Choosing the right open gear lubricant
Berly McCoy, Contributing Editor | TLT Lubrication Fundamentals November 2019
To protect the unprotected, focus on application method, viscosity and temperature.
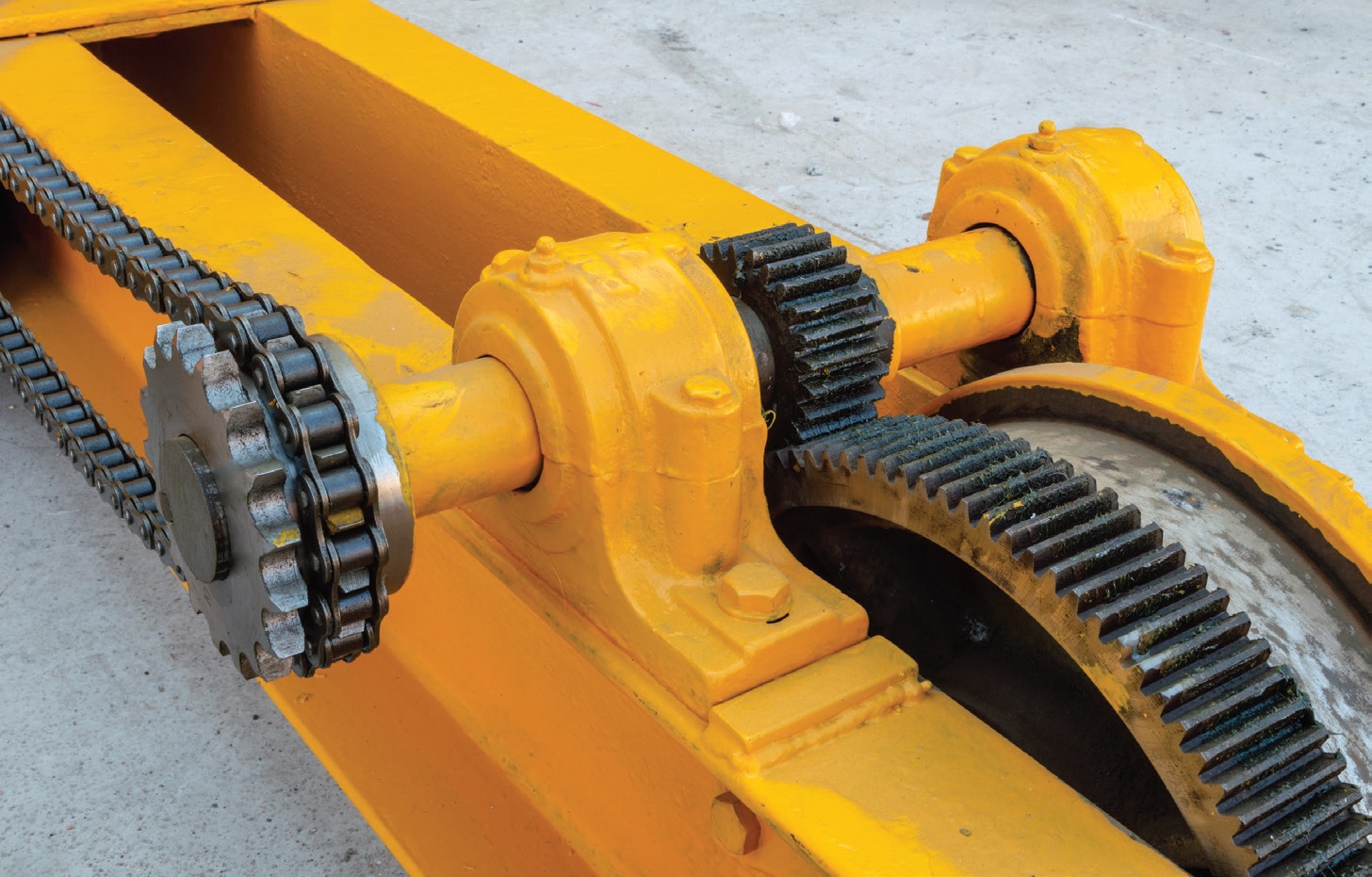
© Can Stock Photo / ipekmorel
Open gear systems are important components in a large range of industrial applications, including mining shovels, excavators, draglines, kilns and ball and grinding mills. These machines are used in mining, steel, cement, concrete and other metal processing industries. Although many of these gears are shrouded, and thus protected from the elements to some degree, it would be impractical to fully enclose them as seen in industrial (enclosed) gearboxes. The vast majority of open gears are large and slower moving compared to conventional gearboxes, and they tend to support much heavier loads. Because of these reasons, lubrication of open gears requires special considerations to ensure that hardware both runs efficiently and is protected.
Gear lubrication is an essential part of machine operations. The lubricant reduces friction between moving parts and also protects the gears from wear. Even the best gears can fail if they are not lubricated properly. This means choosing the right lubricant for the job but also understanding quantity and relubrication specifications. When it comes to lubricating open gears, operators need to take into consideration unique operating conditions.
