Grease fundamentals: What color grease is best?
Dan Holdmeyer, Contributing Editor | TLT Lubrication Fundamentals May 2022
Who knows, but let’s determine what grease would best serve your specific needs.
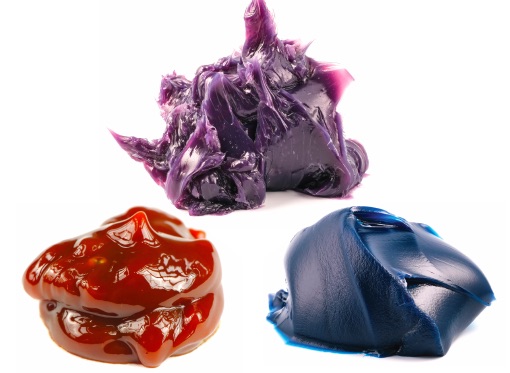
Per Wikipedia, “Grease is a solid or semisolid lubricant formed as a dispersion of thickening agents in a liquid lubricant.” To put that into terms I, an “Ole Plow Boy from Missouri,” can more readily understand: grease is a liquid lubricant containing thickeners so that it is a gelatinous lubricant that stays in place. There are three major components of grease: base fluid, thickener and additives.
The base fluid can be 55%-95% of the grease. Mineral oils are the most common base fluid used in greases today and suitable for moderate operating conditions. Synthetic base fluids such as polyalphaolefins (PAOs) are preferred for more severe operating conditions like very high or low operating temperatures, or for filled-for-life applications. Some of the more exotic synthetic fluids include esters, silicone oils, phosphate esters and perfluorethers, for extreme operating conditions.
Although the thickener can provide some lubrication protection, particularly in oscillating or very slow-moving applications, the base fluid of the grease provides most of the lubrication. Therefore, the base fluid viscosity needs to match the application. Higher viscosity oils are needed in high temperature and heavy load conditions, whereas lower viscosity oils are needed in high-speed applications. The optimum viscosity best meets the needs for all three of these parameters.
A lubrication specialist can help determine the specific base fluid viscosity for your application; however, following are some good, general guidelines for choosing the correct ISO viscosity grade.
• ISO VG 100 for electric motors and highspeed spindles
• ISO VG 220 for most general applications including over-the-road vehicle wheel bearings
• ISO VG 320 for higher loads and medium speeds such as off-road vehicle wheel bearings
• ISO VG 460 for highest loads, slower speeds and higher temperatures.
The most common base fluid viscosity grade used in greases in North America is ISO VG 220.
The thickener makes up 5%-30% of a grease and is the component that turns a liquid lubricant into a grease. The amount of thickener used directionally determines the consistency of the grease. The higher the thickener concentration, the stiffer the grease. There is a myriad of grease thickeners used today, and each one requires different concentrations in the grease to create the same consistency. Grease consistency is measured by ASTM D217, Standard Test Methods for Cone Penetration of Lubricating Grease, and reported as an NLGI Grade 000 to 6, where NLGI Grade 000 is a fluid to semifluid grease, and NLGI Grade 6 is a block of grease. NLGI Grade 2 is the most common grease used.
Switching from an NLGI Grade 2 to an NLGI Grade 1, or even 0, of the same “grease family” (i.e., same thickener, base fluid and additives) may be necessary in outdoor equipment during the winter for easier pumping, or indoors when long grease lines are part of a centralized greasing system. The NLGI Grade 2 is used in the summer, so the grease doesn’t soften too much in the summer heat and run out of the bearing.
NLGI Grade 00 and 000 are commonly used in enclosed slow speed gear sets to help reduce leakage relative to an oil.
Sort of counterintuitively, an NLGI Grade 3 is frequently recommended for very high-speed bearings. The rolling elements of the bearing push the grease just out of the rolling element path, allowing the rolling elements to “wick” enough oil from the grease to lubricate the bearing, and the grease is stiff enough to not slump back into the path of the rolling elements. The grease’s base oil viscosity for these very high-speed applications would be an ISO VG 100, or lower, to help lower the bearings internal resistance.
