Lubricating grease designed for rolling element bearings
Dr. Nancy McGuire, Contributing Editor | TLT Webinars March 2018
This case study provides a lesson on formulating a lubricant for a specific application.
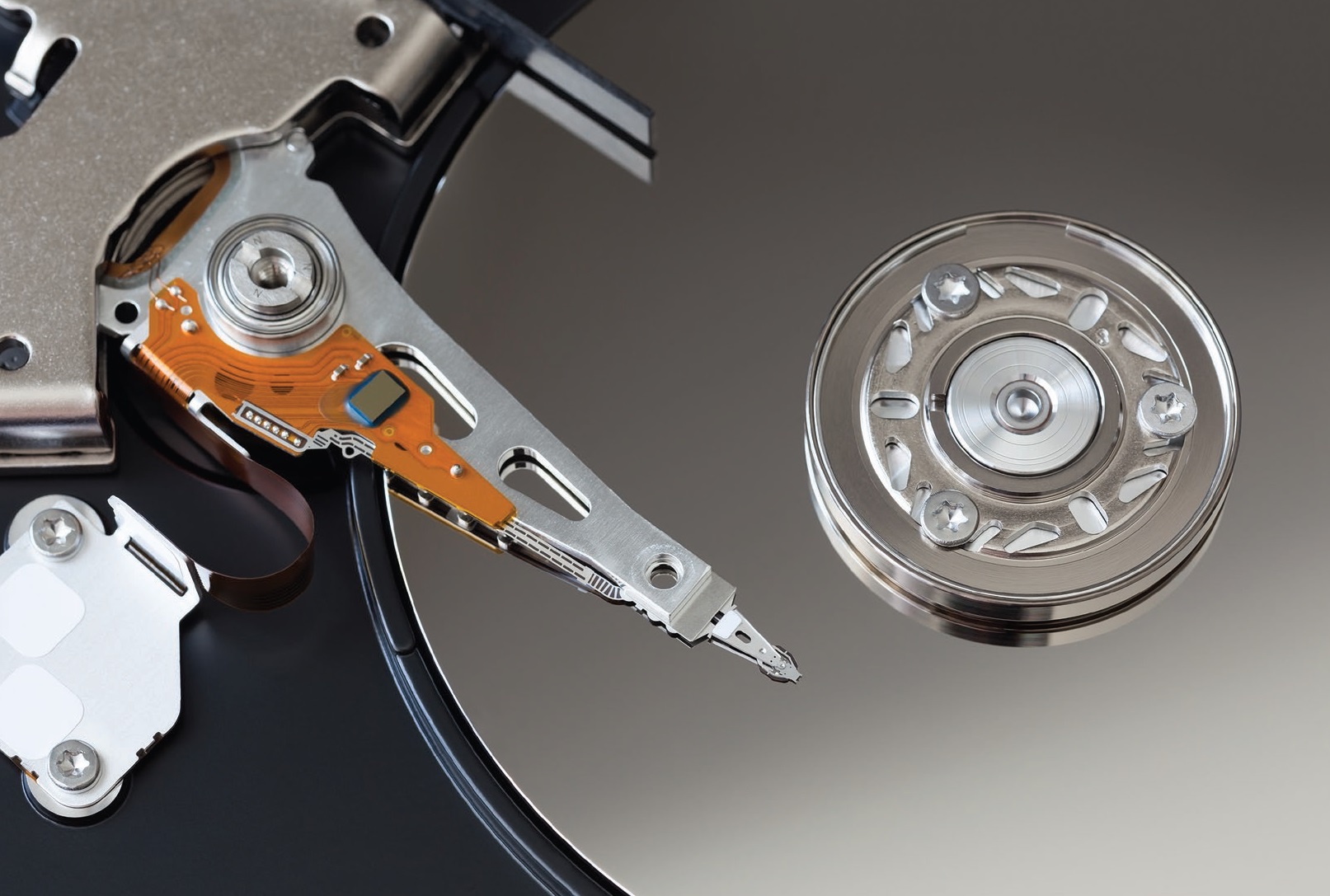
© Can Stock Photo / ASB63
KEY CONCEPTS
•
In the 1980s, computer hard drive manufacturers lubricated bearing assemblies using so-called heritage grease.
•
When heritage grease became a discontinued product, TS&E was tasked with developing a new grease formulation.
