Bridging the gap between metalworking fluid bench tests and machining operations
Dr. Neil Canter, Contributing Editor | TLT Feature Article March 2018
Success depends on how closely you can identify a test with tribological parameters similar to your application.
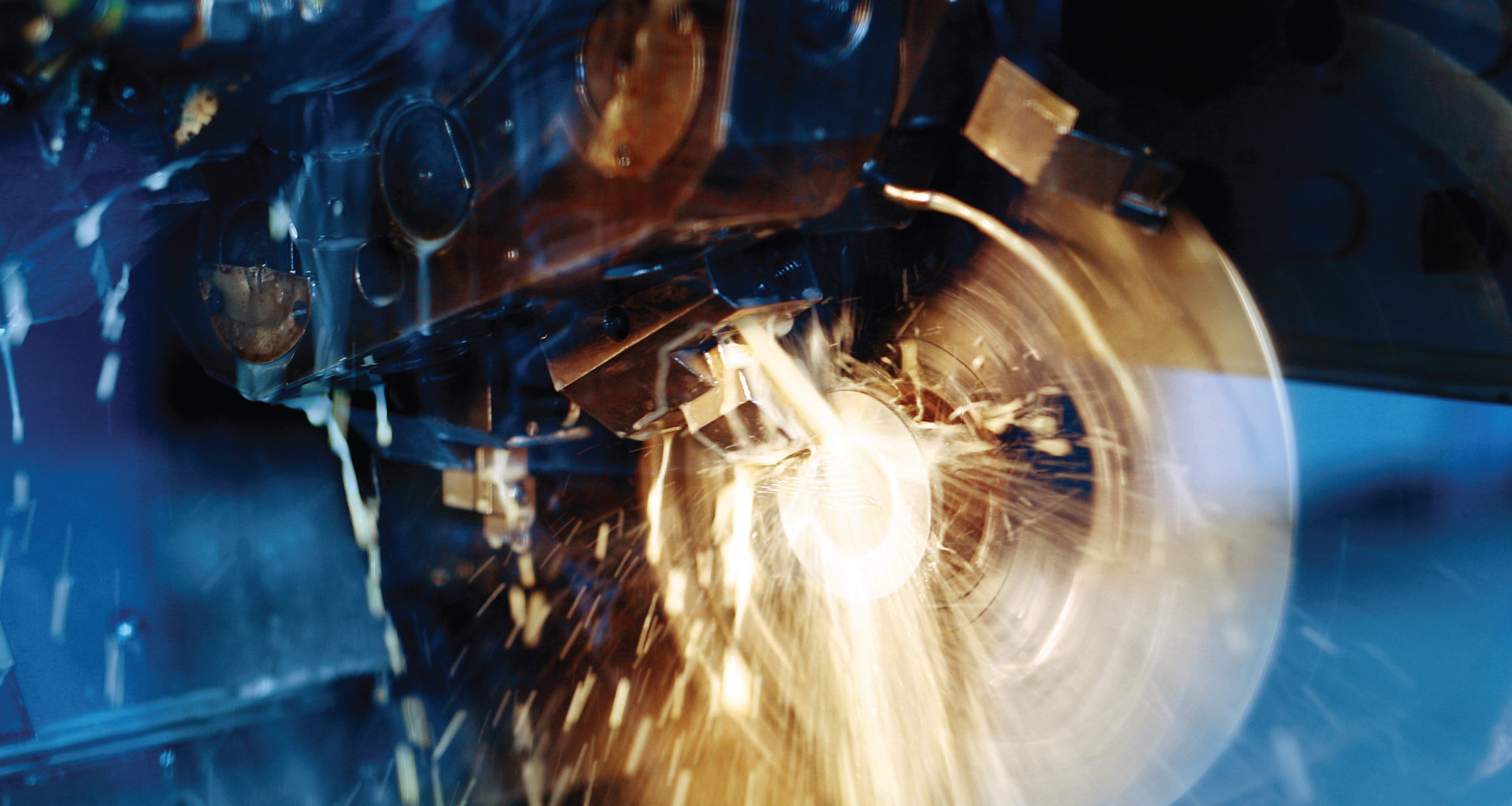
© Can Stock Photo / nd3000
KEY CONCEPTS
•
An extensive number of laboratory bench tests are available to evaluate metalworking fluids.
•
The challenge is to identify laboratory bench tests that correlate well with metalworking operations undertaken by end-users.
•
Good correlation between an actual machining operation and laboratory bench tests can be achieved by understanding the complexity of the machining operation and determining how well it fits tribologically with the laboratory bench test.
