King Industries, Inc.
NA-SUL® 450 & KX455 Water-Based Rust Preventives Provide a Useful Tool to Reduce VOC
By Bill Kingston, Technical Marketing Manager - Rust Preventives, King Industries, Inc. | TLT CMF Plus November 2018
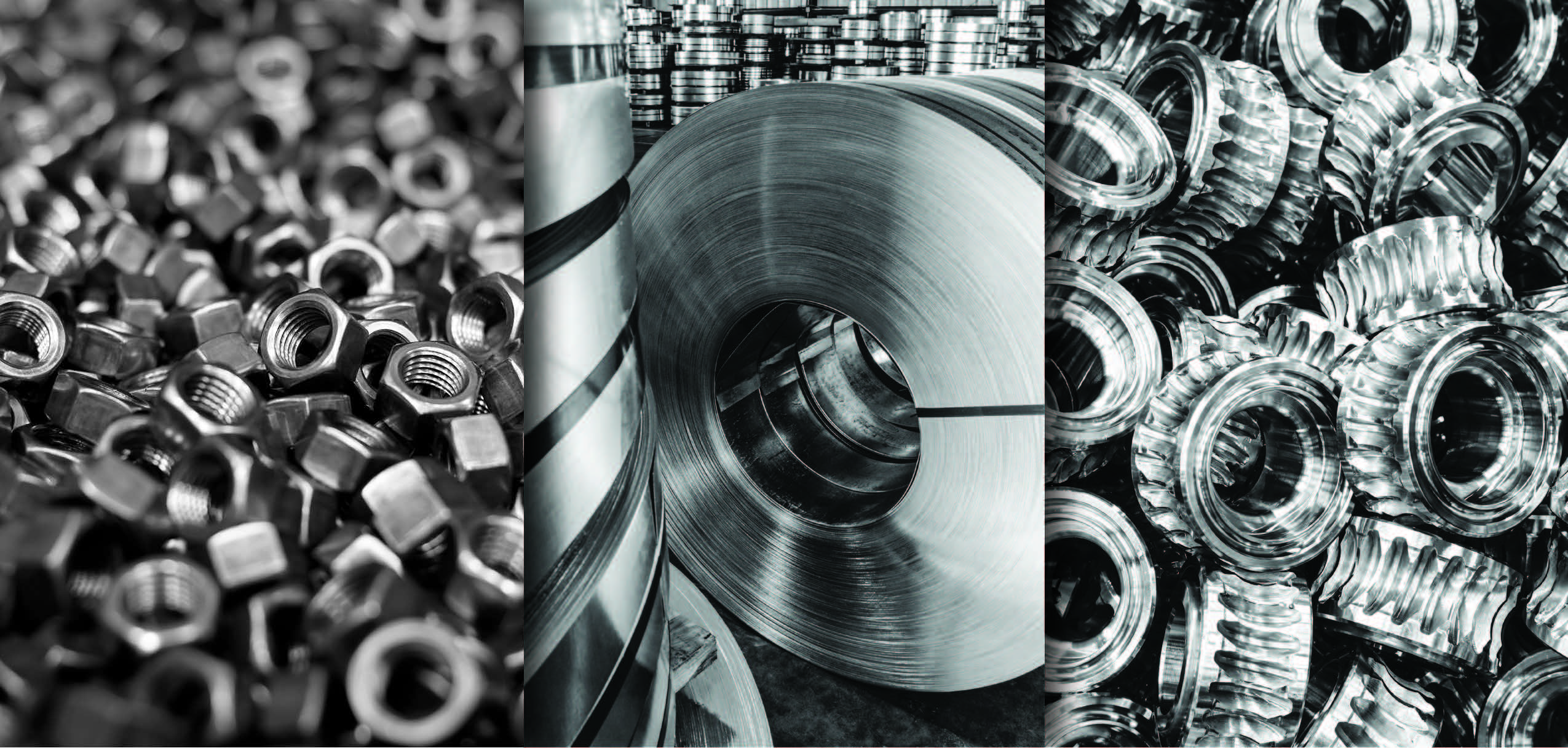
Corrosion is a serious problem resulting in billions of dollars of damage per year. In addition to permanent coatings such as paints, temporary corrosion preventives provide an important tool for prevention of rust on metal parts and surfaces during transportation and storage. Many traditional high performance temporary rust preventive formulations use a combination of oil and petroleum derived solvents as carriers for corrosion preventive additives. These solvents are usually 30% to 95% of the entire formulation. Upon evaporation, these solvents can react with sunlight to form ground level ozone. While this is a minor source of ozone pollution compared to fuel evaporation, the smog problem is so serious in various parts of the world that this source is now coming under regulatory control. Using water in place of petroleum derived solvents is a very effective way to meet even the most stringent Volatile Organic Compound (VOC) requirements.
