Straight oil metalworking fluids: From use to recycling
Dr. Nancy McGuire, Contributing Editor | TLT Webinars June 2019
Proper maintenance is the difference between replacing every few weeks and indefinite reuse.
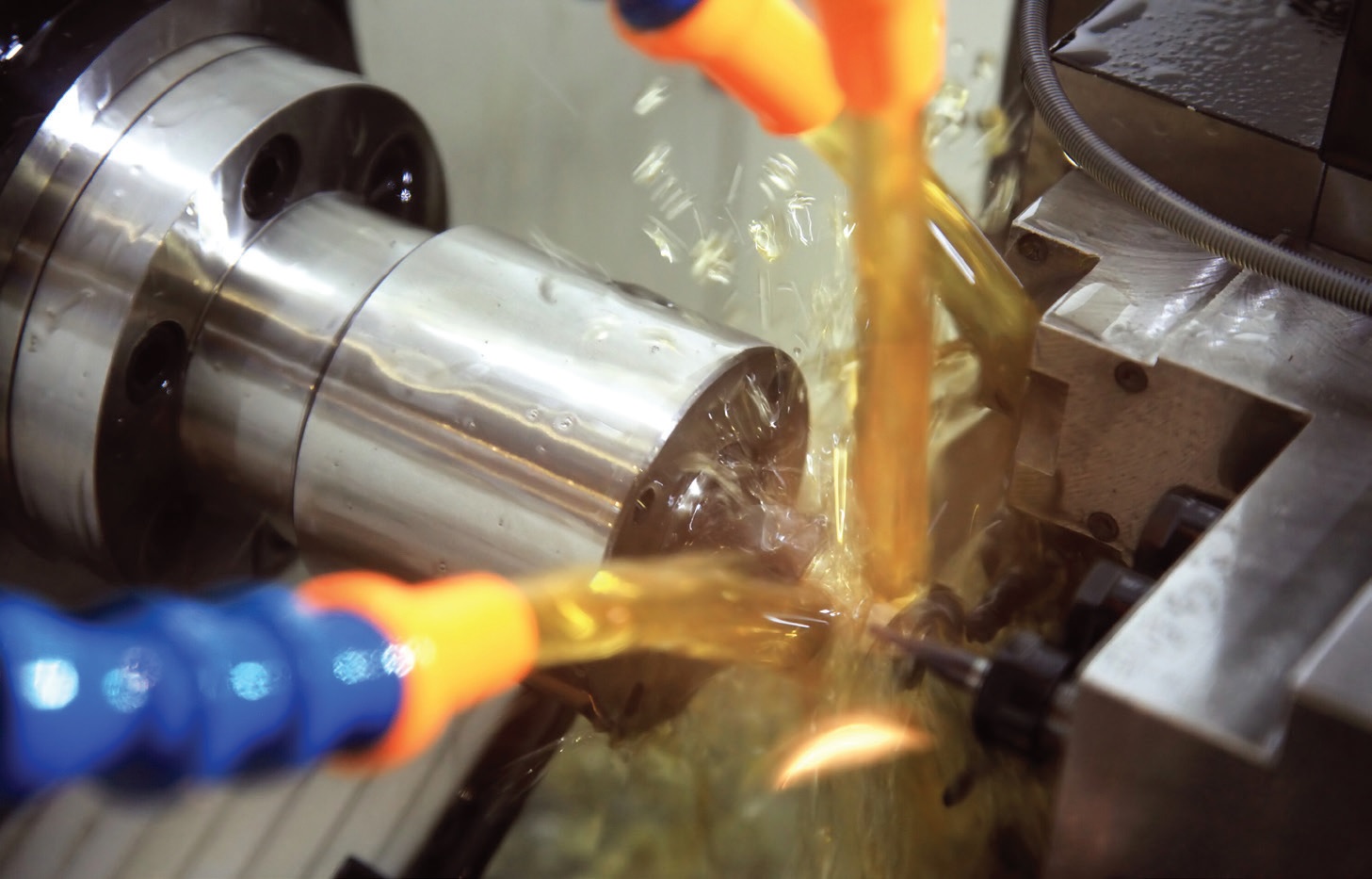
© Can Stock Photo / sspopov
KEY CONCEPTS
•
Processes and process variables determine the choice of a straight oil.
