Spinning natural fibers
R. David Whitby | TLT Worldwide July 2019
To reduce heat, workers add friction-reducing lubricants to yarn.
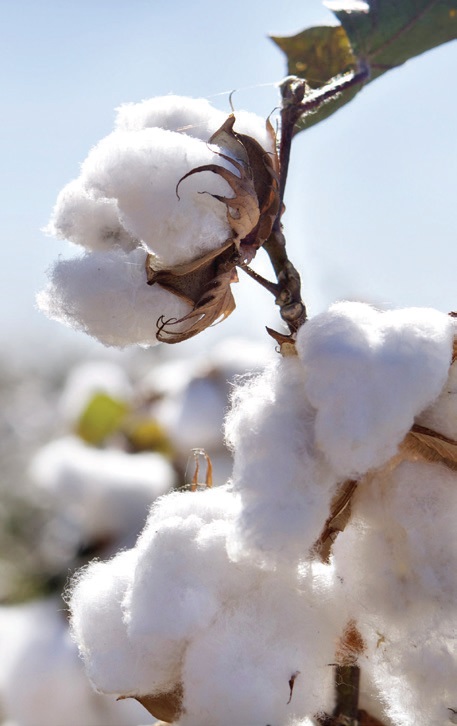
Cotton fibers are almost pure cellulose with six or seven seeds in a boll and up to 20,000 fibers attached to each seed.
© Can Stock Photo / PaulMatthew
Wool fibers, also called staples, are obtained from sheep, goats, muskox and other animals and consist of proteins, known as keratins, together with a few percent of lipids. The fibers are typically between 40 and 150 mm in length, between 12 and 24 microns in diameter. The quality of wool is determined by its fiber diameter (the most important factor), crimp, yield, color and staple strength.
Cotton fibers are fluffy and grow in a boll or protective case around the seeds of cotton plants. Cotton bolls increase the dispersal of the seeds. Cotton fibers are almost pure cellulose. There are usually six or seven seeds in a boll and up to 20,000 fibers attached to each seed. The length of the fibers is the determining factor in the quality of the cotton. In general, the longer the staple grows, the higher the quality of the cotton. Short staple cotton is between 95 and 240 mms in length, medium staple cotton is between 254 and 286 mm in length, and long staple cotton is between 300 and 635 mm in length.
These fibers must be spun into yarn in order to make fabrics. Spinning is an ancient art in which fibers are drawn out and twisted together to form yarn. For thousands of years, fibers were spun by hand using simple tools. But what keeps the spun yarn from unravelling before being woven or knitted into fabrics? The characteristics of spun yarn vary according to the type of fiber, its length, alignment and quantity and the degree of twist.
Wool also has both a complex chemical and physical structure. The fiber’s surface is comprised of overlapping cuticles, which appear scaly under a microscope. This is very different from the smooth surface of synthetic fibers. The scales on wool fibers can lock together under the effects of friction during the initial spinning process. Friction starts the process of forming yarn.
Conversely, cotton fibers have thousands of hydroxyl groups on the outer surfaces of each fiber, so when the cellulose chains are positioned close to each other, thousands of hydrogen bonds can form. The initial spinning process results in the formation of hundreds of chemical bonds holding the chains together. The hydrogen bonds account for much of the stability of cotton fibers.
The direction in which the yarn is spun is called twist. Yarns are characterized as S-twist or Z-twist according to the direction of spinning. Tightness of twist is measured in TPI (twists [turns] per inch). With S-twist, the fibers are twisted from top left to bottom right, resembling the long stroke of the letter S. Z-twists are twisted in the opposite direction. In spinning, the initial twist for the individual strands should be an S-twist. These strands are then twisted together in a final Z-twist to form the yarn.
Two or more spun yarns may be twisted together or plied to form a thicker yarn. Generally hand-spun single plies are spun with a Z-twist, and plying is done with an S-twist. It is important, however, to spin the single plies in one direction and then spin them together in the opposite direction. In this way, the opposite-direction plying keeps the spun yarn from untwisting itself.
Hand spinning began to be replaced by powered spinning around 1764 with the invention of the spinning jenny by James Hargreaves. This was followed in 1779 by Samuel Crompton’s spinning mule. This produced stronger threads and was suitable for mechanization on a large scale. A later development, from 1828-1829, was ring spinning. In the 20th Century, new techniques, including open-end spinning or rotor spinning, were invented to produce yarns at rates in excess of 40 meters per second.
During spinning, the yarn issuing from the drafting rollers passes through a thread-guide, around a traveler that is free to rotate around a ring and then onto a tube or bobbin, which is carried on a spindle, the axis of which passes through a center of the ring. The speeds at which the yarn travels through the guides, travelers and bobbins means that friction becomes an issue, so friction-reducing spinning lubricants are applied to the yarn to reduce heat generation.
So for wool (but not for cotton), friction is important at the start of spinning, and friction needs to be controlled for all fibers during the spinning process.
David Whitby is chief executive of Pathmaster Marketing Ltd. in Surrey, England. You can reach him at pathmaster.marketing@yahoo.co.uk.