Minding the front end with used plant oil
Don Smolenski | TLT Machinery June 2019
You still need off-site services, but the greatest savings comes from within the plant.
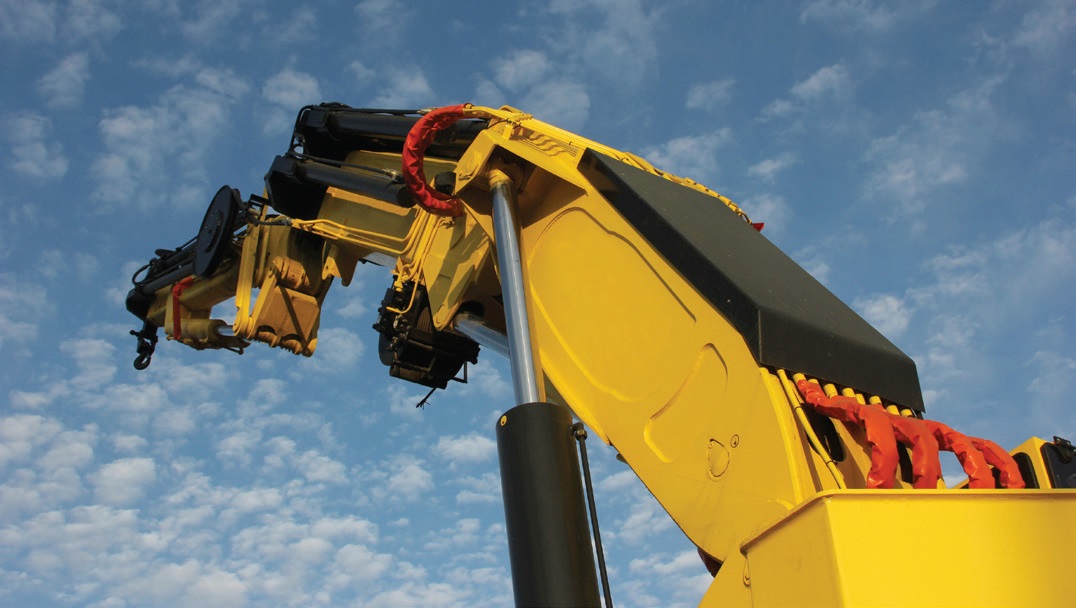
Different streams produce used oil of varying quality. Used hydraulic oil might be 95% or more high quality with some water and dirt.
© Can Stock Photo / SafakOguz
In April I wrote about managing General Motors North American plants’ used oil with off-site oil service providers. Although this is absolutely necessary, the real leverage is in better oil management
within the plant (the front end). Working with several plant people, we developed a holistic approach for plant used oil.
Maybe somewhat surprisingly, good on-site oil management starts with good specifications and an approval process for the fluids and lubricants coming into the plant, as well as good management of products prior to, during and after use in the machines. Sourcing a robust, high-quality hydraulic fluid, for instance, is a good start. Using the wrong oil will result in premature oil changes (generating more used oil) and potential harm to the equipment.
Product consolidation (fewer products) and clear drum and oil fill point markings makes it easier for the oilers and reduces the chance of mis-oiling. Teaching the mantra to “keep the oil clean, cool and dry” also is important. The use of bladder or desiccant breathers reduces the intrusion of moist and potentially dirty air into the hydraulic system. Educating the oilers on the need for very clean containers and careful fill procedures will result in longer oil and equipment life. Using oil analyses to determine the proper oil change point instead of fixed oil change intervals will generally safely increase oil change intervals. Fixing the leaks also is a good idea but generally difficult in practice.
OK, so you do all of the right stuff prior to and during the oil life, but at some point the oil will become wet and dirty and need to be changed, right? Well, maybe not! There is equipment, somewhat analogous to a kidney dialysis machine, that connects to the oil reservoir and dewaters and filters the oil, avoiding, or at least significantly delaying, the need for an oil change.
Despite best efforts, though, used oil is generated. It’s important to understand that each used oil stream has a certain quality. Used hydraulic fluid, for instance, may be 95% or more high-quality oil with some water and dirt—a very good stream as used oil goes. In contrast, a spent soluble oil cutting fluid might only be 10% oil, with rag, microbial contamination, metal fines and the remainder water. This is a poor-quality used oil stream.
It’s important to segregate the good and bad quality streams, provided tankage is available. Commingling the used hydraulic fluid stream with the used soluble oil will generally cost significantly more for off-site used oil services than keeping these streams segregated. This can be difficult for plant people to comprehend, so I developed a beer analogy to help illustrate the point.
If, in one hand, you have a skunky beer that has been sitting in the sun and has a dead fly in it (the nasty-smelling used cutting fluid) and in the other hand a frosted mug with your favorite IPA, lager, wheat beer or whatever is your favorite (the used hydraulic fluid), would you mix these two beers together? Yet, that’s what we do with the used oil streams. Most of the people you share this with will cringe at (but remember) the beer analogy. Whatever it takes to get the point across!
OK, I’m going to wrap up now. For some reason I’m feeling kinda thirsty…
Don Smolenski is president of his own consultancy, Strategic Management of Oil, LLC, in St. Clair Shores, Mich. You can reach him at donald.smolenski@gmail.com.