Until recently, water-based rust preventive formulations could not match the performance of oil/solvent rust preventive formulations, particularly in harsh conditions. NA-SUL®450 and KX455 are two new additives from King Industries designed to give corrosion protection from a thin film, removable coating that is as good or better than protection available from formulations based on petroleum derived solvents. Both additives are effective on steel, aluminum and galvanized steel.
NA-SUL® 450
NA-SUL® 450 is designed to be added to water to provide long term protection in high humidity environments. NA-SUL® 450 emulsions typically use 1% to 5% NA-SUL® 450 in local city water and have very good stability. Films from emulsions made from <3% NA-SUL® 450 are dry to the touch and are removable with detergent cleaning. In addition to excellent results in Humidity Cabinet testing (ASTM D1748), NA-SUL® 450 passes Iron Chip rust preventive testing (ASTM D4627) at 0.5% treat level.
ASTM D1748 Humidity Cabinet testing is a 100% humidity environment at a temperature of about 49°C. Specified test panels are coated with the test formulation and suspended from a rotating carousel after drying. (
Figure 1) The failure criteria are specified in the ASTM D1748 method.
Figure 1. Humidity Cabinet (ASTM D1748)
Humidity Cabinet (ASTM D1748) Results on Steel:
The following results were obtained for NA-SUL® 450 on 1010 cold rolled steel test panels run in duplicate.
2% NA-SUL® 450 in 98% City Water (Norwalk, CT, 50 ppm to 64 ppm as CaCO
3):
There was no rust at 440 hours exposure. (
Figure 2) The first rust spot appeared at 630 hours exposure. (
Figure 3)
Figure 2. 2% NA-SUL 450 on Steel (Humidity Cabinet, 440 hrs.)
Figure 3. 2% NA-SUL 450 on Steel (Humidity Cabinet, 630 hrs.)
5% NA-SUL® 450 in 95% City Water:
The first rust spot appeared at 630 hours exposure. (
Figure 4) The 2nd panel had no rust for more than 1400 hours. (
Figure 5)
Figure 4. 5% NA-SUL 450 on Steel (Humidity Cabinet, 630 hrs.)
Figure 5. 5% NA-SUL 450 on Steel (Humidity Cabinet, 1464 hrs.)
Humidity Cabinet (ASTM D1748) Results on Aluminum:
The following results were obtained for NA-SUL® 450 on aluminum test panels run in duplicate.
5% NA-SUL® 450 in 95% City Water:
There was no corrosion at 1272 hours exposure. (
Figure 6) The panels failed at about 1450 hours exposure. (
Figure 7)
Figure 6. 5% NA-SUL 450 on Aluminum (Humidity Cabinet, 1272 hrs.)
Figure 7. 5% NA-SUL 450 on Aluminum (Humidity Cabinet, 1464 hrs.)
KX455
KX455 is specifically designed to be added to mineral oil and then emulsified using local city water. KX455 emulsions have good stability but may need some occasional mild stirring to restore emulsion homogeneity. KX455 is tolerant of hard water that might be typically encountered. The resulting emulsions give exceptional salt fog (ASTM B117) protection as well as excellent acid atmosphere protection. The performance is comparable with the best oil/solvent formulations.
ASTM B117 Salt Fog testing is a “practice” and not a method. (
Figure 8) Only the internal conditions of the chamber are specified. The conditions are:
•
Collection Rate: 1ml – 2ml per hour (salt solution)
•
pH: 6.5 – 7.2, collected salt solution
•
Temperature: 35°C
Figure 8. Salt Fog (ASTM B117)
King Industries defines failure as rust extending more than 1.5 cm from the top edge or more than 0.5 cm from either side edge of the test panels.
The test panels used were:
•
1010 cold rolled steel with one test panel surface polished and the 2nd test panel surface matte finish
•
Aluminum 2024 alloy duplicate panels
•
Hot dip galvanized coated steel duplicate panels
The formulations tested were:
•
KX455 formulation (water-based)
•
Commercial formulation A (oil/solvent based)
•
Commercial formulation B (oil/solvent based)
Salt Fog (ASTM B117) Results on Steel:
At 26 hours formulation B has failed. (
Figure 9) At 72 hours exposure both formulations A and B have failed. (
Figure 10) At 192 hours the KX455 matte surface panel shows first rust. (
Figure 11) Using 15% KX455 test panels went almost 500 hours before any rusting. (
Figure 12)
Figure 9. 10% KX455 vs SB Formulations on Steel (Salt Fog, 26 hrs.)
