More options than ever for condition monitoring
Mary Beckman, Contributing Editor | TLT Feature April 2020
But dynamics are shifting for those who require oil analysis service—and those who provide it.
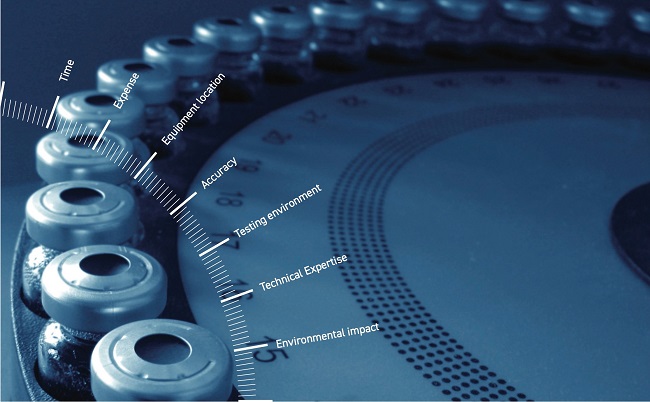
KEY CONCEPTS
- While many believe full-service oil analysis labs are in decline, they’re actually increasing their volumes worldwide.
- Sensors and oil analyzers give end-users more choices than ever and make it easier to bring the service in-house.
- While end-users see the value of oil analysis, price is typically the main factor when choosing a program.
Oil and other lubricants are the lifeblood of vehicles, industrial machinery, agricultural equipment and anything else with gears, bearings, and other mechanical bits. And like human blood testing, testing a bit of it can reveal whether its host is healthy and in good shape or has some underlying concern that might cause illness.
If you’re a person, it’s called blood testing. But the oil analysis industry calls it by a variety of names: in-service lubricant testing, in-service fluid analysis, oil condition monitoring, predictive maintenance or predictive fluid analysis.
With people, doctors interpret results and recommend treatment, if necessary. But what if doctors just sent people home with a slip of paper and a set of values? As more in-house testing becomes available, the industry is finding a way to balance immediate needs for doctors in the house with the comprehensive analysis that commercial labs can offer.
Regular testing began decades ago to protect the large investment that industrial machinery and equipment represents. Then OEMs picked up on the idea—if an OEM was going to sell a customer an expensive piece of equipment and guarantee it with a warranty, it needed a way to monitor the health of that machinery. Even a large bulldozer can cost several hundred thousand dollars, so they needed to protect their investment.
“They wanted to hopefully be able to detect a problem before it became catastrophic,” said Patrick Maggi, president and CEO at Cannon Instrument Co. in State College, Pa.1 “The OEMs recognized that importance, and they’ve been doing it for at least 20 years now.”
But with the advent of in-line sensors and smaller, more compact oil analyzers, are the full-service oil analysis laboratories going the way of the passenger pigeon? Over time, equipment available for oil analysis has changed from wet chemistry to large spectrometers to small desktop and even handheld instruments.
Some industries are opting for small onsite labs that do not require highly trained technicians to operate. Some larger laboratories are opting for highly automated methods that can perform numerous tests and take fewer technicians to staff. Is this the way of the future? “A rule of thumb in the industrial sector has been that traditional oil analysis via commercial laboratories only addressed 10% of the equipment that would benefit from oil condition monitoring,” says STLE-member Dan Walsh, director of product management/technical sales at Ametek,2 a provider of onsite oil analysis solutions in Chelmsford, Mass. “Onsite testing addressed that need.”
Full service means full service
To put the pigeon question to rest, the answer seems to be no, according to Walsh.
“We see full-service laboratories for oil analysis increasing their sample volume across the world, and newer approaches, such as onsite labs or sensors, are actually helping that trend. Overall, the demand is increasing as a result of awareness of the benefits of oil analysis as part of an integrated condition monitoring program,” says Walsh.
