Compatibility of seals with oils and greases
R. David Whitby | TLT Worldwide November 2016
Choosing the correct lubricant is critical to preventing leakage and machinery failure.
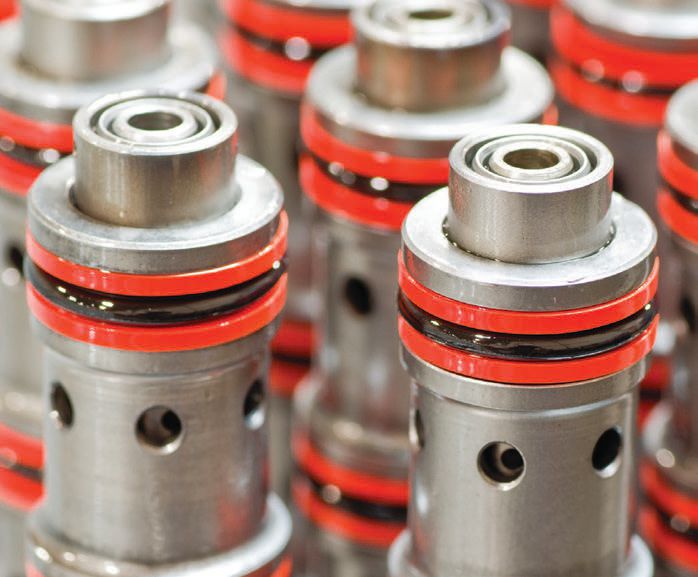
Numerous international, national and OEM tests can help you check for lubricant-seal incompatibility.
© Can Stock Photo Inc. / Scruggelgreen
A SEAL IS A DEVICE OR METHOD that prevents or at least minimizes the passage of a fluid between two surfaces. Seals can be static, dynamic or rotary. Static seals are found in applications in which there is no movement between the surfaces. Dynamic seals are used in machines where linear or reciprocating motion is part of the operation. Rotary seals, although also used in dynamic applications, experience surface speeds that are significantly higher than those found in reciprocating motion. Also, rotary seals are subject to continuous motion.
Commonly used static seals are O-rings, gaskets and metal rings. Commonly used dynamic seals include packing and piston seal rings. There are two main types of rotary seals: oil seals and mechanical face seals. An oil seal might be required to keep the lubricant in and keep solid, liquid and/or gaseous contaminants out. Spring-loaded oil seals are used to retain oils and exclude contaminants, while springless oil seals are used mainly for retaining greases. Many oil seals have an outer lip to keep dirt out, helping to protect the inner sealing lip.
The design of all dynamic seals is a compromise between leakage and wear, in the region in which the seal edges and the moving surface meets. With rotary seals, wear and friction are concentrated in one relatively small sealing band. As a result, rotary seals experience higher temperatures than dynamic seals.
Seals are made from elastomers (polymers) or plastics combined with secondary chemicals that impart specific properties. A seal functions significantly better and for much longer when it is lubricated continuously with an oil or grease that has a suitable viscosity for the application and is compatible with the seal material.
Unfortunately, some lubricants are not compatible with some sealing materials. Some lubricants swell seals, while others cause them to shrink. In both cases, the result is leakage of lubricant past the seal. Seals that become swollen are likely to become damaged or broken.
Some of the most commonly used sealing materials used in lubricant applications are:
•
Nitrile. General purpose, inexpensive elastomer for low-pressure applications; resistant to most mineral oils and greases but not brake fluids, some synthetic fluids or oils containing extreme pressure additives.
•
Viton. Excellent fluoroelastomers for high-temperature applications; resistant to phosphate esters and most mineral oils but not some diesters or polyolesters. There are four types of viton polymers, only one of which (a copolymer of hexafluoropropylene [HFP] and vinylidene fluoride [VDF]) is used for lubricant applications.
•
Polyacrylate. Good resistance to oxidation and temperature, compatible with most oils, including those with extreme pressure additives but not compatible with aqueous fluids.
•
Ethylene acrylic. An inexpensive, heat resistant elastomer that is compatible with most oils and greases.
•
Polyurethane. High-performance material that can be used for high-pressure applications and which is resistant to most oils.
•
EPDM. Ethylene propylene elastomer for high-temperature water, steam, brake fluids and phosphate esters but not mineral oils or greases.
•
Silicone. Generally used for static seals but not for dynamic sealing due to poor tensile strength.
•
Butyl. Compatible with phosphate esters and silicones but not mineral oils, polyalphaolefins, esters or polyisobutenes.
Because the issues with seal and lubricant compatibility are well known, there are numerous international, national and OEM tests to check for incompatibilities. In the U.S., the ILSAC GF-5 specification uses ASTM D7216 to test the volume change, hardness and tensile strength of polyacrylate, hydrogenated nitrile, silicone, and fluorocarbon and ethylene acrylic rubbers after immersion for 336 hours at either 100 C or 150 C. In Europe, ACEA specifies the CEC-L-039-96 Oil Elastomer Compatibility Test, which measures the hardness, tensile strength, elongation rupture and volume variation of five different sealing materials after immersion in a test oil for seven days.
Many OEMs, including Atlas Copco, Flender, Ford, Volkswagen, Mercedes-Benz, General Motors, Alison and others, have their own seal compatibility tests as well. These help ensure that the right sealing material is used for each lubricant application.
David Whitby is chief executive of Pathmaster Marketing Ltd. in Surrey, England. You can reach him at pathmaster.marketing@yahoo.co.uk.