Physical Properties and Tribological Performances of Ni-W Coatings in Lubricated Sliding Contact
Alexis Kruth | TLT Scholarship Research March 2019
Department of Chemical and Biomolecular Engineering and the Timken Engineered Surfaces Laboratory, The University of Akron, Akron OH 44325
Online only in TLT Archives
Booser Scholarship paper focuses on physical properties and tribological performances of Ni-W coatings in lubricated sliding contact
The E. Richard Booser Scholarship Award is awarded annually to undergraduate students who have an interest in pursuing a career in tribology. As a requirement for receiving an STLE scholarship, students participate in a tribology research project and submit a report summarizing their research. For more information about the Booser scholarship, visit www.stle.org.
The 2018 recipient of The E. Richard Booser Scholarship Award is Alexis Kruth, a third-year student studying chemical engineering at the University of Akron with minors in chemistry and applied mathematics who also is partaking in a university cooperative work program. She is scheduled to graduate from her five-year program in spring 2021. She conducted her research in STLE-member Dr. Gary Doll’s Timken Engineered Surfaces Laboratory in the Engineering Research Center on campus. As part of Kruth’s extracurricular activities, she is a member of one of the university’s engineering design teams. You can reach her at aak73@zips.uakron.edu.
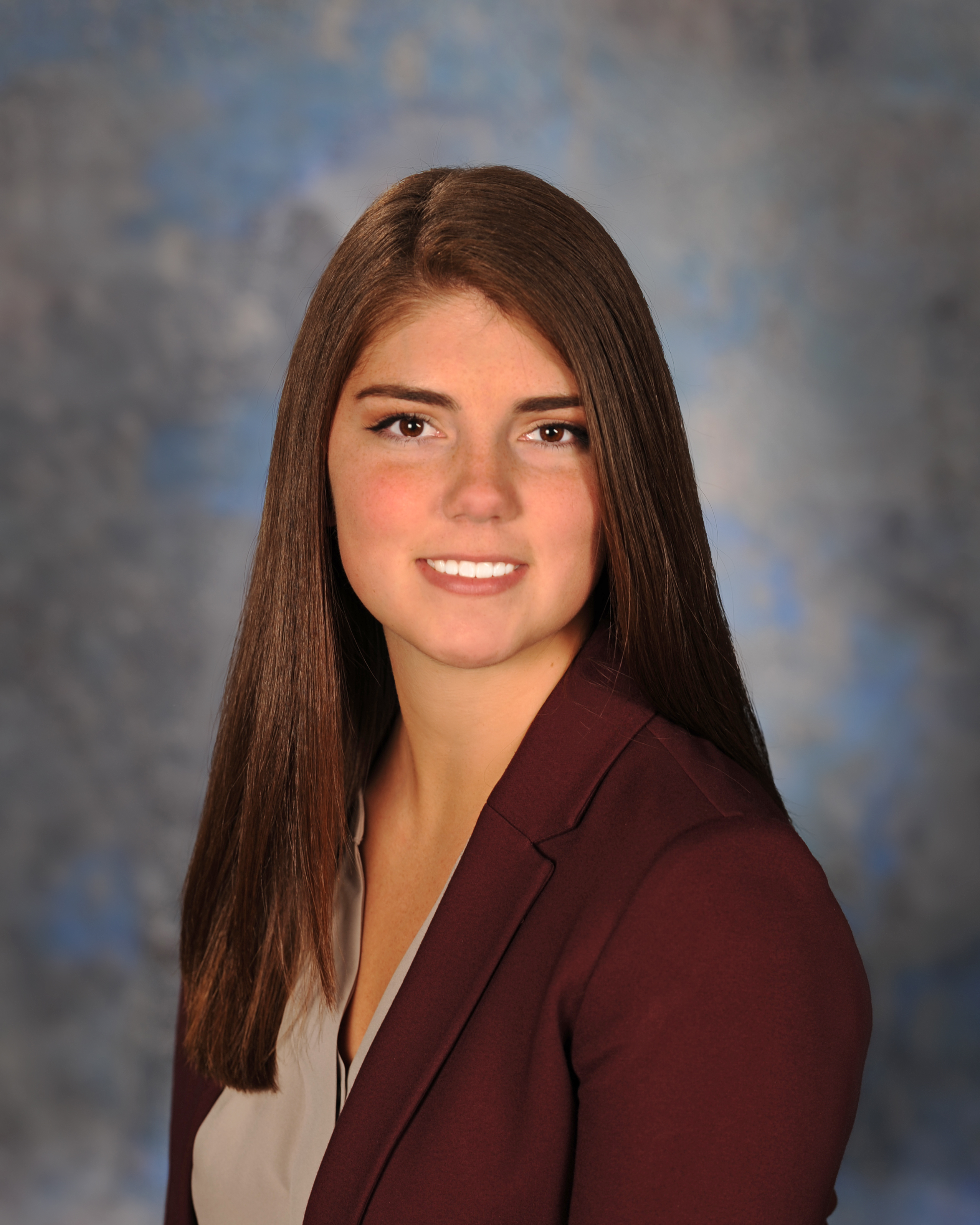
Alexis Kruth
Abstract
The development of alloy coatings with and without nanocrystalline additives by pulsed reversed electrodeposition was aimed at providing friction reduction, wear protection, and corrosion resistance to precision steel components. Nickel alloys with and without nanometer-sized TiO
2 dopants (i.e., Ni-W/TiO
2) were developed and subsequently proved to be particularly beneficial as tribological coatings in sliding contact. Undoped and titanium dioxide doped (TiO
2) Ni-W coatings on steel substrates were evaluated in dry and lubricated reciprocating sliding contact. As a result of tribo-chemical reactions occurring in lubricated contact, WS
2 tribofilm formation was observed on the steel counter faces, which resulted in a significant reduction in wear and friction.
Introduction
The application of wear resistant coatings on steel such as WC/a-C:H [1] or solid lubricant coatings such as Ti-MoS
