Maintenance nomenclature
Evan Zabawski | TLT From the Editor December 2020
Lost in a literal interpretation.
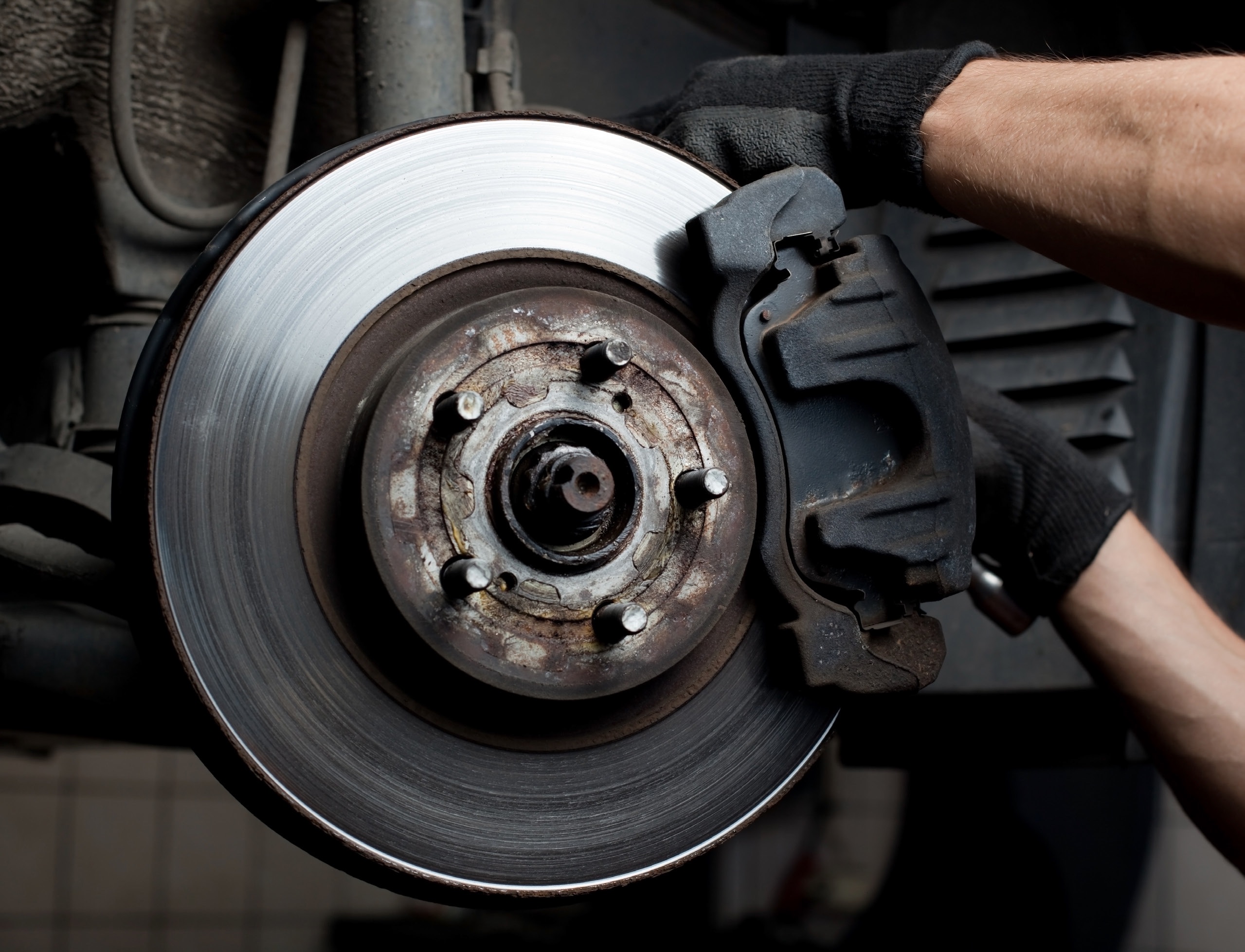
There are four primary maintenance strategies: reactive, preventive, predictive and proactive.