•
Oils can fail, just like water-dilutable products.
•
Recycling methods can slow fluid failure.
MEET THE PRESENTER
This article is based on a Webinar presented by STLE Education on Dec. 10, 2018.
Straight Oils: From Use to Recycling is available at
www.stle.org: $39 to STLE members, $59 for all others.
Alan Cross is a senior project engineer with Houghton International Inc. in Valley Forge, Pa. He received his bachelor’s of science degree in chemical engineering in 2004 from the University at Buffalo and has been in the metalworking fluid industry for 14 years. Cross has been involved in metalworking fluid projects including fluid recycling, industrial wastewater and pure water treatment, process improvement as well as research and development in the metalworking fluid and fluid power areas. Cross has presented many papers at STLE and global conferences and holds two patents. He has co-authored a chapter titled Recycling of Metalworking Fluids with John M. Burke in Metalworking Fluids, Third Edition. You can reach Cross at
across@houghtonintl.com.
Alan Cross
Straight oils can break down over time and fail, just as water-dilutable products do, but fluid failure can be slowed through best practices in recycling methods. Processes and process variables—the type of machine operation, type of metal and surface finish and the cleanliness of parts coming off the machine—determine the choice of a particular straight oil.
Viscosity (i.e., load-carrying capacity) is the major consideration for using straight oils in metalworking applications. Straight oil fluids are preferable to water-dilutable fluids when a high degree of lubrication is a higher priority than high cooling capability. Typically straight oils are used in slower operations and those producing parts with tight tolerances and in severe operations like broaching, pipe threading and gear cutting or in finishing bearing surfaces. They also are used in machines, including some older units requiring high viscosity fluids.
Straight oil types
The general terms
straight oil and
cutting oil, applied to MWFs, can refer to true straight oils, compounded or blended oils and extreme pressure (EP) oils. The term
neat oil sometimes refers to a straight oil formulation, although it more often refers to the base oil before the additives are put in.
Petroleum oils are the most common base oils, but esters can be used when more lubrication is required. Synthetic oils are not commonly used, mainly because of their cost, but they can be useful for specific applications.
True straight oils can be a blend of several base oils, but base oils are the only components of these products. The primary difference between various true straight oils is their viscosity. These oils are typically used for light machining operations like honing or reaming where only small amounts of metal are removed.
Compounded or blended oils contain base oils and specific additives, and they are typically used for medium-duty applications. These oils are used in a wide variety of applications, and various products offer differences in viscosity, lubrication and wetting.
EP oils mix base oils with mild or active EP additives, and they are used in severe applications that remove large amounts of metal but still require a good surface finish. EP additives are generally sulfur, phosphorus or chlorine compounds. EP oils are formulated especially for heavy-duty applications, so using them to reduce the amount of oil needed in lighter applications is not likely to be effective.
Other additives include lubrication enhancers like esters and fatty materials, over-based calcium sulfonates and some polymers. Antioxidant additives protect against oxidation from tramp oil and water, and corrosion inhibitors protect the finish on the active, freshly machined surface. Deaerators (which push air to the fluid surface) are used for applications that generate turbulence and entrained air since defoamers aren’t as effective in straight oils as they are in coolants. Anti-mist agents can be used for machines that aren’t well sealed from the atmosphere.
Oils that contain additives, especially EP additives, require more maintenance in terms of testing and regeneration than true straight oils do. Replenishing an oil can be as simple as topping off the reservoir. However, before an operator pours a new oil on top of the old oil, it’s imperative to check with the fluid supplier or manufacturer and find out if the two fluids are compatible.
