Sulfurized Additives: Types available, key applications and beneficial properties
Dr. Neil Canter, Contributing Editor | TLT Forum April 2019
Multifunctionality enables them to be used in key lubricant applications now and in the future.
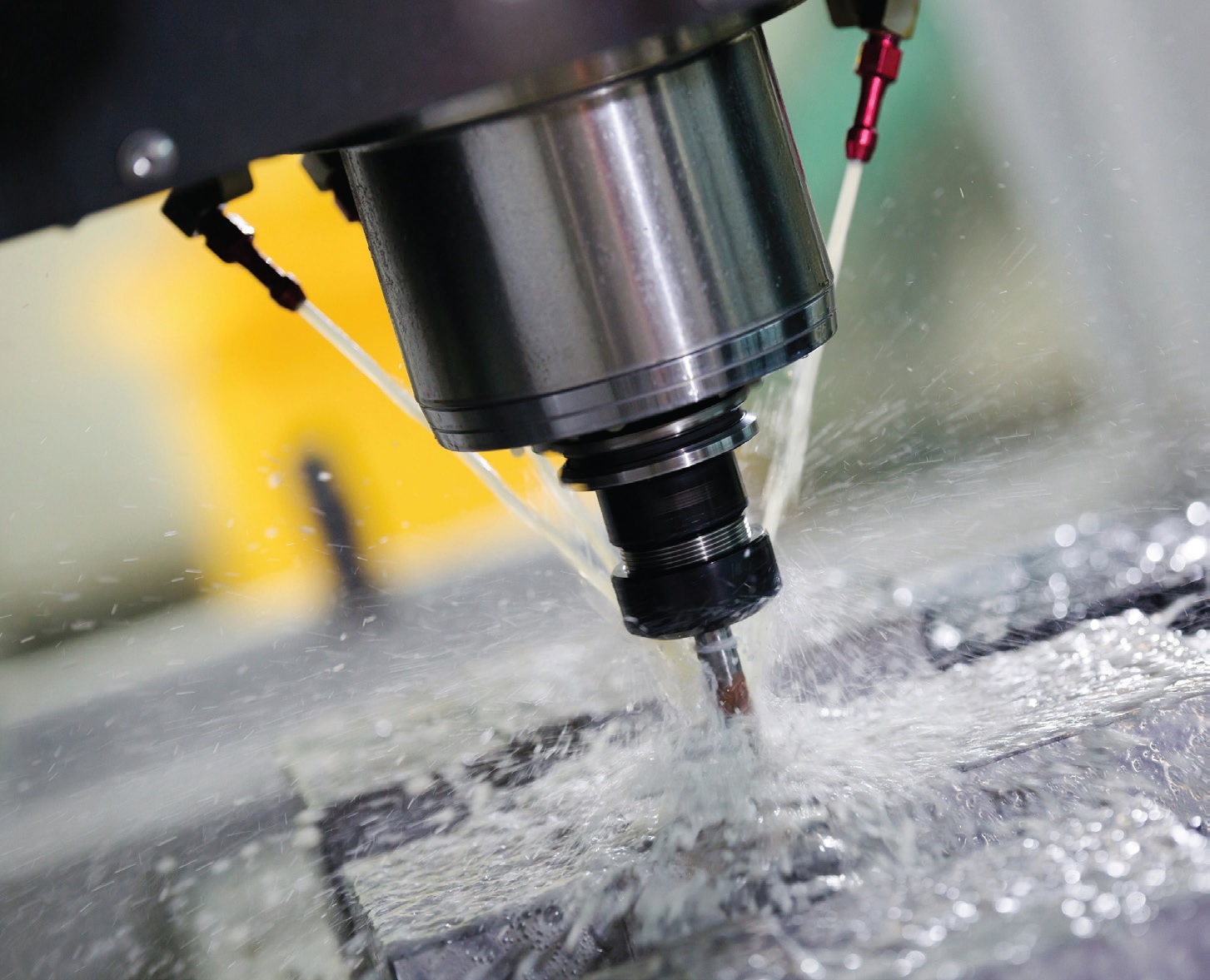
© Can Stock Photo / nd3000
KEY CONCEPTS
•
A wide variety of sulfurized additives are used in lubricants.
