Next generation driveline lubricants for electrified vehicles
Berly McCoy, Contributing Editor | TLT Webinar March 2021
Tribology can help improve efficiency and performance in electric and hybrid electric vehicle transmissions.
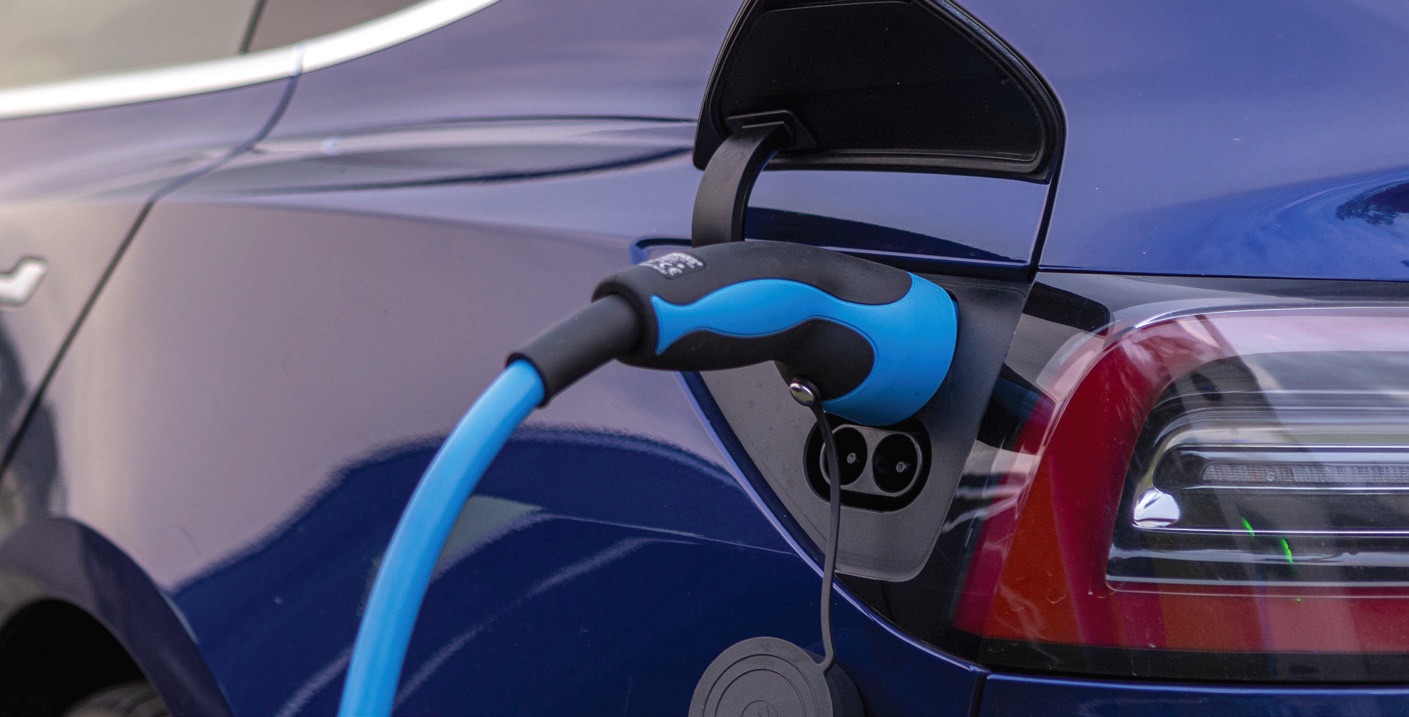
KEY CONCEPTS
•
The sale of electrified vehicles is growing faster than expected, with hybrid electric vehicles (HEVs) and electric vehicles (EVs) projected to make up 50% of the market by 2030.
•
The automatic transmission fluid currently used to lubricate HEVs and EVs is not optimized for
efficiency.
•
Lubricant formulators for HEVs and EVs should focus particularly on thermal conductivity, material compatibility, copper corrosion, electrical resistivity, aeration and wear.
MEET THE PRESENTER
This article is based on a Webinar originally presented by STLE Education on Aug. 18, 2020.
Generation Driveline Lubricant for HEV/EVs is available at
www.stle.org: $39 to STLE members, $59 for all others.
