Measuring a Surface Film of Oil with Surface Continuous Wave Ultrasound
Prof. Rob Dwyer-Joyce, Leonardo Center for Tribology, University of Sheffield, Sheffield, UK | TLT 2016 TFC Abstract Highlights December 2017
For the benefit of our readers involved in tribology research, TLT is publishing abstracts of the best papers presented at the 2016 Tribology Frontiers Conference. Registration for the 2018 TFC opens in May. Until then, you can find 2018 updates and program information at www.stle.org.
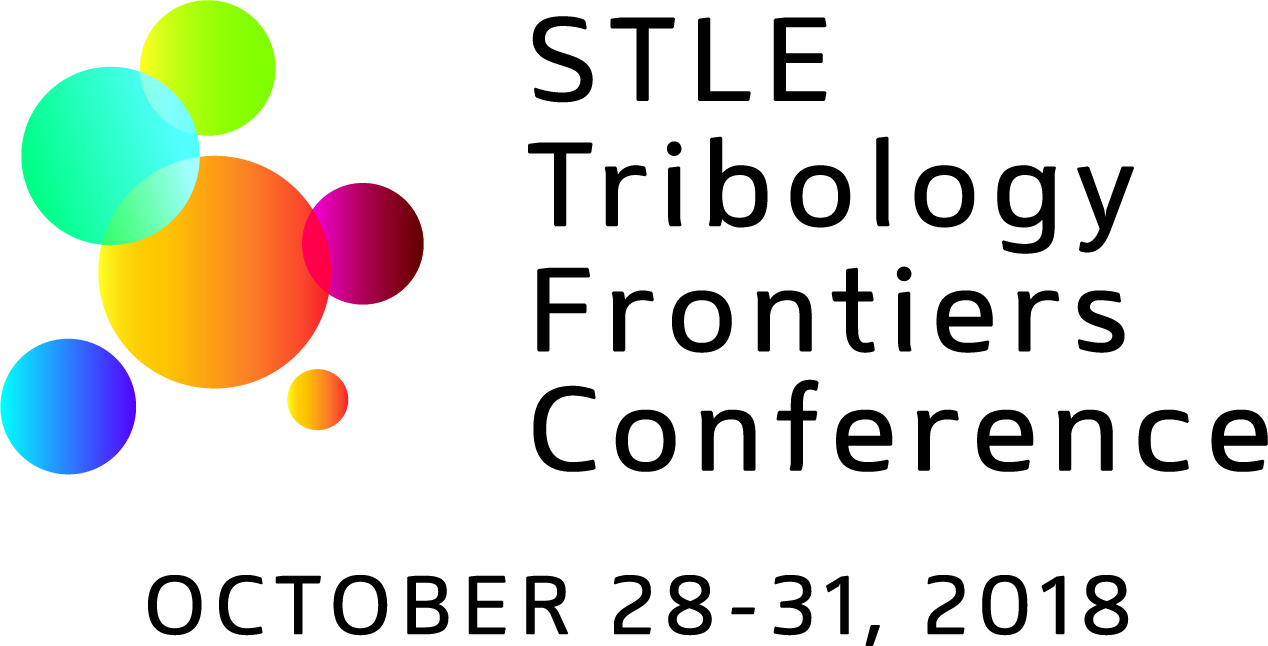
Co-sponsored by ASME Tribology Division.
Measuring a thin oil film deposited onto a surface from the component back face is tricky. We might, for example, want to know how much coolant is left on a rolled metal strip, how oil is distributed around a gearbox casing or how much oil there is ahead of an approaching piston ring. Ultrasound is useful for non-invasive measurements as it can penetrate through components; however, a pulse of sound is almost completely reflected back from a thin surface film and the oil film cannot be detected. This new approach is a way of amplifying the effect of the film. Rather than using discrete pulses, we inject a continuous wave of ultrasound of continuously varying frequency. The wave bounces back and forth inside the component superimposing to form a standing wave pattern that looks like a hedgehog. There are spines when the pulsing frequency is such that constructive interference happens. The nose and tail of the hedgehog are formed because the transducer cannot generate waves at frequencies below 9MHz and above 12MHz. When an oil film is added, two things happen: the component resonances shift a little and a few spines go missing from the hedgehog’s back, in this case at 10MHz. Those frequencies are lost in the oil film resonance. From this resonant frequency, if we know the speed of sound in the liquid, we can determine the film thickness—for this case it is 36μm.