•
Laboratory bench testing can correlate well initially with an actual machining operation, but conditions in the actual machining operation can change over time, making it difficult to evaluate these changes in the laboratory.
Metalworking operations are diverse and complex with many variables to consider such as the type of metal alloy being machined, type of machine tool and cutting tool used, speeds and feeds, how much material is removed or moved in a forming operation and the size of the metal part that is undergoing the operation. This makes it very challenging to figure out the right type of metalworking fluid to use.
To further complicate matters, the same metalworking operation on two identical machines using the same metalworking fluid can lead to different results. STLE-member and TLT technical editor Michelle Brakke, manager industrial and distribution product development at Lubrication Technologies, Inc., in Golden Valley, Minn., says, “The metalworking fluid industry has a good deal of data available showing how specific additives and fluids perform in laboratory bench tests. But applying this data to actual field operations does lead too often to the metalworking fluid failing. What can be done to minimize the risk end-users face in changing metalworking fluids even though they will need to accept some failure?”
This article explores how best to utilize lab bench tests so that a metalworking fluid can be formulated to minimize risk and give both the formulator and end-user more confidence that they will meet the requirements for a specific field operation. Input on this issue was obtained from industry experts who have perspectives from the additive, formulator, testing lab and end-user standpoints.
The following individuals were contacted:
1.
Dr. Anthony Jarvis, Afton Chemical
2.
Brian Hovik, Chemetall/BASF Corp.
3.
Bridget Dubbert, Engineered Lubricants
4.
Mike Anderson, Falex Corp.
5.
Tom Bjellos, Lubrication Technologies, Inc.
6.
John Hogan, The Lubrizol Corp.
7.
Justin Dunlap, MetaLube, Inc.
8.
Dr. Rich Baker, PCS Instruments
9.
Dr. Robert Golden, Pilot Chemical Co.
10.
Pat Holden, Poclain Hydraulics
11.
Dr. Robert Evans, Quaker Chemical Corp.
12.
Ted McClure, SLC Testing Services
13.
Jerry Byers, Independent Consultant
Current laboratory bench tests
STLE-member John Hogan, project manager, industrial additives at The Lubrizol Corp. in Wickliffe, Ohio, indicates that there are many friction and wear tests available to evaluate the lubricity and extreme-pressure capabilities of an additive or a finished metalworking fluid. He says, “The key is to identify a test with similar tribological parameters as the application wherever possible. Often several tests may be utilized to understand different aspects of performance—and different tests may be better understood or valued based on geography, industry or fluid type.”
STLE President Mike Anderson, area manager Asia Pacific/Latin America for Falex Corp. in Sugar Grove, Ill., says, “With many tests available, the question comes down to whether to use a standardized test or a custom-designed test. A standardized test is one in which all or most of the parameters are specified. The benefit is that all users should be able to run the test in exactly the same manner and under the same operating conditions. The negative is that all field conditions are not necessarily the same as those in the standard method and require modifications to the test methods to be more specific to the conditions where the metalworking fluid is used. The best approach is to determine the conditions under which the metalworking fluid will be used before recommending a laboratory bench test. Conditions to evaluate include the contacting materials, loads, motion, speed, contact geometry, temperature and atmospheric conditions.”
Anderson continues, “The final test should be selected that best represents the final use condition. An excellent starting point is to use the Tribological Aspect Number. This identifies the tribological condition of the field application and facilitates the selection of the most appropriate laboratory bench test.”
STLE-member Ted McClure, technical resources manager for SLC Testing Services in Westlake, Ohio, divides the currently available tests into laboratory bench tests used in metalworking and simulation tests. He says, “Laboratory bench tests create a particular tribological condition that may be applicable to some production operations. Examples include the Brugger test, four-ball extreme pressure (EP) and wear tests, pin and vee block test, pin-on-disc test, Reichert friction and wear test, hole expansion test variations and twist compression test (TCT).”
McClure continues, “Simulation tests are scaled-down industrial applications for use in the lab. They generally correlate well with field performance. Examples include the corner fill-tube expansion for hydroforming, draw bead simulator, tapping torque, instrumented Computerized Numerical Control (CNC) machining center and various press metal-forming tests, including limited dome height cup and square or rectangular pan draw tests.”