2 [2] add desirable friction and wear attributes to rolling element bearings and gears. Although these coatings can provide excellent tribological performance, their corrosion protection is rather poor. Failure of engineered parts due to corrosion as well as wear of metallic surfaces leads to loss of efficiency and the potential failure of components. For example, micro cracks at pits formed due to corrosion may cause spalling during impact or roughening of a surface, which will reduce the energy that is needed to abrade away metal. Therefore, tailoring the coating properties on the surface of engineered components, so that their function and serviceability comply with corrosion as well as wear resistance, is very important.
Material couples such as cobalt-based and chromium-boron alloys that are corrosion resistant have been used for many years in mechanical components. However, environmental legislation and application requirements have promoted the development of Cr- and Cd-free surface treatments with improved durability. Ni and its alloys seem to be a promising alternative to Cr and Cd since these materials have good corrosion resistance and form metallurgical bonds to steel alloys. Alloying nickel with other materials, such as tungsten provides not only corrosion resistance, but excellent wear resistance [3]. For example, a Ni-W alloy is employed in high-temperature applications due its excellent resistance to thermal decomposition [4].
Beside corrosion resistance, a very interesting feature of tungsten containing Ni alloys is its ability to form a dichalcogenide film sliding contact occurring in sulfur-containing lubricants. For example, extreme pressure (EP) additives can react with tungsten in the Ni alloy and generate WS
2 in contact areas thereby providing an enhanced wear resistance [5].
One way to achieve this solid lubricant tribofilm is to coat the steel surface with WS
2; however, the tribological performance of WS
2 films is degraded by humid air [6]. Another approach to is to alloy or dope tribological coatings with WS
2 nanomaterials, for example, a WC/DLC/WS
2 composite coating [7].
Pulsed Reverse Current (PRC) electrodeposition is a convenient method for performing the controlled deposition of Ni-W coatings [8]. Ni-W coatings have been deposited by applying square waveforms with different pulse frequencies, current densities and pH values, and the corrosion resistance of several coatings were tested [9]. These results revealed that the Ni-W coatings had excellent corrosion properties, and that doping the coatings with nanoparticles were not only beneficial for corrosion protection, but also increased the hardness and wear resistance of the coatings.