Failure processes
Straight oil failures fall into two categories: contamination and fluid breakdown. Failure mechanisms include contamination by particles and fines, water contamination, heat, evaporative losses, extraneous oil contamination and additive depletion.
Oil contamination by particles and fines represents a nonpermanent failure mechanism: we can remove the material almost as quickly as it’s generated. This is the most common cause of oil failure, and it can’t be completely prevented because one of the functions of a MWF is to wash particles away from the work area. Particles, fines and debris from the machining process are distributed throughout the system along with dirt and debris from the plant. Overall particle levels and size distributions are determined using particle counters or filter tests. More specific particle identification is done using elemental analysis or, less commonly, ash testing.
High particle levels can reduce the cleanliness of parts and damage the surface finish—especially if finished parts are stacked and rub together. Particles also can stain parts and tools. Straight oils are inherently corrosion inhibiting, but dissimilar metals coming into contact (like steel chips on an aluminum part) can set up a galvanic cell that promotes corrosion.
Smaller particles, such as those from grinding processes, are more harmful than larger ones. They are harder to remove, and they can recirculate over and over again throughout the system. Abrasive microfine particles can scar metal pieces (
see Figures 1 and 2).
Figure 1. Smaller particles like grinding swarf are more harmful than large chips. (Figure courtesy of Houghton International, Inc., and Byers, Jerry P., ed., Metalworking Fluids, Third Edition, 2018, CRC Press/Taylor & Francis. With permission.)
Figure 2. Fine particles are difficult to see when dispersed (left) but are clearly visible when they settle (right). (Figure courtesy of Houghton International, Inc.)
Extraneous oils, also called tramp oils, are another source of contamination. These oils can enter a MWF through hydraulic leaks, oil dripping from ways, greases or materials spilling into an open machine. Incoming parts, especially those with rust-preventive coatings, also can introduce extraneous oil. The problem can be worse in a system with a relatively small sump that doesn’t allow extraneous oil to separate out before it is recirculated. Extraneous oil contamination can be determined by measuring general viscosity trends. FTIR analysis can identify specific oils and organic additives, and elemental analysis is especially good for identifying EP additives.
High levels of extraneous oils can significantly raise or lower a straight oil’s viscosity. Additives in extraneous oils can stain parts and otherwise reduce part quality, and the problem is especially bad for yellow metals and aluminum. Hydraulic fluids with EP additives could contaminate a straight oil without EP additives. (Some companies switch to hydraulic fluids that don’t use phosphorus, sulfur or chlorine for just that reason.)
Fluid breakdown is a more difficult problem to solve. It can’t be prevented, but it can be slowed down using best practices.
Water is a contaminant, but it also contributes to fluid breakdown, so water content should be measured on a regular basis. This is especially important in areas with wide temperature swings where water condensation could drip into the oil. Water can drastically reduce the apparent viscosity of a straight oil, which increases friction and tool wear. Certain situations may require continuous inline or online monitoring to catch a water-contamination problem before it gets out of hand. The best method for water-content measurement in straight oils is Karl Fischer titration, which is accurate down to the low (~50) parts-per-million level.
Excess heat can accelerate fluid breakdown by promoting oil oxidation and additive depletion. Heat is generated by the machinery and friction from the metalworking processes and should be removed through heat exchange equipment. Darkening is one sign of heat degradation, but a darkened oil isn’t necessarily out of specification—it depends on what caused the oil to darken (
see Figure 3).
Figure 3. Water contamination causes a variety of problems in straight oils. (Figure courtesy of Houghton International, Inc., and Byers, Jerry P., ed., Metalworking Fluids, Third Edition, 2018, CRC Press/Taylor & Francis. With permission.)
