Mistaken identity
Evan Zabawski | TLT From the Editor April 2021
The correct answer is not always true or false.
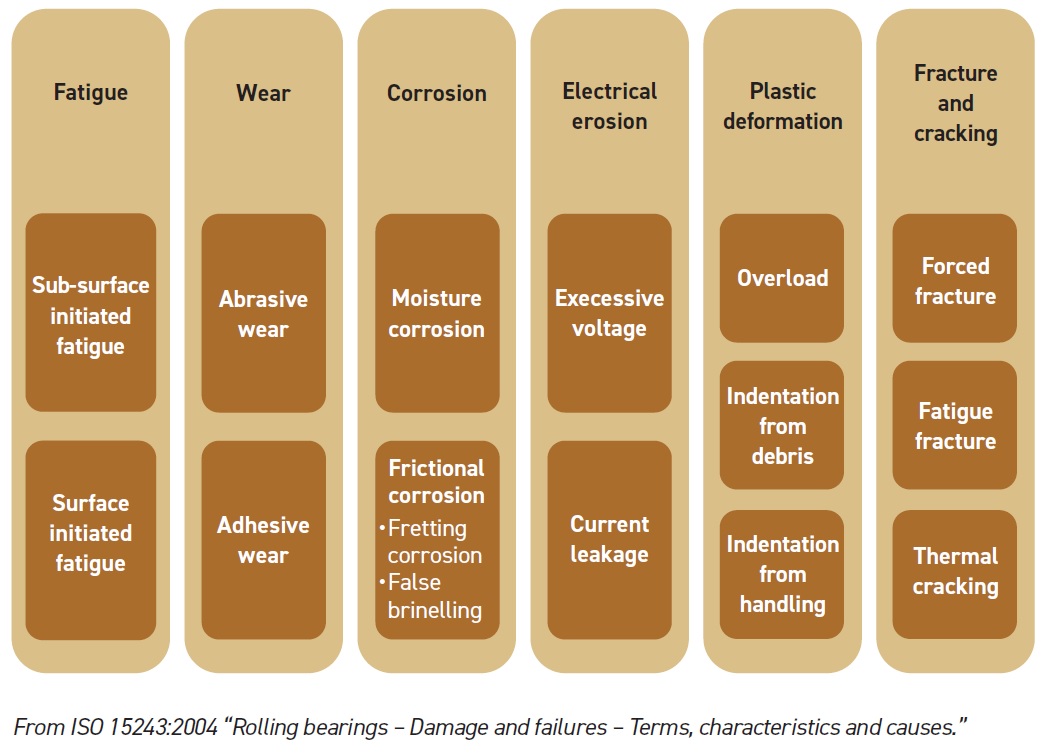
Ask three bearings experts what type of damage appears as evenly spaced, shallow dents in the raceway of a rolling element bearing, and you might get three different answers: true brinelling, false brinelling or fretting corrosion. But give them a detailed description of these dents, plus the color of the wear debris, and they will likely all settle on the same answer—so how do they know?
The term brinelling comes from the first widely used and standardized hardness test in metallurgy that was proposed in 1900 by Swedish engineer Johan August Brinell. The test measures the diameter of indentation (called a brinell mark) caused by a 10 mm diameter steel ball under a force of up to 3,000 kgf against the test piece—the smaller the indentation, the harder the material. When a stationary bearing is overloaded by a static load or a shock load, it might suffer shallow plastic deformations at the evenly spaced, rolling element/raceway interfaces. Due to the similarity in appearance to a brinell mark, this damage is termed true brinelling.
While true brinelling tends to produce shiny indentations, similar smooth polished indentations were purportedly discovered in the 1930s in the wheel bearings of new automobiles immediately after they were unloaded from being transported by train. This damage was traced to the rocking motion imparted to the automobiles by the train car impacting the track joints, and led to the first research on this wear by John O. Almen of the General Motors Research Corp. in his paper “Lubricants and false brinelling of ball and roller bearings,” published in the June 1937 issue of Mechanical Engineering.
Though true brinelling is a form of plastic deformation without material loss, false brinelling is mild adhesive wear caused by small, cyclic vibrations, resulting in material loss in the form of magnetite wear particles. The physical distinctions between the two is that true brinelling indentations should have raised shoulders and still show machining marks, while false brinelling indentations will not have raised shoulders and should appear bright or fretted, coupled with black wear particles eventually surrounding the wear scar.
A third type of wear that is commonly mistaken as false brinelling was first investigated by George A. Tomlinson in his paper “The rusting of steel surfaces in contact,” published in the Proceedings of the Royal Society of London in 1927. This wear was eventually coined fretting corrosion shortly before May 1939 when Tomlinson published his next paper, “An investigation of fretting corrosion of closely fitting surfaces.”
What differentiates fretting corrosion from false brinelling is that fretting corrosion occurs in unlubricated conditions, whereas false brinelling occurs under boundary film lubrication. Fretting corrosion is accompanied by corrosion, an oxidation reaction that produces the iron oxide hematite in steel surfaces. Hematite particles are red and not magnetic, in contrast to false brinelling’s black magnetite particles, which are strongly magnetic. Though the wear mechanisms differ—false brinelling is mild adhesion, and fretting corrosion is severe adhesion—fretting wear might cause false brinelling to progress into fretting corrosion if the fretting wear debris dams the oil from the contact surfaces.
The international standard ISO 15243 contains six primary classifications for rolling bearing damage and failures, each with two or three subcategories. True brinelling is classified as overload, one of three subcategories under the primary classification plastic deformation. Another primary category is corrosion, further subdivided as moisture corrosion and frictional corrosion. Frictional corrosion is further subdivided into fretting corrosion and false brinelling, showing how closely related they are, and that false brinelling is classified under corrosion rather than wear, as is common in other publications.
Ultimately, a close inspection of the wear surfaces—in conjunction with noting the color of any wear debris—should allow anyone to determine the correct type of damage, causing evenly spaced, shallow dents.
Evan Zabawski, CLS, is the senior technical advisor for TestOil in Calgary, Alberta, Canada. You can reach him at ezabawski@testoil.com.