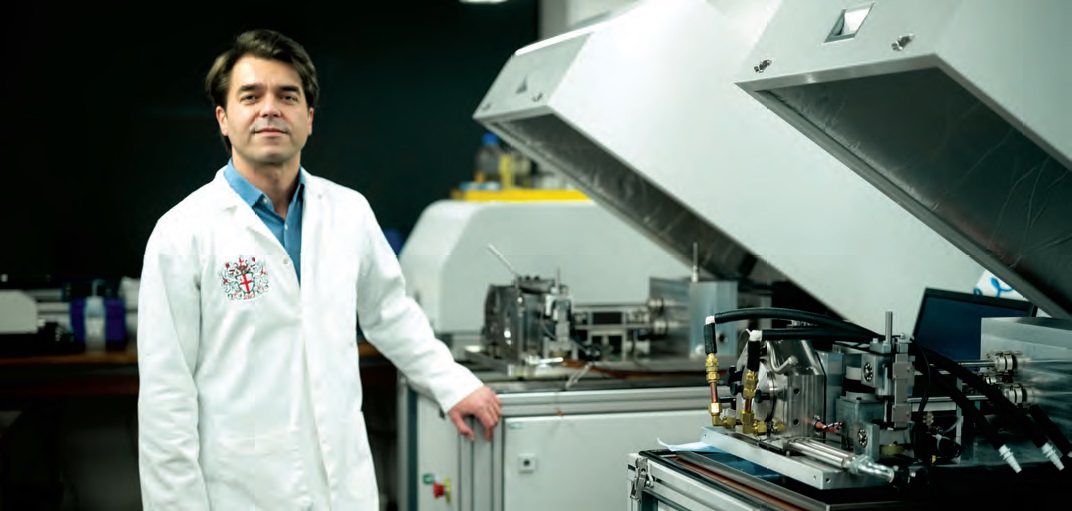
Amir Kadiric
TLT: Which areas of tribology is Imperial’s Tribology Group currently working on?
Kadiric: Our research group has always strived to cover all major aspects of tribology and it is no accident that our research areas, as well as the background of our staff and students, very much reflect the multidisciplinary nature of tribology. We have six members of academic staff and some 50 postdoctoral and doctorate researchers in our research group, so the range of topics we cover is very varied.
Nevertheless, some of the major research themes that my colleagues and I are working on include damage mechanisms in rolling-sliding contacts, including surface fatigue, scuffing and fretting, lubricant chemistry, particularly the mechanisms by which lubricant additives affect contact performance, development of novel methods to probe deeper into the contact including in-contact lubricant rheology measurements using spectroscopic, phosphorescence and fluorescence techniques, as well as new applications of the now well-established optical interferometry technique such as in situ observation of oil and grease films in an operating rolling bearing.
On the modelling side, we are develop truly multiscale models, starting from molecular dynamics simulations to better understand additive behavior and application of crystal plasticity for studies of damage accumulation in rolling contacts, through to rough surface contact tools and CFD models of EHD lubrication, to system level models such as, for example, a tribological model of a complete EV transmission. In practical terms and with the help of our industrial collaborators, this research is addressing current and future challenges in a wide range of engineering applications including EV transmissions, wind turbines, geared turbofan engines, heavy-duty internal combustions engines, biotribology, manufacturing applications and many others.
