King Industries
High Temperature Performance with NA-LUBE® KR Alkylated Naphthalenes
By Ross Dworet, MBA, Technical Marketing Engineer, King Industries, Inc. | TLT CMF Plus November 2019
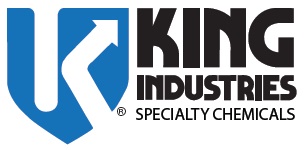
Industrial fluid markets continue to push towards extended life fluids capable of improving both equipment life and production uptime to provide optimal operational efficiency. As such, fluids experience increased flow, higher temperatures, thinner films, reduced volumes, and sealed-for-life systems. More refined base stocks and synthetics have contributed to significant strides in satisfying industrial demands. There are limitations in these fluids’ performance in areas such as additive and elastomer compatibility as well as thermal properties. To meet growing demands in industrial lubricants, automotive oils, e-fluids, and greases, optimized combinations of highly refined petroleum oils and synthetic base stocks have become the mainstay in driving base stock performance.
Properties
NA-LUBE® KR alkylated naphthalenes, classified as Group V base fluids by the API, are typically utilized in lubricant formulations as co-base stocks to replace a portion of Group II, Group III, and/or Group IV oils. Incorporation of NA-LUBE KR enhances thermo-oxidative stability and functional additive response while simultaneously extending fluid operating life especially in dynamic fluid systems. The range of NA-LUBE KR Series products provides several formulating options through a combination of viscosities, aniline points, and volatilities with HX-1 grade alkylated naphthalenes also available.
The structure of alkylated naphthalenes (
Figure 1) consists of alkyl chains attached to a core of two fused six member rings with a highly stable electron rich conjugated π system.
Figure 1. Alkylated Naphthalene Structure
NA-LUBE KR alkylated naphthalenes are supplied as mono alkylated and poly alkylated products and feature properties as shown in
Table 1 including mid-range aniline points, good VI, outstanding hydrolytic stability, and exceptional high performance thermo-oxidative stability.
Table 1. NA-LUBE KR Alkylated Naphthalene Typical Properties
The aniline point range is at a midpoint between traditionally polar esters and non-polar Group II, III, and IV fluids. This improves additive response through solvency, or compatibility, in a formulated lubricant without competing for the surface with functional additives. In dynamic systems, NA-LUBE KR has both bench and field proven varnish control through prevention and solubilizing mechanisms to contribute to long term system cleanliness between fluid change intervals.
This study features the key benefits of NA-LUBE KR:
•
Reduction in system volatility
•
Improvement of thermal and thermo-oxidative stability
•
Prevention of varnish formation.
High Temperature Performance
Key features of NA-LUBE KR products are thermal and thermo-oxidative stability. The balanced composition imparts desirable high-performance properties to lubricant formulations for systems requiring durability under high temperatures.
Previous results of a pan volatility test, where mass loss was measured over a fixed period, evaluated the fluid volatility and mass deposits. The fluid film in the pan was tested under static conditions. At 240°C for 42 hours, a selected polyol ester designed for oven applications exhibited 83% evaporation loss and resulted in a brittle solid varnish remaining in the pan. By modifying the polyol ester with 20% NA-LUBE KR-019, the evaporation loss of the fluid was reduced by 35% and the residue remained fluid (
Figure 2).
Figure 2. Evaporation Loss Results 42 Hours at 240°C
High Temperature Study
In this study, the goal was to demonstrate improvements in thermo-oxidative performance under static and dynamic conditions of two model formulations modified with NA-LUBE KR alkylated naphthalenes.
The two model formulations were designed with different additive treat rates corresponding to the operating conditions for the intended applications.
1.
Bakery Oven Model Formulation (ISO VG 220): H1 Formulation based on PAO with a total HX-1 additive treat of 2.5% wt.
2.
Industrial Model Formulation (ISO VG 220): Ashless High Temperature Chain Lubricant based on ester with a total additive treat of 6.75% wt.
Equipment for food grade applications often requires a less robust additive formulation to accommodate varying loads, speeds, and environmental conditions, such as humidity or foreign contaminants. In both formulations, the base fluid component, PAO or ester was replaced with 0%, 10%, 20%, and 30% NA-LUBE KR-029FG or NA-LUBE KR-019, respectively. Both NA-LUBE KR-019 and the HX-1 grade analogue, NA-LUBE KR-029FG, demonstrate excellent thermal performance.
Thermo-oxidative testing was done using PDSC (ASTM D6186) and a newly developed in-house panel coker test rig to demonstrate the benefits of the NA-LUBE KR modification in each formulation.
PDSC
Both the Bakery Oven and Industrial Model formulations displayed the advantages of the incorporation of the NA-LUBE KR-029FG and NA-LUBE KR-019 in PDSC performance. In addition to extended onset times, the heat flow of the oxidizing sample was significantly reduced with each increasing incorporation of NA-LUBE KR (
see Figures 3 and 4). To measure the onset point of the fully formulated Industrial Model within a reasonable time, the PDSC test temperature was increased from 210°C to 240°C. Both formulations were run under 500 psi O
2 with a 100 mL/min O
2 purge.
Figure 3. PDSC (ASTM D6186) Bakery Model Formulation
Figure 4. PDSC (ASTM D6186) Industrial Model Formulation
The PDSC results show that NA-LUBE KR-029FG and NA-LUBE KR-019 base fluid substitution can extend and improve thermo-oxidative stability under demanding conditions.
