Q.1: How much compromise are you or your clients willing to accept to get a standardized gear oil for an equipment fleet?
TLT Sounding Board March 2018
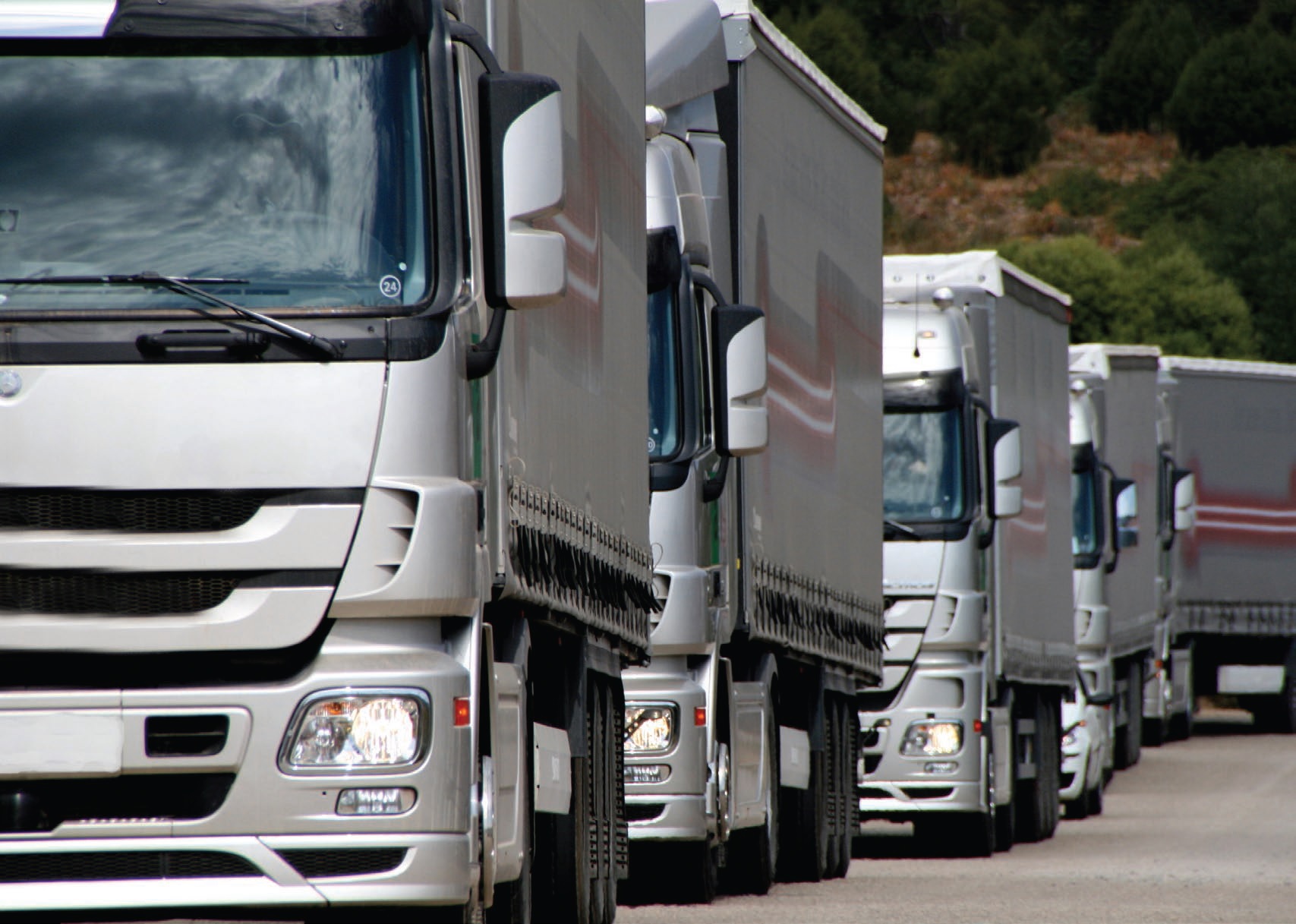
© Can Stock Photo / Ferdinandas
Evaluating, sorting and juggling priorities is one of those skills not taught in grad school that are part of everyday life for the lubrication engineer. Often this means making decisions on how best to protect machinery while at the same time responding to customer requests to standardize lubricants, reduce costs and minimize storage space. Some survey respondents say they will accept little or no compromise on the technical specs of the lubricant, often citing issues with manufacturer warranties. Others are far more willing to standardize lubes as long as the equipment is protected and the lubricant meets OEM specs. Large truck fleets seem to be the customer group most interested in standardizing oils, while gear oil purchasers are the ones most willing to pay more for extra performance. Still other readers rejected the notion of standardized lubricants altogether. “Is there such a thing?” asked one. “I really don’t know that this is possible, though tractor manufacturers might think so.”
Some compromise can be accepted as long as it does not negatively impact the life of the equipment.
I do not believe a standardized gear oil offers much value to me.
We work with our clients in order to recommend the best possible gear lubricant for each application, its operating conditions and OEM specification. We prefer not to compromise on quality or best practice.
Truck fleets greatly prefer a common gear oil for all equipment and will accept higher-priced synthetic products to achieve that goal.
Somewhat. Cost is the biggest player in that decision.
We will not accept any compromise to using a standardized gear oil for a fleet of equipment for risk of expensive maintenance and repairs.