Key issues
By their nature, open gears have some degree of exposure to their external environments. Therefore, unique considerations must be considered to both limit dirt, dust and debris from entering the gears—which can reduce efficiency—and to prevent lubrication fling-off, leaking and evaporation. Lubrication loss is not only inefficient (adding costs and requiring relubrication), it also can increase environmental pollution. Additionally, open gears must tolerate moisture from weather events and humidity.
Most open gear lubricants are high viscosity. This is largely so they are thick enough to prevent loss from fling-off, but high-viscosity lubricants also aid in the protection of large, heavy gears, which operate under extreme pressures focused on small areas. Because oil viscosity increases with pressure, starting with a high-viscosity lubricant helps protect gears under operating conditions. Due to these pressure concerns, open gear lubricants also can contain extreme pressure additives that are often solid, such as graphite and molybdenum disulfide.
Although viscosity is an important feature in open gear lubricants, it can dictate how the lubricant is applied. If a lubricant is too viscous, operators may experience a “channeling” effect when using a bath lubrication application method, says STLE-member Daniel Roberts of Lubrication Engineers in Fort Worth, Texas. “Channeling occurs when the lubricant is so heavy that the gear can ‘carve out’ the fluid faster than it can flow back to its original state,” Roberts says. “Intermittent spray methods or hand/brush-applied methods are most common for these applications.”
Other special considerations for open gear lubrication include formulating a drainable mixture so that the lubricant can be filtered to remove contaminants, and incorporating additives to confer anticorrosion, antirust, antifoam and antiwear properties, as well as seal and paint compatibility.
Industry standards
Because of the wide variety of open gear systems available, there is no one-size-fits-all lubricant for open gears. Instead a lubricant should be chosen based on the end-user’s goals.
In some cases, the OEM will specify a specific lubricant that should be used and whether it can be diluted or not. In other instances, the OEM provides a set of parameters or tests that a lubricant must meet or pass. If the OEM does not suggest a set of parameters, it may point to a particular reference document such as the American National Standard for Industrial Gear Lubrication published by the American Gear Manufacturers Association (current version is ANSI/AGMA 9005-F16) or the document published by Rexnord Industries: “Falk™ Single Helical, Herringbone, or Spur Gears” (document number 638-058). Two other sources for lubricant recommendations are Bucyrus International (part of Caterpillar) SD4713 and P&H (Komatsu Mining) 464 Open Gear Lubricant Specification.
In general, the two main characteristics that decide which lubricant will be used for a particular open gear system outside of the base oil needed to meet quality concerns are the lubrication method and the operating temperature. This is largely related to viscosity. For example, if an open gear system needs continuous lubrication in the form of bath lubrication, the lubricant cannot be too viscous to be applied at ambient temperatures (due to the channeling effect). Other important factors that may dictate lubricant choice are the quantity and application frequency required to protect gears. Roberts says these parameters also are cited by industry guidelines and OEMs, which will depend on the diameter and width of the gear and the nature of the pinion drive.
Industry trends
Manufacturers of open gear lubricants have been moving toward producing more environmentally friendly products. “Traditionally, lubricants fortified with asphalt with or without solvents were used,” says STLE-member Anoop Kumar of Chevron Lubricants in Richmond, Va. “However due to environmental and performance concerns associated with these type of lubricants, semi-fluid type of greases containing suitable tackifiers and performance additives are being preferred.”
The main reason for a push toward greener products by manufacturers is due to government policies that both limit the types of chemicals in lubricants and dictate how lubricants with certain additives must be disposed, which can increase costs. In the 1960s and 1970s, the U.S. passed regulations through the Resource Conservation and Recovery Act that limited the amount of halogen that could be incorporated in lubricants and other products. For this reason, chlorinated compounds generally aren’t incorporated in lubricants. Today the EPA’s National Pollutant Discharge Elimination System controls what can go into lubricants used in the marine and shipbuilding industries through their Vessel General Permit. STLE-member Lawrence Ludwig of Schaeffer Mfg. in St. Louis, says this is resulting in manufacturers producing more grease-like open gear lubricants.
In addition to developing environmentally friendly products, another trend in open gear lubrication is a shift in the application method. Says Kumar: “Historically dip and brush lubrication practices were more common. However, there is an increasing trend to use spray-type systems.”
Other experts that contributed to this article:
John Sander of Lubrication Engineers
From TLT Archives
Want more on open gear lubricants? Check out these TLT Archives articles at www.stle.org.
1. Gresham, R. (2012), “The Mysterious World of Lubricant Additives,” TLT, 68 (9). Available here.
2. Sniderman, D. (2017), “The Chemistry and Function of Lubricant Additives,” TLT, 73 (11). Available here.
Berly McCoy is a freelance writer based in Coram, Mont. You can reach her at https://kimberly-mccoy.com.