•
The new formulation includes an alkylated naphthalene base oil; a lithium complex thickener; and antioxidant, antiwear and rust-inhibitor additives.
MEET THE PRESENTER
This article is based on a Webinar originally presented by STLE Education on March 29, 2017.
Lubricating Grease for Rolling Element Bearings is available at
www.stle.org: $39 to STLE members, $59 for all others.
Paul Bessette is the president of Triboscience & Engineering, Inc (TS&E). He has been involved with synthetic lubricants for more than 39 years. During that time, he spent 25 years at Nye Lubricants and three years at Ciba-Geigy. TS&E was established as a consulting services company in 2000. Since 2005 TS&E has manufactured lubricants, focusing on perfluorinated polyethers. Bessette was vice chair of the NLGI Grease Education Course for 10 years, and he was honored with the NLGI Fellows Award, Meritorious Service Award, Achievement Award, Clarence E. Earle Memorial Award and Author’s Award. Bessette was an associate editor for Tribology Transactions and Journal of Synthetic Lubricants and peer reviewer for NLGI, and he has authored and co-authored chapters in several books on tribology and lubricants. He is a member of NLGI, STLE and ASTM. Bessette earned his bachelor’s of science degree in chemistry from Lowell Technological Institute in Lowell, Mass. His graduate work included polymer chemistry at Brooklyn Polytechnic Institute. He also has a master’s of business administration from the University of Massachusetts at Dartmouth. You can reach Bessette at
pabessette@tselubes.com.
Paul Bessette
Mechanical computer hard drives use a motor to spin a data storage disc. An actuator sweeps a read/write arm over the disc to read or write the data. Most desktop drives spin the platter at 7,200 rpm, but some high-speed server drives can spin at 10,000 rpm or even 15,000. The spindle that rotates the disc contains a bearing that uses grease to lubricate the rolling elements.
During the 1980s, computer hard drive manufacturers lubricated their bearing assemblies using what we will refer to here as heritage grease. This grease was made from a naphthenic base oil and a sodium complex thickener. The company that manufactured this grease discontinued making the product, ostensibly for economic reasons. Thus, the need arose to develop a synthetic bearing grease as a replacement. The story of how lubricant manufacturer Triboscience & Engineering (TS&E) developed a new grease for computer hard drives illustrates how a chemical tribologist formulates a grease for a specific application.
The challenge
Computer hard drives are designed to work equally well whether the hard drive is mounted vertically or horizontally (or at any angle, in the case of laptop computers). Thus, bearing lubricants must stay in place instead of draining to the bottom of the assembly. Because the bearing assemblies are sealed, the lubricant must last the lifetime of the hard drive.
In the early days of personal computers, disk drives used sintered metal bearings, which, while inexpensive and easy to manufacture, were difficult to lubricate over long periods. These bearings have a high copper content, which has a detrimental catalytic effect on conventional lubricants. When bearing companies were able to manufacture rolling bearings to the necessary tolerances, ball bearings became an option for disc drive manufacturers.
As the density of information stored on disk drives steadily increased, precise and stable positioning of the read/write head became increasingly important to ensure that the correct sectors of the disc were addressed. It became imperative to develop lubricants that performed well with the new high-speed, high-precision bearings in the disc drives. Grease manufacturers were called upon to produce greases that were not only suitable for high-speed bearings but also were ultra-clean.
Grease cleanliness was especially important to address a problem called non-repeatable runout, which causes non-systematic errors in the positioning of the read/write head. Contaminated grease or agglomerations of thickener within the grease causes vibration of the bearings that can cause the read/write head to wobble.
Heritage grease had several characteristics that were well suited to computer hard drives. It is a channeling grease—if a groove or void forms in the surface of the grease, it remains there; the grease does not flow to fill it. Channeling greases are useful for reducing torque, a desirable quality for mechanisms that must operate using very little energy. This NLGI Grade 3 grease is suitable for high-speed bearings (high Dn rating, >600,000), and it is economical to produce.
Heritage grease also is amenable to ultrafiltration, which improves the dispersion of the thickener and removes particulate contamination—an especially important property for hard drive systems, which demand smooth bearing operation. Heritage grease had a petroleum base oil and a transparent thickener system. Although it performed well tribologically, the volatile components of the base oil contaminated the media.
Tackling the challenge
After the manufacturer of heritage grease discontinued the product, TS&E was tasked with developing a new grease formulation. Coming up with a working formulation required us to start with the basic properties.