Materials and Methods
Ni-W coatings were PRC electrodeposited onto 10mm diameter by 2mm thick 52100 steel coupons at 65 ⁰C from a sulfate-based electrolyte using a two-electrode configuration and a VersaSTAT 4 Potentiostat boosted KEPCO Bipolar Operational Power Supply/Amplifier. Details of the deposition process have been described in Reference 5. TiO
2 doping of the Ni-W was accomplished by adding 2g/L TiO
2 nanoparticles (average diameter < 5nm) to the solution and placing the suspension to ultrasonic bath for 60 minutes. Prior to deposition of the coatings, substrates were cleaned by rinsing thoroughly with hexane, isopropanol, and deionized (DI) water three times. Based upon previous research [5], the forward current density was set as 40mA/cm
2 while the reverse current density was maintained at 12mA/cm
2. Nitrogen gas was bubbled into the cell at a constant rate while the solution was stirred with a magnetic stir bar.
Tribological tests were carried out using a PCS Instruments High Frequency Reciprocating Rig (HFRR) to measure friction and wear under reciprocating sliding motion at three different temperatures, (40 ⁰C, 75 ⁰C, 100 ⁰C). Coated and uncoated disks were tested in a fully formulated engine oil and an un-additized mineral oil with equivalent viscosities. The HFRR test conditions were 1mm stroke length, 10N normal load, 60 min durations, at 20Hz. The amount of lubricant in each test was 1mL, and the viscosity of both lubricants at 40 ºC was 50 cP. The metallic elements and their concentrations in the fully formulated engine oil are gathered in Table 1.
Table 1: Elemental metal composition of the fully formulated engine oil measured using an ICP-Trace Analyzer
Wear volumes of the balls and coated disks from were measured after each test using a Zygo NewView 7300 interferometric microscope. Additional surface measurements of wear scars were conducted using a Hitachi Tabletop Scanning Electron Microscope (SEM) equipped with an energy dispersive X-ray spectroscopy (XEDS). Hardness and indentation modulus values of the coatings were determined from nanoindentation tests performed with a Hysitron Premier TI Nanoindenter using 10mN loads for 10s.
Results
Physical properties of the coatings
Figure 1 shows plan-view SEM images of undoped and TiO
2-doped Ni-W coatings. The thickness of these Ni–W coatings was determined by Calotest to be about 10μm and the Ni-W surface displays the cauliflower morphology typical of electrodeposited metal coatings. On the other hand, the surface of the TiO
2-doped Ni-W coating in Figure 1 exhibited a decidedly different morphology. Introduction of the TiO
2 particles to the coating resulted in a slightly more uneven coating with different dimensions of spherical shape grains.
Fig.1. SEM plan-view images of undoped a Ni-W and a TiO2 doped Ni-W coating
The hardness of the undoped Ni-W coating was measured to be 9 GPa and its indentation modulus was calculated to be about 175 GPa, yielding an H/E ratio of about 0.05. Using the same deposition parameters but with the inclusion of the nanocrystalline TiO
2 in the solute, the hardness and indentation modulus values of the TiO
2 doped Ni-W coating were found to be 13 GPa and 250 GPa, respectively, also yielding an H/E ratio of about 0.05. The approximate composition of the Ni-W coating was determined by XEDS to be Ni
0.75W
0.25 and the concentration of the TiO
2 in the doped Ni-W coating was estimated to be ~2 wt%.
Tribological performances of the coatings
Reciprocating sliding tests were performed on the TiO
2-doped and undoped Ni-W coatings paired against AISI 52100 steel balls under lubricated conditions. In Figure 2, the average friction coefficients of the coating obtained in the mineral oil and fully formulated engine oil are presented at three different temperatures. The standard deviation in the friction values was determined to be ±0.015.
Friction coefficient values of both coatings measured in the mineral base oil ranged between 0.13 and 0.15. That is, no statistical difference in friction was observed between the doped and undoped Ni-W coatings for each temperature studied; however, the friction coefficients exhibited a slight decrease with increasing temperature. In tests performed in the fully formulated engine oil, the average friction coefficients of both coatings ranged between 0.09 and 0.11. Again, no statistical differences in the friction coefficient existed for the doped and undoped samples.