In-house Panel Coker Method
To provide a suitable thin film dynamic test system, an in-house panel coker was designed to better quantify fluid performance at a high temperature. The in-house panel coker method determines deposit evaluation after a set volume of fluid has passed over the surface of a stainless-steel panel at a predetermined temperature. The delivery mechanism of the test rig consists of a thin walled 1 meter long stainless-steel tube that allows rapid heat transfer to the fluid inside the tube as it is transported to the surface of the panel. After 18 hours, the panel is removed for evaluation of the deposit mass and flow pattern. After the panel has been evaluated, the panel is placed in a heptane vapor degreaser for an hour and evaluated again.
For the purposes of this study, fixed conditions were set regarding the configuration of the test rig, flow rate, fluid volume delivered to the panel surface, and duration. Test panels were placed at 35° with a flow rate of 0.8 mL/hr delivered to the surface of the panel for 18 hours maintained through a built-in pump controller. The evaluation temperatures for the model formulations were selected to be appropriate for the intended application, shown in
Table 2.
Table 2. Chain Lubricant Market Application by Temperature
The coke deposits remaining on the panel were classified into two categories, hard and soft, and quantified into total and cured deposits. Soft deposits are solid with a gummy to lacquer appearance with no flowability. These deposits are readily soluble in solvent and may or may not be soluble in oil. Hard deposits are dry in appearance with no flowability and may or may not be removed mechanically.
Total Deposit, as shown in
Equation 1, is the combined soft and hard deposits remaining on the panel. The reported value is the mass difference of the initial panel (m
p, i) and coked panel (m
p, f) reported as a percentage of the mass of fluid delivered (m
FT).
Equation 1. Total Deposit Quantifying Formula
The Cured Deposit, as represented in
Equation 2, is the remaining deposit on the panel after heptane vapor degreasing. The reported value is the mass difference of the initial panel (m
p, i) and degreased panel (m
d, f) relative to the calculated mass of total deposits (m
TD).
Equation 2. Cured Deposit Quantifying Formula
As the fluid flows down the surface of the panel, a wetting pattern emerges based on the characteristics of the fluid.
Wetting is an important feature to a fluid’s ability to create a tribological film. A fluid with good wetting has been observed to create a wide inverted parabola. High performance fluids with excellent thermo-oxidative stability and good wetting will typically result in an open pattern with faint or low deposits outlining the inverted parabola. At high temperatures, a lack of thermo-oxidative stability or wetting will cause the pattern to close at the bottom of the panel leading to coke build-up.
In-house Panel Coker Results
The Bakery Model Formulation was run at 220°C to evaluate the panel coker performance of the fluids in triplicate. The increasing base fluid substitution with NA-LUBE KR-029FG reduced the Total Deposit (
Figure 5). The Cured Deposits, based on the composition of hard deposits to the Total Deposit, were also reduced (
Figure 6).
Figure 5. Total Deposit (% wt.) Bakery Model Formulation
Figure 6. Cured Deposit (% wt.) Bakery Model Formulation
The coking pattern of the fluid (
Figure 7) displayed an increased opening at the bottom of the panel in addition to a lower 3-dimensional build of the solids along the periphery of the wetted flow route. The lower build of coke suggested both improved thermo-oxidative stability and solubilization of pre-formed and/or formed deposits.
Figure 7. Degreased panels from Bakery Model Formulation Panel Coker Tests
The Industrial Model Formulation was run at 270°C to evaluate the panel coker performance of the fluids in triplicate. The Industrial Model Formulation fluids were robustly formulated to provide the highest potential performance combined with an ester specifically designed for high temperature applications.
The increasing base fluid substitution with NA-LUBE KR-019 did not demonstrate a significant difference or reduction in the Total Deposit under the 270°C condition (
Figure 8), but all results were very low. However, the Cured Deposits results demonstrated a clear reduction in hard deposits (
Figure 9).
Figure 8. Total Deposit (% wt.) Industrial Model Formulation
Figure 9. Cured Deposit (% wt.) Industrial Model Formulation
The coking pattern of the fluid (
Figure 10) again displayed an increased opening at the bottom of the panel in addition to a lower 3-dimensional build of the solids along the periphery of the wetted flow route. The observed pattern and visual deposit flattened with the increased incorporation of the NA-LUBE KR-019. The Cured Deposit data provided support for the visual observation.
Figure 10. Degreased panels from Industrial Model Formulation Panel Coker Tests
Field Performance
Overall, the static PDSC and dynamic in-house panel coker results support the improved thermo-oxidative performance imparted by the NA-LUBE KR-019 and NA-LUBE KR-029FG. In the field, the NA-LUBE KR series performance has correlated to the observed laboratory performance. In a continuous hot press for plywood or MDF manufacturing, the in-service belt lubricant required frequent replacement intervals. The equipment operates continuously at temperatures between 240°C to 260°C and pressures near 5000 kPa moving pressed parts at speeds up to 2 meters per second. NA-LUBE KR-019 was formulated into a new belt lubricant formulation as a co-base stock and put into service. After six months, the fluid had darkened significantly. However, the friction liners used to drive the belt (
Figure 11) were observed to be free of deposits that had built up from the previous oil.
Figure 11. Continuous Hot Press Friction Liners after First Fluid Change Interval
The fluid change interval was completed again with NA-LUBE KR-019 incorporated fluid and this time the fluid did not darken and the friction liners remained deposit-free. The equipment operators observed a reduction in noise and vibration that had previously impacted equipment’s maintenance interval.
Summary
The data generated by static and dynamic laboratory testing supported by field performance demonstrated that NA-LUBE KR alkylated naphthalene formulated into a base fluid delivers a clear benefit in reducing varnish formation, limiting system deposits, and prolonging service life of a dynamically stressed fluid. With a diverse viscosity range, NA-LUBE KR products provide excellent flexibility in designing lubricants for a broad range of applications.