Even though instrumentation is getting smaller, that doesn’t appear to be taking away the value of commercial labs, according to Robert Robie, president of Eurofins ANA Laboratories, LLC3 in Runnemede, N.J.
“What the smaller footprint allows is instrumentation to be a little bit cheaper, more space affordable in a garage or service area, or even more compact like a lab-in-a-box in their facility,” Robie says. “We just don’t see an overwhelming amount of competition from that.”
Initially, tests for used lubricants were based on their fresh oil test standards. But then, with an increase in used oil analysis for predictive maintenance, ASTM International established a subcommittee to specifically examine standards for in-service lubricant testing.
“The increase in testing is not just bulldozers, cars and taxis but things like gearboxes in a machinery intensive industrial complex that could be making anything from aluminum foil to baby diapers,” says Maggi.
Situated under Committee D02 on Petroleum Products, Liquid Fuels, and Lubricants, the Subcommittee D02.96 addresses the fact that the composition of oils and fluids change through use, so the measurement or sampling technique for how you handle that sample also changes. The subcommittee has been developing separate test methods where necessary for oils once they’ve been contaminated or are in-service.
It’s not just the oils that need new testing standards. They are also addressing standards for new instrumentation specifically designed to measure in-service lubricants.
In the labs
Using a full-service commercial laboratory requires owners take samples of fluids from various compartments on the equipment and send them into the lab. The laboratories put the samples through a battery of tests ranging from viscosity measurements to the presence of contaminants. They might often include an interpretation when they provide the results back to the owners. Commercial labs consider many different aspects when deciding whether to offer specific tests.
“All labs consider the test method they are looking to offer to their clients—such as whether it is an approved ASTM test method or an emerging industry demand. They consider its performance in terms of reliability, performance, consumables, cost of ownership. Once those features are defined, lab managers consider the volume demand—is this an occasional or frequent demand? If it is a heavily requested test, then automation of the test via autosamplers, or the ability to work with some automation, becomes an important feature,” says Walsh.
OEMs have come up with another kind of lab midway between commercial labs and in-house ones: running their own testing facilities. For example, some Caterpillar dealerships have testing facilities they use to handle oil condition monitoring for their customers.
Maggi says that provides an added service for their customers. “The OEM knows the most about their particular piece of equipment. And if I was an end-user, I’d want to hear what they have to say about what they’re seeing in the oil. The further you get away from that OEM in terms of the knowledge of the system, the less reliable or informative the information from that analysis is going to be.”
In one of Caterpillar’s testing labs, for example, if they detect some metal in one of the samples, they can tell from the metallurgy of that particle which part it came from.
Smaller footprints, more electronics
Robie says the bigger change in the oil testing industry is not necessarily moving testing in-house but the shrinking of the instrumentation and its footprint.
“I think commercial laboratories are going to be around for a long time,” he says. The positive side of shrinking equipment for companies interested in in-house testing include having bench top accessibility, reduced sample volumes and electronics and computerization that handle what just 20 years ago was manual.
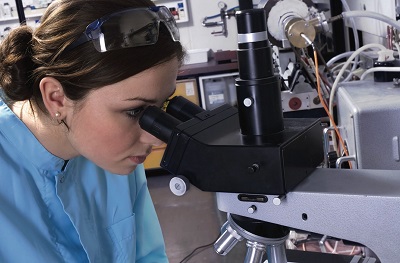
Commercial laboratories can be more accurate and have trained lab technicians.
But the down side comes in servicing the equipment. The smaller workspace and the complicated electronics make in-house maintenance more complicated.
“I liken it to a mechanic working on cars where it was a lot easier in the ’70s and ’80s. But when the 1990s and 2000s came along, you really needed to have some experience with computers because everything was a computer diagnostic on your car,” he says.
Even large laboratories, which are continuing to invest heavily in process automation, will consider compact or field portable equipment when looking for an occasional test requirement, or if they want to offer field support to their customers, says Walsh.