It is safe to say not everyone agrees with the naming convention of maintenance strategies, so let me share how I have come to understand them and see if I can clear up the confusion. First and foremost, we need to agree that there are four primary strategies: reactive, preventive, predictive and proactive. (Already I can hear someone shout, “What about reliability-centered maintenance [RCM]?” To them, I ask for a little patience.)
Assuming that these are the correct terms, let us avoid the trap I find many people falling into by applying a literal definition. For example, which of these terms applies to changing a set of brake pads on a vehicle after an inspection reveals they have <25% remaining? Is it reactive because we are reacting to this information? Is it preventive because we are preventing a brake failure? Is it predictive because we are predicting the pads will fail soon? Or is it proactive because we are changing the pads before they fail?
Herein lies the confusion—the answer becomes clearer if the term is applied to the failure and not the maintenance task, nor the person performing the maintenance.
Reactive maintenance is commonly referred to as “run to failure” insomuch as that no maintenance is performed until the failure occurs. Sometimes this is called corrective maintenance.
Preventive maintenance (PM) is known as scheduled or interval-based maintenance, implying maintenance is performed whether or not it is needed, based on some time or usage interval that is before the common or known failures are likely to occur.
Predictive maintenance (PdM) also is called condition-based maintenance (CBM), which involves condition monitoring, i.e., oil analysis, vibration, thermography, ultrasonics…to take measurements to identify a trend or threshold, indicating a failure is imminent enough to warrant a maintenance task.
Proactive maintenance (PaM) also is called failure avoidance and involves some form of root cause analysis (RCA) or failure modes and effects analysis (FMEA) to identify the root cause of a failure so that it may be eliminated from causing a repeat of the same failure.
I seldom see any disagreement about reactive maintenance being the oldest and simplest strategy, and most authoritative literature seems to indicate it was the only strategy until around World War II. At this time, industry went through a sharp increase in demand for manufacturing while suffering a significant decrease in manpower, which led to a focus on reducing downtime by introducing preventive maintenance.
Where the waters begin to muddy is when people try to separate predictive maintenance as trend-based and condition-based maintenance as, well, condition-based. The suggestion is that predictive maintenance occurs well before the failure, and condition-based maintenance occurs immediately before the failure, but they are the same, and to understand it, let us return to the brake pad example.
By performing a measurement, in this case, pad thickness, the answer to the original question becomes predictive maintenance. We did not allow the pads to fail first, so it is not reactive maintenance, nor did we arbitrarily change the pads based on an interval like mileage, so it is not preventive maintenance. While some argue the condition of <25% means it is condition-based, it does not imply the pads were about to fail. What <25% tells us is that, based on experience, the remaining life of the pad is sufficiently short to warrant replacement—a prediction.
Another point of contention is that some claim proactive maintenance and RCM to be one and the same. When John Moubray wrote Reliability-centered Maintenance, he explained that “the RCM process entails asking seven questions about selected assets” and that the third and fourth questions are answered “by performing a failure modes and effects analysis (FMEA) for each functional failure.” FMEA, or proactive maintenance, is merely a part of RCM.
What are the other parts? NASA’s RCM Guide lists reactive, preventive, predictive and proactive maintenance, which is in line with Moubray’s formal and fuller definition of RCM as “a process used to determine what must be done to ensure that any physical asset continues to do whatever its users want it to do in its present operating context.” RCM is when we apply any of the four strategies individually on a group of assets rather than one strategy for them all.
A typical passenger vehicle operates under RCM: We run the headlight bulbs to fail (reactive), we change the oil predominantly on mileage (preventive), we change brake pads on wear (predictive), and we have alignments done and properly inflate, balance and rotate tires to maximize tire life (proactive).
Simply put, there are four primary strategies, all under RCM, and suggesting there are more just seems like a nuanced interpretation with a commercial bias, or as the Dread Pirate Roberts would say, “Anyone who says differently is selling something.”
Evan Zabawski, CLS, is the senior technical advisor for TestOil in Calgary, Alberta, Canada. You can reach him at ezabawski@testoil.com.