•
Sulfurized additives are used in at least five very important lubricant applications.
•
The future of sulfurized additives is bright in part because non-sulfur chemistry alternatives are facing environmental pressures.
The misleading headline on the cover of the October 2018 issue of TLT that states So Long Sulfur, the sub headline on the cover and the article titled Smarter Sulfur gave readers a confusing view about the current and future state of sulfurized additives (
1). TLT decided to use this article to speak with representatives from three of the major global sulfurized additive suppliers to gain their insights on the types of sulfurized additives used, their key applications and beneficial properties, how they are adapting to changing market conditions and trends and how they will be utilized by the lubricant industry in the future.
The three companies and six managers contributing to this article are:
DIC Corp., Kashima, Japan
•
Dr. Takafumi Iba, technical manager.
Lanxess Deutschland GmbH, Mannheim, Germany
•
Dr. Sandra Horstmann, application technology, sulfurized products
•
Dr. Steffen Sandhoefner, application technology, industrial lubricants
•
Thomas Rossrucker, head of application technology EMEA, lubricants additives business.
The Lubrizol Corp.
•
Udo Roehrs, technology manager, industrial additives, Hamburg, Germany
•
Dr. Gareth Fish, technical fellow, industrial additives, Wickliffe, Ohio.
TLT: What types of sulfurized additives are used in lubricants?
Horstmann: A great variety of sulfur-containing additives are used in lubricants. Typically sulfurized additives are described as organic compounds where the sulfur is bound either to a hydrocarbon or another sulfur atom. The products can contain oxygen as a heteroatom and are produced by reacting sulfur with unsaturated compounds such as olefins, esters and triglycerides.
Traditionally sulfurized fats are widely used in metalworking operations. The first milestone literature that reports this effect was published in 1918 by E.F. Houghton Corp. and involves its use in cutting oils (
2). Since that time, continuous development on sulfurization technology and raw material selection has taken place.
Currently sulfurized additive suppliers use far more sophisticated sulfur carriers, optimized to meet the demands of modern technology. The following product types are most widely used:
a.
Sulfurized esters: natural, vegetable or synthetic
b.
Sulfurized triglycerides (vegetable oils or animal fats or combinations thereof)
c.
Sulfurized acids (mainly long chain)
d.
Sulfurized olefins
e.
Sulfurized combinations from a-d in order to meet special performance requirements.
Roehrs: A wide variety of sulfurized additives are used in lubricants as shown in Figure 1. Key additives include sulfurized olefins, esters, fats and oils. Other sulfur carrier forms include ashless and metal-salted dithiocarbamates and thiophosphates, alkyl phenols and mercaptothiadiazoles. In addition, molybdenum disulfide is widely used in lubricating grease applications.
Figure 1.
Iba: Major sulfurized additives used in lubricants are sulfurized olefins, sulfurized triglycerides, sulfurized fatty acid esters and sulfurized fatty acids.
TLT: What are the key lubricant applications for sulfurized additives?
Roehrs: We know that sulfurized additives are used in five very important lubricant applications: metalworking fluids, engine oils, automotive transmission fluids, lubricating grease and industrial gear oils. Sulfurized additives are used for all types of metalworking processes, especially where heavy-duty operations demand tribofilms to extend tool life and preserve the surface finish of metal machined parts. Examples of operations include broaching, drilling and deep drawing of steel alloys. A variety of chemistries allow formulators the option to add sulfur to water-dilutable and oil-based metalworking fluids. They also serve as a suitable replacement for chlorinated additives for many types of operations.
