Describe the difficulties your company encounters in trying to attract bright young talent for technical positions relating to lubrication.
TLT Sounding Board February 2018
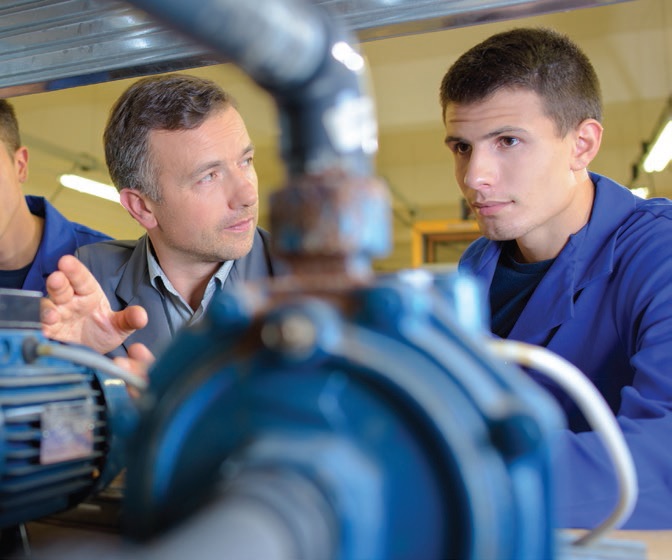
© Can Stock Photo / photography33
The shortage of good technical people entering the field continues to be an issue for the lubricants industry. Competition for young talent is intense, and candidates often are more interested in fields with the words bio or nano attached to them. STLE members in rural areas struggle with competitive wages and the preference many young people have for urban environments. Many survey respondents commented on the lack of awareness young people have about the lubricants industry. One thing all survey respondents agreed on was that in-house training is essential for young hires. “There are few professionals graduating from universities with knowledge in condition monitoring,” said one TLT reader. Lubricant companies typically use existing personnel to train the next generation of technical personnel, as well as conferences, workshops, technical schools and Webinars.
I can’t pay the smart ones enough to attract them to the business.
There is no preparation in schools for this line of work. Can only really be accomplished in an internship-type setting at a manufacturing plant or lube supplier.
While many new, young people have an excellent formal education, they have no understanding of the workplace and no practical experience. In immersing a new person into our team and expecting him to use our cumulative knowledge, both practical and formal, we can bring him along in a comfortable and safe manner.
Union contract does not allow it; lubrication positions come out of the grounds keeping crew. I have to live with it and find training for them as much as possible.
We are currently about to embark on a recruitment campaign for a new technical support engineer. We are fascinated to see how easy or difficult the process will be. We’ve received some impressive CVs from various head hunters the past few months.
The biggest issue is that none of the young talents are aware of the importance of lubricants and lubrication in the industrial environment. We address it in the way that we allow them to carry out certain tests during the familiarization phase to understand, on the one hand, how a lubricant behaves and, on the other hand, to experience how lubricants and lubrication can support customers in their applications in daily work.
The problem is not attracting people to the job but, rather, keeping them in a technical position long enough so they can make meaningful contributions.
We’re still searching for talented people like chemists. What is the best searching method available for small independent lubricant manufacturers?
There are not many experienced lubrication engineers, so we try to offer internship and technical rotation positions to young engineers and chemists.
This has not been an issue with our company.
Low remuneration and poor career prospects are obstacles to attracting young talents to rural areas.
Due to lack of trained and experienced oil analysis experts, we influence technical schools to provide necessary training classes related to tribology, chemistry, oil properties, analysis and results interpretation.
Finding new talent to work in the trenches and not wanting to be the next CEO. Being more selective and setting expectations earlier in the interview process.
The cost of training plus the cost of retaining talent bumps up against the longevity of the employee. Our youngsters seem to think in terms of 2-4 years before moving on.
Our industry is not well-known in academia, so most new graduates are unfamiliar with the field. We actively participate in on-campus recruiting to try to cultivate mind-share with the upcoming graduating class of students.
Humans being replaced by automated systems. We are joining the automated race.
We aren’t hiring.
Deficient salaries. We are not addressing it.
