Lubrication challenges in the wind turbine industry
Dr. Nancy McGuire, Contributing Editor | TLT Webinars September 2019
The right lubricant can increase energy production while lowering capital costs.
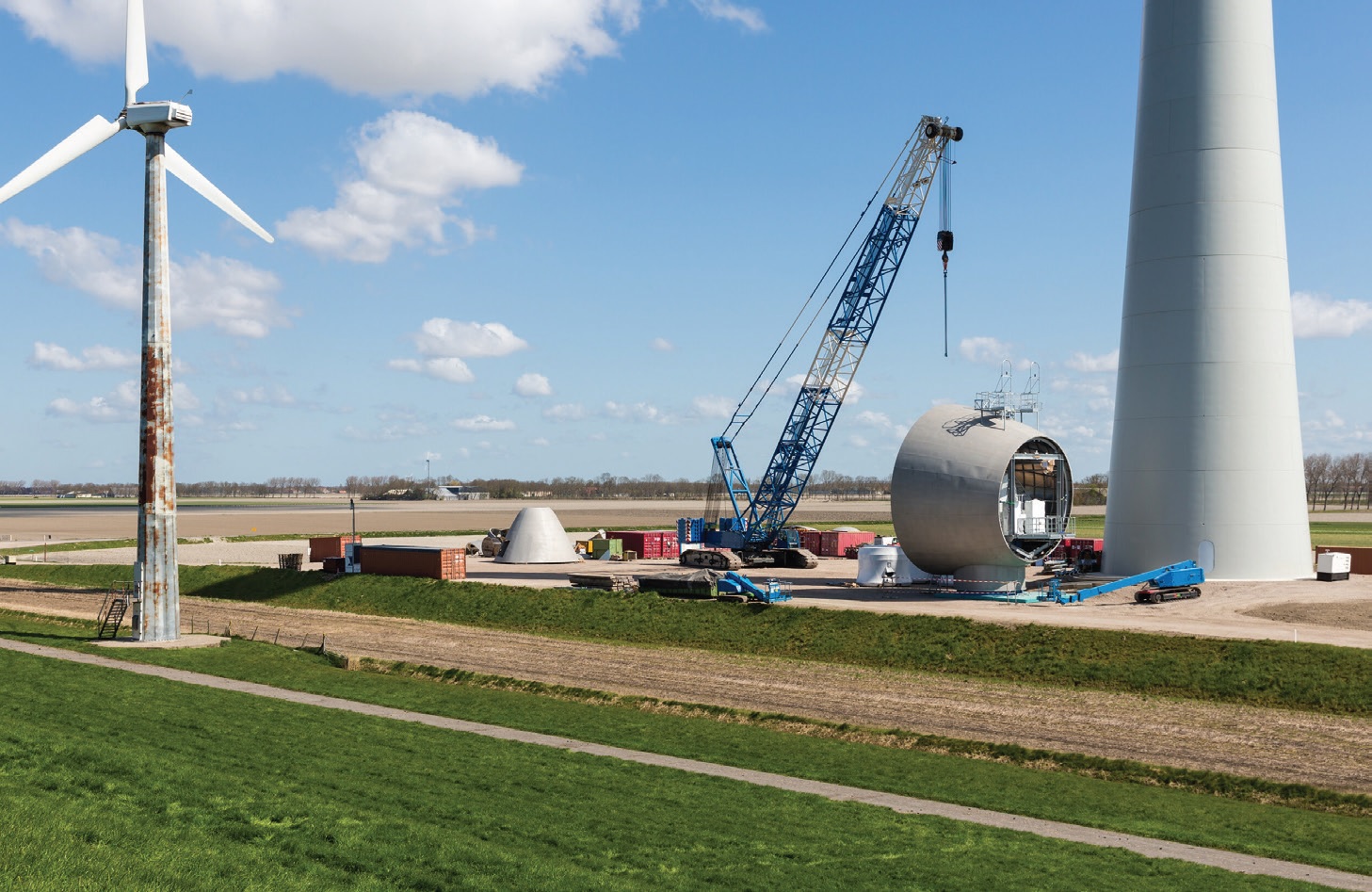
© Can Stock Photo / kruwt
KEY CONCEPTS
•
The trend in wind turbines is bigger everything—blades, towers, bearings and power generation.
•
To compete with natural gas and coal, wind energy capital costs must decrease while production increases.
•
Better designs and lubricants have led to fewer unexpected repairs and less down time for wind turbines.
MEET THE PRESENTER
This article is based on a Webinar presented by STLE Education on March 27, 2019.
Lubrication Challenges within the Wind Industry is available at
www.stle.org: $39 to STLE members, $59 for all others.