Figure 10. 10% KX455 vs SB Formulations on Steel (Salt Fog, 72 hrs.)
Figure 11. 10% KX455 vs SB Formulations on Steel (Salt Fog, 192 hrs.)
Figure 12. 15% KX455 (Salt Fog, 480 hrs.)
Salt Fog (ASTM B117) Results on Aluminum:
At 118 hours formulations A and B have failed. KX455 shows no corrosion. (
Figure 13)
Figure 13. 10% KX455 vs SB Formulations on Aluminum (Salt Fog, 54 hrs.)
Salt Fog (ASTM B117) Results on Galvanized Steel:
At 48 hours exposure both formulations A and B have failed badly. The KX455 protected panels are showing the first sign of corrosion. (
Figure 14)
Figure 14. 10% KX455 vs SB Formulations on Galv. Steel (Salt Fog, 48 hrs.)
Humidity Cabinet (ASTM D1748) Results on Cast Iron:
In addition to protecting steel, aluminum and galvanized steel, KX455 has been found to provide remarkable protection for cast iron in 100% humidity. Cast iron is particularly difficult to protect from rusting due to its comparatively porous structure. A formulation of 10% KX455 with 10% Group I, ISO VG 32 oil and 80% tap water gave over 700 hours of rust protection in 100% humidity. (
Figure 15)
Figure 15. 10% KX455 on Cast Iron (Salt Fog, 720 hrs.)
Practical Considerations
Advantages and disadvantages of water-based formulations
Water-Based Formulations (Advantages):
•
Very low VOC emissions contribute little to air pollution
•
Formulations are not flammable (Improved Plant Safety)
•
Solvent vapors are greatly reduced (Worker Safety)
Water-Based Formulations (Disadvantages):
•
Slower drying than solvent formulations
•
Parts must be dry before packaging or stacking
•
Fluid must be treated before disposal (Not Burned)
•
Formulations are more complex; biocides may be required
One of the major disadvantages of water-based rust preventives is the additional drying time compared with solvent-based rust preventives. Before stacking or packaging parts coated with water-based rust preventives, the coating must be completely dried. Any residual water will result in considerable rusting.
To determine if the heating of parts coated with KX455 formulations was practical, we heated coated test panels to 90°C and measured the effectiveness of the coating. The panels dried very quickly but were left in the oven at 90°C for 1.5 hours to see if the coating would deteriorate over time from heating. The heated test panels were tested in the salt fog cabinet and achieved rust protection approaching 200 hours as was the case for unheated panels.
We have found that salt fog protection was equivalent for test panels dipped in a KX455 emulsion formulation whether the panels were wet or dry when dipped. This opens up the possibility for using KX455 emulsions to replace solvent formulations for dewatering applications. Dewatering has traditionally used formulations with a very high solvent content. Machined parts are often cleaned with detergent based cleaners and then water rinsed before further processing. These wet parts are dipped in solvent-based dewatering formulations where the formulation is expected to displace water and provide a rust preventive coating. Here again, KX455 emulsions can be used to replace petroleum solvents.
Coating parts as well as dewatering will tend to reduce the concentration of KX455 with usage. This will require tank side monitoring of the concentration of KX455. One way that this can be done is by adapting a Hyamine titration that is specific for sulfonates. Known concentrations of KX455 are prepared that bracket the desired concentration of KX455 in the tank that is being used. Titrant is added dropwise to the known concentrations of KX455 with indicator solutions until the endpoint color change occurs. The number of drops until color change for the known concentrations is recorded. The sample from the tank is then titrated dropwise until the endpoint color change is reached. The concentration of KX455 is then determined by interpolation.
In typical dip tank applications, a biocide will be needed to prevent bacterial and fungal degradation of KX455 emulsions. Mergal® K12N, available worldwide from Troy Corporation, was found to be very effective at a 0.1% treat level.
Conclusions
•
The use of water-based rust and corrosion inhibitors is a very useful way of reducing solvent evaporation that results in ground level ozone air pollution.
•
New NA-SUL® 450 and KX455 from King Industries are highly effective for protection of steel, aluminum and galvanized steel and cast iron.
•
NA-SUL® 450 provides superior corrosion protection in high humidity environments.
•
KX455 is superior to most commercial rust and corrosion preventive additives designed for oil/solvent systems as measured by salt fog testing.
•
Both NA-SUL® 450 and KX455 are excellent alternatives to additives designed for oil/solvent formulations giving exceptional performance with a significant reduction in pollution caused by VOC evaporation.