Sulfurized additives are used in all passenger car, small engine and heavy-duty powertrain applications. The primary sulfurized additives formulated in these lubricants are dithiophosphates, dithiocarbamates and sulfurized olefins. Passenger car and heavy-duty diesel engine oils tend to use lower sulfur content additives while maintaining wear protection. Motorcycle applications use higher sulfur content sulfurized olefins as extreme-pressure (EP) additives to provide gearbox protection.
Polysulfides, sulfurized olefins, thiophosphates and thiadiazoles are used in a wider range of automotive driveline applications that cover axles, all types of transmissions (stepped, manual, continuously variable and dual-clutch) and wet brakes in commercial vehicles, construction machinery and farm tractors.
Sulfurized additives are used in industrial gear oils due to their EP capabilities because it is important to protect gears and bearings when operating under very high loads. Gearboxes are used in robotics, wind turbines, general industrial manufacturing machines, etc.
Fish: Sulfurized additives are needed in all applications where the grease is subjected to high load. EP grease accounts for approximately 50% of the global grease market (approximately 600,000 metric tons). Polysulfides, sulfurized olefins and fatty esters and dithiocarbamates are all used in lubricating greases. Sulfurized molybdenum dithiocarbamates and dithiophosphates are used to reduce friction. Molybdenum disulfide also is widely used as a solid lubricant.
For example, 90% of all rolling element bearings utilize grease as their lubricant of choice. Without zinc dithiophosphates and sulfurized EP additives, the performance of these bearings would be deficient.
Sandhoefner: As sulfurized additives are very versatile, their use is widely spread in almost all lubricants. The main applications are metalworking, industrial gear oils and bearings. Sulfurized isobutene (also known as SIB) is the typical sulfur source in gear oils; however, its distinct odor prohibits use in open systems such as those used in metalworking applications.
The largest use for the typical sulfurized products is in metalworking applications. The product type is selected depending on the metalworking process. In metal removal, the sulfurized additives main function is to support the cut, improve the operation and prevent tool wear. In metal forming operations, sulfurized additives form a pressure stable film and prevent adhesive wear. Some of the products are very tolerant to water and can be used in water-based systems. They show good hydrolytic stability and can therefore be used in water-miscible metalworking fluids or outdoor applications.
Plenty of other applications require one or more of the performance features provided by sulfurized products. Outdoor applications with a potential for the lubricant to end up in the environment are widely formulated with selected sulfurized products. Typical applications are greases used in the transportation industry. The sulfur carriers provide EP properties even at low outdoor temperatures in railroad switches and wheel flanges, ensure high lubricity on the fifth wheel of trailers or reduce the internal friction in wire rope greases.
Open gearboxes, chassis greases and wheel bearings are more examples where sulfur carriers are an integral part of the formulation, ensuring reduced friction and wear. In order for the equipment to achieve long life performance, inactive and specially synthesized sulfurized additives are used in greases in applications ranging from bearings to highly specialized lubricants for constant velocity joints.
Iba: Among the major applications for sulfurized additives are metalworking (removal and forming processes), greases and gear oils. Sulfurized olefins are frequently used for metal removal fluids to protect cutting tools and for better surface finish. High viscosity and relatively polar sulfurized triglycerides and esters are often used for this application, which requires not only EP but also low friction. These relatively polar molecules exhibit EP and oiliness effects by adsorption on the metal surface that effectively reduces friction to allow more efficient metal forming. Greases accept a wide range of sulfurized additives, but sulfurized esters tend to be avoided because they swell sealing materials. Those sulfurized olefins with high sulfur are especially preferred for gear oils that require protection under very high loads.
© Can Stock Photo / photovs
TLT: What are the beneficial properties of sulfurized additives?
Iba: Sulfurized EP additives react with the metal surface under extreme-pressure conditions to form metal sulfide tribofilms that prevent direct metal-metal contact. In metalworking operations, surface finish and tool life are improved due to sulfurized additives minimizing direct metal-metal contact. When sulfurized additives are used in machine lubricants, the tribofilm created prevents catastrophic failure.