Dr. Kuldeep Kishore Mistry is a product development specialist for The Timken Co. where he has worked since 2013. His focus is on developing and troubleshooting lubrication solutions for the wind energy sector, as well as automotive, heavy industrial, rail and heavy truck applications. He completed his graduate studies, sponsored by ExxonMobil, at the University of Leeds in the UK. Mistry worked as a post-doctoral scientist in the energy systems division at Argonne National Laboratory, and his postdoctoral work on versatile hard carbon microspheres made from plastic waste received an R&D 100 Award in 2015. He has three patented inventions and several published articles in peer-reviewed journals, and he attends and gives presentations at various conferences. Mistry joined the STLE board of directors in 2019 and is actively engaged in the tribology, grease and lubrication research communities within STLE, NLGI and ISO. He has chaired the STLE Canton Section and engages in STEM activities for middle school students in northeastern Ohio.
This webinar follows up on a previous presentation,
Fundamentals of Wind Turbines, by Dr. Harpal Singh with Sentient Science. Mistry thanks the leadership of The Timken Co. for letting him present and publish this investigation. He also thanks his colleagues (Doug Lucas, Carl Hager, Jerry Richter and Jeremy Kimble) at The Timken Co. for their excellent support of his work.
You can reach Mistry at
kuldeep.mistry@timken.com.
Dr. Kuldeep Kishore Mistry
Around the world more than 200,000 wind turbines (almost 50,000 in the U.S.) turn slowly. Each of these turbines can generate more than 1 mw (megawatt) of power, enough to power at least 750 homes (
1). Because of the turbines’ remote locations and large size, even one repair job can cost $45,000 or more, so it’s no surprise that preventing premature equipment failure is a high priority for wind farm operators.
Aside from wear issues arising from their sheer size and weight, wind turbine parts can wear out because of the wind itself. Wind conditions can range from perfectly calm to gale force and back again in a matter of minutes. Thus, wind turbine bearings, shafts and other parts rely on lubricants that provide a protective film at a moment’s notice in all kinds of weather.
Components
The trend in the wind turbine industry is bigger, bigger, bigger. Blades, towers and bearings are all increasing in size to deliver more power. However, in order to compete with energy from natural gas and coal, the cost of wind energy has to decrease. This is done by reducing the cost of capital investment, producing energy more efficiently and reducing the cost of maintenance.
As a result of better technologies, improvements in standards and increased understanding, wind turbines have become increasingly reliable during the past 30 years. Better designs and better lubricants reduce maintenance costs by keeping turbines running smoothly with a minimum of wear, which reduces the frequency of unexpected repairs and downtime. New wind turbine gearbox designs make it possible to perform repairs uptower without the need for an expensive land-based crane to lower parts to the ground.
Wind turbine blades function as airfoils (
see Figure 1). When wind blows, the blades rotate and turn the main shaft at a speed of about 15 rpm. In some wind turbines, a gearbox between the main shaft and the generator increases the rotational speed from 15 rpm to about 1,800 rpm. Direct drive turbines do not use a gearbox, and the generator operates at the same rotational speed as the turbine blades. Direct electrical current produced by the generator is converted to alternating current, which provides power to a public utility grid.
Figure 1. Wind turbine parts and types of bearings. (Figure courtesy of The Timken Co.)
The pitch, yaw and generator bearings are typically ball bearings with a grease lubricant. Pitch bearings, which allow the blade angles to vary, and yaw bearings, which let the turbine rotate on the tower, experience oscillating motion, vibration, high loads, low temperatures and low speeds. Generator bearings deal with all of these factors, along with electrical currents and high temperatures. The grease lubricants for these bearings must provide low torque and high load capacity, temperature stability and mechanical stability. In addition, these greases must resist water and prevent false brinelling (dents in the bearing elements caused by vibration).
Lubrication challenges
Wind industry customers and OEMs drive expectations for wind turbine gearbox designs. Blades and towers are getting larger, but demand is evolving toward more compact gearboxes that can still carry high loads. Newer gearbox designs put more demands on a lubricant, and the components are at greater risk of micropitting and wear (
see Figure 2). Meanwhile, the need to cut maintenance costs drives a demand for extended oil drain intervals and better filtration. Environmental considerations also drive demand for better lubricants. For example, offshore wind farms require lubricants that resist water contamination and that function well over a wide range of temperatures.
Figure 2. Lubricants must have the right properties to meet the specific demands of wind turbines. (Figure courtesy of The Timken Co.)
No one lubricant offers top performance in all areas. Thus, lubricant formulators must optimize a combination of several factors:
•
High scuffing resistance at normal and elevated loads.
•
Excellent micropitting resistance for protection against premature fatigue damage.
•
Compatibility with paints and elastomers.
•
Compliance with requirements of rolling bearing manufacturers.
•
Good wear protection to prevent premature bearing damage.
•
Dynamic seal compatibility to protect against oil-induced leakage.
•
Excellent aging and oxidation resistance, enabling much longer service intervals.