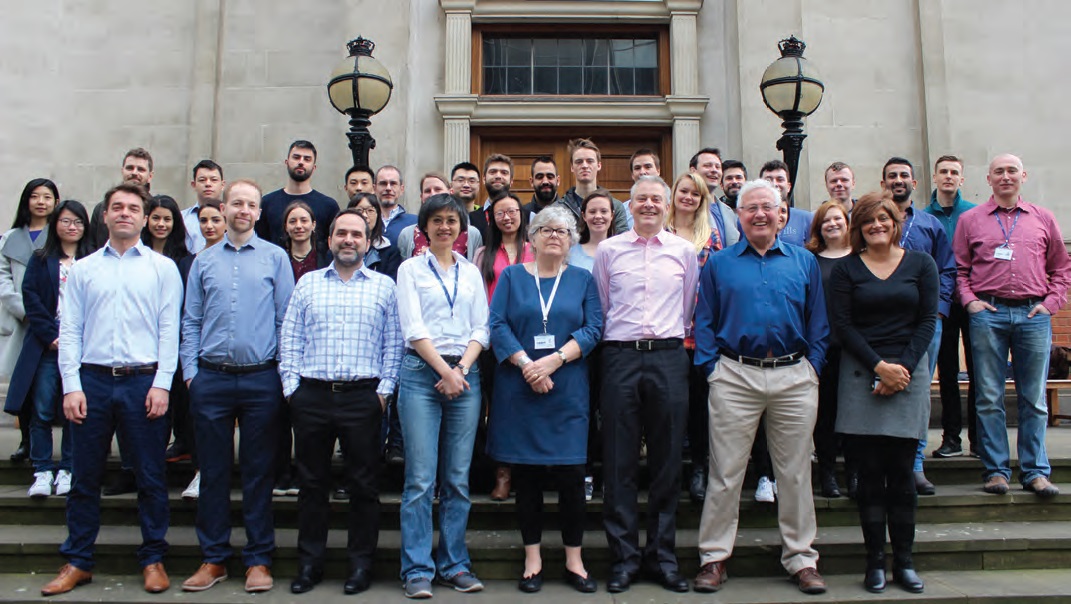
Members of the Imperial College Tribology Group.
TLT: How do you think vehicle electrification will impact your research?
Kadiric: As you may expect, this is already a major area of focus for me and it’s rather exciting to work on a subject that will have such profound effects, not only in terms of new technologies, but on society too. It is a great opportunity to conduct some fascinating and impactful research. Given my background, EV transmission design and operation are of particular interest and I have a number of projects in this area.
For example, we have recently developed a numerical model for prediction of EV transmission efficiency, which is able to account for the effects of lubricant formulation as well as gearbox design on the overall transmission power losses. This model is proving very useful in optimizing the transmission system for the intended vehicle use, including factors such as the number of gearing stages, number of gear ratios, gearbox thermal response and, of course, lubricant properties.
The critical aspect of this work and one of the major challenges in EV drive systems is accurate prediction of relevant temperatures throughout the gearbox. This is, of course, intricately linked to the transmission design but also to frictional and thermal properties of the lubricant itself. To account for this interdependence, we combine detailed tribological contact models with an iterative scheme to predict the whole gearbox thermal response and also utilize multiphysics modelling to obtain relevant heat transfer coefficients.
Additional challenges include developing new tools for prediction of gear churning and bearing losses at the high rotational speeds experienced in EV transmissions. The existing models are unproven at these conditions, particularly those encountered in the first stage of a typical EV transmission. In parallel, some of the newly developed EV fluids are throwing up challenges in terms of bearing and gear durability, and I am working with both lubricant and component manufacturers to address these.
TLT: You have significant research activities in failure mechanisms of tribological contacts. Can you describe your research within this area, particularly in regard to rolling contact fatigue mechanisms leading to micropitting and macropitting failures?
Kadiric: Historically, this has been an important subject for Imperial’s Tribology Group, with some of my predecessors, not least Ritchie Sayles, Andy Olver and Stathis Ioannides, making a vital contribution to the field. Clearly, I have some big shoes to fill.
My current efforts in the field are primarily aimed at improving our ability to predict rolling contact fatigue (RCF) lifetimes, particularly for surface-initiated failures which are dominant in modern machines. To do this, we have been investigating the relative contributions of crack initiation and propagation phases to the overall lifetime using novel experimental setups. This has shown that crack propagation is the dominant phase, which is not always fully accounted for in existing life models.
More specifically, we have identified two phases of crack propagation under rolling contact—one applicable to short cracks, tens of microns in length, where the propagation rates are very low with frequent crack arrest, and the second one for longer cracks where crack growth rates rapidly accelerate, leading to ultimate pitting failure. This behavior bears similarities to classical fatigue and, consequently, we have been exploring the use of classical fatigue prediction methods such as linear elastic fracture mechanics to predict the behavior of RCF cracks, too. This is ongoing work that combines experimental and numerical approaches but is showing some promising results.