STLE Past President and Fellow Jerry Byers, independent consultant in The Villages, Fla., says, “The preferred approach for evaluating lubricity in metal-removal applications is to use actual metal-cutting tests such as instrumented production machines (lathe and surface grinder). Both machines are effective at evaluating additives and then finished metalworking fluids. Another good option is the tapping torque test, which allows for fast and easy evaluation on various metals using smaller fluid volumes (leading to less waste). One laboratory test type that should not be trusted are simple ‘rubbing’ tests that do not simulate actual machining operations.”
STLE-member Dr. Robert Evans, research scientist, metalworking division at Quaker Chemical Corp. in Conshohocken, Pa., agrees that there are numerous laboratory bench test methods available for evaluating the lubrication properties of an additive. He divides the tests into those evaluating EP lubrication and others measuring lubrication under less severe (non-EP) conditions. Evans says, “Common laboratory bench tests evaluating extreme-pressure properties are the four-ball, pin and vee block and twist compression testers. Non-EP conditions are measured by using various types of reciprocating boundary friction testers as well as testers employing a block on ring configuration useful for measuring friction and wear.”
Effectiveness of current laboratory bench tests
McClure finds that problems exist with applying results from bench tests and simulation tests to actual metalworking operations. He says, “Bench tests are generally easier to run, less time consuming and less expensive than simulation tests. However, bench tests require an understanding of how the specific condition(s) created apply or not to the application being investigated. Simulation tests are directly related to the process being simulated, but caution should be used in applying simulation test data to industrial operations other than the specific one being simulated. Figure 1 summarizes the challenges faced with applying bench and simulation tests well. Lubricant formulators need to evaluate a lot of factors (specific raw materials used in particular combinations) and are likely to screen, using bench tests before moving onto simulation tests and then field trials.”
Figure 1. Bench tests, covering a large number of factors, need to be done initially before moving to simulation tests and field trials where a smaller number of factors are involved. (Figure courtesy of SLC Testing Services.)
STLE-member Brian Hovik, metalworking fluids market manager and applications engineer-aerospace for Chemetall/BASF Corp. in New Providence, N.J., says, “Bench tests provide a limited view of a metalworking fluid’s performance because they offer only a snapshot into how a fluid performs in the production machine. There are many variables that influence a fluid’s performance such as the cutter, feeds, speeds and aggressiveness of the CNC machine programmer, to name a few.”
STLE-member and TLT technical editor Bridget Dubbert, technical director for Engineered Lubricants in Maryland Heights, Mo., says, “ASTM procedures such as the four-ball EP/wear are not likely to be misinterpreted if they are taken for what they are; a weld load reported in the EP test is a repeatable, definitive result for a specific attribute of the product. But these tests are more applicable to lubricants than metalworking fluids. The tap torque test, when used very methodically with many repetitions and the right materials, can give a good representation of what will happen in the field because it is an actual metal-cutting/forming operation. But just like any other test, without due diligence, the results can be misinterpreted or misrepresented very easily. The more variables involved in the test, the higher risk of misinterpretation because it is easy to focus on the wrong thing (i.e., looking at torque when you should be studying the wear characteristics). Many tests such as the TCT and the pin and vee block have very flexible method development capabilities, which is great, but interpretation can get into a gray area very easily.”
Dubbert reveals that the pin and vee block has been very useful in comparing additive performances. She says, “If product differentiation cannot be achieved with the current test methods, then we have found that adjusting testing parameters such as increasing speed, load or test time helps to show differences in performance.”
An example is shown in Figure 2, which shows data developed from a modified pin and vee block machine evaluating two fluids in a wear test. The test pins were prepared from two aluminum alloys that were used by the end-user. Extending the test procedure from 80 minutes to 210 minutes enabled the laboratory bench test procedure to distinguish the wear seen between the two fluids. This result correlated well with the actual machining operation.
Figure 2. Torque (left graph) and wear (right graph) studies were done evaluating a semisynthetic fluid and an emulsifiable oil using a modified pin and vee black machine procedure. Extending the time of the test led to differentiating the wear performance of the two metalworking fluids. (Figure courtesy of Engineered Lubricants.)
Hogan believes that test accuracy requires correlation between the lab test results and the customer’s operation. He says, “This relationship must be shown on many samples to be trusted. Based on experience, opinion or both, chemists across the industry do not always agree whether certain tests actually help predict certain manufacturing operations. Nevertheless, precision also is important. Most standard tests, such as the four-ball EP, will have precision statements to aid in understanding of repeatability, reproducibility, bias, etc. For non-standard tests, it is important to understand the test precision for proper interpretation. Statistical analysis is the best practice to generate this data; for example, a tapping torque test with a 3% difference at a 95% confidence level may be more meaningful than just stating a 5% difference in the mean values.”