•
Viscosity performance that provides sufficient lubricant film at high temperatures.
•
Pumpability for mainshaft bearings.
•
Wide operating temperature range.
Gearbox oils and turbine greases
One of Timken’s customers, an OEM, requested a comparison of key characteristics of 19 common commercial wind gearbox oils. We evaluated these oils with respect to their antiwear properties, micropitting and scuffing protection, viscosity index, stability against oxidation, corrosion and rust protection, water handling, filter life, antifoaming properties and how well they protected the equipment. We rated these properties on a scale of 0 to 10 and plotted them on a spiderweb diagram, with the poorest performance at the center (rating 0) and the best performance along the outside perimeter (rating 10). Although no oil excelled in all properties, two of them exhibited the best overall performance (
see Figure 3).
Figure 3. In this comparison of gearbox oil properties, oils H and P did best overall while oil N under performed. (Figure courtesy of The Timken Co.)
Recently we published the results of a study comparing various commercial wind turbine greases for lubricating main shaft bearings (
2). Main shaft bearings, a critical component in the driveline of a wind turbine, operate at slow speeds and high, variable loads and under a wide range of temperature, humidity and wind-speed conditions. Wind turbine greases are critical to extending bearing life. They seal out contaminants, prevent wear, reduce friction and protect against rust and corrosion (
see Figure 4).
Figure 4. Wind turbine application challenges drive the selection of bearing greases. (Figure courtesy of The Timken Co.)
When selecting a grease, it is important to consider water resistance, the operating temperature range, bearing speeds and dynamic conditions that include static operation, oscillation and vibration and heavy or shock loading. Oil bleed properties of the grease (a function of the thickener) promote oil migration and enable the bearings to operate at a lower torque and lower temperature. Adequate film thicknesses promote bearing life and influence component reliability. Selecting the right grease for the application minimizes unexpected bearing damage, minimizes lubricant starvation, promotes bearing life and extends the re-lube intervals.
We looked at 14 different greases, NLGI grades 1 to 2, each with a different combination of strengths and limitations. These greases are all commercially available and commonly used for wind turbine main bearings. The base oils were mineral oils, semisynthetics and synthetics with viscosities ranging from 130 to 460 centistokes. Synthetic base oils, combined with the right additives, reduce power losses, provide stability against oxidation and allow operations under a wider range of temperatures. The synthetic base oils we studied included mostly PAOs and MPAOs, which are the most common base oils for the commercial wind turbine greases.
We focused on the greases’ ability to provide wear protection, lubrication life, low-temperature performance and water handling. We set our baseline using published information from a previous study (
3), and we built on a 2013 Timken study (
4, 5) that compared 10 greases. We performed additional tests and evaluated an additional four greases on 13 different characteristics (
see Figure 5).
Figure 5. The Timken Co.’s 2018 grease comparison study expanded on results of a similar study in 2013. (Figure courtesy of The Timken Co.)
For the current study, we reviewed test details provided by the grease suppliers and performed our own bench tests to evaluate film thickness, traction, torque, temperature performance and grease migration. We found significant variations in grease properties, including viscosity, NLGI grade and base oil types. (We did not evaluate additives in this study.) We chose a small subset of the best-performing greases for additional bench tests to evaluate specific characteristics.
We selected key characteristics for wind turbine grease performance and prioritized them accordingly. Bearing durability and overall performance were given top priority. Other factors we considered include wear performance, grease distribution, grease degradation, corrosion performance, pumpability and low-temperature performance.
We performed three types of tests (
see Figure 6). Film thickness studies (PCS-EHD2 rig) showed the influence of grease thickeners and additives on film thickness formation at various speeds and temperatures and allowed us to compare film thicknesses in new and worked greases. Traction and Stribeck tests (WAM6 rig) allowed us to compare traction coefficients at different slide-to-roll ratios (SRR), speeds and temperatures. We used this information to update bearing calculation tools for modeling grease performance. We used a lubrication evaluation machine (LEM) to investigate the effect of grease selection on bearing operating temperatures and torque and to see how various greases migrated and were distributed within the bearings.
Figure 6. Greases were compared using film thickness tests (top); traction and Stribeck tests (middle); and temperature, torque and grease migration tests (bottom). (Figure courtesy of The Timken Co.)
We found that grease film thicknesses were similar to the film thicknesses of the respective base oils and there was not much difference in the film thicknesses of fresh and worked grease. Raising the temperature to 80 C reduces the film thickness by 75% compared with films at 40 C, but increasing the entrainment speed (the velocity of lubricant between the two contact surfaces) produces thicker films. Higher-viscosity greases produce thicker films, which provides better lubrication.