In parallel, we are using modern analytical techniques to better understand microstructural changes in material subjected to cyclic contact stresses and enhance our understanding of very early crack growth. Combined together, these investigations should help us explain the full life cycle of contact fatigue failures, from crack initiation to eventual pitting.
We are using similar methods to study micropitting, given that it is fundamentally caused by the same mechanism of RCF. Here the recent focus has been on the effects of lubricant composition in relation to the local conditions at asperity contact level. For example, we have recently shown that the main way in which antiwear additives affect micropitting is through modification of asperity stress history: additives that build effective antiwear films at a very fast rate in the initial stages of rubbing prevent adequate running-in of contacting surfaces, which in turn increases the number and severity of asperity stress cycles and hence leads to more surface fatigue damage—and, thus, micropitting.
In contrast, ineffective antiwear additives largely prevent surface fatigue but lead to component failure through excessive wear. The optimum oil formulation provides controlled antiwear film growth rates to allow early running-in while minimizing subsequent adhesive wear.
TLT: Has this research also helped in understanding the phenomenon of white etching cracks, which have been receiving significant attention in the industrial and academic communities?
Kadiric: White etching cracks (WECs) are one example of practical importance of rolling contact fatigue. I must say that I have been somewhat surprised at the level of attention that WECs themselves have received, given that they are not a distinct failure mode but simply another manifestation of contact fatigue, which has been studied well before WECs became topical. WECs occur in many applications, but it is their apparent association with the early failures in wind turbine bearings that has received most attention.
Having a close collaboration with one of the major rolling bearing manufacturers, we have, of course, investigated WECs as part of our wider contact fatigue research. Many TLT readers are no doubt familiar with the plethora of theories that have been proposed as the driving mechanism of WECs. As is often the case with new research areas, we will have to wait for the dust to settle before we reach a universal agreement on the subject and in this respect, it is apparent that the initial frenzy of activity in this field is now subsiding.
Our research has shown that, regardless of all other factors, WECs are generated in a rolling contact by a specific contact stress sequence in time, namely a high but shortlived stress in the early stages of operation, which acts to initiate cracks early in life, followed by prolonged operation at moderate stress levels, which allows the crack faces of the previously formed cracks to rub together and hence produce the microstructural changes in their vicinity that are known as the white etching areas. Crucially, this same stress history is not well accounted for in basic fatigue life theories, owing to their reliance on linear damage accumulation rules which ignore the actual order in which different stress levels are applied.
Putting this together, one comes to the conclusion that WECs and the “earlier than predicted” failures, to use a more valid term than “premature,” are not necessarily directly linked at all; instead they are both a symptom of a third factor, a specific contact stress history. To move the subject forward, we should step away from WECs themselves and focus on improving our ability to predict fatigue failures under such variable stress history.
TLT: What major topics do you think you will be working on over the next 10 years?
Kadiric: Predicting the future is a thankless task but there are a few areas that will obviously attract increasing attention over the next few years. We have already talked about EVs and they are likely to keep us occupied for the foreseeable future. Another area that is likely to become more prominent, and one where we already have some activities, is the application of machine learning (ML) to tribology. It promises to provide some major breakthroughs in health and usage monitoring (HUM) of mechanical systems in particular, but perhaps also in helping us better exploit the vast quantities of experimental and numerical data generated nowadays in daily tribology research. On its own, ML is unlikely to provide much progress, so the key here will be in ensuring a successful combination of our physical understanding of fundamental mechanisms with the machine learning tools.
Last but not least, the next 10 years may well bring about some major advances in tribological materials. With the continuing drive for improved efficiency, the lubrication conditions and power densities of many machines are pushing current materials to their limits. Most of the steels used in tribological components such as bearings and gears are decades old and we are reaching the point where new materials are arguably the best way to make a step change in tribological performance of many machines.
TLT: You have research collaborations with several industrial partners and have also worked in industry prior to your academic career. What is the significance of industry collaboration to academic research in tribology and how do you ensure that such collaborations are successful?
Kadiric: Indeed, I work closely with many industrial partners from a wide range of industries, not only through long-term research programs, but also via technical consultancy projects. Seeing the real-world impact of my research and solving complex practical problems is arguably one of the most enjoyable aspects of my work. It is also an important motivating factor for my doctoral students.