Evaporative losses also can cause an oil to perform poorly. Base oils with various viscosities, boiling points and volatilities are blended to fine-tune the viscosity to the desired value since it’s impractical to make one-component oils for each different viscosity. Lower viscosity oils tend to have lower boiling points and higher volatilities. As they evaporate, the overall viscosity of the straight oil increases. Although this higher viscosity increases the load-carrying capacity, it can present problems with flow and with the lubrication characteristics in the interface between the tool and workpiece. Kinematic or dynamic viscosity tests monitor the effects of heat and evaporative losses.
Normal operations break down or neutralize additives, or they carry additives away on workpieces moving down the line. EP additives react and form new compounds that are carried out on parts or removed during filtration. Additive depletion is determined using X-ray fluorescence, atomic emission spectroscopy or elemental analysis.
Straight oil recycling
Recycling straight oils lowers costs by reducing the amount of new oil purchased and by removing sources of fluid failure to increase service life. Most recycling processes are simple and easy to implement. Recycling methods include removing particulates and water, adjusting the viscosity, removing heat, replenishing additives and partial fluid dumping.
Filtration and separation can be used alone or combined to increase effectiveness. Filters use a physical barrier (filter paper, filter media, screens) to remove particles, and filter aids like perlite or cellulose can improve effectiveness. Filters are usually disposable, but many landfills have stopped accepting these materials because they contain oils and metal particles. Metal screen filters do not present a disposal problem since they can be used over and over again. Portable oil filter units, which can be mounted in a kidney-loop fashion, are good for systems with several individual sumps (
see Figure 4).
Figure 4. (a) Metal screen filters can be reused rather than discarded. (b) A portable filter unit is useful for systems with several small sumps. (Figure 4a courtesy of Rosedale Products, Inc. Figure 4b courtesy of Oil Filtration Systems, Inc. Figure also courtesy of Byers, Jerry P., ed., Metalworking Fluids, Third Edition, 2018, CRC Press/Taylor & Francis. With permission.)
Bulk filter media come in a variety of porosities for different applications. Fine pores will trap more of the smaller particles, but pores smaller than five microns can strip some additives out of a fluid system. Analyzing the residue on the filter media will show whether the filters are contributing to additive loss.
Magnetic ferrous particles can be removed using a magnetic separator with a rotating drum. A blade on the back side scrapes off the magnetic particles sticking to the drum and deposits them into a collection bin so they can be taken to a recycling facility. This method removes even particles in the sub-micron range without filtering the additives out of the oil (
see Figure 5).
Figure 5. A drum magnetic separator captures and collects large and small ferrous particles. (Figure courtesy of Eriez Manufacturing Co. and Byers, Jerry P., ed., Metalworking Fluids, Third Edition, 2018, CRC Press/Taylor & Francis. With permission.)
Liquid-solid centrifuges remove large particles like chips that settle quickly, but they are less useful for separating out microfine particles. Heating the oil to increase the density difference between fine particulates and the oil may not be especially effective, especially if this causes the oil to oxidize and break down sooner. Anyone considering this practice should contact the centrifuge manufacturer for recommendations and determine whether it removes enough extra material to justify the cost of the energy for heating and cooling the oil and the effect on the oil’s performance.
Liquid-liquid centrifuges are only useful in specific applications where there is a large density difference between the straight oil and the extraneous liquid. Lab analysis can determine if centrifugal separation is effective for a particular operation.
Gravity separation is a less common option. It requires time, a large volume of excess oil and periodic sampling to determine when the oil is ready for reuse. Some operations allow used oil to sit in a settling tank for as long as two years before it is put back into service.
Vacuum dehydration is the most commonly used method for removing water from a straight oil. This can be a slow process depending on how much water is in the oil. Heating the oil speeds the water removal, but the temperature should not be raised so high that it degrades the oil. A dehydrator should be kept onsite in areas that are prone to water ingress or where condensation is a problem. Portable dehydrators can be moved from sump to sump using a forklift or a dolly (
see Figure 6).