For the traction tests, we focused on the contact between the rollers and raceway for spherical (SRB), cylindrical (CRB) and tapered (TRB) roller bearings (
see Figure 7). Synthetic base oils and greases made with synthetic oils had lower traction coefficients than for mineral oils and semisynthetic oils. As expected, greases had higher traction coefficients than base oils (
see Figure 8). Also, the traction coefficients at 1% slip (SRR) for tapered roller bearings were less than for spherical roller bearings at >10% slip. Stribeck tests at 5% slip confirmed that different entrainment speeds produced similar traction coefficients for mineral oils, synthetic and semisynthetic oils, and thus, a clear separation of traction coefficients was observed for different base oil types under different lubrication regimes.
Figure 7. Stribeck curves for various types of rolling bearings show that (top) synthetic base oils and (bottom) greases made with these base oils have lower traction coefficients than mineral base oils and greases. (Figure courtesy of The Timken Co.)
Figure 8. Greases typically have higher traction coefficients than their base oils, and greases made with mineral oils and semisynthetic oils have higher traction coefficients than greases made with synthetic base oils. (Figure courtesy of The Timken Co.)
Proper grease distribution within the bearing can reduce wear and lengthen the time between re-lubrication maintenance shutdowns. Desirable grease properties include low grease loss, low operating temperatures and low torque. We conducted grease migration studies on an LEM, a type of single-bearing tester that evaluates the effects of operating temperature, bearing torque and grease distribution in the bearing.
For the best-performing greases, there was minimal grease on the top ring, but the grease distributed well along the roller raceway (
see Figure 9). Less-well-performing greases showed significant grease loss and grease migration to the top ring. Some greases that exhibited significant loss nevertheless left a residual oil film on the rollers and raceway. There was little difference in migration behavior between fresh greases and worked greases. Unlike the results of the traction tests, the greases made with high-viscosity base oils showed higher torque in the LEM tests. The results of these studies were similar to those from spin testing conducted on a full-size mainshaft bearing.
Figure 9. Grease selection has a significant effect on whether the grease remains in the raceway, where it can provide the best lubrication (blue boxes) or migrates to the top ring (black boxes). (Figure courtesy of The Timken Co.)
Grease properties vary not only with the type of base oil and thickener individually but also with the combination of base oil and thickener, so working closely with grease suppliers and formulators is critical to optimizing performance. One grease we studied was made with a high-viscosity base oil that had a 75% higher torque and 15% higher bearing OD temperature compared with the lower-viscosity base oil used for another grease (
see Figure 10, greases A and C, respectively). Nevertheless, because both greases had good migration properties, they both showed similar torque and temperature behavior. In fact, even though the first grease was made with a higher-viscosity base oil, its overall performance was better than that of the second grease (
see Figure 11).
Figure 10. Greases with different base oil and thickener properties can exhibit similar behavior when the base oil and thickener are combined. (Figure courtesy of The Timken Co.)
Figure 11. Grease A from Figure 10 had the best overall performance, even though it was made with a higher-viscosity base oil than grease C, because grease A’s good migration properties provided similar torque and temperature properties. (Figure courtesy of The Timken Co.)
Putting it together
We found that lubricating film thicknesses are similar for greases and their respective base oils, and film thicknesses are similar for fresh and worked grease. As expected, the film thicknesses decrease with temperature but increase with entrainment speed.
Moreover, there wasn’t a big difference in film thicknesses for mineral oils, PAOs and MPAOs. However, greases made with synthetic base oils have lower traction coefficients than for mineral oils and semisynthetic oils. The best-performing greases distribute well along the roller raceway, with minimal migration to the top ring and minimal grease loss. Fresh and worked greases exhibit similar migration behaviors.
Selecting a grease for wind turbine bearing applications requires optimizing several factors, but proper grease selection can reduce maintenance costs and downtime, and it can help prevent unexpected damage to bearings.
REFERENCES
1.
California ISO Glossary; available
here.
2.
Mistry, K., Lucas, D. and Shiller, P. (March/April 2019), “Grease Selection for Main Shaft Bearings in Wind Turbines: Connecting Field Trial Results to Application Testing,”
The NLGI Spokesman,
83 (1), pp. 24-33. Available
here.
3.
Braun, H. (Nov. 15-17, 2011), “Wind Turbine Grease Lubrication,” in
Wind Turbine Tribology Seminar: A Recap, by Errichello, R., Sheng, S., Keller, J. and Greco, A., eds., National Renewable Energy Laboratory Wind and Water Power Program, Boulder Colo., pp. 10-11. Available
here.
4.
Pierman, D., 80th National Lubricating Grease Institute Annual Meeting, Tucson, Ariz., June 15-18, 2013.
5.
Pierman, D. A. (April/May/June 2013), “Main Bearing Lubrication for Wind Turbines: A Systematic Approach for Grease Selection,”
EuroGrease, pp. 28-38 (presentation at the 25th ELGI Annual General Meeting 2013, Amsterdam, The Netherlands). Available
here.