STLE member Dr. Arup Gangopadhyay is a technical leader of powertrain tribology in energy, propulsion and sustainability in research and advanced engineering at Ford Motor Co., where he has worked for more than 30 years. His research focus is on reducing friction and wear in powertrain systems, as well as understanding the interaction between lubricant additives and surfaces and coatings, with the ultimate goal of improving fuel economy. He has published 80 technical papers, holds a number of U.S. patents and was awarded the Engineering Society of Detroit’s Gold Award in September 2020, which honors exceptional engineers and scientists. He has served as a board member for the STLE Detroit Section since 2000 and also served two terms as an STLE board member. He was elected an STLE Fellow in 2004.
You can reach Gangopadhyay at
agangopa@ford.com.
Dr. Arup Gangopadhyay
In the U.S., fuel economy for light-duty trucks and passenger cars has been trending upward since 2005 and 2010, respectively, having remained relatively flat for years. In 2020, the Department of Transportation and EPA issued a new standard
1 requiring that the average fuel economy of these vehicles reach 40.4 miles per gallon by 2026, which would require an incremental improvement in fuel economy of 1.5% per year. Replacing internal combustion engine vehicles with electrified vehicles, which include electric vehicles (EVs) and hybrid electric vehicles (HEVs), will be an important part of meeting this challenge.
Like fuel economy, sales of electrified vehicles have been trending upward as well over the past decade. Data from Boston Consulting Group’s 2020 global automotive powertrain forecast2 has shown that sales of electrified vehicles are growing—and will continue to grow—faster than previously expected. This growth is due to a number of driving forces including tougher emission standards, increase in the number of EV charging structures, government incentives and reduced total cost of ownership due to falling battery prices. Boston Consulting Group predicts that 2030 will be the tipping point at which electrified vehicles will make up more than 50% of the market, with battery-powered electric vehicles (BEVs) and plug-in hybrids (PHEVs) composing a quarter of the market.
2
While this demand has led to innovation in electrified vehicle hardware, formulation for efficient lubrication has lagged. The current standard for lubricating electrified vehicle drivetrains is automatic transmission fluids (ATFs), which is not optimized for HEV and EV performance. Because components of HEV and EV motors come into contact with the transmission fluid, formulators need to keep material compatibility in mind. One prime example is considering metal compatibility, especially with copper. While controlling for copper corrosion is a concern, electrified vehicles also can contain other metals, like neodymium-based permanent magnets. Though the latter is usually protected from fluid by a covering and, thus, is a secondary concern, possible exposure during repair means a lubricant would ideally be compatible to these components as well. Outside of metal compatibility, formulators also need to consider non-metal components that a lubricant will contact, such as elastomers and polymers. And material compatibility isn’t the only thing tribologists need to keep in mind when designing lubricants for electrified vehicles.
Fluid considerations
The ATF that is commonly used today for electric motor lubrication is generally fill-for-life and low viscosity. While it has adequate electrical resistivity, it has not been optimized for HEV/EV applications and is, in turn, limiting performance.
The current fluid requirements for ATF include:
•
Copper corrosion
•
Aeration
•
Wear
•
Oxidation
•
Clutch friction durability
•
Cycling test
When designing driveline fluids for electrified powertrains, an important performance consideration is improving thermal conductivity. This helps take heat away from the metal windings and cool the motor. Improving thermal conductivity also allows more current to pass through the motor, which, in turn, increases the torque output and/or allows the size of the motor to be reduced to improve packaging efficiency. Additional performance requirement considerations include increasing the thermal capabilities to 150 C (existing fluid is one of the limiting factors due to limiting the current), improving or maintaining electrical resistivity and improving fluid oxidation stability, copper corrosion and material compatibility (e.g., compatibility with laminates, insulators and rare earth materials).
STLE member Dr. Arup Gangopadhyay, technical lead of powertrain tribology at Ford Motor Co., says “These properties should be maintained both when the oil is fresh and aged because we are looking for ‘fill-for-life’ oil,” so formulators should aim to reduce the amount of degradation in these properties over time as much as possible. These desired future fluid properties apply for powersplit transmissions as well as e-axles. In these two applications, clutch friction durability and cycling tests are not necessary because there are no clutches present. P2 transmissions, which include clutches, also will benefit from these enhanced properties.