Grease is especially suited to rolling element bearing assemblies, which are often mounted in various orientations. Oil lubricants tend to flow out of a vertically mounted bearing assembly. However, grease remains in place when the bearing is at rest (solid behavior). While the bearing is operating, the grease becomes more fluid, lowering the resistance to ball rotation and reducing energy required for the bearing shaft to move.
Grease has both solid and fluid properties because it is a viscoelastic material. At low shear, elastic properties predominate, and the grease behaves as a solid. However, as the rate of shear increases, the thickener structure collapses and fluid properties of the grease dominate.
The viscosity (resistance to shear stress) of an oil is a linear function of the applied shear rate; that is, oil exhibits Newtonian behavior. The apparent viscosity (the ratio of shear stress to shear rate) is constant. Grease, however, shows a nonlinear relation between viscosity and shear rate (non-Newtonian behavior), and the apparent viscosity changes depending on the shear rate (
see Figure 1).
Figure 1. Grease’s apparent viscosity changes depending on the shear rate (shown here in reciprocal seconds).
All lubricating greases are composed of a base fluid, a solid thickening agent and additives. The base fluid, which constitutes 70%-95% of the formulation, does most of the lubricating work. The thickener immobilizes the base fluid to keep it from leaking out of the interface, and the additives act as antioxidants (AO), corrosion inhibitors and antiwear (AW) agents, among other functions.
When choosing a base oil for the new grease, we (TS&E) had to find an oil that would remain stable for the life of the hard drive, since the bearing system is sealed, and bearing failure is likely to damage or destroy the hard drive. The oil has to withstand temperature cycling as the drive goes from being idle to operational and back again. Impurities coming in from the outside were not an issue because of the sealed system.
We were looking for a grease that would resist volatilization, oxidation and other types of degradation but also prevent the mechanical parts from wearing and oxidizing. The new formulation includes an alkylated naphthalene base oil; a lithium complex thickener; and AO, AW and rust-inhibitor additives.
Addressing the volatility issue
Volatility causes a loss of lubricants and an increase in vapor pressure as the temperature is raised. All lubricants are composed of molecules that readily absorb thermal energy. At some point, these molecules gain sufficient kinetic energy to launch into the vapor phase. Lighter molecules tend to be more volatile and, thus, evaporate more easily at operating temperatures.
Base oils are a mixture of organic hydrocarbons (petroleum oils) or other long-chain compounds (synthetic oils, including silicones and synthetic carbon-based compounds). Natural products like petroleum tend to have more variable compositions than do synthetics. The molecular weights of petroleum components are spread over a greater range than is typical for synthetic oils, which means that they typically contain some volatile constituents. These volatiles can be removed by distillation, producing an oil with a narrower range of molecular weights, but distillation adds to the cost of the oil. Synthetics get around the volatility problem by having few to no volatile components to begin with. Synthetic oils are formulated to have a desired composition, so their components tend to have a much narrower range of molecular weights than do petroleum oils.
For our specialty grease, we tested various base fluids for volatility by measuring weight loss on heating in an inert atmosphere (nitrogen) and in an oxidizing atmosphere (air) (
see Figures 2 and 3). Under the nitrogen atmosphere, we found that Shell’s Pennzane multiply alkylated cyclopentane (MAC) base fluid could go to significantly higher temperatures without significant weight loss than Coray100 (one of Exxon’s older formulations for petroleum-based naphthenic oil) and Tribosyn 315, a significantly lower-priced alkylated naphthylene (AN) base fluid.
Figure 2. Volatility test comparing a MAC oil (Pennzane), a synthetic AN oil (315) and a petroleum-based naphthenic oil (Coray 100) under a nitrogen atmosphere.
Figure 3. Volatility test comparing the same three base oils under an air atmosphere.
However, real-world computer applications take place in an air atmosphere, and here MAC fluid loses some of this advantage, most likely because it oxidizes. Because the cost of the MAC fluid is much greater than that of the AN fluid, we decided it would be impractical to use MAC as a base oil, and we decided to use the AN base oil instead.
Choosing the thickener
Grease microstructure is sometimes described as a type of sponge, with base oil occupying the spaces in a tangled web of thickener molecules. Unlike a wet kitchen sponge, the base oil is the largest component of grease. There must be enough thickener, however, to form a matrix of soap molecules, and this matrix supports the oil phase.