Figure 6. Vacuum dehydration is the most common method for removing water from oil. (Figure courtesy of Oil Filtration Systems, Inc., and Byers, Jerry P., ed., Metalworking Fluids, Third Edition, 2018, CRC Press/Taylor & Francis. With permission.)
Membrane dehydrators have a small footprint, and they can be a permanent addition to straight oil systems, especially small systems with small single sumps. These dehydrators force oil through a membrane-lined tube at high pressure. The oil component flows straight through the tube, but the water is forced through the pores in the membrane and is carried away by a vacuum or a stream of dry air. Membrane dehydrators can run continuously if necessary (
see Figure 7).
Figure 7. A portable membrane dehydrator can be kept onsite. (Figure courtesy of Compact Membrane Systems and Byers, Jerry P., ed., Metalworking Fluids, Third Edition, 2018, CRC Press/Taylor & Francis. With permission.)
Of course, given enough time, water will separate on its own, but turning a system off and letting the water separate out is seldom practical—and water can do a lot of damage in a short time. The time needed to separate the water depends on how much water is in the system and how long it’s been recirculating and mixing in with the oil. If a large amount of water has been dumped into a system, the best practice is to shut the system down and decant as much water as possible, followed by an oil analysis to identify any changes to additives, viscosity and other properties.
In addition to keeping the oil dry, it’s essential to continuously remove heat to keep the oil in specification. Thermostatted chillers, with or without refrigeration units, are attached to machines or sumps to keep the temperature under control, using air or liquid as a heat-exchange medium. Refrigeration works better than radiators in warm climates or shop environments, but radiators are effective in cooler surroundings. Using a sufficient oil volume and reservoir size also helps keep temperatures down by giving the heat a chance to dissipate from the oil before it is put back into service. Residue buildup in a sump can significantly decrease the volume of oil it can hold, so the oil can’t cool down enough before it’s recirculated.
Keeping oil in a sump just for the purpose of letting it rest is generally not necessary. Letting oils sit idle requires purchasing larger volumes of oil, and it can allow the oil to cool down, which could cause water condensation problems. When the oil comes back up to operating temperature, the added water could reduce the oil’s apparent viscosity and increase oxidation and degradation of the oil. Straight oil fluids can be run continuously as long as the operator monitors viscosity, water content, dirt counts or particle levels and oil temperature—and as long as machined parts are checked for specific pass/fail criteria established by the customer.
The chemistry
Modifying the chemistry of the oil is sometimes necessary, but it’s a more difficult solution than the fixes previously described. Verifying the results requires laboratory analysis and guidance from the manufacturer. Adding base oils can bring a fluid’s viscosity back into specification if it has become too high or too low, but this can throw the concentrations of the other formula components out of balance.
Oil additive levels must be checked periodically, and additives must be replenished as they are consumed and removed. Again, this requires laboratory analysis and guidance from the manufacturer, but ordinary maintenance testing and recommendations can be a simple, routine process. Manufacturers often provide standard packages (e.g., lube or EP pack) for commonly required replenishments. These packages are diluted with base oil, then dispersed through the system. Packages that are supplied as solids must be dissolved in base oil (this can require heating the oil) before it is circulated through the system.
As a last resort, when a straight oil has lost its desirable properties and other recycling options are not effective, it may be necessary to dump some portion of the straight oil and replace it with fresh product. The used oil must be disposed of properly, which generally incurs a disposal cost. If this is a recurring problem, you may be using an oil that’s not appropriate for your particular process. When dumping is necessary, the operator should shut off the system and let the water and particulates settle to the bottom of the tank where they can be drained off. This ensures the system is clean before fresh oil is added.
Just like any other metalworking fluids, straight oils can fail. However, their service life can be greatly increased by reducing the mechanisms that cause failure—this largely involves keeping them clean, cool and dry. Proper maintenance can make the difference between replacing the oil every few weeks to reusing the same oil indefinitely with routine replenishment operations.