Ionic liquid-based additives for automotive lubricants
Dr. Neil Canter, Contributing Editor | TLT Tech Beat March 2020
Phosphorus-based ionic liquids show potential as additives in rear axle lubricants and engine oils.
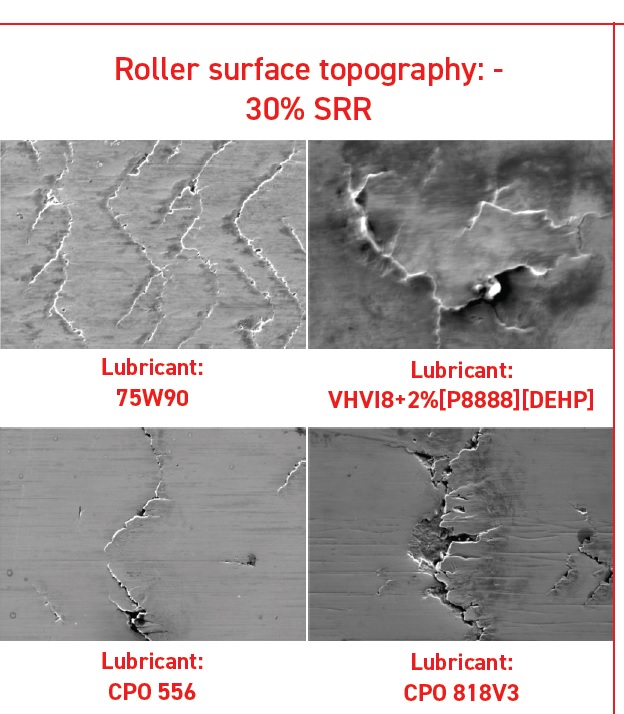
Figure 2. Extensive micropitting is shown in the top left image of the roller surface topography for carburized AISI 8620 steel used in testing of a 75W-90 commercial rear axle lubricant. The other three images of the same surface show much less surface cracking when rear axle lubricants formulated with ionic liquids were evaluated in the same test. Figure courtesy of Oak Ridge National Laboratory and Driven Racing Oil.
KEY CONCEPTS
•
Ionic liquids based on phosphonium cation derivatives and either phosphate or phosphinate anions were evaluated rear axle lubricants and low viscosity engine oils.
•
The presence of the ionic liquids in the axle lubricants led to significantly reduced surface cracking.
•
A synergism between the ionic liquid and a secondary ZDDP in fully formulated SAE 0W-12 engine oils led to reduced wear, a low boundary coefficient of friction and a 9.9% improvement in fuel economy versus a commercial SAE 5W-30 engine oil.
In the effort to improve the efficiency of high-performance lubricants used in racing, researchers are examining a wide range of additives that can be used to supplement the performance of automotive lubricants. One material that has been actively examined is graphene and its derivatives.
In a previous TLT article
1, graphene balls were crumpled through a sonication process and then dispersed in 4 cSt polyalphaolefin (PAO) at a treat rate of 0.1% by weight. Testing done with a pin-on-disk tribometer showed lower coefficient of friction and wear rates compared to graphite platelets. However, graphene is still a solid, so solubility can be problematic.
Another additive type that has been evaluated in lubricants is ionic liquids. STLE Member, Lake Speed, general manager of Driven Racing Oil in Olive Branch, Miss., says, “Ionic liquids are salts that exhibit melting points below 100 C. There are many possible ionic liquids that can be produced from anions and cations.”
Ionic liquids are polar species which can be difficult to incorporate in lubricants because of their potential incompatibility with nonpolar base oils. Speed worked with Dr. Jun Qu and other researchers from Oak Ridge National Laboratory who had developed phosphorus-based ionic liquids to determine how their use may improve the performance of pinion gears used in rear axles and in low viscosity (SAE 0W-12) engine oils. The ionic liquid developed by ORNL demonstrated excellent compatibility and solubility in traditional motor oil and gear oil base stocks.
Pinion gears
The ionic liquids under evaluation are based on phosphonium cation derivatives and either phosphate or phosphinate anions. An example is tetraoctylphosphonium bis (2-ethylhexyl) phosphate which is designated as [P8888] [DEHP].
Speed says, “We evaluated the performance of ionic liquids in rear axle lubricants used in pinion gears. The reason is that the highest load and smallest contact area in the rear axle are observed with pinion gears. This is an application where lubricants are subjected to really high pressure. As a result, lubricants must be formulated with extreme pressure additives to maintain performance under such severe operating conditions.”