But in-house can be drafty and smaller can sometimes be too small. A problem with shrinking instruments and in-house testing is ensuring accuracy. An uncontrolled environment or an instrument that is so small it is sensitive to temperature could affect the accuracy of the test. Measurements such as viscosity for petroleum-based fluids are very sensitive to temperature change.
“You can be off by half a degree, and that would correlate to being off in viscosity by as much as 3%. That might be enough to get a false negative or false positive,” says Maggi.
Expertise is half the battle
While OEMs of instruments suitable for setting up in-house labs provide education about their equipment,4 one of the biggest advantages of a full-service laboratory is the knowledge support that accompany such labs.
“A point I think worth making is whether the measurements are done in the field or in a proper lab, the critical piece is the oil analysis of the results from that testing,” says Maggi. “A typical maintenance mechanic is not a trained lab technician, doesn’t understand good lab practice and might not fully appreciate that the dirt on his finger that just now got into the oil sample could definitely impact the viscosity and give you a false negative.”
Even with good technique, different tests can come out with different results, even if they are measuring the same physical property. For example, cold temperature tests for snow machine oil have traditionally been performed at certain temperatures. Shrinking the instruments means using pressure instead.
“Going from refrigerator to pressure, your numbers might be a little different but still the same acceptable level for the product. If you’re guaranteeing your customers that they’re not going to be waking up to a frozen snowmobile in the middle of winter in Minnesota, you need to be sure their product isn’t going to freeze,” Robie says.
For in-house testing, Robie and Maggi both recommend having certain staff designated and trained to do the sampling and testing to take away the untrained technician factor. A final advantage to a commercial laboratory is documentation and tracking. Even if a municipality wants to perform a quick test when fuel is delivered for their fleet, sending regular samples off means they are documenting that delivery, should anything happen in the future.
Time and place
Whether an owner should perform oil analysis in-house, send out samples or a little of both depends on how quickly the information is needed and even where the equipment to be sampled is located.
Any kind of company or service that relies on instantaneous results will require in-house testing, for example, the railroad.
“You have a locomotive in the shop for a limited amount of time. And if you’re waiting for four or five days for the oil analysis to come back, that locomotive might be well down the tracks by the time they get the results,” said Robie. “Or if your team only has a few days to adjust the belts and check the fluids on an elevator, you may want to hook up something that can test it right there. There are some instances where you have the urgency or desire for that.”
Another example is fleet owners such as municipal transportation groups. When needed, a quick test of their fuel can confirm whether they should pull a vehicle out of service before more damage happens.
Some tests would be better performed onsite, such as mining equipment miles underground. An owner might need to test a piece of equipment below to make sure it doesn’t die in a mine, and cause unexpected downtime costs.
“That’s definitely a nontraditional brick and mortar lab. We’ve seen an uptick in mine labs, especially with the increase in lithium mining for batteries,” said Maggi.
Sensors and algorithms
As valuable as constant monitoring is, sometimes it can seem like overkill.
“A dirty little secret in the industry is that 80% or so of samples come in and show no problem. There’s a high volume of samples that take a lot of time and effort and money to process, only to find perfectly good fluids,” says Maggi.
While that appears to actually be a clean little secret, simply cutting down the number of samples could be problematic. If, for example, an owner decides to start sampling four times a year instead of monthly, a problem could arise almost immediately after the last sample is taken.
“You might not know about the problem for three months and that might be more than enough time for the engine to fail,” says Maggi.
One option would be onboard sensors with diagnostics that monitor oil and fluids constantly, similar to how people with diabetes can now wear sensors that constantly monitor their blood sugar. The sensors send data and alerts wirelessly to a handheld monitor or even a cell phone.
The biggest advancement to get to such diagnostics, Robie says, are development of miniaturized sensors that can be put on units. These could be on a tractor trailer, or in a pump on an escalator. Onboard command centers could be monitoring fluids internally.
