Determining the best particle analysis test
Jeanna Van Rensselar, Senior Feature Writer | TLT Webinars February 2018
Critical factors include industry standards, equipment costs and the amount of expertise required.
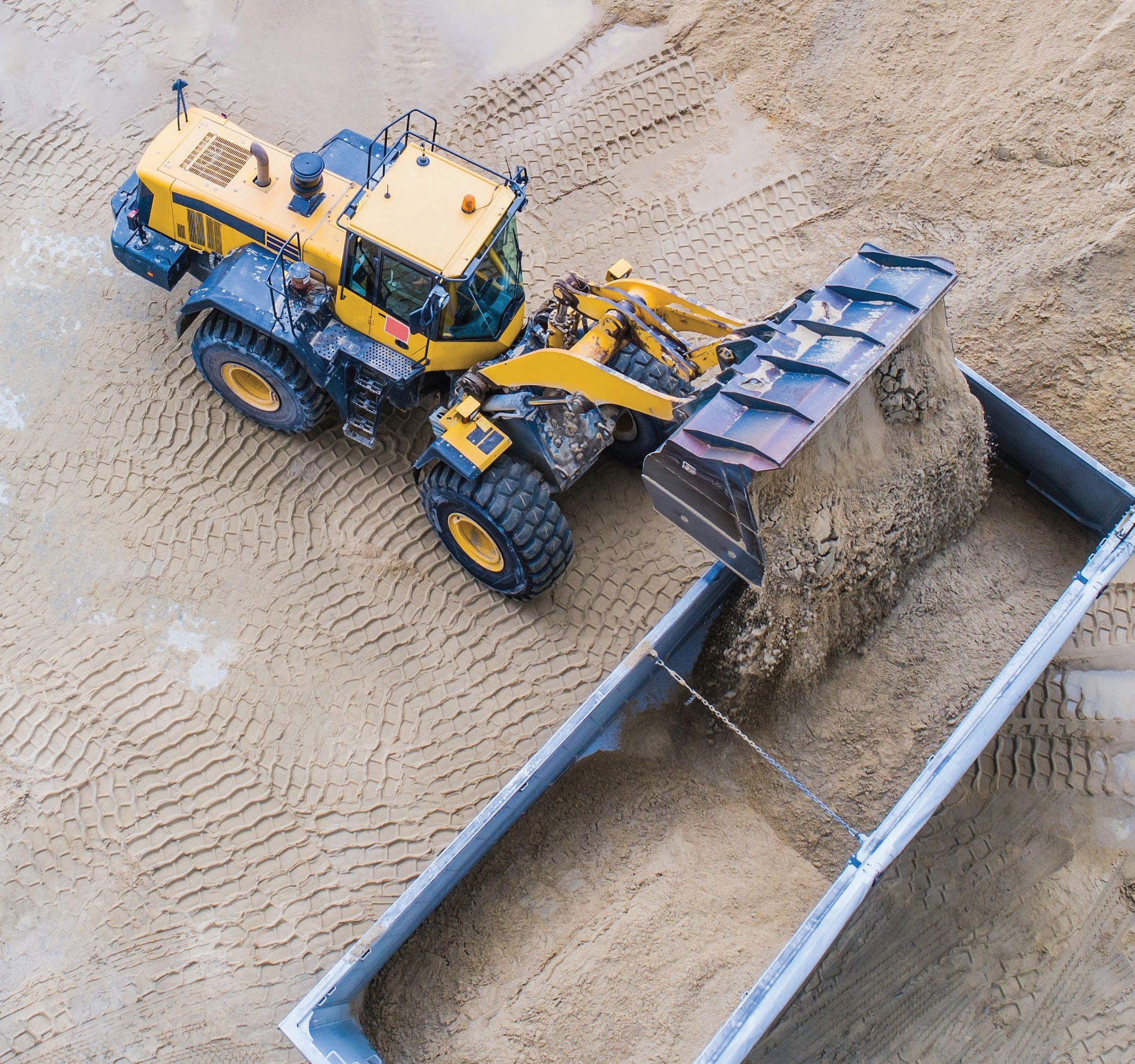
© Can Stock Photo / djedzura
KEY CONCEPTS
•
Make sure you don’t lose sight of the initial reason for considering particle analysis.
