Complexity in ISFA (in-service fluid analysis): Part XXXVI
Jack Poley | TLT On Condition Monitoring January 2018
Increasingly, organizations are choosing a two-tiered approach to oil sampling and analysis.
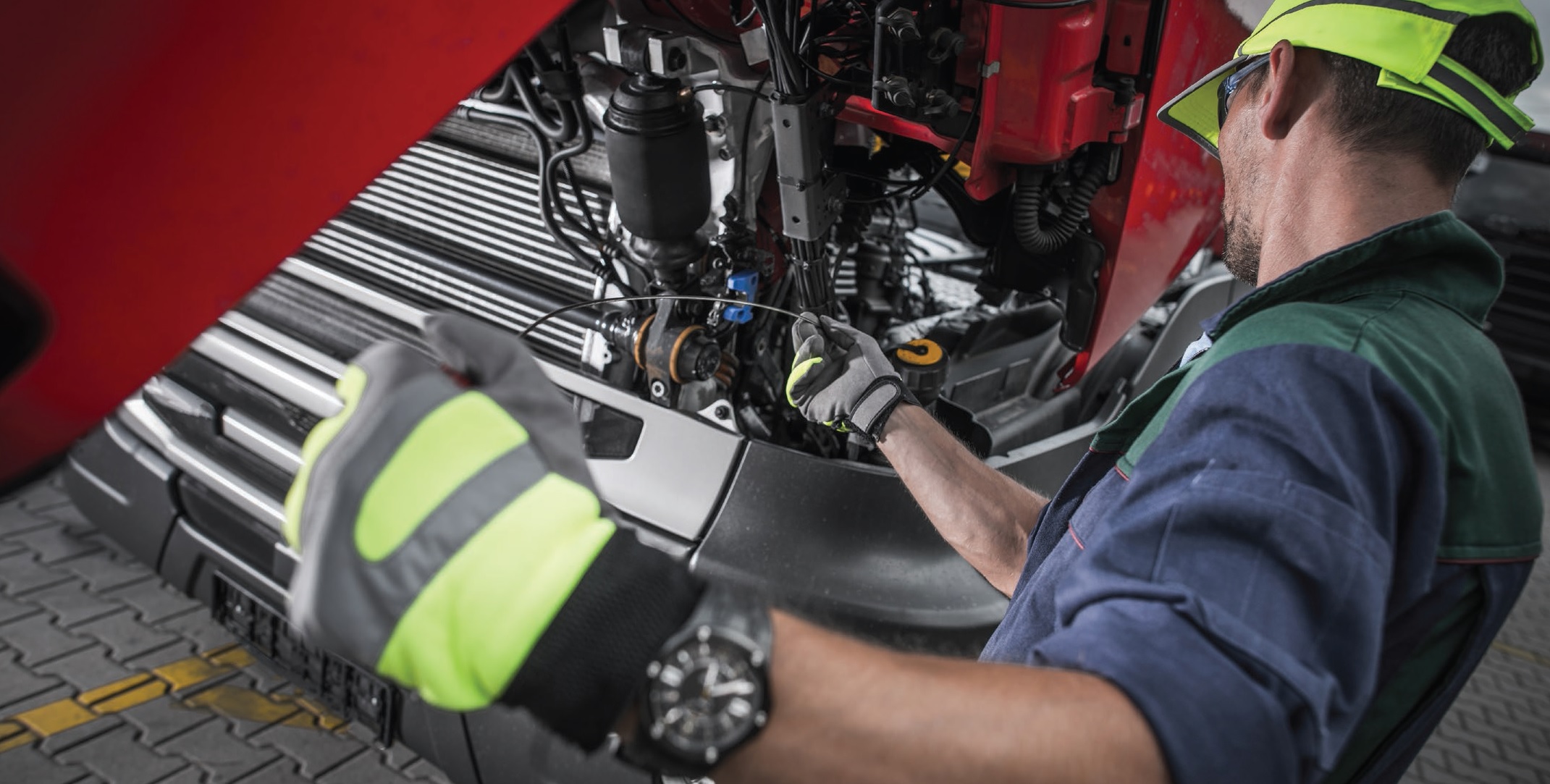
© Can Stock Photo / welcomia
AS MACHINERY CONTINUES TO GET MORE SOPHISTICATED, and as technology continues to proliferate with respect to purpose-built instruments for ISFA, the maintenance community has begun to spawn updated perspectives of what a program is all about or should be.
