What’s up with detergents and dispersants?
Dr. Robert M. Gresham, Contributing Editor | TLT Lubrication Fundamentals January 2018
Both are surfactant subsets, but they differ greatly in their composition and interaction.
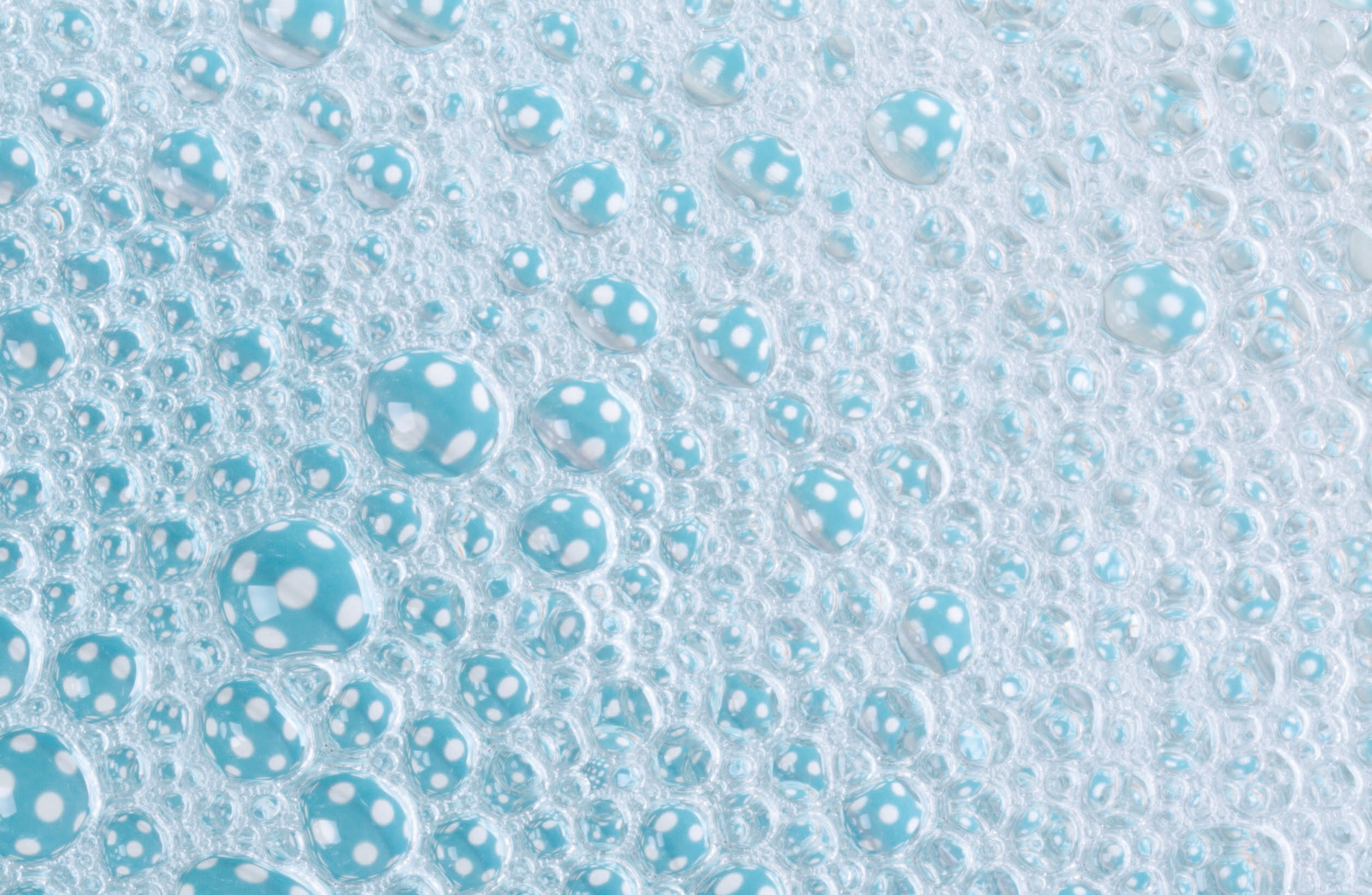
© Can Stock Photo / FomaA
AS A CHEMIST I tend to think about detergents and dispersants as all kind of the same under the general classification of surfactants. There are a gazillion different surfactants that perform thousands of tasks. That is, they all tend to interact with the surface of something, a solid or liquid, while in a fluid or mixture of fluids.