•
There are pros and cons to each test type with more expensive tests generally yielding more in-depth results.
•
Do the homework up-front, particularly if the decision involves purchase of new equipment.
MEET THE PRESENTERS
This article is based on a Webinar originally presented by STLE Education on May 3, 2017.
Determining the Right Particle Analysis for your Application is available at
www.stle.org: $39 to STLE members, $59 for all others.
Bridget Dubbert is the technical director for Engineered Lubricants in St. Louis, Mo. She has been involved in all aspects of the metalworking and lubrication industries for more than 18 years with roles in formulating, lab testing, field support and technical service. Dubbert is a STLE Certified Metalworking Fluids Specialist™. You can reach Dubbert at
bdubbert@englube.com.
Melissa James has worked in industrial lubrication for 24 years. As lead imaging technician for Engineered Lubricants she focuses on used oil testing and investigative analysis. She has extensive experience in X-ray fluorescence (XRF) and wear particle analysis by ferrography, light microscopy and scanning electron microscopy (SEM-EDX). You can reach James at
m.james.stl@gmail.com.
Bridget Dubbert
Melissa James
THE GOAL OF THIS ARTICLE, and the Webinar it is based on, is to help determine which particle analysis test(s) are most appropriate in given circumstances. This article will go over the most common particle analysis tests used to monitor contamination in industrial lubrication. The ultimate goal is to explain the basics of these tests, what information they convey and what needs to be considered when deciding which to choose. It’s important not to lose sight of the initial reason for considering particle analysis. Possible reasons include:
•
The customer is requiring it in order to meet a standard. This means the test and equipment need to meet the requested standard, whether ASTM, ISO or other.
•
A predictive maintenance program is in place that includes trend analysis.
•
There is a need to predict and prevent failures and plan downtime.
•
Customers want to conduct research in order to build a better filter, develop a cleaner oil, keep in-plant lubrication cleaner, etc.
WHICH TESTS ARE BEST?
In-line and on-line analyzers are automated and usually utilize the same technology as laboratory analyzers: light extinction or pore blockage (
see In-line/On-line Testing Options). These are typically used in critical equipment or when sampling can be difficult or dangerous and can include alarms, auto-shutdown and graphing over time. However, this article focuses on at-line and off-line tests.
•
At-line. An amount of fluid is removed from the process system and tested outside of the equipment but nearby in the plant or production area. In other words, a bottle sample is taken and tested immediately on site. This allows for a few more testing options while still providing quick turnaround time and action. Consistency of sampling point is crucial.
•
Off-line. Just as with at-line, a bottle sample is removed from the system, but it is sent to a laboratory. This allows for many more testing options, a controlled environment and focused expertise but also leads to longer turnaround time.
IN-LINE/ON-LINE TESTING OPTIONS
In-line. This refers to taking the measurement or analyzing fluid directly in the process stream. These analyzers do not disrupt the flow. The idea is to get a snapshot of the actual conditions of the fluid at that moment.
On-line. Sometimes the terms in-line and on-line are used interchangeably because neither removes the fluid sample from the process. The difference between them is for on-line; the process fluid is detoured to the analyzer. This allows for control over the flow rate and pressure when the process itself doesn’t allow for accurate results using in-line.
CONTAMINATION SOURCES
There are four means of contamination.
1.
Built-in. The contamination occurs during system assembly or part replacement. These parts/sources typically include: cylinders, hydraulic motors, hoses, fittings, pipes, pumps, reservoirs, valves and fluids.
2.
Generated. Most contamination is generated in use during break-in and operation; this is where predictive maintenance comes in.
3.
External ingression. The source of contamination is external to the machinery (nearby processes). Typical routes include reservoir breathing and seals. Once inside a system, dirt, sand, welding debris, etc., become abrasives and wear down components.
4.
Introduced. The potential for introducing contamination when servicing a system is frequently overlooked. This can happen during disassembly/assembly, via make-up oil and during repairs including replacing parts.
WHAT NEEDS TO BE MEASURED?
The next consideration is what needs to be measured, and while there are many possible measurements, the most common are:
•
Total debris. This is a simple way to monitor overall contamination—the total weight in set volume.
•
Biggest particle. This involves looking for the critical particle. Once particles of a certain size are detected, failure is imminent.