Byers says, “Instrumented production machines and the tapping torque have been found to be very effective at estimating field performance.”
STLE-member Justin Dunlap, product development engineer for MetaLube, Inc., in Youngsville, N.C., also finds the tapping torque test to be useful in evaluating metalworking fluids. He says, “The tapping torque test is significant when considering the lubrication properties of a water-based fluid for general machining.”
Evans feels that in examining the current laboratory bench tests, accuracy and interpretation of the data must be dealt with separately. He says, “For the most part, as long as the testers are functioning properly mechanically, and all measurement or diagnostic tools are calibrated, most testers provide very accurate data regarding the friction and lubrication occurring under the conditions in which the test was performed. The real challenge and often limitations come with the interpretation and application of the test results as they relate to the use of a fluid in a given industrial metalworking operation. This is where a disconnect often occurs.”
Anderson maintains that the current bench tests are only effective if relevant to the specific field condition. He says, “Often a standardized test will be used to rank fluids for their ability to prevent wear or provide EP properties. The more successful candidates must then be tested under conditions more specific to the actual field application. Modifications of the test conditions are essential in the final bench test selection.”
Dr. Anthony Jarvis, R&D manager for global MWF development at Afton Chemical Ltd. in Manchester, UK, indicates that most tests available to raw material suppliers and metalworking fluid formulators can provide consistent data and help differentiate specific fluids.
STLE-member Dr. Robert Golden, senior research chemist for Pilot Chemical Co. in Cincinnati, Ohio, says, “We have found that laboratory bench tests such as the four-ball do not produce a relatively high degree of precision particularly when retesting samples. Our results show that the retesting results show greater differences than between the samples tested. This observation makes it difficult to conclude that differences between samples tested in the lab will be seen in field operations.”
Golden believes that a level of expertise is needed to properly interpret field results. “The most important knowledge is to know the repeatability and reproducibility of the results,” he says. “Expertise also has to include knowledge of the materials being tested.”
Correlating laboratory tests and field trials
Jarvis feels that the types of laboratory bench tests and machine tests available in a lab can all create a disconnect between laboratory tests and field applications. He says, “Only the tapping torque test among the laboratory bench tests available for assessing metalworking fluids is an actual metal-removal application. The other tests are basically metal-on-metal friction tests. Bench tests are undertaken at a much smaller scale than the majority of real-world applications with the primary example being the tapping torque test. While some testing can be done on an actual machine in a laboratory setting, getting consistently reliable results is challenging. One reason is that machining in the lab may be done under different conditions (such as speeds and feeds) than are encountered in the targeted field application.”
Evans feels that three primary factors (contacting surfaces, testing under cutting conditions and length of operation) are responsible for the inability to correlate laboratory tests with field trials. He says, “Often the nature (wear and friction properties) of the contacting surfaces (e.g., tool cutting edge and workpiece) present significant factors influencing the friction, heat and metal adhesion, which occurs in a cutting operation. It is often difficult to utilize or even replicate these materials in many laboratory lubrication tests, and therefore standard materials must be used. This becomes an even greater limitation as more highly engineered materials continue to be developed and machined for many functional parts. The result is that the inability to evaluate the actual alloy used in a specific application often leads to misinterpretation, inaccurate conclusions or misapplication of laboratory test results.”
Evans continues, “In addition to the nature of surfaces, the inability of most laboratory bench tests to involve metal cutting in the process also makes it difficult to apply results to a given machining operation. The third element to consider is the length of time that a fluid is used in an actual machining operation relative to the time required for most bench lubrication tests. Quite often problems in a machining operation surface after a period of trouble-free machining. This can be attributed to a variety of factors that include (a.) modification over time of the contacting surfaces such as chemical changes—as well as mechanical changes such as those due to strain hardening of the workpiece material, (b.) depletion of critical lubrication components that can occur over time and (c.) changes in the nature of the metalworking fluid emulsion, which can often occur due to various factors such as continued shear, recirculation, filtration, etc. These factors and the effect of continuous use and operation of the fluid cannot be studied or accounted for in most laboratory test methods.”
Dubbert points out some of the reasons why correlating laboratory bench tests with field trials is difficult. “There are so many variables encountered in the field in a metalworking environment,” she says. “No matter how successfully these variables can be controlled in the laboratory, conditions are hard to replicate from the field especially when the test sample is maybe four liters (if fortunate) and the metalworking system is greater than 400 liters, takes on tramp oil and who knows what else in normal operations. No one laboratory bench test is available that can reliably replicate milling, drilling, grinding and cutting, which are all operations a machine shop may expect a metalworking fluid to handle. Materials used in the field also can be an issue; many bench tests evaluate steel on steel, which is not always the case in end-user applications.”