Fig. 2. Friction coefficients measured in reciprocating sliding contact for AISI 52100 paired against TiO2-doped and undoped Ni-W coatings, in a mineral base oil and a fully formulated mineral oil. The standard deviation of the average friction values was ±0.015.
Wear volumes generated on the AISI 52100 balls were calculated from measurements of the radius of the wear scar, that is
and
Rb is the radius of the ball [μm], and
r is the radius of the wear scar [μm]. Wear volumes generated on the disks during the HFRR testing were measured by 3D optical profilometry. Wear volumes measured from the disks and the balls are displayed graphically in Figure 3. In this Figure, positive numbers represent a volume of material removed during the testing, while negative values denote material build up (i.e., tribofilm creation) during the testing. Standard deviations in the wear volumes were estimated to be about 10%. Examination of the wear volumes created on the disks reveals that the testing temperature strongly affected the wear of the coatings in both lubricants. Whereas wear volumes created on the Ni-W coating in the mineral oil tests performed at 40 ºC and 75 ºC were approximately equal, the 100 ºC wear volume was significantly greater. Wear volumes of the TiO
2-doped Ni-W that were created in the mineral oil tests were found to have decreased significantly with increasing temperature. In the tests performed on Ni-W in the fully formulated engine oil, negative wear (i.e., a tribofilm buildup) occurred during the 40 ºC testing, while small wear volumes were created during the 75 ºC and 100 ºC tests. Negative disk wear (i.e., tribofilm generation) was found to occur on the TiO
2-doped Ni-W in tests performed with the fully formulated lubricant at all temperatures.
All wear volumes measured on the AISI 52100 balls were found to be negative, regardless of lubricant or temperature. Wear volumes created on the Ni-W and TiO
2-doped Ni-W coatings in testing performed in the mineral oil were much more negative than the wear volumes generated in the tests performed in the fully formulated engine oil. Based on the wear volume analysis, it appears that the material buildup on the balls that occurred in the tests involving the mineral oil was largely comprised of Ni and W removed from the coatings. On the other hand, material in the tribofilms formed on the balls that occurred in the tests performed with the fully formulated engine oil appears to be largely derived from the lubricant.
Optical images of wear scars showing tribofilms generated on the Ni-W and TiO
2-doped Ni-W coated disks during testing conducted in the fully formulated engine oil at 75 ºC are presented in Figure 4. In the case of the undoped Ni-W, the tribofilm was found to reside inside the wear track of both balls and discs and appeared darker than the area outside of the wear scar. As is evident in Figure 4, the wear scar on the TiO
2-doped Ni-W coating visually appears to have been created by polishing rather than material removal.
Fig. 3. Wear volumes of the coated disks and their uncoated ball counterparts created during the HFRR tests. The approximate standard deviation in the wear volume calculations is 10%.
Fig. 4. Tribofilms generated on the Ni-W and TiO2-doped Ni-W coated disks during HFRR testing at 75C in the fully formulated lubricant
Compositions of tribofilms created on the Ni-W coating in tests with the fully formulated engine oil were investigated by XEDS and the results are presented in Figure 5. SEM images of portions of the wear scars generated on the disks and XEDS elemental maps of S and Ca in those locations are displayed for comparison. The dark regions on the edges of the 40 ºC disk wear scar were comprised mostly of S, but the elemental character of the wear scar was mostly Ca. The S content is greater and more uniformly distributed in the 75 ºC and 100 ºC disk wear scars. Although not shown in the Figure, a ~10% depletion of W in the wear scars was observed to correlate with increases in the presence of sulfur. Elemental mappings of the wear scar created on the ball from the same experiment show that the tribofilm on that surface is largely comprised of W, Ni, and S.
Fig 5. SEM/EDAX mapping of portions of wear scars created on disks coated with Ni-W and SEM/EDAX mappings of the wear scar on the ball counterface. The experiments were conducted at 75 ºC in the fully formulated lubricant.
