Short-term formulation trends
Dr. Robert M. Gresham, Contributing Editor | TLT Lubrication Fundamentals July 2018
A look at the factors driving change for five critically important industrial lubricants.
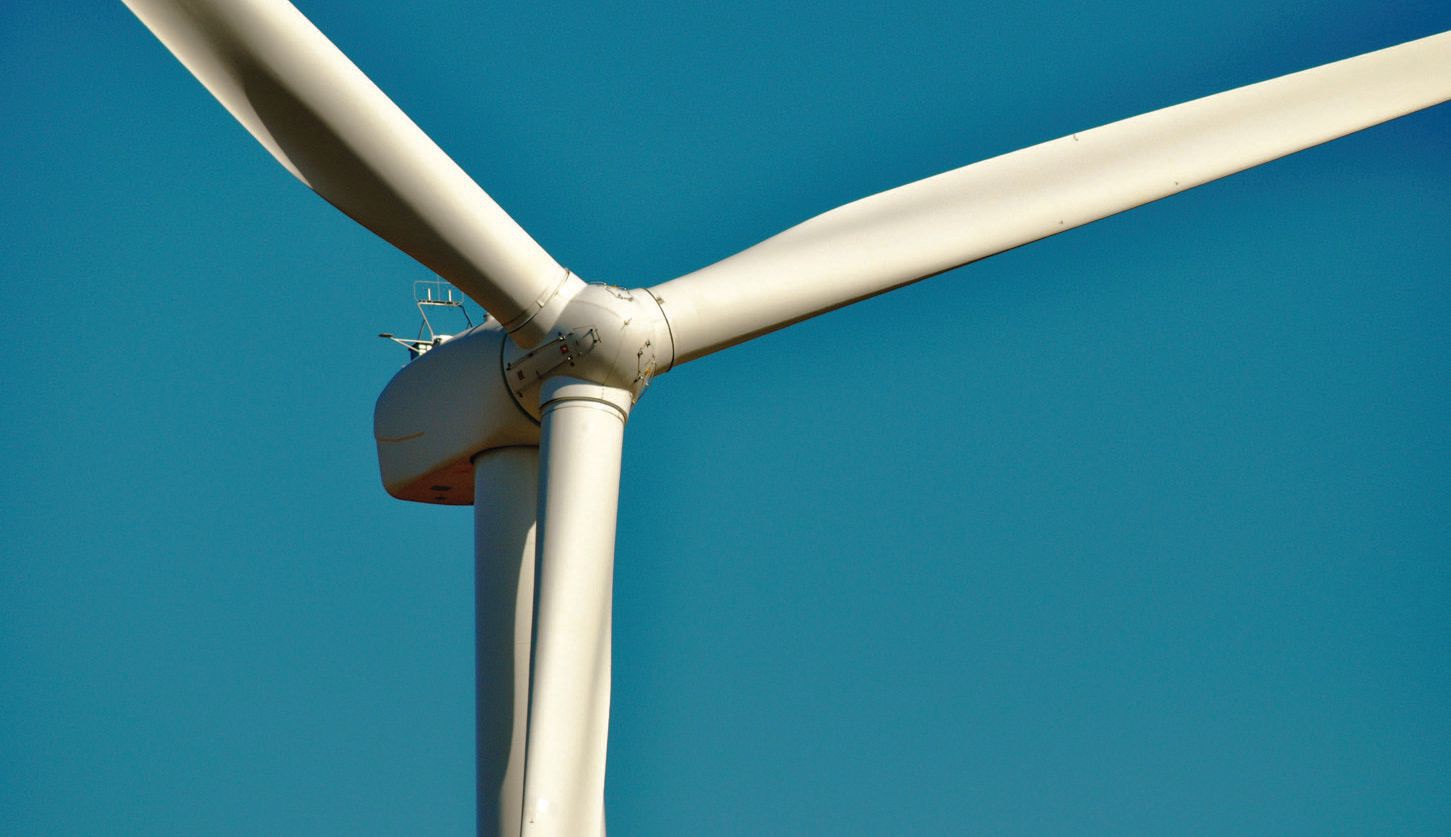
© Can Stock Photo / refocusphoto
To prepare for the recent STLE annual meeting, I re-read parts of the society's 2017 Emerging Trends Report (free at www.stle.org). The report, an update of the 2014 edition, examines the forces impacting a number of industries (transportation in particular) and provides research on technical aspects of society in the U.S., Europe, South America and Asia. Most of these trends are long term and didn't, to my eye, address some of the more practical, short-term changes that would result, especially in industrial lubricants.
So let's take a look. The key lubricants studied in the report are gear oils, hydraulic oils, turbine oils, compressor oils and greases.