Byers says, “The difficult aspect is adjusting laboratory bench test conditions to match in-plant conditions. Many times the in-plant conditions cannot be duplicated exactly. Testing on the same or a very similar metal alloy is critical.”
McClure feels that a major factor is defining the tribosystem in the actual metalworking application and understanding the strengths and limitations of laboratory bench tests relative to the complexity of the tribosystem. He says, “There have been situations where laboratories use two steel surfaces in a bench test, presumably for convenience or because it has worked for them in specific instance(s) in the past, to gain information on how the metalworking fluids will rank in processes involving workpiece materials other than steel alloys. A basic consideration is to match the surfaces in contact in the field operation with those used in the tribotest.”
The choice of specific alloy to test is very important as illustrated by a TCT study comparing a chlorinated paraffin-based straight oil versus an oil formulated with a sulfurized olefin, ester copolymer and a zinc dialkyldithiophosphate (ZDDP) (
1). As noted in Figure 3, the chlorinated paraffin free oil performs very differently on cold-rolled steel as compared to stainless steel even when using the same tribotest.
Figure 3. A TCT study shows the performance of straight oils differs based on the metal alloy used. In this case, a chlorinated paraffin-based straight oil is compared to a straight oil formulated with a sulfurized olefin, ester copolymer and ZDDP on cold-rolled steel (top graph) and 304 stainless steel (bottom graph). Please note that the two tests were run under different conditions with the 304 stainless steel study being run under a lower pressure than the cold-rolled steel study. (Figure courtesy of SLC Testing Services.)
McClure points out that test surface preparation, type of contact and the mode of failure all have to be considered in finding a lab test that will correlate with the actual field operation. He says, “Figure 4 shows four different types of contact geometries, and the one that is involved in a specific application may determine if the metalworking fluid is depleting.”
Figure 4. Determining the type of contact geometry involved in a specific metalworking fluid application is important in finding a laboratory bench test that will correlate with a field application. Four contact geometries to consider from left to right are point contact, line contact, area contact (depleting—sharp edge) and area contact (non-depleting beveled entry). (Figure courtesy of SLC Testing Services.)
McClure feels that perhaps the biggest issue for lack of correlation between lab testing and field trials is communication. He says, “The end-user and formulator should have direct contact. The formulation chemist should see the operation(s) and challenges first hand in the manufacturing environment. A good understanding of laboratory bench tests can mostly be wasted if the application is not equally well understood.”
In designing laboratory test equipment, Dr. Rich Baker, general manager of PCS Instruments in London, UK, provides input on how to develop laboratory bench tests that correlate with field applications. He says, “We look at the field application test conditions and then look to replicate these as closely as possible in a compact affordable laboratory instrument. We are developing instruments to look at fundamental research and our customers expect fully automated instruments that give quick, repeatable and reliable results.”
Input from major additive and lubricant producers also is important to Baker. He says, “We have very good relationships with the major global additive and lubricant companies who are willing to share with us the instrument capabilities they are missing and which techniques could be improved to further their lubricant development. We also work with the academic community as we retain close ties with the Tribology Group from Imperial College in London.”
Dunlap believes one of the problems is that many of the key parameters impacting field trials are standardized in the laboratory but are variable in actual machining operations. He says, “By definition, laboratory tests for lubricity are performed in an environment that is controlled to such an extent that the results of any two tests are directly comparable. Parameters that affect the lubricity of a metalworking fluid in use include the type of additive chemistry, make-up water quality, machine design, machine settings, application parameters, contamination control and type of tooling.”
Hovik agrees that there is a myriad of variables that are almost impossible to test for in the laboratory. He says, “In many respects, the trial-and-error process seems to still work best, using laboratory bench data as a place to start.”
Golden says, “There are two issues that make it difficult to correlate laboratory bench tests with field trials. The first and far more problematic is that the actual machining operation is sometimes reported as a qualitative impression or, worse, it is sometimes biased by folklore. As a result, impressions and prejudices are found to be preferred over laboratory bench tests even if the latter are properly designed.
Golden continues, “A second factor deals with the duration of the machining process. As many fluids—particularly in metal-removal applications—recirculate over time, they undergo some changes that might be specific to the operation and the machine tool. The result is that initial correlation of the actual operation with laboratory bench tests may change over time.”