This article is based on an STLE Education Webinar presented Aug. 18, 2020, by Gangopadhyay. See
Meet the Presenter for details.
Winding temperature
The main components of an electric motor are the stator and the rotor. When electric current is passed through the copper wire windings in the stator (
see Figure 1), the subsequent creation of a magnetic field turns the rotor, which generates mechanical motion. During this
process, the copper windings heat up due to resistance.
Figure 1. Stators with exposed copper windings. Temperature increases as a result of current decrease efficiency.
To determine the best way to cool the electric motor, Gangopadhyay and his team focused on investigating how to decrease the winding temperature. “We’d like to get about a 15 C drop in the winding temperature,” Gangopadhyay says. “If we achieve that, we can get a substantial improvement in torque or allow for a significant decrease in the size of the motor or a combination of the two.”
Gangopadhyay’s team developed a mathematical model in order to predict electric motor winding temperatures. It’s a heat transfer equation that is a function of viscosity, specific heat and thermal conductivity. Using this equation, they found that the heat transfer coefficient is most impacted by thermal conductivity, whereas specific heat and viscosity have a much smaller effect (although they also are important) (
see Figure 2). Based on the model, a 50% improvement in thermal conductivity or a 50% improvement in specific heat (which would result in improvements in thermal conductivity) with a constant viscosity would result in a 15 C drop in winding temperature. When the team applied the model to current developmental fluids, Gangopadhyay found most have only achieved a 3-7 C drop in winding temperature.
Figure 2. Graph of the resulting surface temperature of copper windings when one of three parameters is varied: viscosity (v), thermal heat capacity (Cp) or thermal conductivity (k). Varying thermal conductivity results in the largest temperature decrease.
How to move forward
It is clear that there is a need for more efficient HEV/EV fluids. But to realize those needs, the field needs a better understanding of the mechanism of heat transfer in the lubricant (i.e., how structure affects properties), which can then help develop formulation chemistry.
One growing area of research is the formulation of nanofluids. Gangopadhyay led a small study that showed adding carbon nanoparticles to ultralow viscosity oil improved the thermal conductivity by 15%-20%. “If we can get 20%-25% from the base oil and maybe another 20%-25% from nanoparticles, then we might hit our target of 50%.”
Test developments
The current standard test method for corrosiveness to copper is the copper strip test (ASTM D130). But because it is simply an immersion test, it is likely not the most relevant for HEV/EV systems. A better measure of copper corrosion for electric motors could be one in which an electric current passes through the copper wire.
Oil aeration is an important factor to examine when developing lubricants because it can significantly impact performance. Although aeration is already a consideration in ATF, electric motors typically run at much higher speeds than automatic transmissions—around 15,000 rpm—and might go as high as 30,000 rpm in the future. Therefore, high-speed aeration tests need to be explored if these high speeds significantly impact durability and other performance features.
Tests that measure material compatibility also should be an important focus because there are a number of both metal and non-metal materials used in the construction of electric motors. For example, copper coils are often coated with a modified polyester layer followed by polyamide imide coating. Any fluid also should be compatible with the polyester fibers that secure the copper coils. Epoxy is another common material of electric motors—used for varnishing, layering and coating—that also might come into contact with fluid.
Current industry activities
In 2019, the Society of Automotive Engineering (SAE) formed an electric drive fluid task force, which has been very active since its inception. To date, they have developed three sub-task forces focusing on material compatibility, aeration and thermal conductivity and electrical resistivity. In 2020, the Coordinating Research Council initiated a project titled “Thermal and Electrical Properties of Lubricants for HEV/EV Applications.” Their objective is “to develop a database of thermal and electrical properties of base oils from Group I to Group V for selection of appropriate base oil chemistry to meet the performance requirements of next generation driveline fluid for future hybrid and pure electric vehicles.” The purpose of the project is to generate lubricant data that could be publicly available instead of remaining within private companies. For more information about these activities, contact SAE or Gangopadhyay.
REFERENCES
1.
Click here.
2.
Click here.
Berly McCoy is a freelance science writer and producer based in Northwest Montana. You can reach her at kimberly.mccoy@westernalum.org.