Only a little bit; I would be more worried about compatibility for “accidental” top ups.
A lot. All customers are aiming for one product for all applications and, while it is not achievable, they still are willing to compromise.
They want quality at low price, which will not happen normally.
We have limited tankage and space for additional lubricants, so we standardize where it makes sense.
Anytime you can standardize, it is worth much compromise.
Somewhat as long as the gear oil provides adequate protection.
Is there such a thing? I really don’t know that this is possible, though tractor manufacturers might think so.
Somewhat. It would depend entirely on the quality of the oil.
You can’t compromise much with the newer equipment because the specs are so tight.
Will accept some if it provides better protection and meets OEM specifications.
Gear oil seems to still be a product where users are willing to pay a little more for additional performance. They’ll also use different oils in various applications if needed to reduce failures.
Minimal.
No compromises.
In an industrial facility, it is difficult to rationalize gear oils to one. Usually one ISO VG is required for worm drives and another ISO VG for most other gearboxes. Beyond this, it is usually possible to harmonize to one gear oil technology (e.g., PAO, PAG, mineral oil). However, this often requires changing over from OEM fills that are not compatible (clean downs) or ignoring OEM recommendations, which some maintenance departments will not allow.
Not much. Gears are different across manufacturers and can vary greatly even within the same gear set. Standardization is not a great idea.
A bit, if it can reduce inventory SKUs and possible misapplication of gear lubes.
So long as the lubricant is within specified perimeters and meets vehicle specs, it can be standardized (generally) across a fleet. There will be exceptions, but few.
Little to none.
Very receptive if the specs of the oil meet the requirements of the fleet. Then customers are willing to standardize and move to a single oil if possible.
Depends entirely on individual compartment requirements. Generally this would not work across a large fleet of diverse equipment.
As long as performance isn’t compromised, as a lubrication specialist I can accept some level of gear oil standardization. Typically my customers/clients will only accept gear oil standardization that will in no way conflict with OEM requirements.
I would 100% be willing to compromise.
Very little. Quite the opposite, in fact. Due to the lack of PM time and difficulty of change out, I upgrade my customers rather than compromise.
Depends on gear lube cost.
None right now. Not with manufacture warranties on the line.
Depends on customer type. Over-the-road fleets are pretty standardized these days on synthetic multi-viscosities, whereas industrial applications can vary by gearbox design, application, etc.
We are willing to standardize to eliminate multiple bulk storage tanks.
Not that much compromise. All gear systems are defined by specification, so standardizing can be difficult based on viscosities required.
Enough to make it economically sound.
None.
Is periodic condition monitoring applied to your equipment’s gear oil, and is it effective?
Yes. Condition monitoring is applied. It is effective and suits our needs.
46%
Yes. Condition monitoring is applied. It is rudimentary and we need more of it.
13%
Yes. Condition monitoring is applied. It doesn’t tell us anything we don’t already know.
4%
No. Condition monitoring is not applied but should be.
13%
No. Condition monitoring is not applied. We change oil based on service time.
19%
Other
19%
Based on responses sent to 13,000 TLT readers. Total exceeds 100% because some readers chose more than one answer.
© Can Stock Photo / romarti
Q.2: Describe the differences you see in gear oil lubricant maintenance and change rate for different countries and regions.
It is fairly constant without a lot of change. We are often the drivers of change.
None that I’ve noticed.
I see gear oil maintenance as non-existent with our customers.
The dustier, murkier, colder/hotter the conditions, the greater the need for gear oil changes. Gearboxes must breathe, so this, combined with the above factors, means there must be differences—quite extreme ones!
Ambient temperature seems to be one factor affecting the degradation of gear lubricants here in Texas.
The Asian-Pacific region seems to be more lenient in prolonging intervals between oil changes.
In an industrial context, it depends more on the application than the country, i.e., speeds, loads, operating temperatures, contamination levels, etc.
Gear oil-change frequency varies based on humidity and temperature across different U.S. regions.
It’s weather dependent.
My company mainly deals with offshore applications that use gear oil lubes, and during the hot and rainy summer months contamination and thinning occurs greatly and results in more frequent oil changes.
OEM recommendations and EP additives. Change frequency due to conditions and plant requirements.
It depends on temperature range. Tropical climates for off-road use require more frequent changes.
Less in EU countries.
Just follow what OEM engineers spec, because they know and care about protection more than others.
Typically U.S. and Canada customers rely on oil analysis to set up gear lubricant maintenance schedules. Other countries tend to change the lubricant either on a fixed schedule or when the lubricant is considered to be bad.
Most companies with good to excellent maintenance practices will change out routinely by miles or hours.
Yearly drain intervals in north central Texas.
Depends on whether oil sampling and condition monitoring are being performed.
I don’t see much deviation. Changes are typically defined by oil-testing results.
It differs on the ambient temperature. Normally in tropical countries where temps are higher, we go for higher-viscosity grade oils so that it maintains the film at the operating temp.
In South America, Central America and the Caribbean area, they use gear oils blended with Group I base oil, so this implies short change rates.
Editor’s Note: Sounding Board is based on an email survey of 13,000 TLT readers. Views expressed are those of the respondents and do not reflect the opinions of the Society of Tribologists and Lubrication Engineers. STLE does not vouch for the technical accuracy of opinions expressed in Sounding Board, nor does inclusion of a comment represent an endorsement of the technology by STLE.