Hogan says, “Assumptions often need to be made and compromises are required when running laboratory tests to demonstrate performance. One example could be performing a drilling lab test that shows low-cutting forces and minimal tool flank wear, which might suggest good tool life for a drilling application. This may not prove to be the case in the field when drill bits prematurely fail due to a different mechanism (such as chipping wear from the machine or part fixture vibration) than what is observed in the laboratory.”
Hogan maintains that product development laboratories have limited testing capabilities that can often not match what is occurring in an actual machining operation. He adds, “Metalworking fluid raw material suppliers and formulators will use whatever available instrument(s) with which they are comfortable and have experience using. Since the metalworking fluid industry is more geared toward comparative performance than meeting specifications, this is in some cases sufficient.”
Laboratory tests correlating well with field trials
Hovik says, “There are three tests that correlate to specific metalworking fluid applications:
1.
Drilling test. Measuring torque on the spindle.
2.
Milling test. Similar to drilling but measuring tool life and torque on the spindle.
3.
Grinding test. Measuring wheel geometry and/or wear along with surface finish.
A comprehensive approach for evaluating metalworking fluids involves the use of eight types of laboratory tests ranging from machinability to biostability as shown in Table 1. Metalworking fluids from the four main types (neat oils, emulsifiable oils, semisynthetic fluids and synthetic fluids) were evaluated on a scale ranging from 0-5 for each type of test. The 17 metalworking fluids were initially evaluated and then ranked by adding up the scores.
After 180 days of use in production, the top four metalworking fluids were re-evaluated and given ratings based on production use as shown in Table 2. Changes in the top four fluids are shown over on the right. Hovik says, “This was a good test to determine how well laboratory data translated into production data. The lab analysis did quite well in showing how well a product would perform as compared to in-production analysis. This validated the lab testing protocol and data.”
Table 1 and Table 2. Eight laboratory bench tests were used to evaluate 17 metalworking fluids as shown in Table 1. Each fluid was rated on a scale from 0-5, and the values for each test result were added up in the right column. The fluids were ranked from highest to lowest. After 180 days of use in production, the top four metalworking fluids were re-evaluated and their scores listed in the right column in Table 2. Good correlation was seen between the laboratory test data and how well the metalworking fluids performed in production. (Tables courtesy of Chemetall/BASF Corp.)
Byers offers some pointers for raw material suppliers and formulators prior to running laboratory bench tests. He says, “The metal being tested in the laboratory needs to be similar to the metal the end-user is working with. Often it is useful to fabricate test pieces from the actual end-user parts. Water also is an important factor in laboratory bench testing and it is desirable to use the actual water available to the end-user in the laboratory.”
With this as a basis, Byers believes the following laboratory bench tests will correlate well with field trials. He says, “We found that determining the G-ratio using a surface grinder gives a good estimate for most grinding operations. The instrumented lathe and the tapping torque tests gave good predictions of performance for most cutting applications. The block-on-ring test seemed to predict performance on reaming, where there was not much cutting but a lot of rubbing. Cup draw tests, and to a lesser extent the twist compression test, were good for predicting stamping and drawing operations. Unfortunately, in my experience no laboratory bench test was able to accurately predict broaching performance.”
Dubbert finds that the twist compression, pin and vee block and the four-ball wear tests can provide correlation with specific machining operations. She says, “Twist compression is effective for drawing and stamping, pin and vee correlates to many cutting and grinding operations, particularly when the method can be modified to mimic metals and conditions in the field, and four-ball wear (modifying methods and sometime the 40-kilogram wear) can correlate well to oil-based cutting operations.”
Hogan admits that individuals working in the metalworking fluid industry do not always agree on whether certain tests help predict results in certain manufacturing operations. He says, “We feel that the following four laboratory bench tests relate well to certain metalworking applications.”
1.
Mini-traction machine (MTM). Rolling oils because of its slide/roll configuration.
2.
Tapping torque test (TTT). Relevant for many metalworking applications because of the flexibility it offers for tool/material/condition selection.
3.
Twist compression test (TCT), cup draw tests and strip draw tests. Most often applied for metal-forming applications. These tests may be performed under varied conditions with different metals to relate to a specific application.
4.
Actual production machining tests (e.g., CNC milling). Offer great flexibility and the ability to match laboratory testing to production conditions. However, working with such tests is relatively resource intensive.
Hogan says, “For instance, we found that TTT is effective in correlating with field performance for steel machining. In the study shown in Figure 5, we evaluated five commercially available metalworking fluids with known field performance via TTT (form tapping 1018 steel). The TTT results correlated to the known field performance and provided differentiated results among the five fluids at the 95% confidence level.”
