Antioxidants: The challenge for additive manufacturers
Dr. Robert M. Gresham, Contributing Editor | TLT Lubrication Fundamentals August 2018
Formulators are tasked with reducing oxidation with fewer choices in their chemical toolbox.
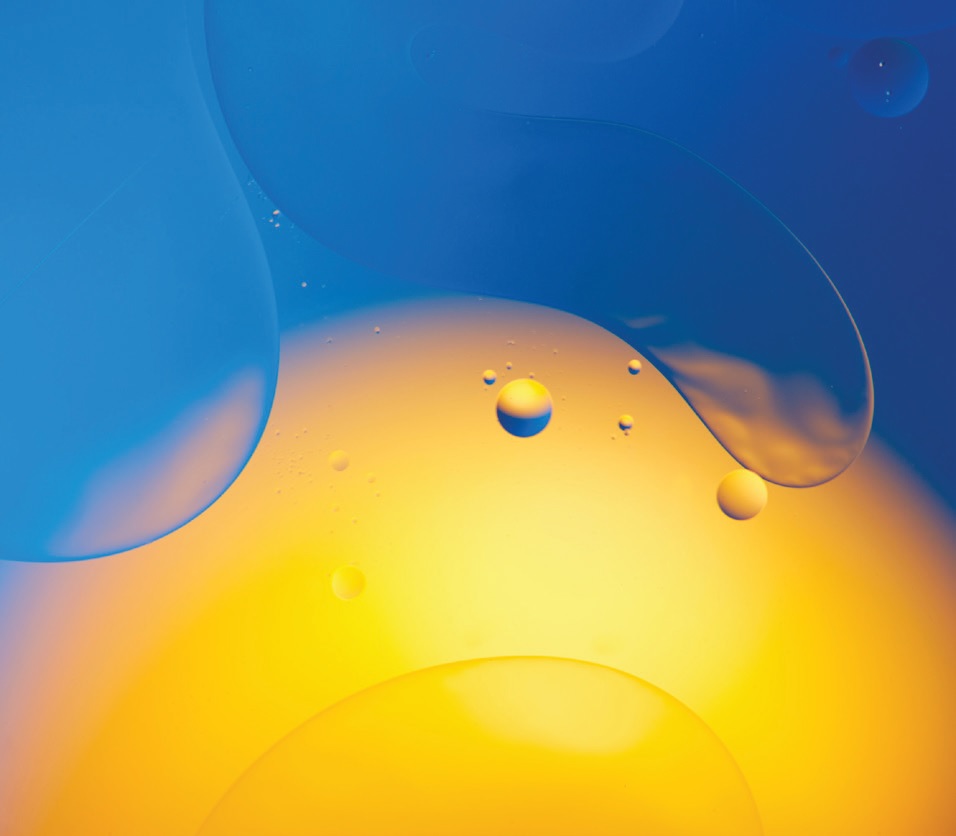
© Can Stock Photo / alekseyrezin
Last month we talked about trends in industrial lubricants, referencing the 2017 STLE Emerging Trends Report (available free on www.stle.org). We concluded that we will see continued emphasis on protecting the environment and reducing waste (which also can impact the environment, as well as cost), increased use of more highly refined base oils and synthetics—that will inherently be more oxidation and temperature stable—and improved formulation-compatible additives delivering their various performance properties to the formulation. Especially, we will need better, longer-lasting oxidation inhibitors. So it might be useful to look into what’s going on in oxidation-resistant additives.
Today, nearly all lubricant formulations contain some kind of antioxidant in some concentration. This is because oxidation is the primary cause of oil degradation. Thus, improving oxidation resistance is critical to improving lubricant stability and the operational life of the lubricant, in turn allowing for extended oil drain intervals. Extending drain intervals saves direct maintenance costs, reduces waste treatment costs and potential exposure to the environment and reduces overall cost and consumption from well head to the waste treatment plant. Further, design engineers are designing machines with smaller sumps and reservoirs, lube-for-life bearings and closer tolerances. All of which means that less lubricant, often at lower viscosities, must run longer and hotter, and often must run under higher loads and speeds, all at thinner film thicknesses. The totality of which definitely leads to conditions that promote oxidation of the lubricant.