Gear oils
Starting with gear oils, we find such applications as hoists, mobile equipment, grinders, rock drills, mixers, etc., and applications where the goal is speed reduction or increase. The current ten-ton gorilla in the room, more or less literally, is wind turbines. Gears used in these various applications vary considerably in size, design and material of construction. All involve some combination of relative rolling and sliding contact, with worm gears having almost exclusive sliding contact.
Gear oils used in these applications often have highly varied requirements to fulfill. At the same time, the formulator's arsenal, for environmental reasons, has lost such materials as lead compounds and chlorinated solvents. Today's gear boxes are designed to reduce weight and improve efficiency, resulting in higher gear speeds, loads and temperatures.
Further, as we have found with wind turbines, the primary failure mode in gears is caused by micropitting. This is a process we're still trying to explain, but it seems related in part to surface engineering and finish. The upshot is that trends for gear oils will involve the further development of the following properties:
• Improved oxidation resistance
• Improved high-temperature EP performance
• Improved thermal stability
• Improved surface fatigue resistance
• Extended demulsibility
• Lower friction.
• Improved foam control.
Clearly, one of the key properties is related degradation due to temperature, which is usually an oxidative process.
Hydraulic fluids
There are three main types of hydraulic pumps: vane, gear and piston. Vane pumps tend to run at the highest pressures and require the highest wear protection.
To service these machines, hydraulic fluids must:
• Transmit power
• Protect and lubricate system components
• Remove heat through circulation
• Protect the system from oxidation and corrosion
• Provide wear protection
• Provide appropriate viscosity and compressibility
• Exhibit hydrolytic stability
• Exhibit filterability
• Show system compatibility
• Show good demulsibility or emulsibiliy for the system.
Environmental concerns will remain a key market force for hydraulic fluids, as many applications are in locations and environments where leaks or ruptured hoses can result in a significant spill. Thus, additive companies and formulators will remain pressured to create biodegradable fluids with nontoxic additive chemistries and chemistries that do not bioaccumulate.
The next trend is reducing the costs of fluid systems (by making the equipment smaller to reduce the risk of large-quantity oil spills) and waste disposal. There also is a simultaneous desire to extend oil-change cycles. This necessitates systems that operate at higher temperatures (since reservoirs are smaller and less able to cool the fluid). Extended use at higher temperatures, in turn, necessitates fluids with better oxidation resistance.
To deal with these factors, formulators will need to evolve base oil use from Group II to Group III to III+ to use of PAOs. Additives will have to be compatible with these more highly refined oils and higher temperature, and antioxidants will need improvement.
Compressor oils
Oils used in high-pressure compressors require lubricants stable at high temperatures for extended times. Further, since discharge temperatures can be as high as 500 F, these oils must not tend to form deposits at hot spots in the valves. Oils for such applications are usually formulated from diesters and polyol esters. Rotary vane compressors require oils that reduce wear and vane-sticking problems. The gas being compressed will affect the oil chemistry, as well.
As the future unfolds, mineral- based oils still will be used in normal, non-critical applications where the gases are nonreactive. Diesters, polyol esters and PAOs will be used for more demanding applications. Once again, the need for greater oxidation stability is critical and necessitates the use of synthetics, Group III mineral oils and enhanced oxidation-resistant additives.
Turbine oils
Oils for steam and gas turbines must provide bearing and gear lubrication, remove heat through circulation systems, be stable to oxidation, resist sludge and deposit formation, resist foaming and allow for separation of water contamination, and function as a hydraulic fluid for system controls.
As we look to the future, turbine oils are inherently kinder to the environment as their additives are metal free. Future turbine oils will need ever-more oxidation resistance and reduced tendency to form sludge and deposits. Thus, more use of Group III and PAO-based oils will continue with better oxidation resistant additives.
Greases
They vary considerably in terms of applications and composition, so generalizations are a little tricky. However, since many greases are used in non-restricted open systems, environmental contamination has been and will continue to be a major concern. Related to this is reduction of waste-disposal costs.
Future formulations will not have additives with heavy metals, metal powders used in thread compounds and certain solid-lubricant additives. Another trend is the increased use of sealed, so-called lube-for-life bearings, which reduce the environmental contamination potential and maintenance costs associated with re-greasing. Grease makers will use more and more Group III oils and PAOs, increase their use of polyuria thickeners and, of course, formulate compatible oxidation inhibitors.
As we look at future trends in industrial lubricants, we'll see continued emphasis on:
• Protecting the environment
• Reducing waste
• Increasing the use of more highly refined base oils and synthetics that themselves will be more oxidation and temperature stable
• Creating compatible additives that deliver their various performance properties to the formulation. We'll especially need better, longer-lasting oxidation inhibitors.
Now we have an idea of what to expect in lubricant formulations based on STLE's Emerging Trends Report. A trend that really bears further analysis is what's new in oxidation resistant-additives, perhaps the subject of a future article.
Bob Gresham is STLE’s director of professional development. You can reach him at rgresham@stle.org.