Figure 5. A tapping torque test study shows results from five commercially available metalworking fluids that were form tapping 1018 steel. These results correlated well with known field performance. (Figure courtesy of The Lubrizol Corp.)
Jarvis feels that one important aspect in correlating laboratory bench tests with field trials is the metal in question. He says, “The tapping torque test works particularly well with aluminum, which is relatively easy to cut (or form a thread) when testing semisynthetic fluids. This test is less effective when a hard metal such as titanium is used.”
Other tests that are effective according to Jarvis are shown below.
1.
TCT is considered valuable for forming applications.
2.
Reichert test is good for polyalkylene glycol (PAG) based synthetic fluid formulations.
3.
Pin and vee block and four-ball tests are good for EP differentiation on straight oils.
4.
Cup drawing is good for drawing and stamping applications.
Dunlap lists specific metal-removal operations that work well when using the tapping torque test. He says, “Some general removal operations that correlate well with the tapping torque test are milling, drilling, turning and tapping.”
Development of new additives
To effectively develop new products using existing laboratory bench tests, a number of strategies need to be considered. Jarvis says, “Four elements are important in developing new products that include employing a variety of different laboratory-based tests. Metalworking fluid companies cannot rely on just one. Conduct small-scale field trials/machining trials using real-world CNC machine tools. Develop a collaborative approach with end-users, fluid formulators and additive suppliers to improve a specific situation. As these trials are underway, look for tool life, breakages, number of components machined, improved productivity, etc.”
Hogan believes that the objectives and scope need to be properly defined when developing a new additive or metalworking fluid. He says, “It is easy to make a broad objective such as ‘improved tool life,’ but without defining what that means and how it will be measured, it may be difficult to succeed. There also are many other properties important to modern machining fluids, including sump life, foam tendency, corrosion protection, operator acceptance, regulatory concerns, cost, etc., which must be considered. A collaborative effort must be established between a supplier and a customer, and responsibilities and communication channels must be clearly defined.”
Dubbert says, “An additive supplier should provide test results on multiple types of metals if possible and disclose as much information as possible about how the testing was conducted (including load, speed, temperatures, etc.).”
Dunlap believes that additive suppliers need to help out in two ways. He says, “The best step an additive supplier can take to help with their customers’ product development is to have technical service people in the field/lab who have experience in formulating metalworking fluids. A close second is to have at least some in-house lubricity test capability to aid customers in validating formulations and making the best possible decision for a specific end-use.”
Hovik says, “Basic performance data from recommended tests (such as for drilling) represent a great start. If possible, case studies with applications that show improvement in lubricity or tool life also work well.”
McClure stresses that correlation between laboratory bench tests and field trials should be established early in the process. He says, “Metalworking fluids should be tested that have both positive and negative field performance history to establish applicability and analysis protocol. Metalworking fluid formulators should see the application first hand and preferably be present for trials of new formulations. Everything possible about field and laboratory test conditions should be documented.”
McClure continues, “In an effort to determine if a particular laboratory bench test is relevant for a specific application, a tool called a TSA or tribosystem analysis should be used to first understand the industrial process and then to match this with the appropriate tribotest. Further details on TSA can be found in a recently published book on tribosystem analysis (
2).
Golden feels that additive suppliers must rely on their in-house expertise to effectively develop new products. He says, “We are focused on understanding how emulsifiers function and their role in stabilizing water-based metalworking fluids. By further understanding the emulsion structure, we can refine additive properties to improve an important characteristic to formulators such as hard water stability.”
Need for improved laboratory tests
Two areas that should be improved are testing for high-speed machining and foam. Dunlap says, “There is need to measure lubricity at high-fluid application pressures and velocities. An approach that might work would be to combine a tapping torque tester with a chip blaster. Modern machines have higher spindle speeds and higher pumping pressures that certainly affect the lubricating properties of the fluid.”
Hovik comments as well on the need for better testing under high-speed conditions: “It is difficult to translate laboratory test data into a satisfactory correlation due to the added variable of high-speed machining (over 25,000 rpm). Trial and error appears to be the most effective current solution for this application.”
Golden says, “The lack of an ASTM test for foaming is an issue, particularly since field performance is dependent on antifoams and defoamers. There are significant conceptual issues that surround what the test should look like.”