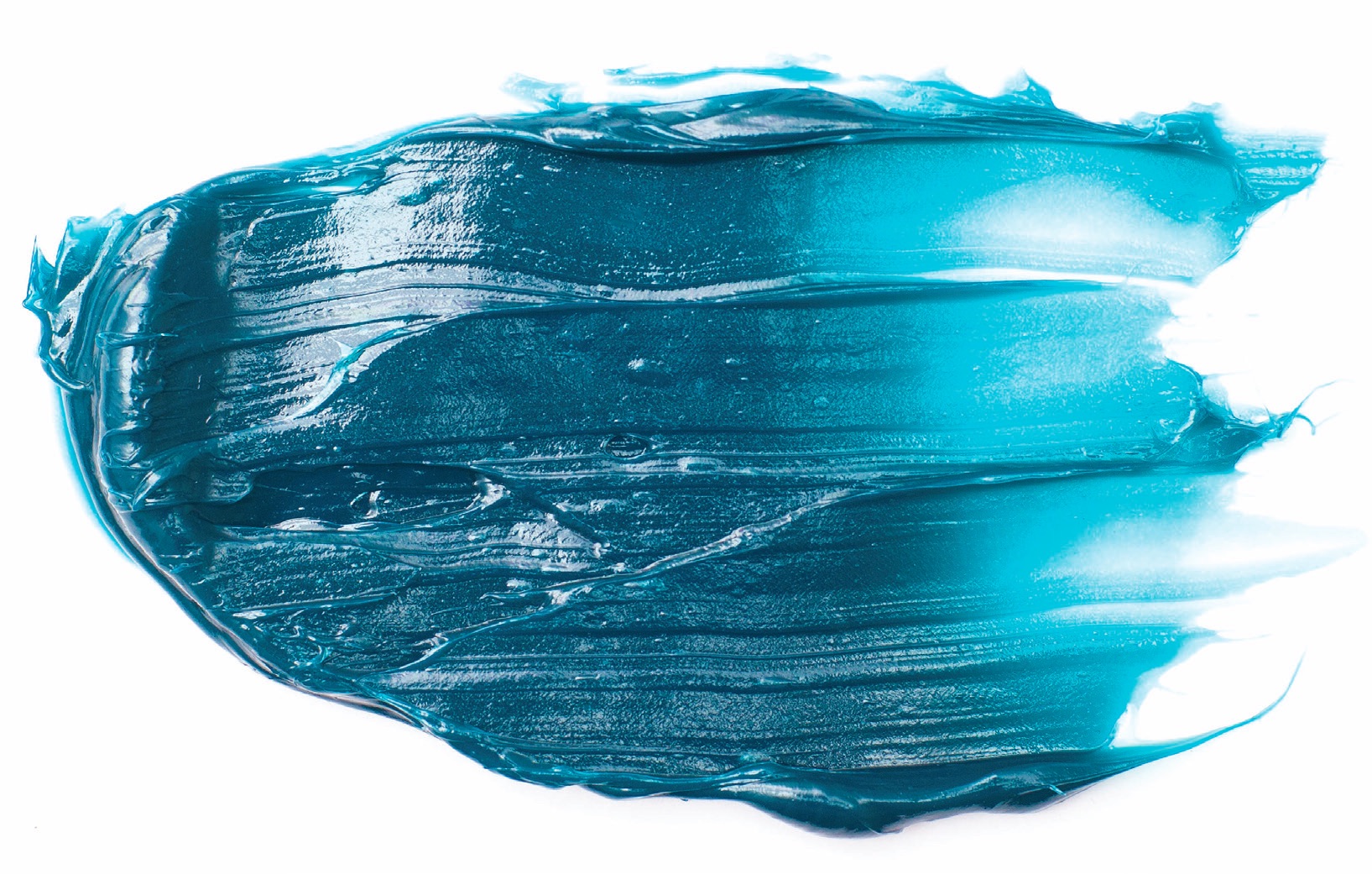
Switching NLGI Grades within a grease family is not an issue as usually the only change is the concentration of thickener used to change the NLGI Grade. However, switching from one grease family to another can be problematic, particularly if the thickener type is different. Some thickener types are incompatible with other thickener types. The incompatibility presents itself in a couple of ways. The first way is a significant change in consistency, either softening or stiffening too much. Too soft and the grease runs out of the bearing, starving it for lubrication. Too stiff and grease pathways become blocked, and regreasing becomes difficult, again starving the bearing of lubrication.