•
Distribution. Size distribution is used most often. This is most common in lubricant condition monitoring.
•
Composition. This is another frequent measurement—identifying the element/alloy and identifying the source.
TEST OPTIONS
There are a number of test options. The discussion here will center on the basic principles of how they work, what they are actually measuring and the pros and cons. These tests include:
1.
Elemental Analysis: ICP-OES, XRF-EDS
2.
Gravimetric
3.
Automatic Particle Counting, Light Extinction/Light Diffraction, LaserNet Fines, Pore blockage
4.
Ferrous Analysis: Ferrous Index/PQ, DR Ferrography
5.
Advanced Analysis: Manual Optical Microscopy—FPT, Automatic Optical Microscopy, Analytical Ferrography, SEM-EDS.
There are three time-related options for testing oil:
•
Before use. Test new oil as received, when cleanliness is critical.
•
In use. This is when the fluid is tested while in service. There are many advantages to this and several ways to accomplish it.
•
After use. Testing at time of lubricant replacement; during scheduled changes some of the drained fluid is analyzed.
1. ELEMENTAL ANALYSIS
For this test, inductively coupled plasma atomic emission spectroscopy (ICP-AES) is used. A liquid sample is introduced as an aerosol to a plasma. The plasma excites atoms in the sample. When the electrons of these atoms return to their ground state, they emit electromagnetic radiation (light) at wavelengths characteristic to each element. In other words, every element gives off a unique wavelength that can be detected and measured. The intensity of this emission correlates to the concentration of the element within the sample.
•
Pros of ICP-AES: sensitive to trace metals, accurate, high sample throughput.
•
Cons: size limit typically <10 μm, daily calibration, sample prep, destructive, expensive (often prohibitively).
Another elemental analysis test option is XRF-EDS.
•
Pros: no particle size limit, no regular calibration, non-destructive, fast, can be at-line.
•
Cons: not as sensitive, matrix-dependent, interferences, expensive.
2. GRAVIMETRIC
Gravimetric is one of the most basic tests (
see Figure 1). The insoluble contamination is determined by passing a fluid sample through a membrane filter disk with a known pore size and measuring the resulting increase in the mass of the filter. These membranes come in different pore sizes and materials.
•
Pros: basic lab equipment, inexpensive, easy.
•
Cons: no particle sizing/distribution, no morphology, no composition, includes ALL insoluble material, not sensitive.
Figure 1. What gravimetric analysis measures.
3. AUTOMATIC PARTICLE COUNTING (AUTOMATIC OPTICAL LIGHT)
Automatic optical or light particle counters can be on-line, at-line as portable devices or off-line laboratory equipment. When in the laboratory, the fluid sample is diluted, shaken and placed in a vacuum to remove any entrained air. The fluid is then drawn through a capillary tube past the light source. Then a photo detector on the opposite side works in one of the following ways.
Light Extinction/Light Diffraction/Light Extinction
This measures light scattered in terms of equivalent circular diameter (ECD). The software uses the analyzed total area of the particle and answers the question, “If the particle were a perfect circle, what would the diameter be?”
•
Pros: easy, fast, meets many standards, on-line, at-line, off-line.
•
Cons: no composition, largest particle size limited by sensor choice (typical 600 μm).
LaserNet Fines® Automatic Optical/Light
LaserNet Fines® was developed by Lockheed Martin and the Naval Research Laboratory to measure the size distribution and shape of wear debris in lubricating oil. It has been successfully deployed aboard naval vessels in an oil analysis-based predictive maintenance program and used by oil analysis labs. It only detects shadows, but by using a camera detection shapes can be categorized.
•
Pros: on-line or off-line; no regular calibration, water, fibers (better with dark); some morphology.
•
Cons: no composition, size limits 4-100 μm.
Pore/Mesh Blockage
Testing devices come in portable, handheld or on-line versions. The fluid is passed through a calibrated mesh screen or screens with known pore size. This is basically a metal version of the gravimetric test. As the mesh traps particles, the flow of fluid is slowed. A detector measures this change in pressure and converts this into a value.
•
Pros: on-line or off-line; not affected by air, water; dark oils, multi-phase, large particles.
•
Cons: no morphology, no composition.