Discussion
Based upon the experimental results of this study, it is evident that the addition of W in the Ni-W coatings serves at least two functions: it increases the hardness and wear resistance of Ni, and it synergistically interacts with S-containing additives in lubricants to form beneficial tribofilms on mated steel surfaces in sliding contact. The temperature dependence of the tribofilm formation indicates that the reactions between the W and the S are thermally driven. Additionally, the elemental analyses performed on the wear scars on the coated disks indicate that the W atoms are being tribologically abstracted from the Ni-W material. Further experiments should be performed to investigate the effects of contact stress on the tribofilm formation mechanism.
TiO
2-doping of the Ni-W increased the hardness over the undoped Ni-W, and thereby increased the wear resistance. The presence of TiO
2 did not negatively impact the tribofilm formation mechanism, and may have actually aided in the process.
XEDS mapping of the ball and disk wear scars in Figure 5 showed that both calcium and sulfur were present in the wear scars developed on the coatings, and that their concentrations were temperature dependent. That is, at 40 ºC, a Ca-rich layer formed in the wear track of the Ni-W coating. However, at temperatures of 75 ºC and 100 ºC, the calcium concentration reduced, and was replaced by S. Interestingly, Ca was not detected in the 40 ºC wear scar created on the TiO
2-doped Ni-W. Instead, a relatively high sulfur concentration was present. It was also observed that the tungsten concentration was ~10% less in the wear tracks of both coatings than in the coating composition outside of the wear track.
Fully formulated engine oils contain antiwear and extreme pressure additives, as well as detergent packages. Detergents are often added to engine oil formulations to keep oil–insoluble combustion products and wear particles in suspension. These are typically calcium compounds. Antiwear and extreme pressure additives are usually Zn, P, and S containing compounds (ZDDP). Results of this study suggest that two reactions play important roles in the wear mechanism of Ni-W coatings paired with steel: (a) the formation of a Ca-containing tribofilm at lower temperatures and (b) the formation of sulfur-containing tribofilm. The tribological and tribochemical performance of several calcium-containing detergents has been studied by Yu et al [10]. They observed the deposition of nanosized CaCO
3 as well as tribochemical reactions, which led to changes in the oxidation state of S in the corresponding tribofilms. It was also observed by others that the antiwear activity of a tungsten-containing coating was due to an ‘affinity’ of S for W in tribological contacts [11,12]. Niste at al [13] studied the tribological performance of powder metallurgy-consolidated Al composites reinforced with either fullerene- like WS
2 or 2H-WS
2 particles (particles that are built up of hexagonal unit that consist of two layers). They attributed a reduction in friction and wear at lower temperatures to the physical properties of WS
2, however at higher temperatures, the enhanced tribological behavior was connected to the chemical reaction of WS
2 with the aluminum matrix. Tribochemical reactions were also observed to occur between WC functionalized 304 steel and a W-DLC coating [14]. It was observed that the kinetics of the WS
2 tribofilm formation depended on the contact pressure, as well as the sulfur concentration. When the contact pressure was large, tribofilm formation was instantaneous, however, excessive contact pressures led to a ploughing effect. Additionally, at lower sulfur concentrations, tribofilm formation was retarded. It is noteworthy that although W-DLC is widely used as a wear-resistant coating on gears and engine components, it has been reported to unacceptably high wear rates when experiencing sliding contact in lubricants containing large amounts of S-additives [15]. One of the implications of this study is that whereas the TiO
2-doped Ni-W coating has a hardness similar to some commercial W-DLC coatings, the beneficial and synergistic interactions of the Ni-W with high S-containing lubricants improves the wear resistance of the coating/steel interface.
Conclusions
TiO
2-doped and undoped Ni-W coatings were deposited by pulsed reverse current electrodeposition and their physical properties and tribological performances in a mineral and a fully formulated engine oil were evaluated. Although the friction coefficients in lubricated, reciprocating sliding contact paired against uncoated steel surfaces were not affected by the dopant material, significant differences in the wear performance were observed. In unadditized mineral oil, the TiO
2-doped Ni-W showed significantly less wear with increasing temperature than the undoped Ni-W. In testing performed in the fully formulated engine oil, tribofilm formation on the coatings and on the steel counterfaces was observed with both coatings. The tribology of the additive-derived tribofilm was found to depend on the coating and test temperature, which suggests a temperature-controlled, tribochemical reaction occurs between the additives and the coating material as a result of the tribological contact.