The most common thickener is lithium soap. Lithium simple soap and lithium complex soap thickeners make up more than 80% of the grease used in North America, and they are most likely compatible with each other. Complex thickener-type greases are more popular because of their higher operating temperature range and load-carrying capabilities compared to simple soap thickener types.
When dissimilar thickeners are mixed in an application, incompatibility is a real possibility, and purging of the old grease is highly recommended. Some other soap thickeners are aluminum, calcium, barium and sodium. Other non-soap thickeners include polyureas, silica, clay, calcium sulfonate and others. When it is determined necessary to switch to a dissimilar thickener, compatibility testing should be done between the grease currently in use and the proposed grease. This will help determine how much purging of the old grease is necessary. Always purge if possible. If purging is not possible, monitor application temperatures to be assured the application is not starving for lubrication.
Compatibility testing involves mixing different concentrations of the greases (1:1, 1:2 and 2:1) to see if the consistency or dropping point changes significantly from each of the two greases’ specifications. If the grease mixtures soften significantly, the regreasing interval may be shortened to replenish the grease until only the new grease is in the bearing. This is an alternative option to purging. If the grease mixtures stiffen significantly, then purging is necessary. Purging can be accomplished even without a purge plug by pumping in the new grease, removing the grease zerk and allowing the bearing to operate for about 10 minutes and, thus, purge itself of any excess grease. Repeat this step until only the new grease is purging from the grease zerk opening. Be sure to replace the grease zerk after purging.
The other part of the compatibility testing looks at the dropping point of the grease mixtures relative to the two greases’ specifications. This is critical when the application is operating within approximately 150 F of the dropping point. Lubricated parts should be approximately 150 F cooler, or more, than the grease dropping point. Dropping point is the temperature at which the thickener can no longer hold oil in place; essentially the grease is no longer gelatinous but liquid and will not stay to lubricate. This is a specification listed on most grease technical data sheets.
Characteristics other than compatibilities and temperature limits are affected by thickener type. Water spray off, water washout, shear resistance, pumpability, oil separation and elastomer (think seals) compatibility are all affected by thickener type, and even within a thickener type, there are variations in these characteristics. The nuances are too numerous to get into here, but know that these performance characteristics for each grease should be available from your grease supplier.
Additives constitute up to 15% of the grease, and many of the additives found in lubricating oils are utilized in grease. Some of those additives include corrosion inhibitors, oxidation inhibitors, antiwear additives and extreme pressure (EP) additives. Corrosion inhibitors are critical in wet or moist applications to protect metal surfaces. I’m thinking of boat trailer wheel bearings that are frequently submerged in water while loading and unloading boats through submersion in the recreational water reservoir or stream. It is a good practice to regrease boat trailer bearings, if possible, at the end of the boating season to purge out water contaminated grease with fresh grease. Oxidation resistance is key in hot environments, particularly considering that grease has relatively low chance to remove heat from the source, unlike a circulating oil. While most greases will incorporate additives to minimize corrosion, oxidation and wear, not all greases will have EP additives. Grease with EP is a demarcation from other greases and should be considered when lubricating heavily loaded, or start-stop, applications. EP greases should not be used in electric motor bearings as the EP additives are corrosive to the insulation in the motors’ windings that may short out due to over greasing.
Molybdenum disulfide (moly) and graphite are solid (non-soluble) additives used in grease and rarely used in lubricating oils. Moly or graphite are commonly used on the fifth wheels of over-the-road trucks and in the bushings of the feet of construction equipment outriggers. These applications are under heavy load and do not have enough movement or rotation to generate an oil wedge that would separate the moving parts; thus, the solid lubricant maintains the lubricant film between the moving parts. These solid lubricant additives should not be used in rolling element bearings, e.g., wheel bearings, since the solid lubricants may damage the rolling elements and raceways.