Lubricant (hydrocarbon) oxidation is promoted by heat and exposure to oxygen. Oxidation is further accelerated by catalysis from metals such as copper iron and nickel—often the very machine materials themselves. Of these various machines, in-service internal combustion engines represent the most numerous and hostile of environments. Many of the industrial applications can be equally challenging.
To meet these challenges, we find growing use of more and more highly refined base oils, such as Group III+, PAOs and a variety of application-specific synthetic base oils, all of which have inherently better oxidation stability. So-called bio-base oils, which inherently have poorer oxidation resistance, are being more highly refined or genetically modified to improve their oxidation resistance. These oils can be used singly or in synergetic blends to maximize their oxidation resistance as well as other needed operating properties. Regardless, they all need improved antioxidant additives. There are at least 11 different classes of chemistries that have been used over the years as antioxidants. They tend to fall into two fundamental types: organometallic and oil-soluble organic antioxidants. However, in the future these new additives must be system compatible and easier on the environment by compliance with recent regulations limiting the amounts of such materials as sulfur, phosphorous and various metal containing additives to reduce SO2, NO2 and soot emissions. These regulations also limit the amounts of sulfated ash, phosphorous and sulfur (SAPS). Thus, there is the trend to develop ashless antioxidant additives not containing sulfur or phosphorus, at least for engine oil lubricants.
The oxidation process of hydrocarbons is reasonably well known. It is a free radical process of four fundamental steps: chain initiation, chain propagation, chain branching and termination.
In chain initiation, through heat, oxygen, UV light or mechanical shear stress, and catalyzed by heavy metals, hydrocarbon carbon-carbon or carbon-hydrogen bonds can be cleaved, resulting in a free alkyl radical (R∙). This free radical, which is highly reactive with almost anything, usually oxygen, rapidly forms an alkyl peroxyl radical (ROO∙). This free radical can readily abstract a hydrogen atom from a hydrocarbon. Thus, these free radicals rapidly create a large number of hydroperoxides—no good. With chain branching, these hydroperoxides can in turn cleave into alkoxy radicals (RO∙) and hydroxyl radicals (HO∙). This process is often accelerated by metal ions. These bad boys, in addition to producing more alkyl-free radicals, also can create aldehydes and ketones. These species all lead rapidly to the negative properties characterized as the result of oil oxidation: sludge formation, varnish deposits, increase in viscosity, etc. When two alkyl-free radicals react with each other, known as chain termination, the resultant is a higher molecular weight hydrocarbon, which increases viscosity.
Thus, there are two fundamental approaches used to inhibit these oxidation reactions: trapping of catalytic metal impurities and destruction of the alkyl, alkyl peroxyl and hydroperoxide-free radicals themselves. So-called metal deactivators come in two types: chelators and passivators. Chelators capture the catalytic metals by reacting with the metal to form less reactive species. Passivators act by attaching to the metal surface to form a protective layer. Free radical scavengers, known as primary antioxidants, capture the alkoxy and alkylperoxide-free radicals by donating a hydrogen atom terminating the process. Secondary antioxidants, peroxide decomposers, reduce the alkyl hydroperoxides in the radical chain to relatively nonreactive alcohols. One new approach is to develop time-delay antioxidants to further extend the lubricant’s useful life. It seems clear that rather than find the “Magic Bullet,” formulators will improve the individual performance of the various types: chelates, primary and secondary and develop synergistic blends for each application, which also could include time-release additives as well as oxides to less harmful alcohols. Thus, speed of reaction time is key. These inhibitors must react faster with the free radicals than the free radicals can react with other hydrocarbon molecules.
Clearly this is pretty complicated chemistry. Regulation removes many arrows from the quiver of the chemist’s chemical arsenal. Yet the demands, as noted, are ever increasing. One new approach is to develop time-delay antioxidants to further extend the lubricant’s useful life. Thus, it seems clear that additive suppliers will be working to improve the different antioxidants types: chelates, primary and secondary antioxidants and then develop synergistic blends of these, perhaps with time-release chemistries as well, to develop a pretty customized package to fit the application and base oil composition.
I can only say good luck to the additive companies working on solutions to these challenges of the future.
Bob Gresham is STLE’s director of professional development. You can reach him at rgresham@stle.org.