20 Minutes With Robin Olson
Rachel Fowler, Managing Editor | TLT 20 Minutes June 2018
This Rexnord executive works with experts on the American Gear Manufacturers Association to develop methods to predict the effect of gear lubrication on life.
Robin Olson - The Quick File
Robin Olson is chair of the American Gear Manufacturers Association’s AGMA 925 Subcommittee of the AGMA Helical Gear Rating Committee. She has served on various AGMA technical committees since 1995. Robin also acts as a U.S. delegate to ISO Working Group 6 (Gear Calculations) and is director of applications engineering in the Material Handling Vertical at Rexnord Industries where her team is responsible for the engineering and design of modified and customized gear drives for quotes and orders.
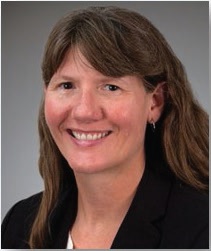
Robin Olson
TLT: What is AGMA 925?
Olson: AGMA 925 is an AGMA information sheet that covers the Effect of Lubrication on Gear Surface Distress. That’s a big topic! There are a wide variety of lubricants available to the gear engineer, and the way they respond to the sliding and rolling contacts in a gear mesh makes the difference between healthy operation, marginal operation and no operation.
Specifically the document discusses gear lubricants, their viscometric behavior and film thickness considerations. It presents methods that can be used to calculate the risk of scuffing, calculate the impact of regimes of lubrication on macropitting and predict wear between gear teeth.
AGMA 925 discusses micropitting but doesn’t contain any methods that can be used to determine when micropitting between two gear teeth will start. The AGMA Helical Gear Rating Committee identified that this is an area of improvement for the document. In 2015 the committee started a subcommittee to review the document and develop a way to calculate micropitting risk. This project is well underway in the committee.
AGMA 925 is an information sheet, not an AGMA standard. As an information sheet, it serves as a general guideline and source of information about lubricants, their properties and their general tribological behavior in gear contacts. It was introduced as an aid to the gear manufacturing and user community and relies on the accumulation of feedback data for future enhancements and improvements. It is not meant to be used as criteria for contract acceptance. The document was last revised in 2003.
TLT: What is the role of AGMA 925 in designing a gear and setting an application envelope?
Olson: AGMA 925 is a companion document to the general rating standard, AGMA 2101-D04 (
Fundamental Rating Factors and Calculation Methods for Involute Spur and Helical Gear Teeth) and its application standards. After a gear design is completed and the mechanical ratings are known, AGMA 925 can be used to determine whether the combination of loads, geometry lubricant and application conditions affects the gear teeth in operation. Many of the users of the document refer to it when they suspect that scuffing or wear may be influential in the life of the gearing.
If the methods predict that there will be a problem with tooth surface distress, then the gear engineer must decide what to change to avoid the damage. This could be a change to the lubricant, a recommendation for application changes or a modification of the gear tooth geometry. This may require recalculation of mechanical capacity.
TLT: What role does lubricant selection have on gear application and life?
Olson: Lubricants create a film thickness that separates the gear tooth surfaces as they pass through mesh. Within a gear drive, it also prevents roller bearing surfaces from coming in contact and evacuates the heat that is generated within the bearing. The basic mechanical ratings for gear tooth strength and durability and bearing L10 life assume that the proper film thickness is maintained.
The lubricant also is influenced by the application. Hot temperatures cause the oil viscosity to drop and decrease film thickness. Cold temperatures cause the oil viscosity to become so thick that it doesn’t flow properly. Water and contaminant ingress also decrease the effectiveness of the oil. Lubricants are formulated with either mineral or synthetic base stocks as well as additive packages to adjust the way that they react to the various application conditions.
Lastly, the viscosity of the lubricant and the lubricant fill level influence the amount of heat that is generated by the gearing as it passes through an oil bath within a gear drive. Thick oil is good for separating tooth surfaces and also for generating extra heat through churning.
Given all of that, lubricant selection is a critical factor in the successful performance of a gear drive in application. An incorrect selection can quickly lead to damage in the gear teeth or bearings or overheating in operation. When selecting the lubricant, it’s best to follow the recommendations of the gear drive supplier for lubricant type, viscosity and quantity. Preventive maintenance checks should be set up to regularly test the oil for oxidation. Ideally this would be done through onboard monitoring of the oil as we’ve seen in the new IIoT offerings for gear drives. If regular testing and monitoring is not possible, plan to regularly change the oil. This will ensure that the gear drive has the best chance for a long life.