4. FERROUS INDEX (FERROGRAPHY)
This is the study of ferrous wear (anything containing iron). There are three main tests associated with this.
PQ (Particle Quantifier)
These machines essentially have two magnets situated so the magnetic field is in equilibrium. When oil is set on the analyzer, any ferrous debris will disrupt this field. The amount of disruption is assigned a unit-less value that relates to level of disruption to the magnetic field. This unit-less number is called the Ferrous Index or PQ index.
•
Pros: fast, low-cost, little sample prep, trends well.
•
Cons: no size, no morphology.
Direct Read Ferrography
Direct read ferrography involves an oil sample diluted in solvent that flows through a tube over a powerful magnet. Larger ferrous particles attract to the magnet when they first approach the magnet, while smaller particles settle out further down the line. Photo detectors measure the amount of light blocked to give the density of large or small particles. This results in a unit-less value called Density Large or DL and Density Small or DS. These are used to calculate:
•
DL: Large particles >5 μm
•
DS: Small particles <5 μm
•
WPC: DL+ DS wear particle count
•
PLP: DL/DS percentage large particles
•
WSI: DL-DS wear severity index.
•
Pros: easy; trends well; more information; two size classes; as with ferrous Index, it trends well but only to itself, as it gives unit-less values.
•
Cons: relatively expensive, no morphology, limited composition.
5. ADVANCED ANALYSIS
Analytical Ferrography
This involves visual inspection of debris on a slide. Analytical ferrography uses the same idea as direct read—passing oil over a magnet except that a slide is used instead of a tube (
see Figure 2). Instead of detectors, the slide is placed under a microscope and viewed manually. It is best used as follow-up when trends identify a change. It can diagnose root cause and predict failure.
•
Pros: a powerful diagnostic tool, relatively better morphology, some composition.
•
Cons: time intensive, requires highly trained tech, expensive.
Figure 2. Analytical ferrography slides.
Filter Patch—Optical Microscopy Inspection
Another simpler way to visually inspect particles under a microscope is the patch test. The debris on the membrane is looked at under a microscope. While this isn’t as in-depth as analytical ferrography, this simple test can sometimes be all that is necessary. This certainly helps guide investigation to the source.
•
Pros: simple.
•
Cons: not as in-depth as other tests.
Automatic Optical Microscopy
This takes the same membrane and automatically inspects every particle with a microscope. A membrane is placed under the microscope, computer software is used to define the area under examination and thresholds are set. Then the microscope goes frame by frame and measures and classifies each particle on multiple axes.
•
Pros: customizable sizes, detailed morphology, flexible, large particles.
•
Cons: expensive equipment, requires skilled technician.
SEM-EDX
This involves a complete inspection of particles. A scanning electron microscope (SEM) produces images by using electrons instead of light and glass lenses, allowing for clear images and much higher magnifications. A beam of electrons travels down a column toward the sample. As the beam scans the surface, electrons within the sample are ejected. These are collected by detectors and converted into a digital image. Many parameters can be measured and classified: maximum diameter, minimum diameter (useful when testing filtration), area, perimeter of each particle, etc. Full elemental analysis on each particle then can be performed using EDS-XRF (
see Figure 3).
•
Pros: customizable size classes, detailed morphology, full elemental analysis, images of each particle.
•
Cons: expensive equipment, requires highly trained tech, can be too much data.
Figure 3. SEM-EDX particle classification/measurement results.
To sum all of this up:
Considerations for particle analysis include:
•
Do standards need to be met?
•
The cost of the equipment, supplies, personnel.
•
In-house or outside lab?
•
Is expertise required?
•
Are there special requirements (i.e., water)?
Sources for help with particle analysis test decisions (
see Figure 4) include:
•
OEMs
•
Equipment manuals
•
Filtration suppliers
•
Lubricant suppliers
•
Testing equipment suppliers
•
Third party labs
•
Internet: peers, blogs, videos
•
Trade organizations such as STLE conferences, workshops, magazines, webinars.
Figure 4. Particle analysis test overview.
The best approach is to do the homework upfront, particularly if the decision involves purchase of new equipment.
Jeanna Van Rensselar heads her own communication/public relations firm, Smart PR Communications, in Naperville, Ill. You can reach her at jeanna@smartprcommunications.com.