Similar sensors already exist on some passenger vehicles made by OEMs such as Mercedes Benz and BMW. Oil passes through the filter and then through the engine to provide lubrication and then ultimately through a small scanner of a sensor as it passes back through to the filter to be cleaned again. These sensors alert owners when to change their oil.
But most automobile oil monitors aren’t directly testing the oil. Instead, auto manufacturers developed computer algorithms that predicted oil life based on the car’s usage.5
By running engines in varying conditions and analyzing the oil on those engines, for example, OEMs have simulated all the different possible driving dynamics and correlated that to the effect on oil. A car engine’s computer knows how many times it was started, the position of the throttle while it is being driven, the fuel consumption and engine load, the temperature of the engine and more. The monitor puts all that information into algorithms that tell you how many miles or what percentage of useful life you have left on your oil.
“Those are predicated on time,” says Robie, “but ultimately they could be predicated on any kind of contamination or extreme situation that a sensor may pick up from the oil or fuel.”
A sensor that directly tests fluids is just what OEMs have been searching for. Although Mercedes Benz has developed a sensor that keeps an eye on oil directly, it only works with the right kind of oil. 6
“The heavy-duty and automotive vehicle industries have invested millions of dollars attempting to find a sensor that is robust enough to survive in that environment and has the accuracy to detect some meaningful change,” says Maggi.
Bottom line?
“In my opinion, what forces people to do something in-house versus sending them out to a commercial lab always boils down to price,” says Maggi. “Depending on the volume of what you’re doing, it might be cheaper to do it yourself. But that’s usually what the motivator is, the cost.”
To drive the costs down industry wide, instrumentation in commercial labs and in-house labs needs to decrease the cycle time for measurement analysis for faster turnaround time. More automation that reduces lab technician labor also helps.
Maggi says the industry also wants to reduce the environmental impact of testing. Many methods require the test instrumentation to be cleaned with solvent between samples, for example, so they are looking at ways to reduce solvent consumption and other consumables, such as being able to use the same test vial between multiple instruments.
“People get results in a timelier manner, and they pay less for them,” says Maggi.
After all, lubricants might be the lifeblood of industrial machinery and heavy equipment, but greasing the skids with cost and environmental savings will help keep the blood flowing freely.
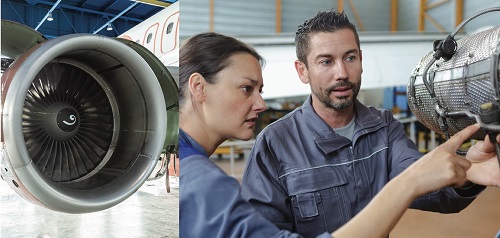
Marking metals
Although testing by OEMs can tell an owner what components certain wear metals in their oils are coming from, the aircraft industry goes a step further.
“They specifically dope the metal of certain components so that if they see the dopants in the oil, it’s like a marker,” Maggi said.
Airlines don’t own the engines on their jets. Companies such as Pratt & Whitney, Rolls Royce7 and GE8 “rent” the engines, and airlines pay for hours of flight time on each engine. By renting the engines for less than it costs to make them and charging for upkeep, OEMs can recoup their investments and at the same time ensure that their engines are safe to fly with.
“If the engine needs to be replaced or serviced, that service is provided by the OEM,” said Maggi. “So OEMs rely on that oil analysis to tell them if they have a problem before it becomes catastrophic.”
With different metallurgies in different parts of the engine, then even if the engine has two otherwise identical fuel pumps, the OEM can tell where issues are coming from without having to dismantle a whole plane.
Mary Beckman is a freelance science writer based in Richland, Wash. You can contact her at mbeckman@nasw.org.
REFERENCES
1. Click here.
2. Click here.
3. Click here.
4. Click here.
5. Click here.
6. Click here.
7. Click here (subscription required).
8. Click here.