Complexity in ISFA (in-service fluid analysis): Part XXXVII
Jack Poley | TLT On Condition Monitoring March 2018
Looking at maintenance in a different light can result in huge savings.
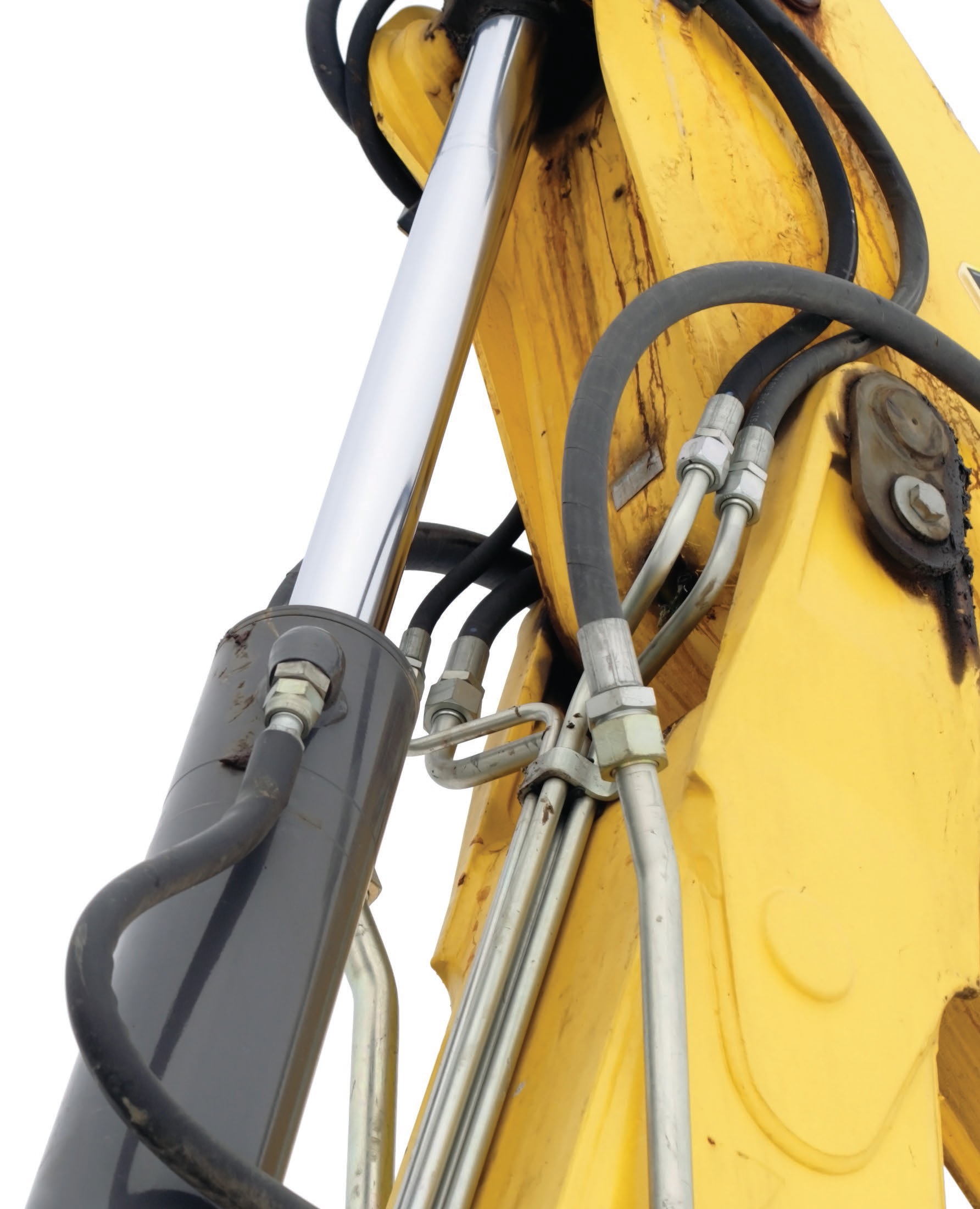
© Can Stock Photo / blasbike
Following on the heels of last column’s observation, of an increasing movement to conserve lubricant use via safely extended drains, is the need to justify condition monitoring (CM) programs with realistic numbers. The annoying thing about maintenance is that when it’s good, things work the same as they always did. It’s like mowing one’s lawn. A constant vigil. All that work (expense) just to stay even.