Another key property is that surfactants generally have the ability to dissolve in both polar and nonpolar solvents. While so dissolved, they can spontaneously form a variety of microstructures or organized groups of molecules. As a result, surfactants can be foaming agents, non-foaming agents, soaps, dispersants, detergents, boundary lubricants—the list is long.
In terms of lubricants, surfactants contribute toward lower friction and wear, help to lower emissions, improve filtration and cooling and provide solubilization and stabilized mixtures of polar and nonpolar materials.
Surfactants have in common a chemical composition characterized by a polar head, which can be ionic or nonionic, and a nonpolar tail, which is hydrocarbon like. Better terminology is a hydrophilic head and a lipophilic tail.
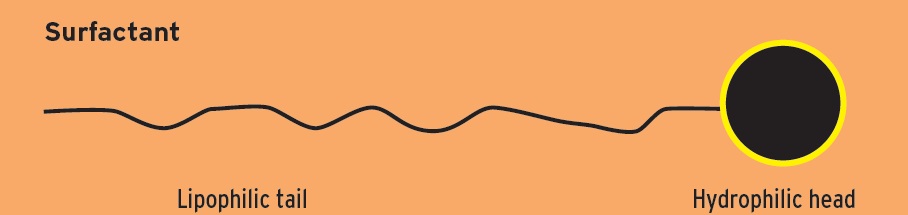
So detergents and dispersants are a subset of surfactants in general. Let’s take a closer look at the differences.
The first major difference is in their composition. Detergents contain metals like calcium, magnesium, sodium and barium as part of their hydrophilic head. Thus, they are soaps, the result of the neutralization of an organic acid with the appropriate alkaline earth metal. Detergents, especially those with pretty basic structures, even contain a reserve metal usually in the form of metal hydroxides or carbonates with calcium carbonate being the most common.
Detergents with this reserve are said to be overbased. Thus, detergents have the ability to neutralize combustion or oxidation byproducts as sulfuric and nitric acids and organic acids from oxidation processes. The reserve metal extends the effectiveness of the detergent.
Dispersants by contrast do not contain these metals and have little, if any, acid-neutralizing capability. Some dispersants do contain amine structures which are weak bases. For some applications where combustion is involved, such as engine oils, a downside of using detergents is that when burning they can leave an ash residue. Where reduced ash is required, some of the calcium carbonate is replaced with magnesium carbonate, which tends to form less ash.
Another key difference between detergents and dispersants is that dispersants have much higher molecular weight, by as much as a factor of 10 or so. Their polar or hydrophilic head contains oxygen or nitrogen compounds, known as ester dispersants or amine dispersants. Ester dispersants themselves are inherently neutral and thus do not have the ability to neutralize oxidation products. Amine dispersants can at least neutralize some oxidation products.
The molecular weight of the lipophilic tail of dispersants can fall into two types. Those with molecular weights on the order of 1,000-2,000 are called polymeric dispersants, and those with molecular weights of 25,000-plus are called dispersant polymers, which also can act as a viscosity index improver.
Detergents and dispersants are teamed with oxidation inhibitors and are called stabilizers or deposit-control agents. The oxidation inhibitor reduces the number of free radicals that form as a result of oxidation and/or combustion which, in turn, are precursors to deposits, varnish, sludge and soot formation. Detergents remove deposits and work together with dispersants to keep these entities in suspension in the lubricant. Thus, they also prevent the formation of large aggregates of these polar contaminants which can settle on surfaces. As a result, when the oil is changed these contaminants are removed along with the used oil.
As you might guess the largest application for detergents and dispersants (and anti-oxidants) are in engine oils where they can comprise as much as 80% of the additive package. They also are used in industrial applications where combustion or oxidation is anticipated, which can lead to varnish, soot, sludge formation and deposits.
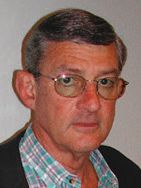
Bob Gresham is STLE’s director of professional development. You can reach him at rgresham@stle.org.