There are two areas that I notice are being looked at more closely as machinery gets bigger, more complex and certainly more expensive:
1.
Maximizing the ISFA program to gain beyond the obvious big saves. This includes paying closer attention to the testing package and logistics—what does the suite of tests address? What can it detect, and how far in advance can it detect what it detects? And how long will it take?
2.
The need to validate savings (true net gains) from the program. The days of assumption of savings, while likely valid, are being replaced with a more thorough assessment of practices and benefits. Reliability
and accountability are beginning to be demanded of maintenance departments.
Concentrating on Point 1 for this installment, there are more questions being asked, for example, about lubricant and machine longevity. The lubricant and the machine are surely symbiotic with each other to a great extent, but the rising cost of lube changes and the sensible notion of conservation in general have caused numbers of companies to investigate lube drain extension with greater urgency.
When I first entered fluid analysis as a career in the early 1960s, I heard more than once, “Oil is cheap—I just change my oil regularly in my car and my trucks (or dozers or gear sets).” Lubricants haven’t been cheap in a long time, and the labor that changes the fluid also has increased. Add disposal costs stemming from EPA regulations, and it’s a different world entirely. Even the common denominator automotive market seeks extended lubricant service with increasing interest.
A more recent phenomenon is the popularity of onsite, smart portable labs, often including handheld, fast-acting instruments that address contamination (dirt, water and the like) and degradation (lube chemistry condition) with very good precision. VIS also can be site provided. There are a couple such devices that use miniscule amounts of sample and can be wiped clean for the next analysis. The longest part of the process is taking the sample. With an easy but very capable testing capability onsite, a truck coming in for general service can have its lube checked for continued use, enabling a decision to be made in real time. Offsite labs, though perhaps more thorough, cannot match this type of convenience and real-time process. A safe lube drain extension can only be realized if a relatively quick and informative testing process is available before the truck needs to go back into service.
But the remote lab does have the advantage of being able to detect machine wear, and wear detection is the backbone of ISFA. Knowledge of fluid condition is certainly important, but machine condition monitoring is the most important information to have. Yes, I mentioned some small-footprint ferrous (Fe) detection devices in my previous article (
November 2017), but they involve a bit more labor and time. The rapidity and ease with which handhelds can test sets up new possibilities.
This apparent dichotomy of lube condition versus machine health, coupled with viable onsite testing, has led to the notion of tiered testing, wherein a normal lube condition/contamination test results in an extended drain interval, but a sufficiently abnormal result leads to a second sample being sent to an offsite lab (or similar scenario). It is easy to argue that only testing for wear metals when the lube is suspect poses risks. However, it is generally conceded that a majority of machine failures are due to lubricant contamination or breakdown (degradation). It’s just another way of thinking, and time will sort it out.
In a fairly recent move, segments of the U.S. military are practicing this approach; where Tier 1 is a lubricant quality test and Tier 2 is a wear-trauma assessment when the quality test fails.
There are insufficient data available as to the efficacy of the tiered approach, but a successful story by the military would certainly enhance demand for onsite fluid condition testing. We also know the sampling world wants to have samples analyzed promptly—that points to eliminating the shipping time and inherent delays therefrom.
Jack Poley is managing partner of Condition Monitoring International (CMI), Miami, consultants in fluid analysis. You can reach him at jpoley@conditionmonitoringintl.com.
For more information about CMI, visit www.conditionmonitoringintl.com.