Because they are often perceived to generate no income, instead generating costs, maintenance departments are often step children in the plant, the necessary evil. Maintenance is often the first area management looks toward to make budget cuts when times get rough. This can’t be a good practice, can it? Is there a way to look at maintenance in another light?
I’m no economist in the professional sense, but it seems to me that saving dollars is as good as earning them. I’ve often used the phrase money conservation. This serves to decouple cost from accounting vernacular. It sounds good, but what does it mean? I’d say it means returning at least as much as you were given (paid) at minimum and hopefully substantially more over time. To simplify, if one can establish that more money is returned/conserved than spent from maintenance, that should be a good deal. And that could be called ROI (return on investment).
So now we have maintenance as an investment, if you will allow, and you have to because I’m writing this story. So the question is, how well does this investment pay off? That depends—my favorite answer to open-ended questions—on the culture of the business and all the players involved, including such things as level of the investment (budget) and how well it’s spent (decision-making by maintenance). We hope a generous amount for CM is included in that spending.
I’m not aware of any CM program that wasn’t perceived to have returned a positive ROI due to the low-hanging fruit, particularly for ISFA, within the various CM disciplines because of the first of the two points posed last column: safe lube drain extensions. Keep in mind that is the bonus of oil analysis, not its primary benefit.
Lubricant savings is capable of covering costs in a great number of ISFA programs. What’s not to like? But it is this very benefit that can be the Achilles heel of a program: positive ROI is deemed good enough. Not nearly so, if all one can brag about is saving lubricant costs above program costs. Another plateau of opportunity is usually available, but it will take some effort from maintenance.
What kind of things can maintenance do with an ISFA program?
•
Conserve lubricants (we already said that—what else?).
•
Swiftly act on problems identified by the program—a forewarning has been provided—don’t lose the tempo you may have gained. Tend to problems
immediately so that they don’t become crises. In some ways this is the dollar moment, where you conserve/save the most money from your ISFA program: less repair cost, more uptime (maximized revenue).
o
Order parts in advance or, as remote operations like offshore oil rigs might do, order a replacement component and swap it out at the moment of truth (that usually means failure). This happens more than one might like to think, and there are times when such action must be taken, in the minds of those in charge, given the situation. A frequent occurrence, when an offshore rig is producing at full bore and has good ISFA (or other CM) information that a component is at risk, is to bring in a replacement component with the notion of risking/allowing total failure as worth it to continue to deliver product. This is a decision that is the sole province of the rig manager. Product simply trumps risk, in such cases.
•
Connect the dots when problems arise to dig out root cause, practically described as the real problem, as opposed to the symptom:
o
A certain machine type repeatedly exhibits the same symptoms—either the repair was superficial/ineffective or nothing at all was done other than, perhaps, to change lube. Changing lube never solved a problem, but it does forestall some. Allowable exception: Going back to our offshore example, when a top drive gets contaminated from drill mud, drain frequencies are often increased so that there is some effort to forestall failure while awaiting a replacement’s arrival. In this case, oil
is cheap.
o
But the crux of root cause is that it be pursued once repeat failure types present themselves.
Macro-recap:
•
For the third time, yes, lube drain extension is a front-end ISFA gift if properly monitored.
•
Swift action—that’s the operative term. There is a clock running once a developing problem is detected with an ISFA sample, and, with good data evaluation from a domain expert (also called subject matter expert or SME), be it human or software, minimal damage is the reward. I’ve seen those rewards range from $1,000-$2.5 million. It all depends on what component is at risk, what its role is in the production process
and how quickly the developing problem is addressed. There’s money waiting to be conserved. Acting in timely fashion is potentially the biggest reward one can receive from ISFA. It’s like running to the bank to make a deposit of found cash.
•
Root cause is often spoken about but not always chased down. It’s not always easy, and it surely involves time, but it is the second most powerful ROI takeaway in most programs when availed.
Next issue I’ll provide a practical example of root cause.
Jack Poley is managing partner of Condition Monitoring International (CMI), Miami, consultants in fluid analysis. You can reach him at jpoley@conditionmonitoringintl.com.
For more information about CMI, visit www.conditionmonitoringintl.com.