The physical viability of a grease depends on a delicate balance between two opposing forces. Too much solubility of the thickener in the base oil leads to a one-phase system: there’s no thickener web to contain the oil when it’s not under a load. However, too little solubility causes the base oil to separate from the thickener. The grease must be formulated with the base oil and thickener compatibility somewhere between these two extremes.
A grease with an optimized degree of affinity between the base fluid and the thickener will tend to be transparent. Transparency indicates an absence of light-scattering particles; that is, the thickener particles are smaller than the wavelength range of visible light, and they are well dispersed within the base oil. Greases with ultra-small thickener particles, which are especially suited to high-speed operations, are the result of not only a good formulation but also the proper processing techniques during manufacturing. Because the thickening agent is the main disadvantage to using grease rather than oil, the less thickener used and the smaller the thickener particles, the better.
Putting it all together
We put our base oil and our grease formulation through a series of standard tests, along with some company test methods (CTM) that we have found to work as well as the corresponding standard tests (
see Tables 1 and 2).
Table 1. Base oil properties for the new specialty grease
Table 2. Grease properties for the new specialty grease
The kinematic viscosity (KV) values and viscosity index (VI) for our base oil were typical for high-speed rolling element bearing grease applications. We performed Brookfield Viscosity tests to determine the grease’s apparent viscosity as a function of temperature, taking the temperature down as low as -38 C. We did cone penetration tests to determine the consistency of the grease under storage (unworked, P0) and working conditions (P60 double-stroke), and we determined that this is an NLGI Grade 3 grease.
We checked the chemistry of our formulation using Fourier transform infrared (FTIR) spectroscopy to confirm the activity of the hydrocarbon components and the amount of lithium 12-hydroxystearate thickener present.
We performed four-ball wear tests under boundary conditions. The Tribosyn 315-based grease protected against wear better than a PFPE grease that we used for comparison, as evidenced by the larger wear scar for the PFPE grease. Unfortunately antiwear agents haven’t yet been developed that are suitable for PFPE grease (
see Figures 4 and 5).
Figure 4. A ball bearing protected with a grease made using Tribosyn 315 AN base oil showed only a small wear scar (small white spot indicated by black arrow).
Figure 5. A similar grease made with a PFPE base oil was less able to protect a ball bearing against wear.
We also did extensive testing of the thermal behavior of our base oil and grease. We found that our base oil did not become volatile, even after 24 hours at 100 C. We used an in-house method, putting the oil in a petri dish in a test oven. We have found that this method is good for routine testing, and it produces results similar to those from ASTM P972. Using our company test method, we found that evaporation of our grease formulation was 0.4%.
To check for volatility at elevated temperatures, we performed thermogravimetric analysis (TGA). This method is useful for measuring the volatility of microgram quantities of materials (on the scale of the amount of grease used in a computer hard drive assembly). The TGA tests showed that the grease sample could be heated to 300 C before it showed a 5% evaporation loss.
The grease’s dropping point is higher than 260 C, but it’s important to note that the dropping point is not the highest grease operating temperature. That is, you can’t use a hydrocarbon grease for a protracted time period at the dropping point temperature without it breaking down. So even though we now have thickeners that give you a high dropping point, that’s not your operating temperature.
A more useful test for finding a maximum operating temperature is pressure differential scanning calorimetry (PDSC), which measures the thermal oxidation potential using very small samples. We ran tests under very demanding conditions, 210 C under 3,500 kPa (500 psi) of pure oxygen. The sample failed to exhibit an exotherm (which indicates chemical degradation of the grease) even after two hours. Because typical petroleum-based greases would last less than five minutes under these conditions, and many synthetics would last fewer than 30 minutes, our formulation clearly had superior thermal stability.
Thus, our formulation balanced several factors. We addressed the volatility problem of the heritage grease by using a synthetic base oil rather than a mineral oil, but we chose an economical alkylated naphthalene that performed almost as well as a more expensive MAC under operating conditions. We used a widely available lithium complex thickening agent. The optical transparency of the grease showed that this thickener was present as very small, well-dispersed particles. When we combined these with antioxidant, antiwear and rust inhibitor additives, the result was a nonvolatile grease that resisted chemical degradation even under severe conditions.
Nancy McGuire is a free-lance writer based in Silver Spring, Md. You can contact her at nmcguire@wordchemist.com.