In practical terms, having previous industrial experience certainly helps me in better defining research projects and communicating our research findings to our partners. As tribologists, we are fortunate to work in the field which has such wide practical importance and I would encourage tribology academics to make use of this to enrich their careers. Industrial collaborations are par for the course at Imperial College—we are a technical university that strives to conduct fundamental research with application in industry. In some cases, we have taken such collaborations a step further by setting up industry-sponsored University Technology Centers (UTCs). I lead one of these, the SKF UTC for Tribology.
Such centers, obviously, entail significant research investment from the partner, but invariably offer numerous benefits over and above those from single, ad-hoc research projects. They enhance the impact of academic research owing to a number of factors including better project definition, critical volume of researchers working in a given field and more effective dissemination of results through well-established communication channels. An additional benefit of these collaborations is that they provide an important recruitment channel for our partners, and many of our former doctoral students are now in leading industrial positions in Europe, U.S. and Japan.
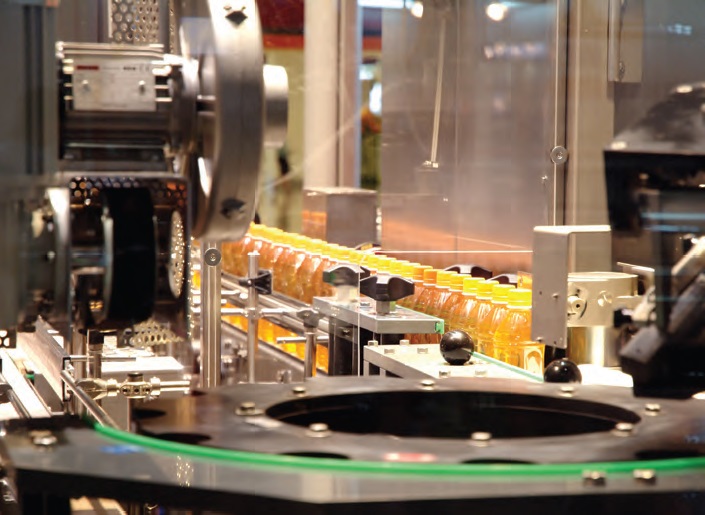
To improve efficiency, the lubrication conditions of machines are pushing current materials to their limits.
TLT: You are also involved in undergraduate and postgraduate teaching in tribology. How do students perceive the subject of tribology and what can we do to encourage more students to work in the field?
Kadiric: Yes, we are one of the few universities that offers a tribology course, available as an option to our third- and fourth-year undergraduate students, as well as to master-level students in mechanical engineering. I also lead the Mechanical Transmissions Technology course which involves many practical aspects of tribology.
I often hear tribologists bemoan the lack of interest in the subject and the lack of recognition of its significance, particularly within the younger generations. You may, therefore, be surprised to hear that both our Tribology and Mechanical Transmissions courses are some of the most popular and well attended courses in their respective groups, year after year. At Imperial, both lecturers and course content are regularly reviewed by the students themselves, and both of these courses repeatedly get positive reviews with students finding them stimulating and challenging.
Based on my experience, the key to making tribology popular is to ensure that students quickly become aware of its relevance to contemporary issues and practical applications that are of current interest. One way I try to achieve this is by using selected examples of our latest research in my undergraduate classes. For example, our students are acutely aware of the importance of renewable energy in today’s world, so I have used our research into the wind turbine transmission failures to illustrate to them the concepts of rolling contact fatigue. Geared turbofan aviation engines are another useful example, as are, of course, electric vehicles.
Away from formal teaching, my colleagues and I regularly participate in outreach activities, be it through evening tribology lectures to non-specialist audiences or exhibition stands at major science fairs in London. The message, I suppose, is that the talented young engineers and scientists are not at all averse to tribology. On the contrary, they usually jump at the opportunity to explore it once they are introduced to the subject in an interesting and challenging manner that is relevant to today’s world. It is up to us to ensure the latter.
You can reach Amir Kadiric at a.kadiric@imperial.ac.uk.