Polymers may be added to provide “tackiness” and give the grease a “stringy” appearance that may enhance water resistance. Shear stability of these additives, as well as the thickener itself, is critical to maintain performance throughout the regreasing interval.
Not that you’ve become an expert from reading this article, but you now have the knowledge to ask the right questions before deciding on a grease for your application. For automotive applications, NLGI helps with its automotive wheel bearing and chassis lubricant certification. An NLGI GC-LB certified grease has been tested and meets key characteristics required for automotive applications. For non-automotive applications, the key grease properties to consider are:
• Thickener type: Is it compatible with the grease in use?
• Base fluid viscosity: Most applications are fine with an ISO VG 220, but load, speed and temperature variations may indicate a different ISO viscosity grade.
• Grease consistency: Most likely an NLGI Grade 2, or if in a cold environment or pumping through long grease lines, a softer NLGI grade may be warranted.
• Extreme pressure additives: As long as it is not in an electric motor.
• Solid additives: Only in journal bearing and bushing applications with limited movement.
• Dropping point: If the application operates above 200 F, consider synthetic base fluids.
• Water resistance: Is the application exposed to water contamination?
Grease color is not a consideration to determine what grease meets your application needs. The coloring dyes added to grease have no impact on its performance.
Grease color is used for marketing purposes and identification purposes only. Color can help users know they are using the right grease if different greases, of different colors, are in inventory for specific applications at a site.
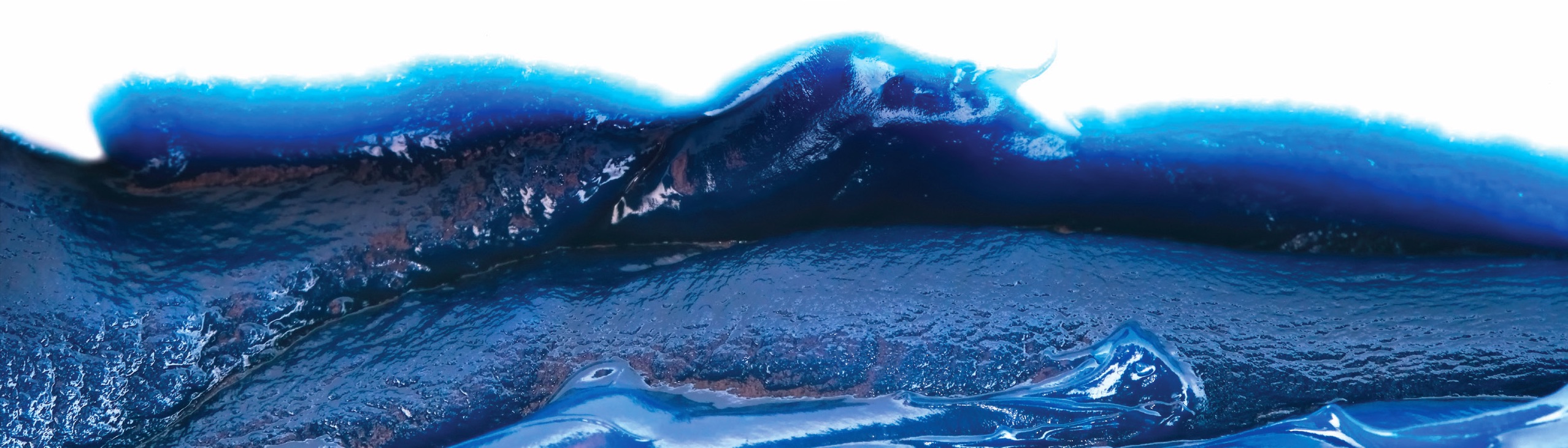
Dan Holdmeyer is retired from Chevron Lubricants and is based in Washington, Mo. You can reach him at dan.holdmeyer@gmail.com.