Describe an example where component failure was mitigated, or a reliable technology was developed, with the aid of a properly selected tribotest.
TLT Sounding Board January 2018
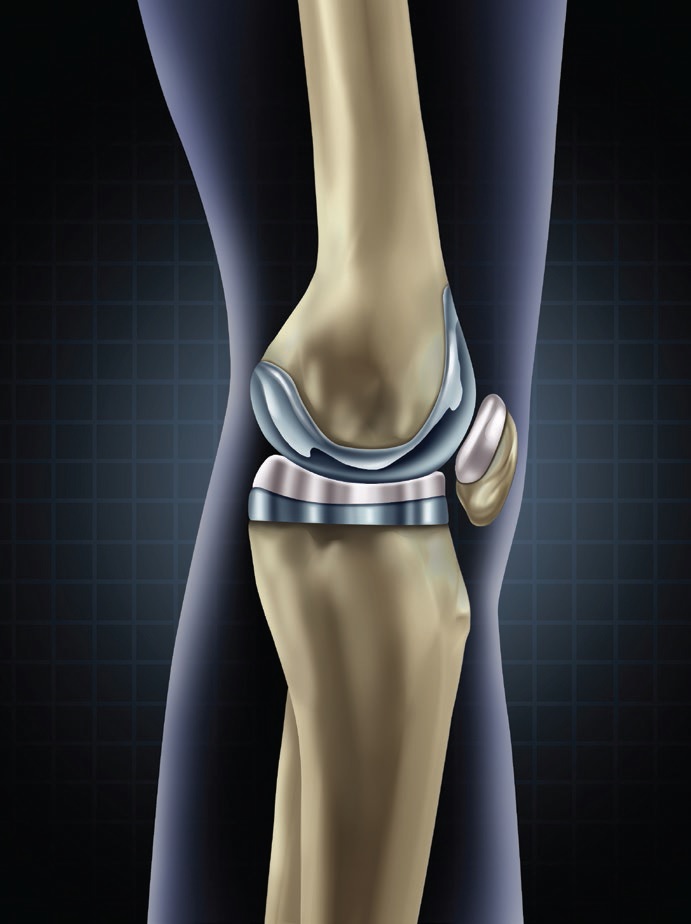
© Can Stock Photo / focalpoint
Tribotesting diagnoses failure issues, prevents major machine repairs and replacements, identifies lube-related problems and, in some cases, averts injuries and fatalities, according to TLT readers responding to this month’s survey. The pin-on-disc and four-ball wear procedures were the tribotests most frequently cited in survey answers, and gearboxes are the pieces of equipment where lubrication engineers are most likely to employ tribotesting. Readers also emphasize the need for OEMs to take lubrication issues into account during product design. Two-thirds of TLT readers say insufficient consideration is given to the selection of relevant tribotests in product development and failure analysis.
Re-designing a lubricant test program that included a run-to-failure tribotest to also include a tribotest that correlated with steady-state operation. This enabled the application of lubricants that provided greater performance during normal operation.
Construction machine axle transfer case filled with ATF Dexron II. An oil analysis showed that this oil had aged extremely after 700 hours and, therefore, the oil change interval of 1,000 hours was not reached. We converted to ATF Dexron III H. Oil analysis after 1,000 hours all right. Oil change interval after 1,000 hours was maintained.
We were looking at the wear of cams and followers in fired engines. A rig test was developed that looked at the contact, and several influencing factors were identified. Drained crankcase oil was used in the tribotest, as this gave more realistic results compared to using new oil.
Antiwear coatings can be developed with aid of wear tests.
This was long ago but involved developing wire drawing lubricants for copper wire. We used a tribotest featuring hardened steel specimens, which seems wrong. However, the material properties of the specimen better represented the properties’ various oxides and other very hard inclusions and hard spots in the worked wire. Thus, we were able to develop a lubricant that could handle much lower quality wire rod and still produce a salable wire product.
Many users seem to rely on visual or basic routine testing to inform them of abnormal wear and contamination. Use of a filter patch field test and cheap microscope camera provided proof that a gearbox oil color was not an indicator of failure and prevented a rash decision to replace the equipment.
We were delivered incorrectly labeled containers with the wrong viscosity grade. Testing showed this prior to installation in a machine, and we set up a program to test all lubricants prior to using in the field.