Location of work sites.
One difficulty I see is when talent does arrive, there are minimal processes and training to bring the new person up to speed. This eats time, and the longer this takes the more likely they are to leave.
If you need to hire a lubrication engineering specialist, do you look for a chemist, chemical engineer or mechanical engineer? We usually rely on known academic professors and programs for candidates, but it is confusing for HR generalists to know how to help in recruiting.
Availability. Resign yourself to teaching them.
Convincing them of the future need for oil products.
The lubrication industry doesn’t seem to have the draw to younger generations. Better incentives, including pay, would help.
Young technical minds are mostly interested in biomed, nanotech and exotic fields. We are trying to show our attempts in utilizing renewable resources for lubricants. Quite often young talents become interested in replacing mineral oils and toxic components.
They find it is not an interesting topic. The solution is to show them simple analysis of oil and the results of it.
No one knows anything about lubrication. That and our HR department wants to have experienced people. They are afraid to be responsible for training new staff and then having them leave.
Which scenario best describes how well your company stays current with technical advances in oil condition monitoring databases?
We successfully adapt our database to the new software when the old version becomes obsolete.
31%
We use the newest software but have lost data when migrating to the new system.
9%
We are still using the same database we used 10 or more years ago.
18%
We use a notebook database system.
12%
Other
30%
Based on responses sent to 13,000 TLT readers.
How does your organization transfer knowledge about condition monitoring to the next generation of lubrication engineers?
I am still mentoring to a degree, but in my situation I must protect intellectual property. Thus, I don’t actively market for fear of IP leaks.
Word of mouth and training provided by a lubrication person.
School of hard knocks. Live it and learn it in the field; train them in classes and on-the-job activities.
We have to act as a true team because we all have different areas of expertise and must rely on one another for answers to questions that we have not previously encountered ourselves. A new man, as well as other team members, are constantly accumulating information in this manner.
We train them ourselves through our experienced engineers.
Very poorly. They are trained by the previous lubricator who also was trained by the previous lubricator.
Our company has invested heavily in the past 18 months in new training material that is readily available online to all our consultants. The New Year will see an even more effective online training tool made available.
Our organization transfers knowledge by arranging conferences and workshops.
Condition monitoring is not a core business of our company. Nevertheless, as our products need to operate in combination with condition monitoring sensors, we teach them how to combine condition monitoring with automatic lubrication systems.
We keep written records on nearly all the tests and procedures. In fact, we make many of them public by publishing short articles in conference proceedings.
No organized process other than word of mouth.
Our department hires and trains new lubricant engineers in lubricant condition monitoring.
Senior personnel work with younger staff prior to retiring.
Sending personnel with experienced technicians in the field to learn on the job.
Hands-on training in the field and classroom.
Training and transferring information as new technologies are employed.
Hands on training as well as every Webinar available.
Cooperative efforts, learning from senior engineers.
My organization does not seem to worry about losing knowledge gained through experience. They generally do not make any effort to have senior members share their experience. It is up to individuals who show interest in learning to carry out this vital function.
Currently everyone is too busy to be able to have the talks and learning moments that are key. It is a “figure it out” mentality culture. This is fine but takes additional time, and re-inventing the wheel can be costly.
Personal training, on-the-job learning, best practices and archived reports.
Utilize current technical experts as mentors.
Publish papers, educational workshops.
Standardized work documents.
Laboratory exercises made by student directly, such as on the motor stand.
We don’t do a good job of this.
Who makes decisions based on your oil analysis reports?
We rely on the lab’s recommendations.
6%
Our lab reports don’t include recommendations, so we rely on our internal experts.
9%
We combine lab reports and our internal experts.
64%
We use an intelligent system that tells us what to do with the data.
0%
Other
21%
Based on responses sent to 13,000 TLT readers.
Editor’s Note: Sounding Board is based on an email survey of 13,000 TLT readers. Views expressed are those of the respondents and do not reflect the opinions of the Society of Tribologists and Lubrication Engineers. STLE does not vouch for the technical accuracy of opinions expressed in Sounding Board, nor does inclusion of a comment represent an endorsement of the technology by STLE.