From a lubricant standpoint, the problem is that conventional axle lubricants are formulated with sulfurized additives that can promote micropitting. Speed says, “Sulfurized additives can attack the grain structure in the pinion gear leading to micropitting and cracking.”
Further challenging the researchers is the move by the automotive industry to reduce the viscosity of rear axle lubricants from SAE 75W-140 to SAE 75W-90 which could lead to increased surface damage (due to rolling contact fatigue) and sliding wear. The benefit of this viscosity reduction is a 1.4% improvement in efficiency.
Speed and his colleagues investigated the performance of two of the phosphorus-based ionic liquids as additives in fully formulated axle lubricants. Traction coefficient and wear results showed that several low-viscosity axle lubricants formulated with the ionic liquids exhibited comparable friction and wear to commercial 75W-90 and 75W-110 gear oils.
The researchers used scanning electron microscopy to examine the micropitting seen on the metal surface after testing. Figure 2 shows the roller surface topography for carburized AISI 8620 steel used in evaluation testing. For this particular test, the gears were subjected to a slide to roll ratio of 30%. The image of the 75W-90 commercial oil shows extensive micropitting while the three other images for axle lubricants containing the ionic liquids exhibit significantly reduced surface cracking.
Low-viscosity engine oils
The researchers also evaluated the ionic liquid additives in fully formulated SAE 0W-12 engine oils. Due to the phosphorus-based nature of the ionic liquids, the researchers decided to evaluate them in combination with a secondary zinc dialkyldithiophosphate (ZDDP).
Speed says, “We found that a 1:1 ratio of the ionic liquid with the ZDDP led to superior results including a 50%-80% reduction in wear and a very low boundary coefficient of friction (0.03-0.04). Cam lobe wear was also reduced by 40%, and the engine oil displayed a 9.9% improvement in fuel economy versus a commercial SAE 5W-30 engine oil.”
The optimum treat rate for the ionic liquid and the ZDDP was found to be 400 ppm each. Speed says, “We looked at other ratios but did not see the same synergy.”
The researchers found that the surface concentration of phosphorus, sulfur and oxygen in engine oils with both the ionic liquid and ZDDP are 30 to 70 time higher than those in the bulk oil. This result may help to explain in part the synergism seen between the ionic liquid and ZDDP.
An interesting phenomenon noted by the researchers was that extended friction testing using the Plint Reciprocating Rig resulted in an increase in friction and higher wear due to the micropitting after 10 kilometers of sliding at elevated temperatures. This result occurred in all engine oils tested including commercial lubricants containing no ionic liquid. Speed says, “We believe that running at a temperature of 100 C with pure sliding produced a unique tribofilm leading to micropitting. ZDDP and the friction modifier appear to be the major contributors to the micropitting. Because engines operate in a dynamic environment of both sliding and rolling, we were not overly concerned by the findings. However, we did develop a formula that greatly reduced the micropitting.”
With the movement to lower viscosity-based lubricants in an effort to improve efficiency, this work shows the potential for using ionic liquids as additives to improve the performance of automotive lubricants and minimize concerns such as micropitting and wear.
Additional information can be found in presentations given at the 2019 STLE Annual Meeting
2 and at the 2019 SAE World Congress
3. Details on the composition of the ionic liquids can be found in US Patent 9,957,460 published in 2018.
4 Driven Racing Oil can also be contacted at
Tech@DrivenRacingOil.com.
REFERENCES
1.
Canter, N. (2016), “Evaluation of a new lubricant additive: Crumpled graphene balls,” Tribology & Lubrication Technology,
72 (4), pp 12 – 13
2.
Roy, S., Luo, H., Leonard, D., Qu, J., Voila, M. and Speed, L., “Effects of ionic liquids on micropitting behavior for rear axle lubrication,” Presented at the STLE Annual Meeting in Nashville, TN on May, 21, 2019
3. Qu, J, Kumara, C., Luo, H., Viola, M., Barnhill, W. and Speed, L., “Ionic Liquid Enhanced Low-Viscosity (SAE 0W-12) Engine Oils,” Presented at the SAE World Congress in Detroit, MI on April 9, 2019
4. Qu, J. and Luo, H. “Ionic Liquids Containing Symmetric Quaternary Phosphonium Cations and Phosphorus-Containing Anions, and Their Use as Lubricant Additives (2018),” US Patent 9,957,460 B2
Neil Canter heads his own consulting company, Chemical Solutions, in Willow Grove, Pa. Ideas for Tech Beat can be submitted to him at neilcanter@comcast.net.