Enhanced run-in performance of gears by novel lubricants in ball-on-disc investigations.
While pulling an oil sample, there was extreme back pressure on the inspection plug. Looking for the reason we discovered that there was no breather, just a plug. Testing deemed this gearbox would fail and had the potential to stop production with the potential for fatal injury or death.
Gears scuffing.
Resistance to micropitting.
Bleeding behavior of lubricants in automatic systems helped identify the right lubricant for a long-term solution of automatic lubrication in the field. Failure of the lubricant (thickener blocking the distributors and lines) leads to component failure and high maintenance work.
Bearing material and grease for an improved long-stroke motion mechanism in a DVD player.
Engine seizure.
There are the several tribotests, but the pin on disc with high load may be the most important for us.
A four-ball wear machine and newly modified procedures were used to evaluate PTFE powders in model greases and dispersions. The applied load was ramped up at constant speed, and then, in some cases, the load was maintained at a constant value or ramped back down (cyclic test). The temperature was not controlled, and the speed was standard. Friction and temperature data were collected during each test, analyzed and related to wear scars and wear particles. Results for greases, liquid dispersions of PTFE and base oils were compared and used to identify modes of wear and benefits of PTFE as a lubricant additive.
Is sufficient consideration given to the selection of relevant tribotests in product development and failure analysis?
Yes
33%
No
67%
Based on responses sent to 13,000 TLT readers.
We used in a major citric-juicing operation where fluid analysis and testing were critical to root-cause failure detection. We moved from reactive to proactive maintenance strategies.
Plain bearings are a target-rich environment for that. Especially important is the harmonic contents of the shell form versus the flow speed and development. Not sure that qualifies as a tribotest, however!
Development of a line of centrifugal/vacuum oil cleaning equipment developed as a result of many years of microscopic analysis and telling clients to change oil simply because it was loaded with contaminants when the oil was in perfectly good condition. Information regarding lube oil management practices has been market driven by oil companies that want to sell oil, not look after their clients’ interest.
Lubricity testing of diesel fuel in conformal contacts on a Plint-Cameron TE77.
Through tribotesting, we have found varnish issues in turbine fluids that lead to servo valve failures. The testing helped determine a path to successful conversion and success.
We were able to screen various transmission oil formulations using the MTM (mini-traction machine) and select the formula with the predicted best fuel economy.
IC engine valve train.
SRV for engine oil antiwear component development.
Comparative lubricant performance screening via OSU/EWI/CPF testing (cup-drawing).
We use ferrography quite often. It has aided in scheduling replacement machinery such as large gearboxes.
Development of zirconia coatings for knee implants. Multiple tests were run-in joint simulators.
Top drive gearbox failure due to using high-EP-level gear oil in yellow metals environment.
The situation of component failure with regard to engine oils can be catastrophic and leave you stranded with costly repairs. Seizing an engine due to gelation of the engine oil is an example where component failure can be avoided with the aid of the MRV tribotest. MRV (mini-rotary viscosity) (D4684 Standard Test Method for Determination of Yield Stress and Apparent Viscosity of Engine Oils at Low Temperatures) is a reliable technology and keeps this from occurring.
The process of dragging the fiber through the eyelet was dependent on the very narrow range of the rounding radius of the eyelet. Tribotest studies found the optimal value of it.
Analytical Ferrography identified abnormal wear properties in a propane refrigeration screw compressor. This allowed the end-user to plan an inspection and repair. Because the in-process failure was detected early, the required repairs were only a fraction of what they could have been.
Development of a new additive for a six-high breakdown cold rolling mill where excessive wear of the working roll has occurred.
Electrical conductivity testing.
Do you think dedicating additional resources to tribotesting capabilities is a good idea, or should those resources be devoted to other research projects?
Developing tribotesting capabilities
88%
Devote those resources to other research projects
12%
Based on responses sent to 13,000 TLT readers.
Editor’s Note: Sounding Board is based on an email survey of 13,000 TLT readers. Views expressed are those of the respondents and do not reflect the opinions of the Society of Tribologists and Lubrication Engineers. STLE does not vouch for the technical accuracy of opinions expressed in Sounding Board, nor does inclusion of a comment represent an endorsement of the technology by STLE.