Rossrucker: The beneficial properties of sulfurized additives depend widely on their composition. An important aspect is that sulfurized additives can either contain active (free/weakly bonded) or inactive sulfur (strongly bonded). Key performance benefits include their EP properties (i.e., the ability to prevent cold welding by efficiently separating two metal surfaces through formation of a sulfide layer). In particular, the active types show strong synergies with other additives such as overbased sulfonates, overbased succinimides and unsaturated esters.
The polarity of sulfurized additives can be adjusted/controlled by raw material selection. Depending upon the polar centers in the molecule and the polymeric structure, typical sulfurized products are very efficient lubricity additives covering a wide temperature range through formation of physical layers at lower temperatures and chemical layers at elevated temperatures.
Very inactive sulfurized additives exhibit mild antiwear properties and also may be used in environmentally friendly outdoor applications depending on the raw material selection. Inactive sulfur carriers show a synergism with aminic antioxidants, which is very distinct in low or even sulfur-free base oils.
Sulfurized additives also can act as friction modifiers.
Roehrs: In metalworking applications, sulfurized additives offer excellent EP properties for machining ferrous metals. Additional non-EP lubricity properties are provided by sulfurized esters, fats and oils for both ferrous and non-ferrous metals.
Zinc dialkyldithiophosphates (ZDDPs), dithiocarbamates and sulfurized olefins provide multifunctional properties in engine oils. They act as antioxidants and provide antiwear properties by reacting at high temperatures and pressures to form protective films.
Sulfurized additives also play multiple roles in driveline lubricants. Besides EP performance, reducing friction in gears and sliding contacts, metal deactivation/passivation and acting as scavengers, sulfurized additives play a role in managing complex friction performance in driveline applications such as in clutches, torque converters and wet brakes.
The main benefit that sulfurized additives impart to industrial gear oils is enhanced load-carrying properties of ferrous metals contacts.
Fish: High-performance greases cannot be formulated without sulfurized additives. Today it is impossible to pass industry standard requirements for EP greases without the use of sulfurized additives. Good 4-ball wear test performance cannot be achieved without the use of ZDDPs. Molybdenum dithiocarbamates and dithiophosphates have been shown to reduce sliding friction coefficients by up to 50% and give improvements in energy efficiency.
TLT: How have sulfurized additives adapted to changing market conditions and trends?
Roehrs: Newer sulfurized additives with lighter color, lower odor and various sulfur levels and activities have become broadly accepted by metalworking fluid formulators. Sulfurized additive manufacturers have adopted more sustainable backbone choices with excellent performance and stability.
While not an adaptation, sulfurized EP additives have experienced two main resurgences within metalworking in recent history. The first occurred with the discovery of synergies between sulfurized additives and other lubricity additives such as overbased calcium and sodium sulfonates more than 30 years ago (“Passive” EP system). The second involves the environmental scrutiny facing chlorinated paraffins in many regions and the effectiveness of sulfurized additives as replacements in many applications.
Mirroring other market applications, sulfurized additives used in driveline fluids have advanced in terms of effectiveness and efficiency, customer and end-user cosmetics (e.g., odor, color), regulatory and supply sustainability. They have been customized to work synergistically with complementary antiwear and friction modifiers to achieve higher overall standards of fluid performance.
Gearbox downsizing has increased the stress on industrial gear oils. This trend has led to the reoccurrence of some old failure mechanisms and the development of some new ones. To adjust, the balance of sulfurized additives and antiwear chemistry in additive packages has changed over recent years to enhance gearbox protection. The types of sulfurized olefins selected also have changed.
Fish: The Passive EP system also has been shown to be effective in enhancing the load carrying of certain types of grease. Lower-odor sulfurized EP additives have been applied to greases used in hand-assembled automotive components due to concerns about odor. One downside observed is that lower odor typically equates to a lower sulfur content. To deliver the same level of EP performance, a higher level of the lower-sulfur-containing additives is needed. For example, a 44 wt% sulfur polysulfide will deliver the same amount of sulfur at a treat rate of 0.25 wt% as 1 wt% of a 11 wt% sulfurized fatty ester. In many off-highway and construction machinery applications, levels of molybdenum disulfide of 5 wt% are still specified, despite the cost of the material increasing five-fold in 20 years.