STLE-member Tom Bjellos, OMA I, CLS, with Lubrication Technologies is critical of the currently available foam tests. He says, “With higher pressures being used in machining and issues with polypropylene filters, foaming in water-based metalworking fluids is becoming more prevalent in the field. It would be beneficial for troubleshooting, product recommendations and product formulations to have a more accurate device for foam testing.”
Hogan says, “It would benefit the industry to have more relevant foam and sump life tests. There are a number of ASTM tests for corrosion, foam and microbiological resistance, but they may not be relevant for all applications. Often, the accuracy and precision of these tests are insufficient. Additive suppliers, formulators and end-users may develop their own methods, and even equipment, to address this issue. These methods may be based on their needs, experience or the specific property being considered.”
Golden also feels that a test procedure that can assess how the metalworking fluid changes over time and be used as a way to assess sump life will be useful. He adds, “Although the specific timing for such a test will differ based on the particular application, there are likely some changes that can be predicted and imparted into the test fluid to improve performance.”
Jarvis says, “We feel that improved laboratory bench tests are needed to evaluate hard metals (e.g., titanium and inconels).”
McClure sees the need for better evaluation of high-strength aluminum alloys and advanced high-strength steel alloys. He says, “With the increased use of both of these alloy types in automobiles, edge crack testing is an important research area presently. Some of the high-strength aluminum alloys, 7XXX, are formed at elevated temperatures. Work on testing at these temperatures is important.”
End-user perspective
Pat Holden, maintenance manager for Poclain Hydraulics in Sturtevant, Wis., offers his perspective on the value of laboratory bench tests and how the results apply to the operations in his facility. He says, “With a majority of our fluid products, we find that the standard analytical testing offered and supported by most vendors’ internal laboratories are sufficient and provide the level of information we would use for decision making. When we consider a fluid change within a critical process, we may require more detailed testing such as infrared scanning of residues from test parts for presence of a product at various intervals in the production process.”
Holden evaluates a number of characteristics throughout the manufacturing process in assessing the performance of a fluid. He says, “Among the parameters examined are surface finish requirements, tool life, dimensional influence and cleanliness.”
But Holden feels that laboratory bench test data lags too far behind what is happening in the shop environment. He says, “Lab data is very useful for benchmarking certain metalworking fluids at the beginning of their life cycle. But we very rarely make metalworking fluid condition decisions based on lab results because they are not reflective of what we are seeing in our facility over time.”
Holden has some advice for metalworking fluid companies to bridge the gap. He says, “Metalworking fluid companies need to understand the process and environment that the products are being applied. The more a metalworking fluid company understands about the end-users’ environment, the better they will be in position to provide corrective actions if issues arise.”
Bjellos raises a key issue about the reluctance at times for end-users to evaluate a new metalworking fluid. He says, “Change can be a scary proposition when an end-user has been working with the same metalworking fluid for years. Even though improving the process, saving them money and reducing downtime would appear to be logical determining factors, just the idea of changing the fluid can be the biggest hurdle. The challenge is figuring out which factor(s) are the most important ones to the end-user.”
Laboratory bench testing plays a very useful role in the process. Bjellos says, “If the end-user does not see a need before a field trial, they see one after the subject comes up.”
Bjellos believes that the risk of doing a trial can be reduced by accumulating as much information as possible. He says, “Whether it is a simple or complex application, the metalworking fluid formulator needs to fully understand the process from beginning to end. It is the attention to detail that creates the best opportunity for success. It goes beyond tooling, fluid usage and fluid biostability. Health and safety issues, regulatory considerations, reducing waste streams and energy savings are a few of the other issues that are important to end-users.”
Caution should be used in working with readily accessible laboratory bench tests or tests that raw material suppliers and metalworking fluid formulators are comfortable in using. The tests will probably not correlate well with the real-world application. The gap between laboratory bench tests and machining operations can only be closed after carefully reviewing the actual operation and determining how well it fits tribologically with the laboratory bench test. Following this approach should lead to good initial success, but work still needs to be done to determine if there is a way to evaluate the performance of a metalworking fluid in the laboratory over time.
REFERENCES
1.
McClure, T. “Boundary Lubricity Additive Response Comparisons on Various Metals Using Twist Compression Tests (TCT),” presented at the 72nd STLE Annual Meeting on Monday, May 22, 2017, in Atlanta, Ga.
2.
Blau, P. (2016),
Tribosystem Analysis: A Practical Approach to the Diagnosis of Wear Problems, CRC Press, Boca Raton, Fla.
Neil Canter heads his own consulting company, Chemical Solutions, in Willow Grove, Pa. You can reach him at neilcanter@comcast.net.