Due diligence
Paul Hetherington | TLT President's Report September 2020
As lubrication specialists, the decisions we make can prevent—or lead to—serious consequences.
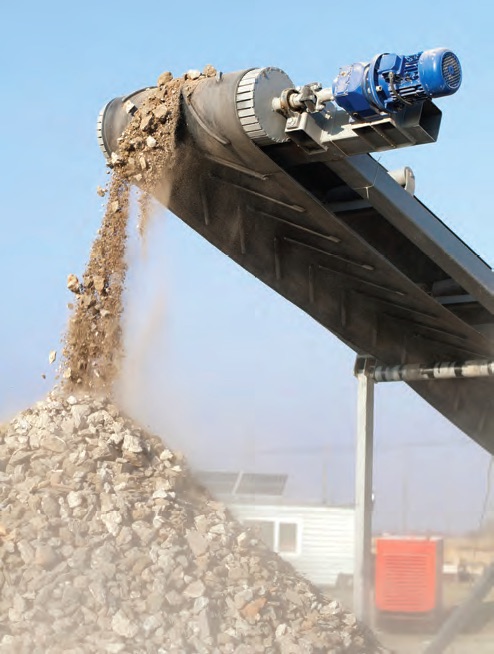
Due diligence is all about reducing risk with actions that you could defend and justify.
I would be hard-pressed to find two more important words that have guided me throughout my career than the term
due diligence. There certainly have been many times in my role as a lubrication specialist, in fact almost daily, where I made decisions that could lead to significantly negative consequences if I made a mistake. The somewhat perceived simple task of selecting the right grease or oil for a specific application could lead to the failure of that single component or shutdown of an entire operation.
OH&S Canada and the Cambridge dictionary defines due diligence as:
•
OH&S Canada: Due diligence is the level of judgement, care, prudence, determination and activity that a person would reasonably be expected to do under particular circumstances.
•
Cambridge dictionary: An action that is considered reasonable for people to be expected to take in order to keep themselves or others and their property safe.
Very simply, before making a decision we need to first determine all the facts and assess all the possibilities and consequences before selecting the best option.
One day many years ago, I was called by one of our area plant engineers with a query about the lubricant—in this case a grease—that we were using in one of our conveyer systems. The engineer noticed the OEM indicated the grease must not contain EP additives. The component was an item called a backstop—its primary purpose was to prevent an inclined conveyor from accidentally running backward with a heavy load of material on the conveyor belt (rock or sand, etc.) when it was shut down. Sometimes gravity is not our friend.
As you can well imagine, this could be a serious safety concern if the conveyor ran backward and dumped its contents onto an unsuspecting employee. Because of this many local governments’ safety codes or standards, including the Province of Alberta where I was working at the time, have a strict law indicating that an inclined conveyor must have a “functioning” backstop device.
So why did the OEM indicate no EP additives? The backstop is a clutch-type mechanism that relies on friction to engage and prevent the conveyor from running backward. Since the primary function of EP additives is to reduce friction between matting surfaces, generally most backstop OEMs recommend using a lubricant without these additives. So, based on the information from the plant engineer, it would now appear that we had been using an incorrect grease and, more important, left the inclined conveyor in an unsafe situation if the backstop became engaged but didn’t hold. So now what?
The first priority was to flag off the area around or near the bottom of the inclined conveyor. Although the overall risk was deemed as fairly low, the actual consequences could literally be deadly; therefore, the entire situation required appropriate due diligence.
The second problem, of course, was how to change the grease to a suitable non-EP type and be confident that the integrity of the backstop is still not compromised. The EP additive in the original grease was a common S-P (sulfur-phosphorus) type, which by function reacts with the metal surface at high-friction temperatures to produce a tenacious sacrificial low-friction layer. So the concern was even if we flushed out the bearings and removed all remnants of the EP grease, how would we know if the backstop would still properly engage and that any lingering EP film would be eliminated?
Unfortunately, this event occurred about 25 years ago, and I don’t have all the specific data, but basically I solicited the help of our product supplier’s R&D to see if we could come up with a test protocol. After a fairly extensive testing regime utilizing a fourball EP apparatus and scanning electron microscope, we were able to satisfy ourselves that, under the normal operating conditions of the backstop, any residual EP film would be quickly eliminated and have no effect on the operation of the backstop. Eventually all of the backstops were thoroughly flushed of the old grease and replenished with the proper non-EP product. Finally, the warning flags were removed from the area around the conveyor. Due diligence is all about reducing risk with actions that you could defend and justify.
One final word on due diligence—my experience, as reiterated in this article, cannot be used as a basis for making a similar decision on a similar event today. Why? Very simply, that would not be an act of due diligence on your part.
Paul Hetherington is manager technical services for Petro-Canada Lubricants in Peachland, British Columbia, Canada. You can reach him at paul.hetherington@hollyfrontier.com.