Complexity in ISFA (in-service fluid analysis): Part XLII
Jack Poley | TLT On Condition Monitoring January 2019
Where are in-service fluid analysis and non-destructive CM going?
This marks my last column for On Condition Monitoring, as it’s time to move on after nearly 100 articles over almost 15 years.
It’s been a fun run, if a bit harrowing as to print deadlines from time to time. I truly appreciated the encouraging emails I’ve received over the years, where something resonated for a reader. The idea was always to inform and spark interest and even healthy debate and discussion on occasion.
So, simply, thank you for being a great audience. I’m not retiring just yet and will stay actively involved in STLE, ISFA and asset condition monitoring (ACM), just in other ways. This last column refers to areas I will be particularly concentrating on, learning and applying knowledge gained to better advance ACM science. Best, jp.
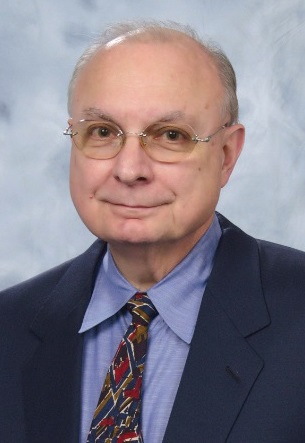
Last column I left off with the observation that artificial intelligence (AI), the Internet of Things, Industry 4.0, among other initiatives, will be at the forefront of improving and advancing ACM and management.
Since the turn of the 21st Century, and especially in the last five to 10 years, huge steps have been taken to apply technology toward solidifying and amalgamating ACM. Here are some thoughts along those lines.
Instrumentation innovation has provided numbers of breakthroughs.
•
Thanks to adaptation of XRF (X-ray fluorescence emission spectroscopy) to ISFA, multi-element LPWM (large particle wear metals, those 4µ and greater, matching up with particle counting at lowest standard detection levels) can now be applied to virtually all common ISFA metals, e.g., the Big 4 wear metals: iron, aluminum, copper, lead and tin, chromium, nickel, titanium, silver, zinc, molybdenum and vanadium. The element list includes silicon for pre-abrasive monitoring, i.e., the ability to spot likely pre-lube-charge contamination from poor lube handling practices. Normally one finds that out the hard way by seeing the wear effects of ground up large (>4µ) silicon-based abrasives. Some of this effect can be intercepted by earlier detection, then fully mitigated. Catastrophic failure avoided.
LPWM, along with fundamental ISFA tests like VIS, IR (multi-testing) and particle count, is currently under evaluation in field-portable labs by the U.S. military with positive feedback to date. LPWM closes the detection gap where normal AES (atomic emission spectroscopy, used for fluid analysis wear metals for the preponderance of existing laboratories), falls short at particle sizes as low as 4µ or even less, dependent on the metal and how it might be alloyed. LPWM is especially good at spotting near-term failure modes in time to potentially render them to a non-event, not just with prewarning of abrasives but of wear itself when abrasives might not be the root cause (
see Figure 1).
Figure 1. FL58 field-transportable multi-test lab. (Figure courtesy of Spectro Scientific, Inc.)
•
Nearly all traditional/
de facto in-service lubricant tests have been adapted and sufficiently miniaturized with low footprint such that onsite laboratories are increasingly viable, essentially bringing comprehensive testing to the machine at brick-and-mortar lab quality.
While not as instantaneous as information provided by online sensors, such as VIB and ultrasonics provide, onsite ISFA testing can quickly assist in vetting a sensor alarm in a matter of minutes, or at least a couple of hours, dependent on installation logistics, rather than days when offsite labs are involved. Onsite analysis installations are likely to accelerate, providing a major, comfortable bridge to the possibility of all-sensor ACM, the real-time Holy Grail of ACM. The future looks highly encouraging.
There is a subtle but powerful bonus in onsite labs: asset maintainers, possessing the greatest knowledge of machinery in the plant (or vessel or fleet), will add value to the advisory (evaluation and report commentary) in a more connected sense than an offsite lab can, since they will be in position to do so as primary evaluators. More insights and revelations will be an inherent part of the onsite process.
And if this theory holds, perhaps the ISFA industry, as a whole, will enjoy a second bonus, the gift of real feedback for as-found machine inspection scenarios for wear and other trauma. As things stand today, feedback at offsite labs is miserable (from direct experience, I estimate no better than 15% of situations where it would have likely been invaluable), and not all that accurate or complete either, although better than nothing, I suppose. Still, that seems like a weak accomplishment in a world where maintenance precision is increasing thanks to intelligent technology application. Feedback will soon become a relentless pursuit.
Intelligent agents (IAs) applications will expand.
This will occur as laboratories and end-user entities apply advanced AI to ISFA. Actually, ISFA has already been involved in appropriating these tools for nearly 40 years, circa 1979, when Lubricon, a commercial ISFA laboratory, created software for data evaluation and advisories, based on pattern recognition, the core of AI.
We didn’t have the more complex subroutines (machine learning, both supervised and unsupervised) now available that can crunch data in a variety of ways at warp speed, ferreting out data patterns we might never have noticed. But we had the logic at full capacity for the situations we did know about, and that proved sufficient for more than 98%-99% of samples received from seemingly every type of application. Why not shoot for 100%?
AI now can be applied to searching for and vetting more esoteric combinations of data, crossing into other ACM disciplines to find data correlation. Oh, and, yes, feedback will happen because those of us informing IAs as domain experts will finally force the issue, once and for all, with AI surely involved.
Many of you know I consider the employment of ACM to be a matter of money, conservation thereof (well, don’t we all). The idea of money conservation is to not leave it on the table, but pocket it to ROI gain. Once the IA is a common tool in ACM, feedback will be the last impediment in the ACM data collection milieu. Vetted feedback is the only way to achieve legitimate verification of ROI. Then, we can sit back and wait for sensors to make their inevitable ascension as primary machinery maintenance sentinels.
More than a decade ago, I presented a diagram (
see Figure 2) that suggested a software concept and data flow that would seek to synergistically blend/amalgamate any and all available ACM data. I am surer than ever that this crude graphic is a reasonable model and portent of things to come in ISFA, indeed, all ACM, and I’m excited about continuing to be actively involved in contributing to its potential realization.
Figure 2. A holistic, integrated ACM model.
And where are ISFA and ACM going? Directly to the machine.