Acknowledgements
The author would like to thank the STLE for honoring her with the E. Richard Booser Scholarship, and Jeremy Wagner of the John Deere Company for sponsoring portions of this research. Additionally, she is grateful for Arindam Paul for aiding in the completion of the project. She is especially indebted to Dr. Barbara Fowler for her mentoring and Prof. Gary Doll for his guidance, support, and encouragement.
References
1.
Eckels, M., M. N. Kotzalas, and G. L. Doll. "Attaining high levels of bearing performance with a nanocomposite diamond-like carbon coating." Tribology Transactions 56.3 (2013): 410-416.
2.
Mutyala, K.C., Singh, H., Fouts, J.A., Evans, R.D. and Doll, G.L., 2016. Influence of MoS 2 on the rolling contact performance of bearing steels in boundary lubrication: a different approach. Tribology Letters, 61(2), p.20.
3.
Davis, J.R. ed., 2001. Surface engineering for corrosion and wear resistance. ASM international.
4.
Zhong, Z. and Clouser, S.J., 2014. Nickel–tungsten alloy brush plating for engineering applications. Surface and Coatings Technology, 240, pp.380-386.
5.
Shreeram, D.D., 2017. Development of Wear and Corrosion Resistant Nickel Based Coatings Through Pulse Reverse Current (PRC) Electrodeposition Process (Doctoral dissertation, University of Akron).
6.
Wolfe, D. and Eden, T., 2007. Cold spray particle deposition for improved wear resistance. In The Cold Spray Materials Deposition Process (pp. 264-301).
7.
Voevodin, A.A., O'neill, J.P. and Zabinski, J.S., 1999. Nanocomposite tribological coatings for aerospace applications. Surface and Coatings Technology, 116, pp.36-45.
8.
Detor, A.J. and Schuh, C.A., 2007. Tailoring and patterning the grain size of nanocrystalline alloys. Acta Materialia, 55(1), pp.371-379.
9.
Shreeram, D.D., Bedekar, V., Li, S., Cong, H. and Doll, G.L., 2018. Corrosion-and Wear-Resistant Pulse Reverse Current (PRC)-Based Electrodeposited Ni-W Coating. JOM, 70(11), pp.2603-2610.
10.
Yu, L. G., Yamaguchi, E. S., Kasrai, M., & Bancroft, G. M. (2007). The chemical characterization of tribofilms using XANES — Interaction of nanosize calcium-containing detergents with zinc dialkyldithiophosphate. Canadian Journal of Chemistry, 85(10), 675–684.
11.
Podgornik, B., 2008. Tribological behavior of DLC films in various lubrication regimes. In Tribology of Diamond-Like Carbon Films (pp. 410-453). Springer, Boston, MA.
12.
Gustavsson, F. and Jacobson, S., 2016. Diverse mechanisms of friction induced self-organisation into a low-friction material–an overview of WS2 tribofilm formation. Tribology International, 101, pp.340-347.
13.
Niste, V.B., Ratoi, M., Tanaka, H., Xu, F., Zhu, Y. and Sugimura, J., 2017. Self-lubricating Al-WS2 composites for efficient and greener tribological parts. Scientific Reports, 7(1), p.14665.
14.
Totolin, V., Ripoll, M.R., Jech, M. and Podgornik, B., 2016. Enhanced tribological performance of tungsten carbide functionalized surfaces via in-situ formation of low-friction tribofilms. Tribology International, 94, pp.269-278.
15.
Kalin, M., Vižintin, J., Barriga, J., Vercammen, K., Van Acker, K. and Arnšek, A., 2004. The effect of doping elements and oil additives on the tribological performance of boundary-lubricated DLC/DLC contacts. Tribology Letters, 17(4), pp.679-688.