Horstmann: The movement of metalworking operations from straight cutting to near net shape technologies, namely forming and fine blanking operations, has required the use of sulfurized additives with improved thermal stability and high lubricity while still being soluble in highly refined base fluids. This has led sulfurized additive suppliers to convert from uncontrolled sulfurization with just flowers of sulfur to higher quality raw materials and tightly controlled production processes.
Light color, significantly reduced odor and improved thermal stability have been in the focus, and additives have been developed with these properties to meet industry trends. Currently products can be synthesized to ensure solubility in modern base fluid such as Group III base oils and polyalphaolefins (PAOs).
Iba: Concern about the odor of dark-colored sulfurized additives that exhibit excellent EP performance, especially in high-loading, heavy-duty applications, led to the synthesis of light-colored sulfurized additives through cleaner reactions. These additives display much lower odor, improving their acceptance with lubricant formulators.
© Can Stock Photo / aleksanderdn
TLT: How will sulfurized additives be utilized by the lubricant industry in the future?
Roehrs: The future of sulfurized additive use will be bright in part because non-sulfur chemistry alternatives are facing environmental pressures. This is certainly the case in metalworking fluids, driveline fluids and lubricating greases.
In metalworking, sulfurized additives will provide lubricity and other benefits for all types of fluids and processes. Sulfurized additives will play a key role in future-proofing driveline formulations against regulatory pressures while enabling higher performing fluids to meet future efficiency and durability needs.
Dithiophosphate use in engine oils will continue, although a move toward lower phosphorus-containing oils could see their use diminished. Sulfurized olefins also will continue to be used, as there is no other equivalent performing antioxidant.
In industrial gear oils, sulfurized additives will continue to provide highly effective and proven lubricating solutions and other benefits for all types of fluids and processes.
Fish: EU Legislation from 2000 led to the banning of lead compounds and chlorinated paraffins and has placed regulatory scrutiny on borated additives. This means that in the EU, the only ready source of EP additives is based on sulfur.
In the U.S., some of these EU-banned additives can still be used with appropriate labeling in non-automotive applications, but they typically become hazardous waste once their useful life is over.
Iba: The role of sulfurized EP additives in lubricants will become more important because lower-viscosity base oils will be needed to enable machinery to reduce energy consumption. Demand for sulfurized additives will increase because the lower-viscosity lubricants will generate much thinner oil films on metal surfaces. This will lead to lubricants operating more extensively in the mixed and boundary lubrication regimes where EP additives are essential.
Sandhoefner: Not much change is expected in the use of sulfurized additives in metalworking fluids. Almost any type of metalworking fluid will continue to use sulfurized additives. In industrial gear oils, the increasing temperature and mechanical stress in gears may sooner or later require EP additives with improved thermal stability, but similar tribological features compared to the currently used sulfurized isobutene.
TLT: The future of sulfurized additives appears to be bright as they provide multi-functional performance characteristics that are critical to the successful preparation of lubricants for at least five key applications. Sulfurized additive suppliers have adapted to changing market conditions by developing new products that meet ever more challenging customer requirements.
In several cases, sulfurized additives have emerged as the sole option for certain applications because competitive additive chemistries have come under regulatory scrutiny. It is clear that the lubricant industry is recognizing the value of working with sulfurized additives now and into the future.
REFERENCES
1.
McGuire, N. (2018), “Smarter Sulfur,” TLT,
74 (10), pp. 46-56.
2.
Pressell, G. (1921), US Patent 1,367,428, assigned to E.F. Houghton & Co., Philadelphia, Pa.
Neil Canter heads his own consulting company, Chemical Solutions, in Willow Grove, Pa. You can reach him at neilcanter@comcast.net.