TLT: Do you see advancements in the lubrication and gear fields that will get worked into an update of the standard?
Olson: Two main advancements are in the development of lubricants and surface finish techniques.
In lubricants, synthetic base stocks with additive packages that enhance performance or accommodate severe operating conditions have become increasingly available. They typically have flatter viscosity indices, which means that they retain viscosity over a wider variety of temperatures than a mineral oil will. This results in less oil changes and longer lubricant life. Each type of synthetic lubricant has unique properties and all have limitations such as compatibility with other lubricants, seals, backstops, paints, filters and plastics.
The use of failure load stage to classify the scuffing or micropitting resistance of a lubricant also is becoming a familiar parameter in lubricant specifications. This value indicates how well the lubricant performed on an FZG test rig per an ISO- or FVA-specified test. It doesn’t necessarily include the performance of a specific gear set in a particular application, but it does provide a relative comparison for performance between lubricants.
The update of AGMA 925 will contain new sections to cover lubrication, elastohydrodynamic lubrication (EHL) regions in the zone of contact, FZG testing and selection of lubricants to avoid micropitting. This is great reference material!
The AGMA 925 committee also is reviewing advancements in the measurements of tooth flank roughness. When the original testing for scuffing and wear was completed back in the 1950s and 1960s, surface finish measurements were fairly basic and depended on the measuring tool and the filters that were applied. Today the measuring tools can work in several different measurement methods with varying filter levels. It’s important that the measurements are taken in the correct direction along the tooth surface. In addition, we are reviewing the inclusion of waviness in the roughness measurement to determine when asperity contacts are significant in the life of the gear set. The AGMA 925 update will contain definitions of the various roughness methods as well as discussion of how to use filters in measurement and dimension and tolerancing symbols on drawings.
TLT: What changes do you anticipate pursuing in relation to the standard?
Olson: The primary reason for opening a project with AGMA 925 is to add a calculation method for the risk of micropitting. Micropitting has been mentioned in the document for some time but with only a description of its appearance and no method to predict it. With the development of ISO 15144-1 (
Calculation of Micropitting Load Capacity of Cylindrical Spur and Helical Gears), specification societies and end-users have expressed an interest in predicting the onset of micropitting. Unlike ISO 15144-1, which is based on film thickness limits, AGMA is working to develop a method based on asperity fatigue limits.
The AGMA 925 committee also is adding sections to the document that clarify and explain the aspects of EHL, FZG testing, surface roughness specification and measurements and lubricant selection. Our goal is to create a document containing:
•
General methods that can be used to predict surface distress
•
Helpful information about the influences on surface distress.
TLT: What is the difference between micropitting and scuffing?
Olson: Micropitting and scuffing are two different damage modes on gear tooth flanks. Micropitting is a Hertzian fatigue mode in which asperities on the surface of the tooth deform under cyclic Hertzian stresses and experience plastic flow. After a period of incubation, micropits begin to form. The region of micropitting appears dull, etched or stained with patches of grey. Micropitting can continue to grow, jeopardizing the tooth surface and leading to macropitting. It also can arrest as the asperities flatten out and stop contacting each other. Micropitting typically develops in the region of highest negative sliding along the line of action between the pinion and gear (
see Figure 1).
Figure 1. Micropitting on misaligned carburized gear. (Figure courtesy of American Gear Manufacturers Association - ANSI/AGMA 1010-F14, Appearance of Gear Teeth - Terminology of Wear and Failure.)
Scuffing is a much more severe adhesion that is not a fatigue mode. It occurs when tooth surfaces come in contact, causing transfer of metal from one surface to the other. Typically this is caused by frictional heating due to high sliding velocity and surface pressure. Scuffed areas of the tooth have a rough texture and will appear as bands oriented in the direction of sliding. Because scuffing is not a fatigue phenomenon, the damage from scuffing appears quickly in the life of the gearing and typically progresses to failure (
see Figure 2).
Figure 2. Mild scuffing. (Figure courtesy of American Gear Manufacturers Association - ANSI/AGMA 1010-F14, Appearance of Gear Teeth - Terminology of Wear and Failure.)
You can reach Robin Olson at Robin.Olson@rexnord.com.